钨铜复合材料由导电性高的铜和难熔金属钨组成。金属钨和铜之间既不互相溶解也不形成金属间化合物。钨和铜只能形成假合金(pseudoalloy)。其中钨铜两相单体均匀混合,因此钨铜合金既呈现出钨的耐高温、高硬度、低膨胀系数等优点,又呈现出铜的高导热、导电性等综合优异性能,在电工、电子和军事等领域得到了广泛的应用[1-3]。制备钨铜复合材料最常用的方法是熔渗法和活化烧结法。活化烧结法通常是在钨粉中加入少量的活化剂Fe、Ni、Co等,经过混粉压制后,即可在较低的烧结温度下活化烧结出所需密度的钨坯,再进行渗铜[4]。但对于靶材,活化剂会成为材料中的杂质元素,严重影响靶材的使用。因此,主要研究在无活化剂添加的情况下,烧结温度对钨骨架及钨铜复合材料组织与性能的影响。
1、实 验
所用原料为:钨粉(纯度高于99.8%,粒度为6~8μm,氧含量为0.04%)和纯铜块(按GB523 1-85选用T2铜)。首先钨粉压制成形,紧实率为60%;将压坯置于管式炉中在100℃烘干2~3 h,取出后置于石墨坩埚内,在真空碳管烧结炉中进行烧结。烧结温度分别为1550,1650,1750,1850和1950℃,保温时间为2 h,随炉冷却。真空度保持在1×10之Pa以上;最后将熔渗金属铜块和烧结坯叠放在石墨坩埚内,置于温度为1200~1400℃的H2气氛烧结炉内熔渗1~2 h。用阿基米得原理测定样品的密度。氧和氮含量用EMGA.620W氧氮分析仪测试。电导率用7501型涡流电导仪测试。硬度用HB一3000型布氏硬度计测试。在JSM一6700F型扫描电子显微镜上对显微组织和断口形貌进行观察。
2、结果与分析
2.1 烧结温度对钨骨架收缩率及相对密度的影响
表1列出不同烧结温度下钨骨架收缩率及相对密度值。由表l可以看出,在高温烧结过程中,宏观上发牛体积收缩与致密化,线收缩率和体收缩率均随着 温度的升高而增加,相比较线收缩率而言,体收缩率 增加得更为迅速。1950℃高温烧结使试样的密度显著增加,钨骨架的相对密度相应由60%增加到74.8%。
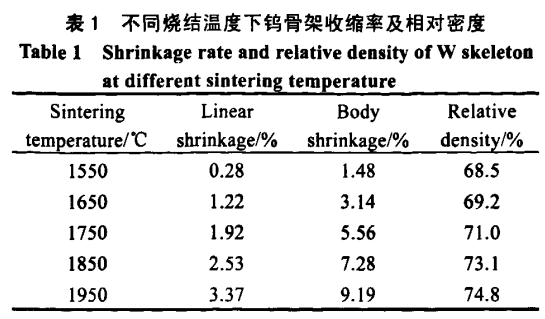
2.2烧结温度对钨骨架形貌的影响
图1为不同烧结温度下的钨骨架形貌。由图中可以看出,当烧结温度为1550℃时,钨骨架已经形成,颗粒呈现不规则的形状且颗粒之间由点接触转化成粘结面结合(图1a)。经1750℃烧结后,钨颗粒边缘逐渐球化,粘结面不断扩大导致烧结颈逐渐变大且数量增加(图1b)。当烧结温度为1950℃时,钨骨架中的烧结颈长大趋势更加明显,颗粒之间由机械啮合转变为冶金结合,从而进一步增强了钨颗粒间的粘结力;部分钨颗粒有不同程度的长大,其中骨架中的孔洞球 化现象更为明显,但是骨架中的大部分孔隙是连通的,这样的骨架结构对后期的熔渗非常有利。
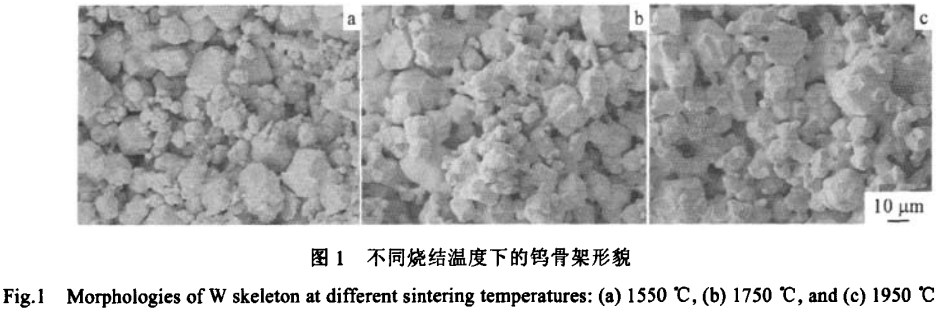
根据Coble[5]的定义。固相烧结可分为3个阶段:第l阶段即烧结初期,该阶段包括了一次颗粒间一定程度的界面即颈的形成f颗粒间的接触面积从零起始,增加并达到一个平衡状态);第2阶段即烧结中期始于晶粒生长开始之时,并伴随颗粒间界面的广泛形成,此时,孔隙相互连通成连续网络,而颗粒问的晶界面仍是相互孤立而不形成连续网络,大部分的致密化过程和部分的显微结构变化产生于这一阶段:第3阶段即烧结后期,烧结过程中孔隙变得孤立而晶界开始形 成连续网络。在这一阶段孤立的孔隙常位于两晶粒界 面、三晶粒
问的界线或多晶粒的结合点处,也可能被包裹在晶粒中。烧结熔渗法制备钨铜复合材料时,控制烧结在第2阶段完成后就不再进行,以保留孔隙的连通,这点不同于粉末冶金的致密化烧结过程。
2.3 烧结温度对钨铜复合材料组织与物理性能的影响
图2为不同烧结温度的钨骨架熔渗铜后的显微组织。可以看出,不同温度烧结钨坯渗铜后的金相组织中晶粒细小均匀,不存在大于200 gtm的铜相或钨相聚集区,铜呈网状分布。随着烧结温度的升高,钨骨架连续性程度愈大,孔隙越小、越球化。性能良好的钨渗铜复合材料的理想组织应以钨相形成连续的骨架,液相铜填充在钨骨架的孔隙内,凝 固后形成立体的网状结构,铜相围绕钨颗粒间隙和钨颗粒间的烧结颈处,均匀连续地分布[6-7]。
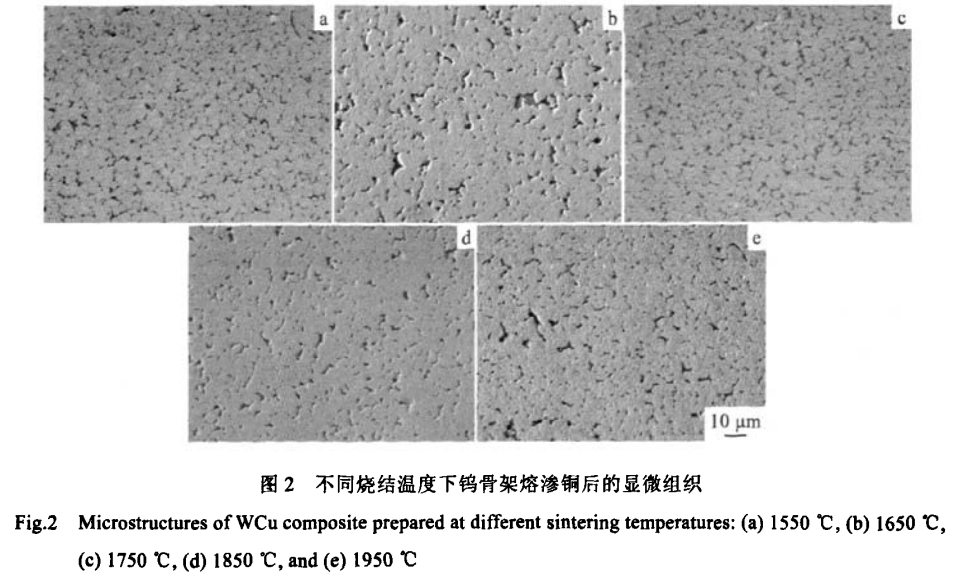
图3是1950℃烧结钨骨架渗铜后的钨铜复合材料的SEM面扫描照片。由图中可以发现,钨和铜两相均匀分布,这种组织 均匀的钨铜复合材料有利于发挥复合钨、铜两相各自的优异性能,可大大提高材料的导热及导电性能[8]。
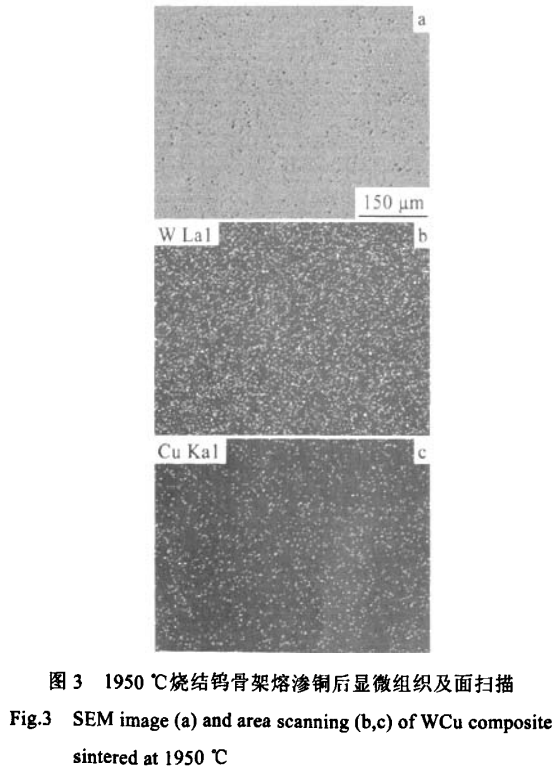
图4为钨铜复合材料硬度和电导率随烧结温度的变化曲线。可见,随着钨坯烧结温度的升高,硬度不断增加,当钨坯的烧结温度从1550升高到1750℃时,钨铜复合材料的硬度(HB)随烧结温度的升高变化明显,由2250提高到2450 MPa。当烧结温度超过1750℃时,硬度变化曲线变得平缓,当烧结温度达到1950℃时,钨铜复合材料的硬度(HB)为2520 MPa。
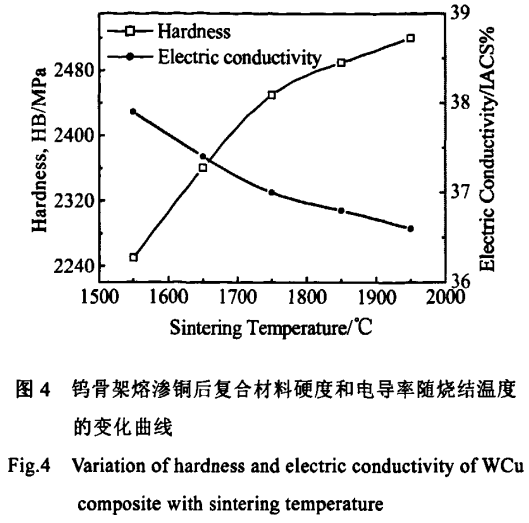
对于钨铜粉末冶金材料,影响其性能的主要因素是孔隙度和晶粒度。随烧结温度的升高,钨坯中钨颗 粒粘结面增加,钨骨架强度提高,故钨铜复合材料的硬度不断增加。
由图4还可看出,钨铜复合材料的电导率随烧结温度的升高而降低。这是因为随着烧结温度的升高,材料的收缩晕增加,导致钨坯的密度增加,孔隙减少。在随后的熔渗过程中铜含量也相应减少,导致电导率 呈现出与硬度相反的趋势。但因本研究中钨铜复合材 料未添加其他活化元素,所以在1950℃烧结后,仍获得了很高的电导率,达到了36.6 IACS%。
2.4烧结温度对钨铜复合材料致密度及含气量的影响
对于本研究中的烧结温度,已远远超出钨的再结晶温度,由于高温烧结引起的收缩,使烧结坯的孔隙率发生一定变化,故渗铜后的钨铜复合材料理论密度由下式计算:

式中,ρ理论为钨铜复合材料的理论密度,g/cm3;ρ为纯钨的密度,取19.32 g/cm3;ρcm为纯铜的密度,取8.96 g/cm3;V致为全致密钨坯的体积,cm3;V烧为钨坯烧结后的体积,cm3表2列出不同烧结温度下钨铜复合材料的收缩率和相对密度。由表中可以看出,随着温度的升高,钨铜复合材料的相对密度一直保持线性增加。钨坯经1950℃,2h烧结渗铜后,致密度达到96.9%。这说明1950℃高温烧结钨坯,钨铜复合材料可以获得较高的相对密度。
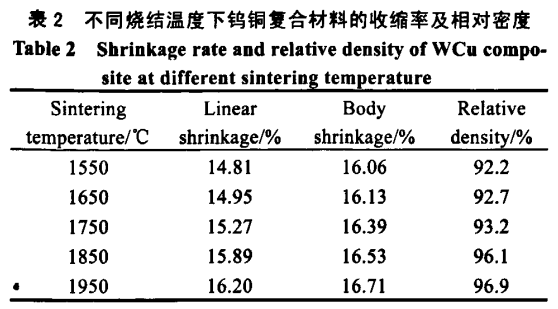
在大多数情况下,气体对材料的使用性能有不良的影响。钨铜薄膜在电子设备和表面装饰方面有巨大的潜在应用前景,对于高质最的薄膜主要是由磁控溅射靶材的方法获得[9]。而钨铜靶材的镀膜质量与靶材的气体含量密切相关,所以对于钨铜复合材料中气体含量的控制就显得尤为重要。
文献[10]报道,钨中通常含有少量的氢,氧和氮的含量则要多一些,而氧也易溶于电阴性最强的过渡金属铜中。所以对于钨铜复合材料,气体含量主要是氧和氮含量,钨和铜可以与氧形成氧化物,而氮则一般不形成化合物容易除去[11]。研究表明,低价氧化物 比高价氧化物难以被还原[3]。经检测分析,钨坯经1950℃,2 h烧结渗铜后,其氧含量为仅为4×10-6,明显低于文献[11]中13×10-6的氧含量,而氮含晕也只有3×10-6。在无活化剂添加的条件下,钨坯经过高温烧结后,低熔点杂质及难还原的低价氧化物通过挥发和分解被除去,从而提高了钨坯的纯度,继而提高了钨铜复合材料的纯度。
3、结论
1)真空高温烧结钨骨架时,随着烧结温度的升高,钨骨架和钨铜复合材料相对密度不断增加。当烧结温度从1550升高到1950℃时,钨骨架的相对密度由68.5%增加到74.8%,钨铜复合材料的相对密度由92.2%增加到96.9%。
2)随烧结温度的升高,钨铜复合材料的硬度不断增加,电导率下降。当烧结温度从1550提高到1950℃时,硬度(HB)由2250增加到2520 MPa,电导率由37.9IACS%降低到36.6IACS%。
3)真空高温烧结钨骨架熔渗铜制各的钨铜复合材料,烧结温度升高到1950℃,钨铜复合材料的氧含量为4×10-6,氮含量为3×10-6。
4)当钨生坯的紧实率为60%时,采用1950℃真空烧结钨骨架后渗铜的工艺,可以获得综合性能良好的钨铜靶材。
参考文献 References
[1]GermanR Metal.Int.JPowderMetall[J],1994,30(2):205
[2]Liang Qiong(梁琼)et a1.Aerospace Materials&Technology(宇航材料工艺)[],2001,5:36
[3]Fan Zhikang(范志康)et a1.High Voltage Electrical ContactMaterial(高压电触头材料)[M].Beijing:China MachinePress,2004:1
[4]Fan Zhikang(范志康)eta1.The Chinese Journal ofNonferrousMetals(国有色金属学报)[J],2001,11(S1):102
[5]CobleRL.JApp,Phys[J],1961,32:787(793)
[6]Yang Xiaohong(杨晓红)eta1.Rare Meml朋a把砌如and Engin—eering(稀有金属材料与工程)[J],2007,36(5):817
[7]Li Dasheng(李大圣)et a1.Rare Metal Materials andEngineering(稀有金属材料与工程)[J],2007,36(6):1008
18]ZhuAihui(朱爱辉)et a1.China Tungsten Industry(中国钨业)[J],2006,2l(3):39
[9]Li Ying(李英).Journal ofDongguan University of Technology(东莞理工学院学报)[J],2005,12(1):20
[10]Zhang Qixiu(张启修)et aL Tungsten MolybdenumMetallurgy(钨钼冶金)[M].Beijing:Metallurgical IndustryPress,2005:12
[11]Wang Xingang(王新刚)eta1.ChinaTungsten Industry(中国钨业)[J],2007,22(3):28
相关链接