引言
磁控溅射是一种被广泛应用于薄膜制备和表面改性的高效物理气相沉积技术。在磁控溅射过程中,靶材受到离子轰击,产生高能量的离子和中性粒子,从而使靶材表面的原子或分子被剥离并沉积到基底表面,形成所需的薄膜[1]。而溅射靶材的微观结构对于薄膜质量起着至关重要的作用。为了实现所需的薄膜特性,必须精确调节靶材的纯度、相对密度、晶粒尺寸和晶粒取向等因素。金属污染和孔隙存在也会对薄膜电阻率产生不利影响[2]。此外,无择优取向的溅射靶材可用于沉积光滑且连续的薄膜,而较小晶粒尺寸也已被证明可以提高溅射速率[3]。
钨基合金是磁控溅射常用靶材之一,因其具有优良的热稳定性、化学稳定性和机械性能,在先进光学涂层、半导体行业等应用领域中具有重要的地位。因此,钨基合金靶材在先进光学涂层、半导体行业等领域中扮演着至关重要的角色[4]。同时,由于钨及其合金通常具有较高的熔点,因此一般采用粉末冶金来替代传统的熔炼铸造来制备粉末冶金靶材。使用纳米尺寸的颗粒可以提高高熔点金属粉末基烧结体的相对密度。近年来,钨基合金靶材及其磁控溅射薄膜也受到了广泛关注和深入研究,例如:W-Mo靶材[5],W-B靶材[6],W-S[7],W-Cu[8,9]靶材等等。本文介绍了钨基合金靶材的制备方法以及其在磁控溅射薄膜性能和应用领域方面的最新进展。
1、钨基合金靶材的粉末冶金制备工艺
粉末冶金法是制备钨基合金靶材最常见的方法,通常先将钨粉与其他合金粉末按比例混合,然后通过球磨或机械合金化等方法使其均匀混合。随后,将混合粉末置于模具中压制成坯料,最终进行烧结处理以获得靶材。由于烧结方法不同,通常分为热压、热等静压、放电等离子烧结等方式[10]。
1.1热压技术((HP)
热压烧结同时进行加热和加压,使粉料处于热塑性状态,有利于颗粒的接触扩散和流动传质过程,因此成型压力仅为冷压的1/10;同时能降低烧结温度、缩短时间,并抵制晶粒长大,得到晶粒细小、致密度高以及机械、导电性能良好的产品,并且热压烧结可以大概分为真空热压和惰性气体热压两种气氛条件[11,12]。
黄志明等[13]利用平均粒度为7μm的钨硅混合粉末,以10℃.min-1的升温速率,在1200℃的真空热压条件下保温1~3h,成功制备出了组织结构均匀且相对密度≥99%的高纯钨硅靶材。
如图1所示,可以看出靶材的组织结构均匀且无明显孔洞(颜色较浅的区域为WSi2,颜色较深的区域为Si)。Dunlop等[14]采用TiH2粉末与W粉混合,在1350℃、35MPa的真空热压条件下制备了致密度约为99%的W-Ti合金靶材。通过TiH2脱氢时对碳、氧等气体的吸附作用,使总气体含量小于0.085%(质量分数),碳含量少于0.01%(质量分数),从而减少磁控溅射薄膜产生颗粒数量。Wang等[15]运用真空热压烧结技术成功制备了致密度达到97.8%的W-10%Re高纯合金靶材。此外还有Xu等[16]采用热压微波烧结制备钨铜合金,Ma等[17]通过真空反应热压法从元素钨和无定形硼粉末合成四硼化钨。
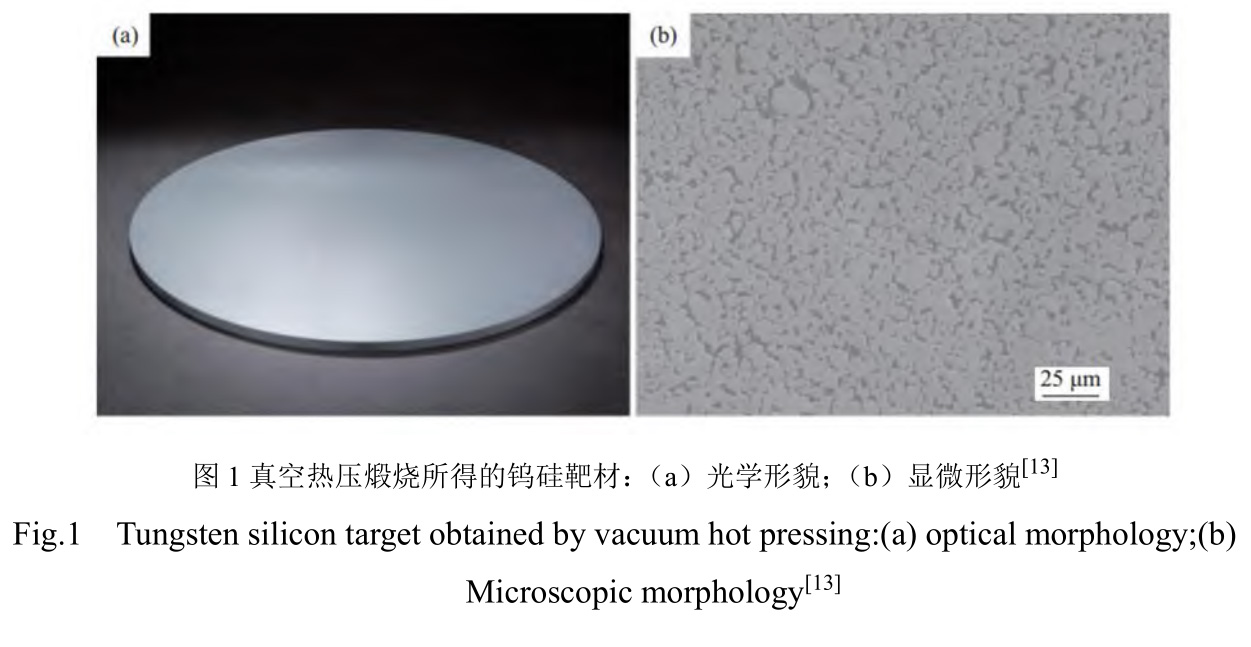
热压烧结具有较高的经济效益,因而成为目前最常用的粉末冶金技术。上述研究表明,通过热压烧结所得到的钨基合金靶材大多具有较高的致密度和较均匀的组织结构,所以目前商业化的钨基合金靶材大多都是通过热压技术制备和生产的。
1.2热等静压技术((HIP)
热等静压技术(HotIsostaticPressing,HIP)是一种高温高压制备工艺,其主要用于制造高性能金属、陶瓷和复合材料等工程材料[12]。该技术通过将待加工的材料置于高温高压下,并实施均匀的加压和温度控制,使得材料在压力和温度作用下达到等静压状态。在这种状态下,材料内部的气孔、微裂纹和其他缺陷会被均匀地压实和填充,从而提高了材料的密度和均匀性[18]。
Wickersham等[19]利用热等静压(HIP)技术制备了钨钛合金靶材,并在高压条件下发现,温度超过885℃会导致富含钛相的形成。对于在885℃至740℃温度范围内制备的靶材,富含钛相的生成取决于具体的加工工艺。当温度低于740℃时,不会形成富含钛相,并且靶材密度接近100%。此外Hu等[20]研究了热等静压工艺参数对钨合金性能和断裂行为的影响,Li等[21]通过喷雾干燥技术和热等静压制备了接近理论密度(99.69%)和高电导率(86.78%IACS)的Cu-20%(质量分数)W(Cu-20W)复合材料。
综上所述,由于HIP制备钨基合金靶材需要严格的高压条件和较高生产成本,因此大多数情况下仍停留在实验阶段而未能实际应用于生产。
1.3放电等离子烧结技术((SPS)
放电等离子烧结(SPS,SparkPlasmaSintering)技术是一种高效的粉末冶金制备技术,它是一种结合了电热效应和机械效应的新型压固工艺,能够在相对较短的时间内实现高密度、高强度的材料制备[12];该技术主要原理是利用电流在导电材料中产生的局部加热效应,结合机械压力,实现材料的快速烧结和致密化[22]。
Mo-W合金非常适合电子、纳米技术、传感器和TFT-LCD栅电极的应用[23],但是熔炼法不适用于熔点较高的金属和金属合金,例如Mo、W及其合金[24],所以Kim等[5]利用SPS技术在1400℃条件下制备出了高纯度钨钼合金靶材,其致密度高于99%。研究发现,使用Mo和W高能球磨的纳米粉末制备的样品相对密度较低,分别为97.04%、97.17%和98.55%,而氧化物还原的纳米粉末制备的样品在相同温度下表现出更高的烧结相对密度分别为98.21%、99.28%和99.62%。图2展示了氧化物还原粉末制备并在1300℃以上烧结后的压坯具有光滑晶界和致密微观结构。
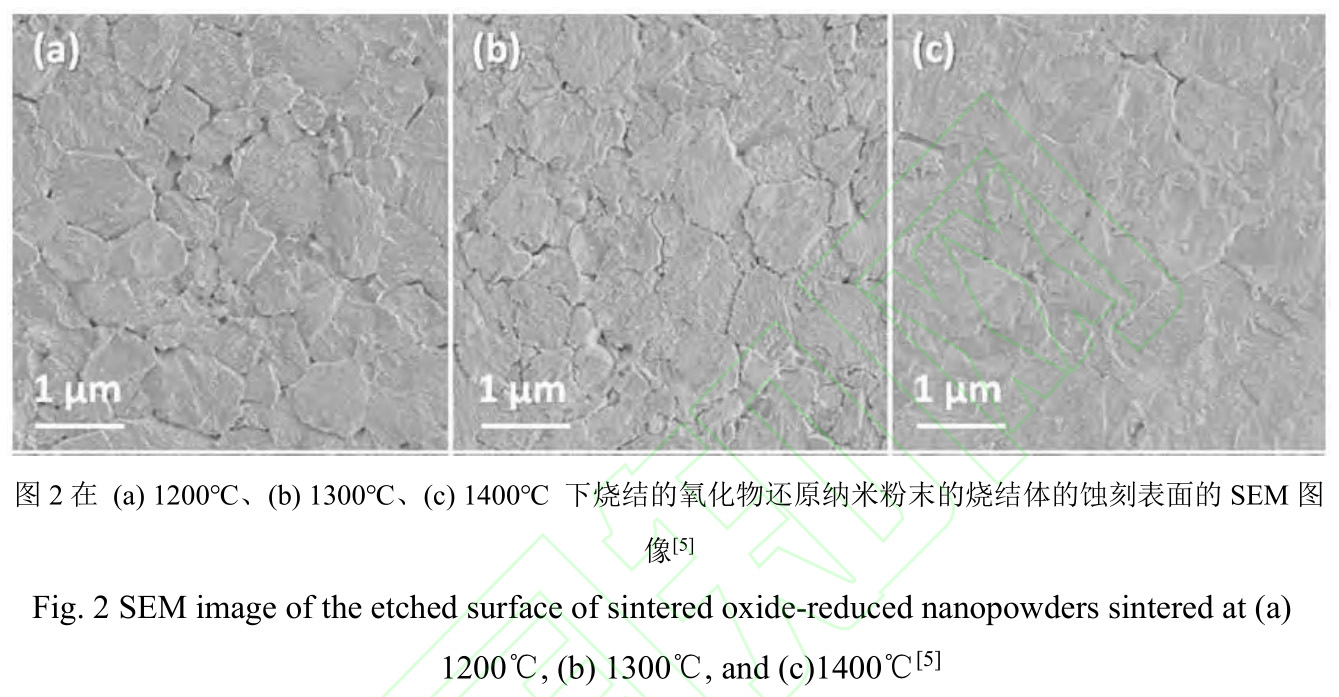
综上所述,由于目前SPS在钨基靶材的制备中相关研究较少;需制备的靶材尺寸越大,对SPS设备的压力和功率要求也越高,因而采用SPS规模生产溅射靶材受设备限制的情况尚待解决。
从现有的研究发现,无论是SPS还是HIP,目前由于其较高的使用成本或是较为严苛的使用条件,暂时都还无法大规模的用于工业生产,相较于这两种制备方法HP经过了数十年的发展已经十分完善,其经济效益都相对较高,但同时也是由于其多年的发展,通过其制备的靶材很难有太多的创新及改善。所以笔者认为未来钨基合金靶材的发展的未来还是在于新型的工艺技术,将会有更多先进的工艺如增材制造(3D打印)[25,26]、等离子烧结[27]等应用于钨基合金靶材的制备中。
2、磁控溅射薄膜的应用及特性
磁控溅射技术是在20世纪60年代和1970年代开发的,此后一直是等离子体溅射沉积的主要方法。多年来,磁控溅射技术不断发展,以增加金属电离、提高靶材利用率、避免反应溅射中的靶材中毒、提高沉积速率,并最大限度地减少电弧的电不稳定性,并降低运营成本[28]。功能性涂层和层状结构需求持续增长,促使整体质量和功能不断提高。溅射沉积工艺的发展得到推动,因为需要提高溅射源利用率、沉积薄膜均匀性、实现金属定向沉积以及满足控制需求。离子轰击基材能量影响成膜材料,而磁控溅射已成为广泛应用于工业中的重要技术[29]。
2.1钨基合金薄膜的应用领域
2.1.1W-Ti/CoW无扩散屏障材料
集成电路(IntegratedCircuit,IC)是一种微型电子器件,它将大量的电子元件(如晶体管、电阻、电容等)集成到一个单一的半导体芯片上,通过特定的电路连接方式实现了各种功能,例如放大、逻辑运算、存储和控制等[30]。磁控溅射钨基合金薄膜在半导体集成电路中具有多种重要应用,用于连接、阻抗调节、电极结构和介电层等方面,对于提高集成电路的性能、稳定性和可靠性具有重要意义[31]。
目前,含Ti量为10%(质量分数)~30%(质量分数)的W-Ti合金已成功应用于Al、Cu和Ag布线技术[19]。作为扩散阻挡层材料,W-Ti薄膜不仅可稳定扩散阻挡层,还可以作为反应型扩散阻挡层。它与硅有良好的粘附性,并且对Cu的扩散阻挡作用尤为明显[32]。
Guidi等[33]利用W-30%Ti靶材,采取磁控溅射方式在导电金属Ag和基体Si之间镀了一层W-Ti薄膜,并进行了热处理。观察到以下现象:温度接近700℃时,薄膜中的银原子开始大量聚集,并导致了硅的生成,从而使薄膜的电阻系数迅速增加。这表明,W-Ti薄膜不仅在低温下有效阻挡了银布线与单晶硅之间的扩散,而且还展现出潜在的高温应用价值。同时,Su等[34]发现50%(质量分数)的CoW合金磁控溅射薄膜具有与目前主流铜互连中的扩散屏障材料TaN相似的抗扩散能力和润湿能力,并且在CoW薄膜上接近70nm的孔洞也满足Cu在其上面的镶嵌要求,表明其可能作为下一代Cu互连单层无籽势垒的有前途候选者。
如图3所示,在CoW衬底上初始阶段核密度高于Ta、TaN或W衬底,并且随电镀时间增加呈均匀变化。因此,在这种情况下可以在CoW基板上实现连续且光滑的Cu膜。
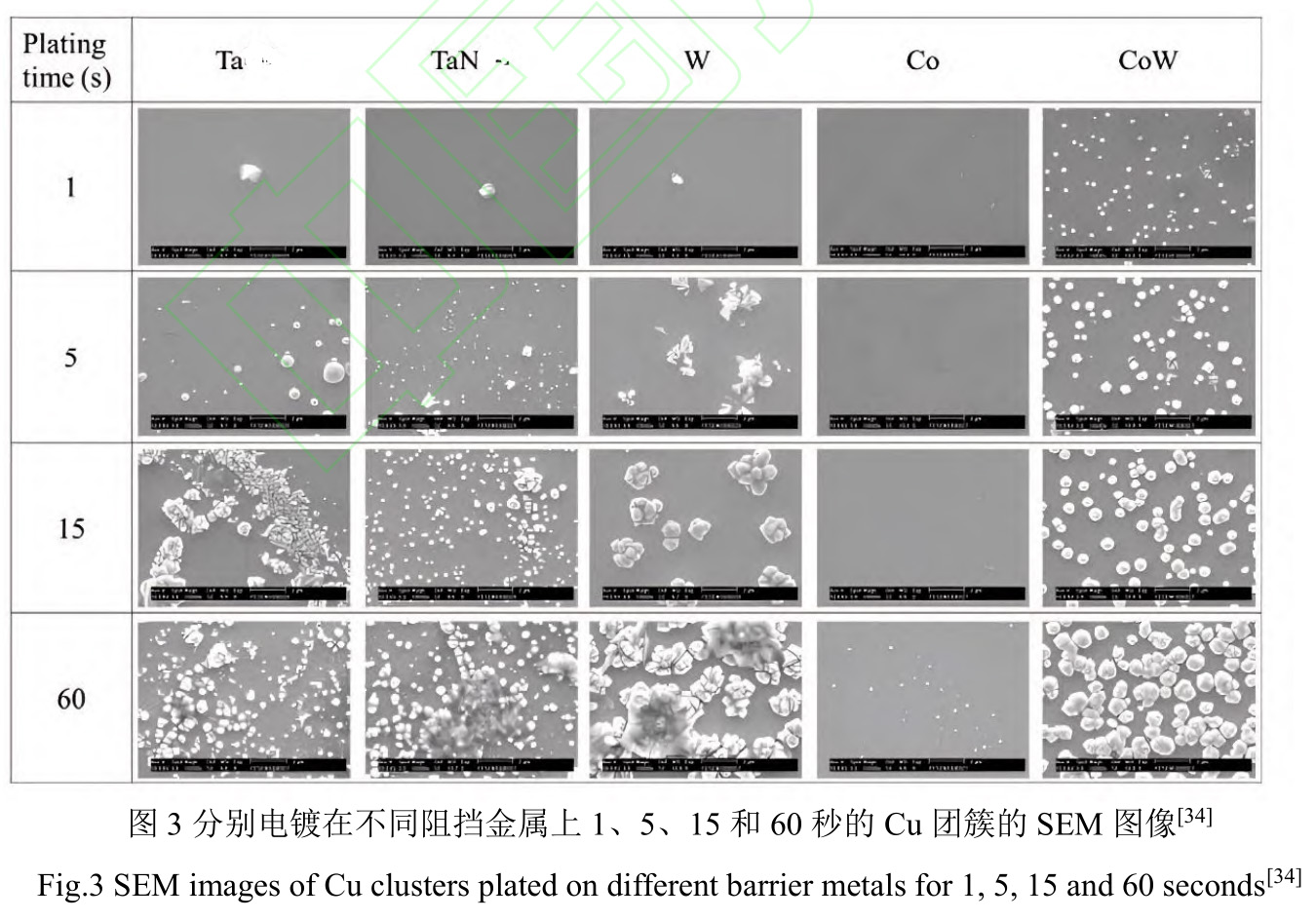
综上所述,由于钨具有较强抗原子扩散的能力,目前的研究中大多都是以钨为基体应用于集成电路的抗扩散阻挡层材料,添加的其它元素大多起到增加粘附性的作用,有些元素也起到少量的抗扩散作用例如Ti等[34]。
2.1.2W-Si超导材料
超导材料是一类在低温下表现出超导现象的材料。当这些材料被冷却到临界温度以下(即超导临界温度)时,其电阻突然变为零,并呈现完全的电子输运现象[35]。钨(W)和硅化钨(WSi2)具有低电阻率、抗应力迁移和强电迁移能力等优点,因此成为当前研究的热点。Suzuki等人[36]利用低压化学气相沉积(LPCVD)方法,使用六氟化钨(WF6)和硅烷(SiH4)制备的W薄膜显著提高了超导转变温度。随后Kondo[37]通过磁控溅射技术和热扩散技术成功制备出W-Si和W-Ge非晶超导薄膜,使用LPCVD时,膜在高达354°C的温度下沉积,并表现出超导性。同时发现溅射和热扩散对于获得具有高热稳定性的非晶态W-Si也是有效的,并且分析了W-Si和W-Ge薄膜中准金属含量与电子特性和晶体结构的关系。这些材料不仅适用于现有超大规模集成电路(ULSI)应用,也适用于未来大规模集成超导晶体管的材料。
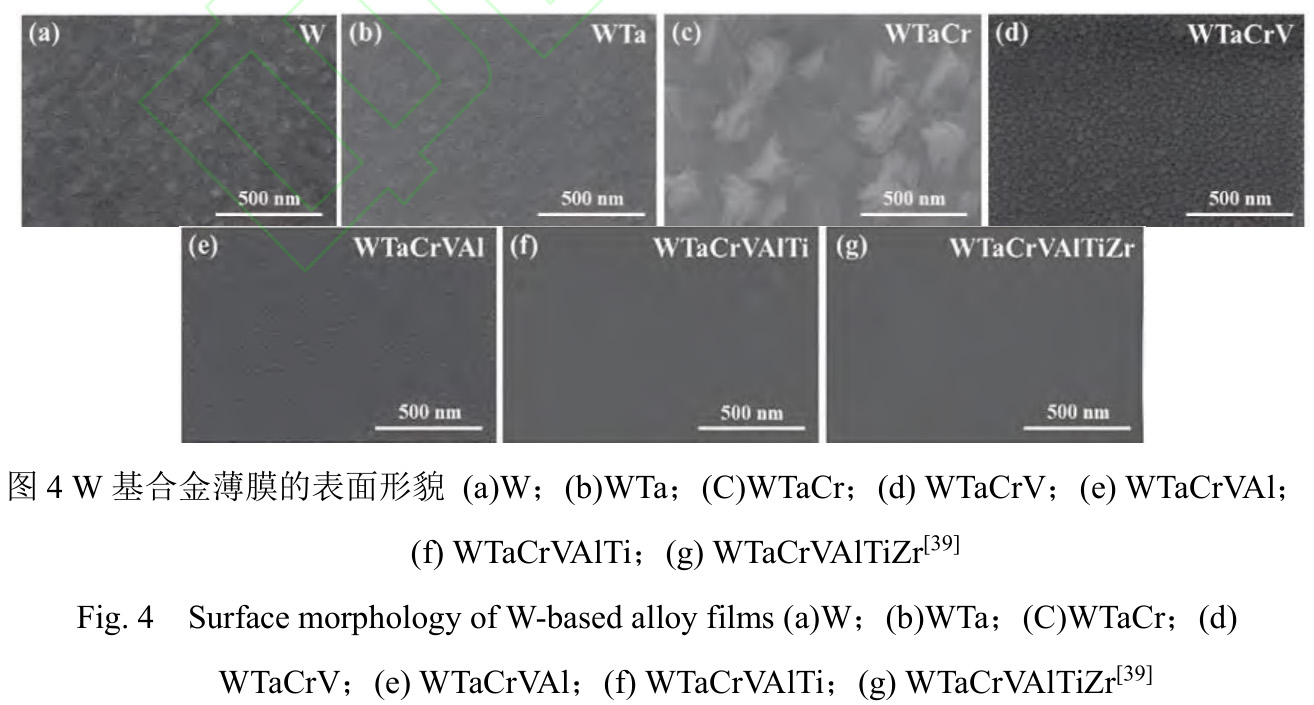
2.1.3WTaCrVAlTiZr面向等离子体材料((PFM)
等离子体材料的研究和开发对核聚变能、等离子体物理研究以及等离子体喷涂技术具有重要意义。面向等离子体材料是指用于等离子体物理研究和应用的材料,其特性和性能在等离子体环境中起着关键作用[38]。钨因其高熔点、低热膨胀系数、高电阻率和低中子活化而被视为未来聚变装置中最重要的面向等离子体材料(PFM)候选材料[39],同时高温抗氧化性是PFM的重要安全标准,自钝化钨合金和表面涂层保护技术可以使钨合金具有优异的抗氧化性和耐腐蚀性。Zhang等[39]人利用磁控溅射技术成功制备了一系列连续添加元素的W基合金薄膜。实验结果显示,当合金中加入Al和Ti时,其抗氧化能力显著提高。此外,Zr元素可显著增强镀层的抗氧化性能、提高膜层附着力,并改变其生长机制以降低氧化速率。同时WSi2涂层呈现出致密且典型的双层微观结构,具有显著的抗氧化性能。
2.1.4W-B硬质涂层
刀具的硬质涂层是一种将优异硬度和耐磨性材料覆盖在刀具表面以增强其性能的技术。这些涂层通常由碳化钨(WC)[40]、氮化钛(TiN)、氮化铝(AlN)[41]、碳化硅(SiC)等硬质材料制成[42],被广泛应用于钻头、铣刀、车刀、切削工具等,以提高其性能和使用寿命。
Chrzanowska等[43,44]观察到了相似的特性,他们研究了平面不锈钢基材上αWB涂层的摩擦系数和耐磨性。通过射频磁控溅射(RFMS)沉积的αWB薄膜具有良好的附着力。Jiang等人[45]表明,直流磁控溅射(DCMS)制备出具有亚稳态AlB2型结构的αWB2涂层,其纳米复合材料结构表现出约43.2±5GPa的超硬度。Radziejewska等[46]在商用WC-Co切削刀片上通过射频磁控溅射沉积了WBx和(W,Ti)B2涂层,如图5所示。在难切削304不锈钢车削试验中,W-B涂层刀具比未涂层刀具表现出更好的耐磨性,并且与未覆盖WC-Co刀片相比,覆盖W-B薄膜后刀面磨损量减少了30%,此外,在测试条件下保护了边缘碎裂情况发生。
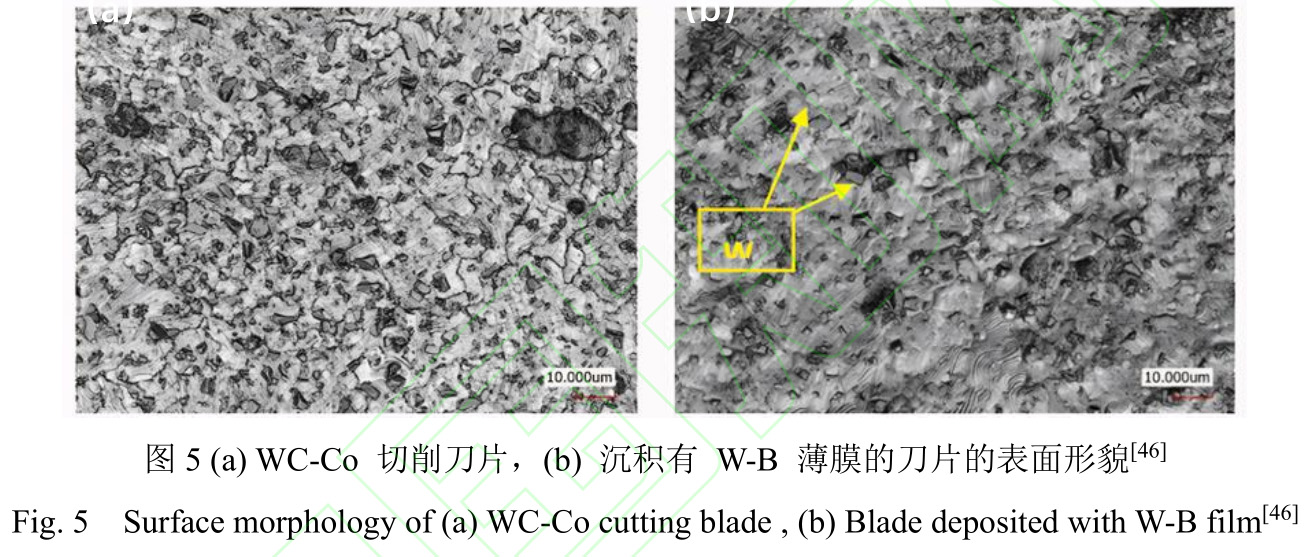
2.2钨基合金薄膜的性能分析
2.2.1抗扩散性能
钨基合金薄膜主要应用于电子器件、半导体和集成电路板等领域。其中,钨基合金薄膜的关键性能在于其抗扩散特性。由于钨元素具有高熔点、低扩散系数、稳定晶体结构和化学惰性等特点;因此,使得钨基合金薄膜在高温环境下能够保持较好的结构稳定性,并且具有抵抗扩散现象的特点[47]。目前在抗扩散领域,磁控溅射的WTi合金薄膜是应用最广泛[32]。
其中,钨起主要的抗原子扩散作用,钛则主要加强薄膜的耐腐蚀性能。此外,还有用于铜互连应用的磁控溅射CoW薄膜[3]。钨元素增强了对铜的抗扩散能力,并且可以抑制薄膜的氧化和损坏。如图6所示,随着钨含量增加,失效温度也相应提高。失效温度升高意味着优异的抗扩散能力,因为铜在达到扩散温度之前会更长时间保持稳定状态;而作为铜粘附层的钴表现出良好粘结性能。
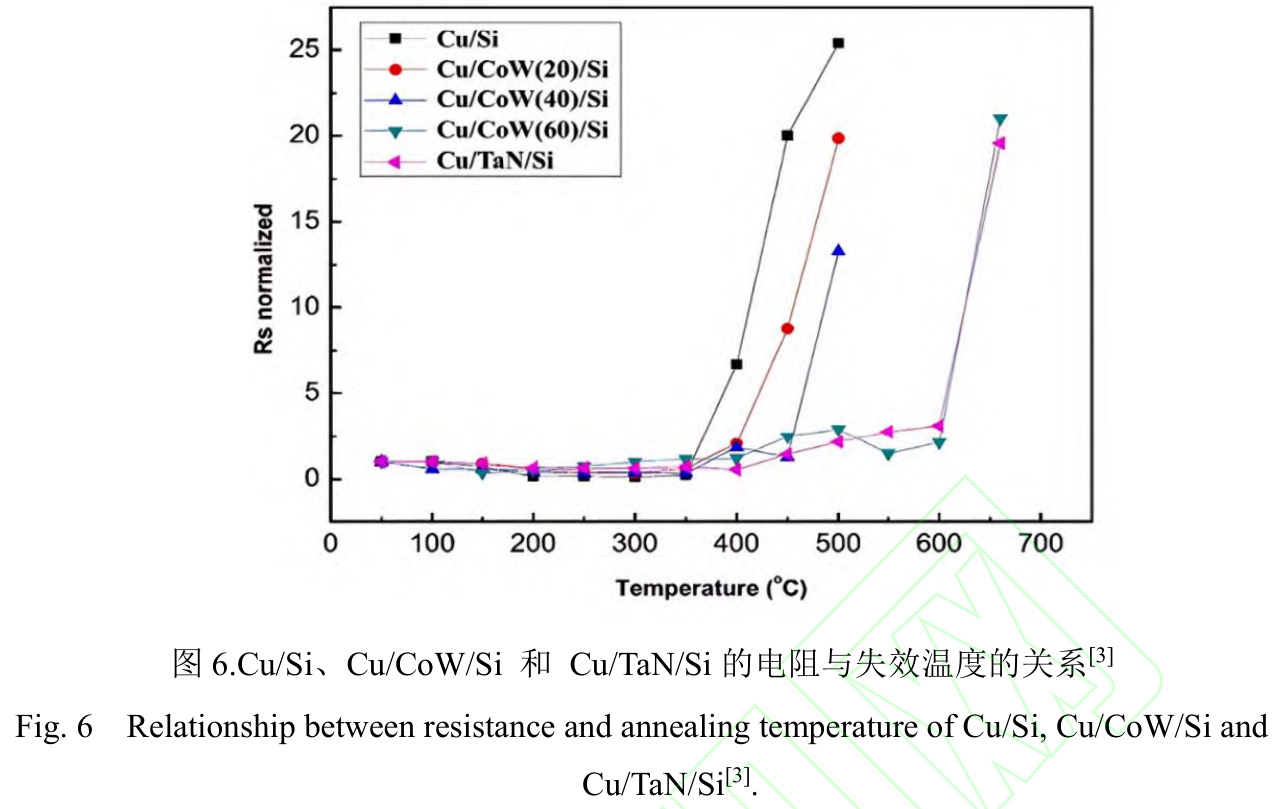
2.2.2摩擦磨损性能
磁控溅射制备的钨基合金薄膜具有高硬度、低摩擦系数、耐高温性和化学惰性等优异的摩擦磨损性能,例如W-N[48]、W-Zr[49]、W-B[50]等。Jiang等人[45]磁控溅射所制备的W-B薄膜具有亚稳态AlB2型结构的直流磁控溅射αWB2涂层表现出约43.2±5GPa的超硬度。在这种情况下,滑动过程中测得的稳态摩擦系数为0.23,薄膜的磨损率为6.5×10−6mm3·N−1·m−1,表明其具有优异的摩擦磨损性能。Euchner等[51]发现通过磁控溅射在整个成分范围内沉积的Ti1−xWxB2−z固溶体薄膜均以AlB2结构类型结晶,并且表现出良好的热稳定性和40GPa左右的高硬度。同时Smolik等[52]观察到添加10%(质量分数)钨元素可使二硼化钛涂层断裂韧性KIC增加7倍以上,从KIC(TiB2)=0.67增加到KIC(TiBW)=4.98MPa·m1/2。与TiB2涂层相比,Ti-B-W薄膜具有更高的硬度(400mN载荷下H=38GPa)和相似的表面粗糙度。
此外,在文中提及了W-B薄膜耐磨性优于Ti-B-W薄膜,如表1所示。
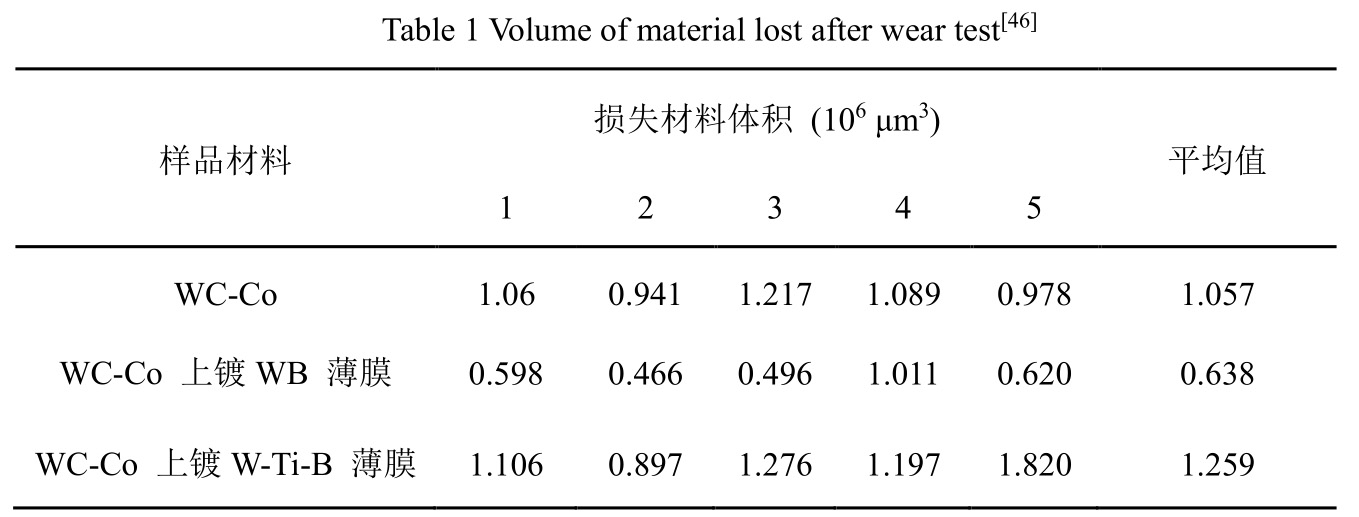
从以上可以看出钨作为高硬度,低摩擦系数的金属,以其合金作为靶材所制备出的薄膜同样也拥有着优异的摩擦磨损性能,从中可以看出使用它们来保护难加工材料的WC-Co切削刀具的可能性。
2.2.3抗腐蚀氧化性能
在过去几十年中,针对机械应用的钨基合金硬质涂层进行了大量研究。除了具有非常高的硬度和附着力外,钨基合金涂层还需要具备抗腐蚀性和抗氧化性,在使用温度达到数百摄氏度时不会失效[53]。例如,WSi2磁控溅射涂层呈现出致密且典型的双层微观结构,其优异的抗氧化性能源于表面致密、光滑[54]。Louro等人[50]对W-N-M(M=Ni和Ti)溅射涂层的沉积和氧化行为进行了详细分析,发现W-Ti薄膜良好的抗氧化性归因于在氧化层晶界中以非常细小的颗粒形式形成TiO2,这有助于阻碍氧离子向内扩散。另一方面,对于含镍薄膜,如果Ni含量足够高以促进足够厚的NiWO4层,则NiWO4尖晶石型相外层的形成可以产生优异的抗氧化行为。Zhang等[39]采用磁控溅射方法制备了一系列连续添加元素的W基合金薄膜。从图7和图8可以看出,随着元素数量增加,W基合金薄膜表面形貌逐渐变得光滑,并且其耐酸碱的腐蚀性和抗氧化性也逐渐提高。
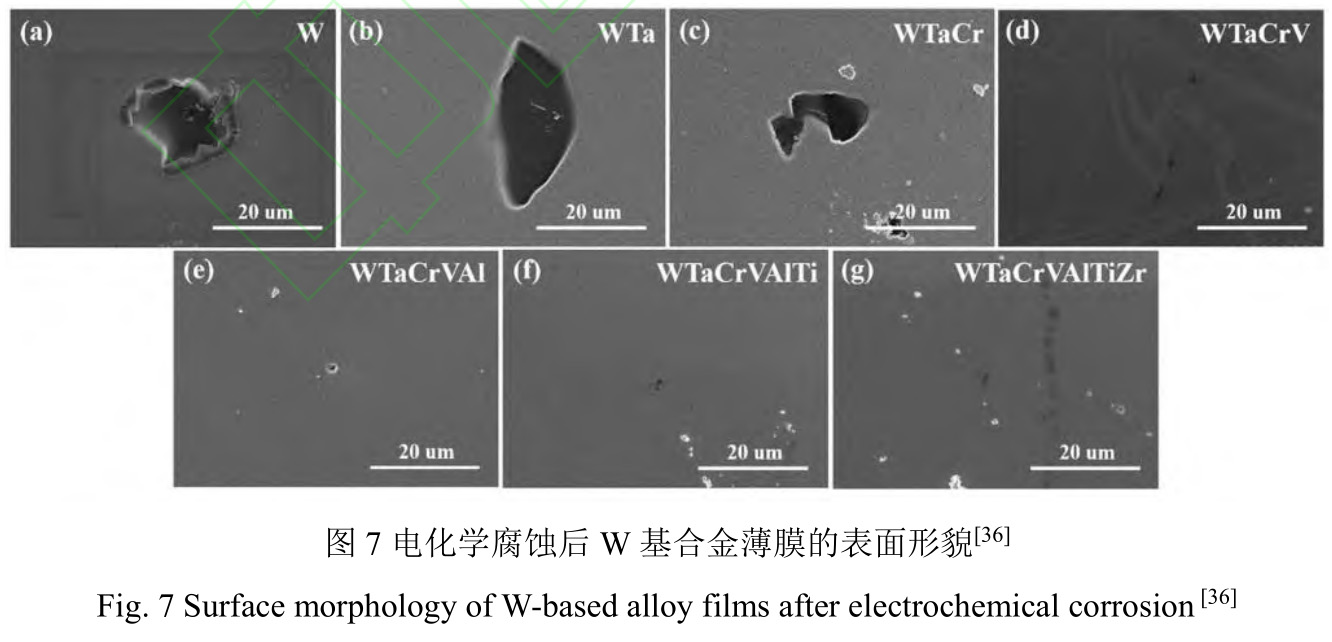
综上所述,随着元素数量的增加,膜层的耐腐蚀性和抗氧化性逐渐提高。混合熵的增加降低了吉布斯自由能,使钨基合金更加稳定,是耐腐蚀性和抗氧化性同时提高的重要原因之一。此外,Cr、Al、Ti、Zr元素具有较强的钝化作用,易于形成致密的氧化膜,这也是提高耐蚀性和抗氧化性的重要原因。这也使得未来钨基合金薄膜作为硬质涂层拥有广阔的发展前景。
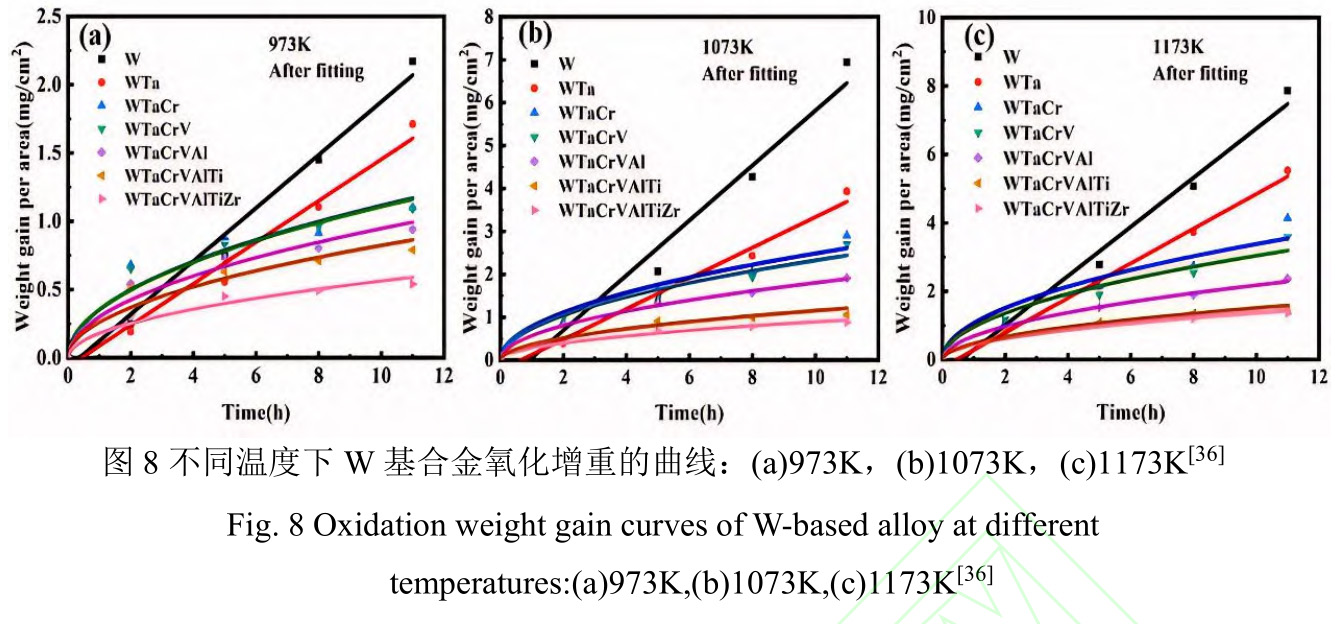
3、展望
磁控溅射钨基合金薄膜具有优异的抗扩散性能、摩擦磨损性能、抗腐蚀氧化性能等多项优异性能,使其在集成电路、硬质合金涂层和等离子材料方面具有重要应用和研究价值。我国近年来加快了对钨基合金合金靶材的研究与应用,虽然目前真空热压仍然是是钨基合金靶材的主要制备技术,但也有一些在此领域还少有研究的技术(如SPS技术)用于钨基合金靶材的制备研究。
未来主要的发展方向有几个,首先是制粉,粉末的晶粒大小直接影响其烧结合金的多项性能,例如合金的致密度,导电性能,硬度等等。同时提升所制备粉末的纯度也是一个重要的发展方向;其次是烧结工艺的改进,目前新型烧结工艺主要的问题还是在于到达所需致密度的烧结条件较为苛刻,而致密度又严重影响着其磁控溅射薄膜的连续性;最后,计算模拟和智能制造技术的应用,将进一步提高钨基合金靶材的生产效率和产品一致性。通过计算机仿真技术,可以优化工艺参数和产品设计,缩短研发周期;通过智能制造系统,可以实现生产过程的实时监控和调控,提高生产的自动化和精确度。
4、结语
本文论述了近年来钨基合金靶材主要的以及新兴的制备方法,并从其磁控溅射薄膜的性能出发介绍了其几种主要的应用领域。相信在未来,随着超纯粉体生产能力的提升和靶材制备工艺和设备的升级,粉末冶金法制备的钨基合金溅射靶材的纯度、致密度和性能将持续提高,在电子器件、硬质涂层等领域的应用前景将更加广阔。
参考文献
[1] GUDMUNDSSON J T. Plasma Sources Science and Technology, 2020, 29(11).
[2] CHELVANATHAN P, SHAHAHMADI S A, ARITH F, et al. Thin Solid Films, 2017. DOI:10.1016/j.tsf.2017.07.057
[3] REZA M, SAJURI Z, YUNAS J, et al. IOP Conference Series: Materials Science and Engineering, 2016. DOI: 10.1088/1757-899x/114/1/012116
[4] WANG Q X, LIANG S H. Vacuum, 2011.85(11), 979
[5] KIM S, KWON T, KIM S, et al. International Journal of Refractory Metals and Hard Materials,2024, 118.
[6] IVANOV E, DEL RIO E. International Journal of Refractory Metals and Hard Materials, 2018,72: 223-7.
[7] GELLERUP S, ARNOLD C L, CAIRNS E, et al. Vacuum, 2023, 213.
[8] AI Y-P. Chemical Physics Letters, 2017, 690: 1-4.
[9] AMIRJAN M, ZANGENEH-MADAR K, PARVIN N. EInternational Journal of Refractory Metals and Hard Materials, 2009, 27(4): 729-33.
[10] LI Z-B, ZHANG H, ZHANG G-H, et al. Metallurgical and Materials Transactions A, 2022,53(3): 1085-98.
[11] GERMAIN F S, SLOSARIK S E. JOM, 1962. DOI: 10.1007/bf03378159
[12] Manikandan R, Raja Annamalai A. Materials Today Communications, 2024,39.
[13] Huang Z M,Wang D Z,Wu Z Z, et al. Powder Metallurgy Technology,2021 39(05): 445-51. (in Chinese)
黄志民, 王德志, 吴壮志, et al. 粉末冶金技术 . 2021, 39(05): 445-51.
[14] DUNLOP J A, RENSING H. U.S. patent application, US4838935,1989.
[15] WANG Y M, TANG Q H, ZHOU P. Journal of Materials Engineering and Performance, 2021,30(10): 7223-35.
[16] XU L, SRINIVASAKANNAN C, ZHANG L, et al. Journal of Alloys and Compounds,2016,658,23.
[17] MA K, CAO X, YANG H, et al. Ceramics International, 2017,43(12),8551.
[18] BYUN J M, LEE E S, HEO Y J, et al. International Journal of Refractory Metals & Hard Materials, 2021,99, 105602.
[19] WICKERSHAM C E, POOLE J E, MUELLER J J. Journal of Vacuum Science & Technology A: Vacuum, Surfaces, and Films, 1992, 10(4): 1713-7.
[20] HU B, CAI G. Materials, 2022, 15(23), 8647.
[21] LI X, WANG Q, WEI S, et al. Journal of Alloys and Compounds, 2023, 975, 172571.
[22] DINE S, BERNARD E, HERLIN BOIME N, et al. Advanced Engineering Materials,2018,20(8), 1701138
[23] WANG Y, TANG Q, CHEN D, et al. Journal of Thermal Spray Technology, 2019, DOI:10.1007/s11666-019-00958-x.
[24] HAO Y, TAN C, YU X, et al. Journal of Alloys and Compounds, 2020, 819, 152975.
[25] MüLLER A V, DOROW-GERSPACH D, BALDEN M, et al. Journal of Nuclear Materials,2022.
[26] TALIGNANI A, SEEDE R, WHITT A, et al. Additive Manufacturing, 2022,566.
[27] KIM J Y, LEE E S, HEO Y J, et al. Powder Metallurgy, 2023,66 (5) , 644
[28] WANG Y, TANG Q, CHEN D, et al. International Journal of Refractory Metals & Hard Materials, 2019,87.
[29] ENGWALL A M, SHIN S J, BAE J, et al. Surface & Coatings Technology, 2019,363,191.
[30] PAULEAU Y. Thin Solid Films, 1984, DOI: 10.1016/0040-6090(84)90051-8
[31] BHAGAT S, HAN H, ALFORD T L. Thin Solid Films, 2006, 515 (4) , 1998
[32] LO C-F, GILMAN P. Journal of Vacuum Science & Technology A: Vacuum, Surfaces, and Films, 1999, 17(2): 608-10.
[33] GUIDI V, BOSCARINO D, COMINI E, et al. Sensors and Actuators B: Chemical, 2000, 65(1):264-6.
[34] SU Y-H, KUO T-C, LEE W-H, et al. Microelectronic Engineering, 2017, 171: 25-30.
[35] LAZARIDES N, TSIRONIS G P. Physics Reports, 2018, 87 (3).
[36] SUZUKI M, KOBAYASHI N, MUKAI K, et al. Journal of The Electrochemical Society ,1990,137(10): 3213.
[37] KONDO S. Journal of Materials Research, 1992. DOI: 10.1557/jmr.1992.0853
[38] NISHINO N. Carbon, 1997. DOI: 10.1016/s0008-6223(97)82814-x
[39] ZHANG W, QI Y, ZHANG L, et al. Surface and Coatings Technology, 2022, 434.
[40] PERO R, MAIZZA G, MONTANARI R, et al. Materials, 2020,13 (9).
[41] ZHOU Z, XU Y, CHEN X, et al. Ceramics International, 2020,46 (4) , 4095.
[42] YUMASHEV A, MIKHAYLOV A J P C. Polymer Composites, 2020, 41(7): 2875.
[43] CHRZANOWSKA J, KURPASKA Ł, GIŻ YŃSKI M, et al. Ceramics International, 2016,42 (10) , 12221.
[44] CHRZANOWSKA-GIŻ YŃSKA J, DENIS P, WOŻ NIACKA S, et al. Ceramics International,2018,44 (16) , 19603.
[45] JIANG C, PEI Z, LIU Y, et al. Physica Status Solidi (A) - Applications and Materials Science,2013,210 (6) , 1221.
[46] RADZIEJEWSKA J, PSIUK R, MOŚ CICKI T. Coatings, 2020, 10(12).
[47] MAHJABIN S, HAQUE M M, BASHAR M S, et al. Energy & Fuels, 2023, 37( 24), 19860.
[48] YU H, YANG X, XIAO X, et al. Advanced Materials, 2018, 30 (51).
[49] Č ERVENá M, Č ERSTVý R, DVOŘ áK T, et al. Journal of Alloys and Compounds, 2021, 888.
[50] SADOVSKIY Y, BEGRAMBEKOV L, AYRAPETOV A, et al. Journal of Physics: Conference Series, 2016, 748.
[51] EUCHNER H, MAYRHOFER P H, RIEDL H, et al. Acta Materialia, 2015, 101 , 55.
[52] SMOLIK J, KACPRZYŃSKA-GOŁACKA J, SOWA S, et al. Coatings, 2020, 10 (9).
[53] LOURO C, CAVALEIRO A. Journal of The Electrochemical Society, 1997, DOI:10.1149/1.1837394.
[54] SERDOBINTSEV A A, STARODUBOV A V, KOZHEVNIKOV I O, et al. Journal of Physics:Conference Series, 2020, 1697(1).
李锐,2023 年 9 月于昆明理工大学获得工学学士学位。现为昆明理工大学材料科学与工程学院硕士研究生,在刘意春教授的指导下进行研究。目前主要研究领域为金属靶材及表面工程。
赵琪,昆明贵金属研究所助理研究员。2022 年中南大学材料科学与工程专业博士毕业,2022 年博士毕业后到贵金属研究所工作至今。目前主要从事金属靶材和金属基
复合材料等方面的研究工作。发表论文 20 余篇,包括 Materials Science and Engineering: A , Journal of Alloys and Compounds, Diamond and Related Materials,Journal of Materials Research and Technology 以及 Applied Surface Science 等。
刘意春,昆明理工大学材料科学与工程学院教授、博士研究生导师。2001 年 7 月上海交通大学材料科学与工程专业本科毕业,2011 年上海交通大学材料学专业博士毕业后到昆明理工大学工作至今。目前主要从事粉末冶金和金属基复合材料等方面的研究工作。发表论文 100 余篇,包括 Materials Science and Engineering: A , Materials Characterization, Diamond and Related Materials, Journal of Materials Research andTechnology 等。
无相关信息