金属钼凭借其高导电率、 高温稳定性以及绿色环保等优点, 被广泛应用于电子、 光伏等领域,并主要以薄膜的形式用作电极层以及配线阻挡层材料。钼薄膜大多通过真空蒸镀、 磁控溅射这类物理气相沉积方法获得, 钼靶材作为沉积源, 其纯度、 致密度、 粒径及取向分布直接决定薄膜的溅射效率和成型质量[1-2] 。
钼是一种高熔点(2620 ℃)金属, 通常采用粉末冶金的工艺将其烧结成钼制品, 然而烧结钼的孔隙率高、 致密度差、 各向同性, 无法满足优质钼靶材的需求, 因此有必要通过如轧制锻造等热变形处理提高钼靶材的致密度和织构度。Oertel等[3-4] 指出单向轧制会产生不完整的α织构, 随着轧制变形量的增加, 其最高强度的织构从{100}<110>转变为{112}<110>; 尤世武[5] 研究发现冷轧钼板在30%~60%的变形量时形成α织构, 70%~80%的变形量时形成γ织构, 变形量达到90%时(001)型织构减弱而(111)型织构增强。由于轧制使晶粒变形, 通常需要回复再结晶使晶粒均匀化[6] 。
Chaudhuri等[7] 发现<0 0 1>织构在动态再结晶期间会增强。本研究以钼靶烧结熟坯为原料, 通过探索不同变形量的单向轧制, 再结合系列温度退火工艺, 最后利用精密测量、 金相观察、 扫描电镜(SEM)、 X射线衍射(XRD)、 电子背散射衍射(EB⁃SD)等方法表征成品的理化性能和组织特征, 揭示钼靶材制备工艺与组织性能的关系, 为制备高性能钼靶材提供实验依据和技术指导。
1、 实 验
本研究用于轧制的原料是通过烧结得到的钼靶材熟坯。为确保轧制时具有良好的成型性效果, 熟坯致密度应大于95%。
首先将一级钼粉(费氏粒度3 µm)通过冷等静压压制成生坯, 生坯再经过2000 ℃高温烧结得到钼靶熟坯, 其相关性能见表1, 烧结熟坯的XRD衍射图谱如图1所示。随后采用氢气加热炉对钼靶加热, 加热至轧制温度后进入两辊轧机轧制。每一道次的轧制加工(包括开坯和热轧)需要加热至相应的温度。第一道次开坯温度为1300 ℃, 开坯变形量为25%左右; 开坯后, 继续将样品放进加热炉, 加热至 1200 ℃。每次轧制变形量为 15% 左右, 轧制1~2次后进加热炉保温, 并以此循环轧制到目标变形量。
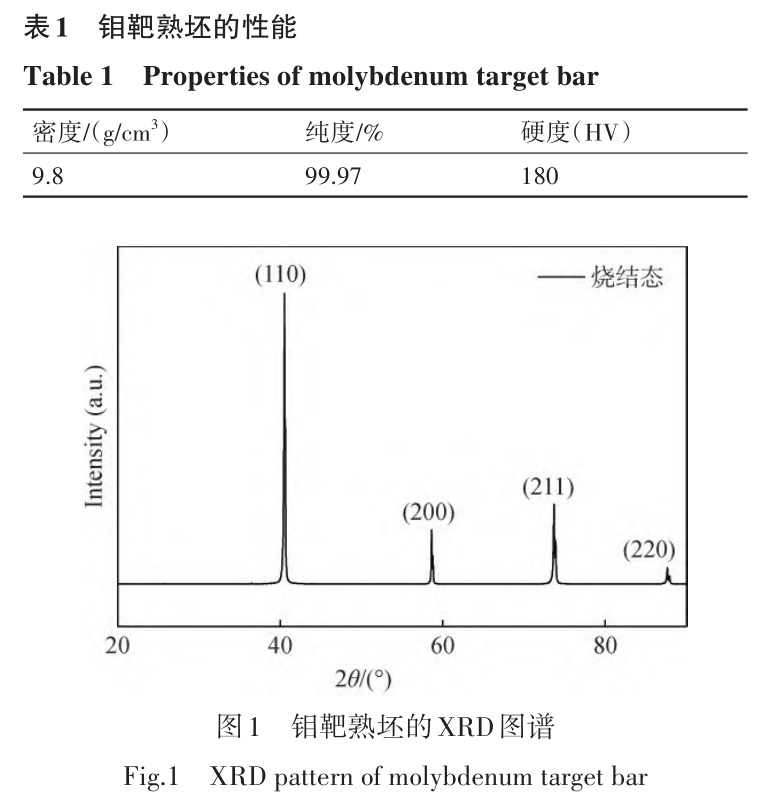
本研究设定目标厚度均为10 mm, 基于此设计了轧制变形量60%~90%的5组实验, 轧制方式均为纵向单向轧制, 轧制实验组见表2。利用真空退火炉对轧制态钼靶进行热处理, 保持真空度<5 Pa, 将轧制变形量 85% 的靶材试样分别在 900,1000, 1100, 1200 ℃下退火 1 h, 研究退火温度对钼靶组织性能的影响。
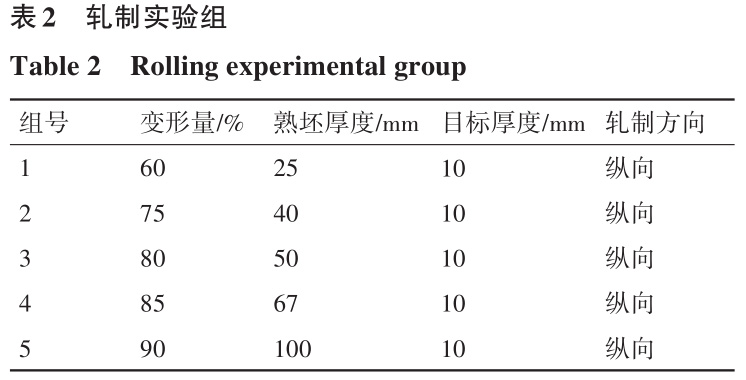
本实验采用德国Bruker公司的D8 Advance型X射线衍射仪采集样品的XRD衍射图谱, 采用日本奥林巴斯公司的OLS5000型激光共聚焦显微镜观察钼靶材金相组织, 采用美国赛默飞的Apreo hi⁃vac型场发射SEM的(EBSD)组件获取靶材的晶粒取向。电解抛光法制备EBSD样品工艺如下: 将表面无划痕的金相样在10%硫酸乙醇溶液中通入直流电, 加载电压为10 V, 电流为1 A, 在室温下电解抛光15 s。
2 、结果与讨论
2.1 轧制变形量对显微组织的影响
在物理气相沉积过程中, 钼靶材中的钼原子倾向于沿着晶体密排方向向靶材表面逃逸, 钼块体的结晶方向直接关乎溅射速率和溅射膜层厚度的均匀性。因此, 钼靶材的结晶取向调控是需要突破的关键技术环节。研究发现, 制备最利于成膜的钼靶材织构取向{100}<011>存在诸多难点, 其中, 热变形钼板的再结晶组织控制因素较为多元, 主要矛盾尚未明晰, 在热处理条件基本一致的前提下, 主要影响因素有轧制温度、 变形率、 轧制方向和轧制方式等, 且表层和中间层织构特征也存在明显差异[8-11] 。
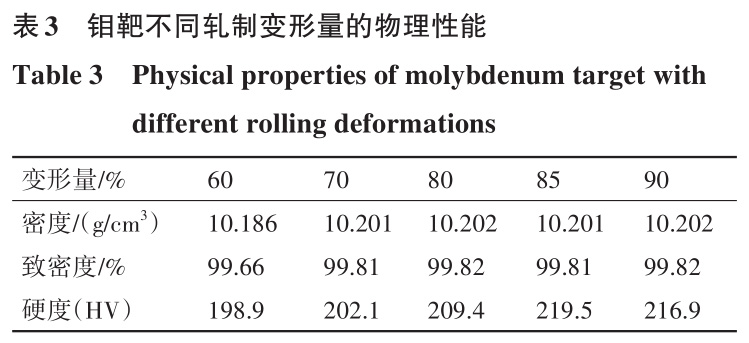
表3为钼靶材不同轧制变形量的轧制效果, 可见致密度随着轧制变形量增加而递增, 当轧制变形量增至 70%, 钼靶材的致密度不再进一步随轧制变形量增加而改善, 当密度达到 10.20 g/cm 3 以上, 对应致密度超过 99.8%, 接近钼的理论密度值, 仅内部少量气孔无法通过轧制工艺轧合。硬度随轧制变形量增加而递增, 当变形量超过85%,硬度增加不明显。图2展示了不同轧制变形量钼靶材RD-TD面(即溅射面)的内部金相组织, 图中呈现的孔隙率能够直观体现靶材致密度。轧制变形量为60%的钼靶样品内部存在细小的气孔, 这是由于轧下量不够导致内部细小气孔未轧合; 钼靶材内部气孔随着轧制变形量增加而减少, 当变形量超过70%时, 内部未发现明显的气孔, 致密度显著提高, 与前述致密度定量测试结果相吻合。
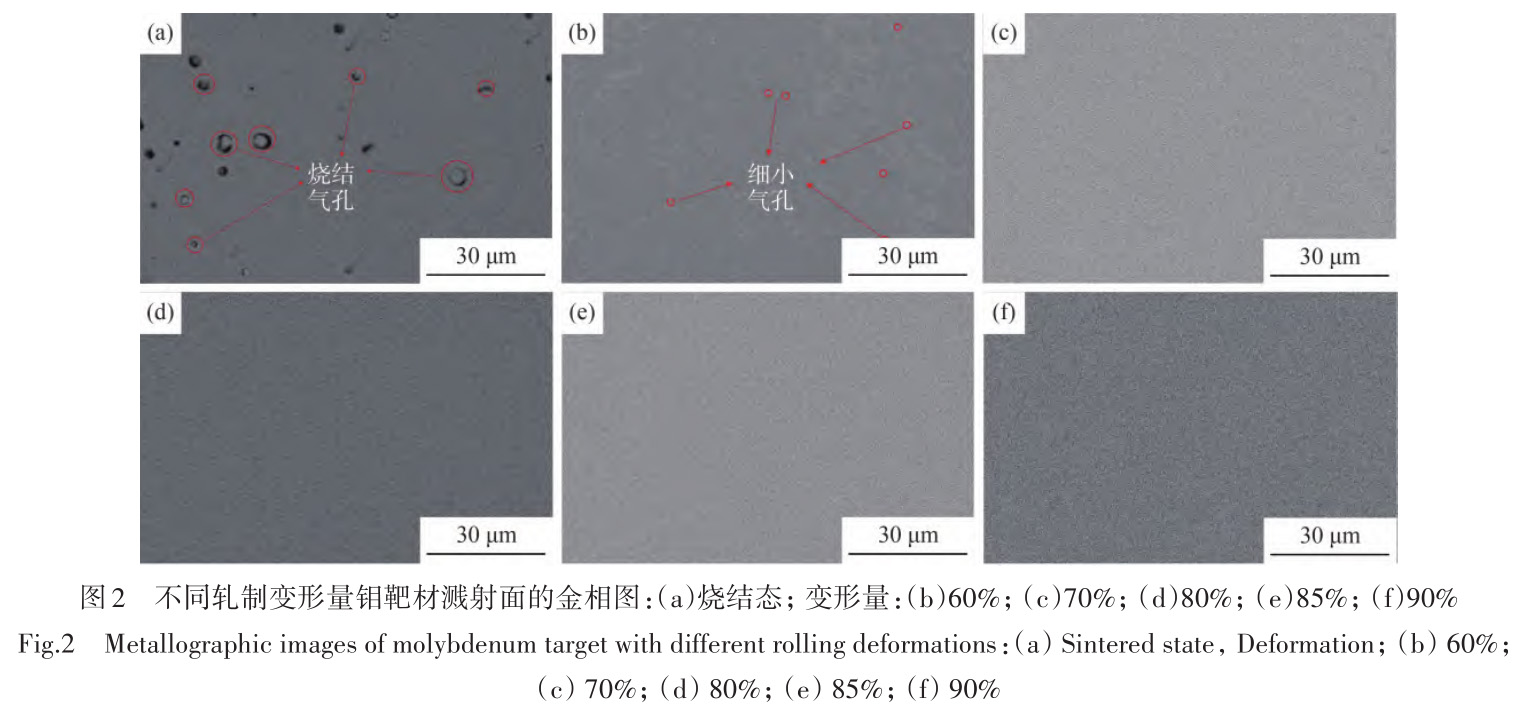
轧制过程中上下轧辊对钼靶材产生持续挤压, 晶粒发生受迫形变, 晶粒形变过程优先将烧结的真空孔洞填实, 使之完全闭合, 同时气体孔洞受压应力逐渐减小, 部分气体元素固溶到基体晶格中。晶粒组织图能直观展示晶体经过不同轧制变形量轧制后的形貌特征。图3为钼靶材经过不同变形量热轧后的RD-ND面的晶粒组织, 其形态为变形态晶粒, 其中大晶粒周围伴随着碎晶, 由于轧制温度处于再结晶温度之上, 局部夹杂着少量的再结晶组织。热轧过程中, 晶粒承受固定纵向轧制, 等轴状的晶粒沿着轧制方向延伸, 晶粒被轧制成扁平状。随着轧制变形量增加, 晶粒变形程度也增大。当轧制变形量达到70%时, 晶粒变形程度进一步加大, 出现明显的拉伸状。随着轧制变形量逐渐增大, 拉伸变形越来越明显, 晶粒也越来越细长, 直至变形量达到80%, RD-ND面逐渐出现纤维状组织。当变形量达到 85%, 纤维状组织开始密集, 呈现细长条纤维组织状态, 纤维组织相互搭接交错。当轧制变形量达到 90%, 纤维状的组织进一步密集, 部分纤维组织断裂变短, 故表现出更为密集的形态且长度缩短。然而, 过度的变形量会使得纵向的晶界开裂, 不利于提升钼靶材的内部质量。因此, 适当控制变形量才能保证靶材组织最优化。
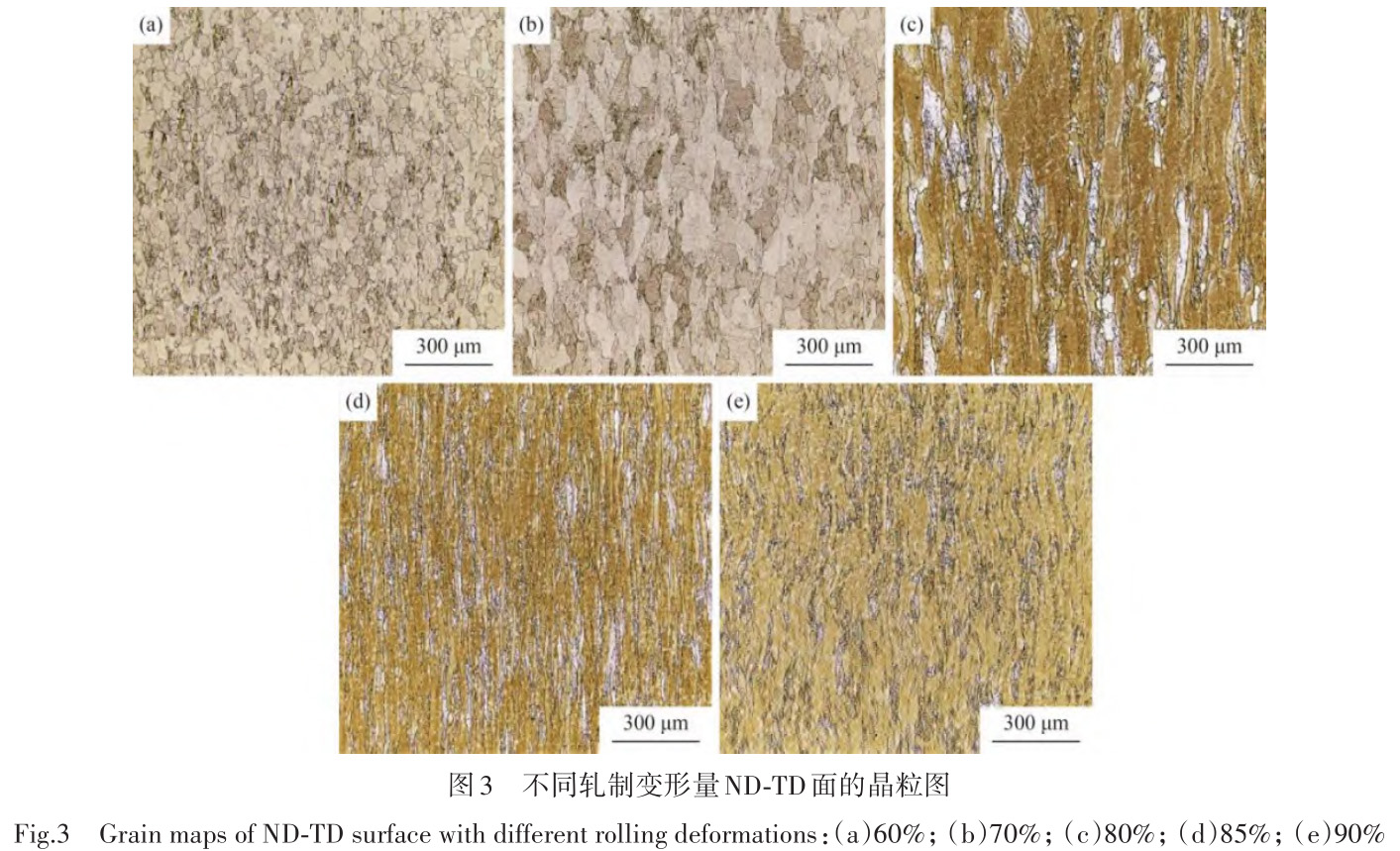
对比分析钼靶材烧结态的XRD衍射峰和不同轧制变形量钼靶材的溅射面XRD衍射峰(图4), 发现烧结态的钼靶材与钼粉的峰强相似, 表现为随机取向, (110)成为最强峰, 这些现象的最终状态由钼粉的结构因子、 多重性因子、 吸收因子、 角因子所决定[11-13] 。将烧结态钼靶材和不同轧制变形量的钼靶材XRD衍射峰与钼粉的衍射峰对比发现,烧结态的钼靶材可视为轧制变形量为0, 即为随机取向状态, 随着轧制变形量增加, 衍射峰强由[110]逐渐转变为[200], 即在压力轧制的作用下,由随机取向转变为{100}取向。当轧制变形量增加至85%, 衍射峰强在[200]方向明显增强, 增强变为主峰; 轧制变形量继续增加, 衍射峰强没有明显变化。因此, 轧制变形量为85%, {100}取向达到最强, 继续增加变形量, 取向改变不明显。
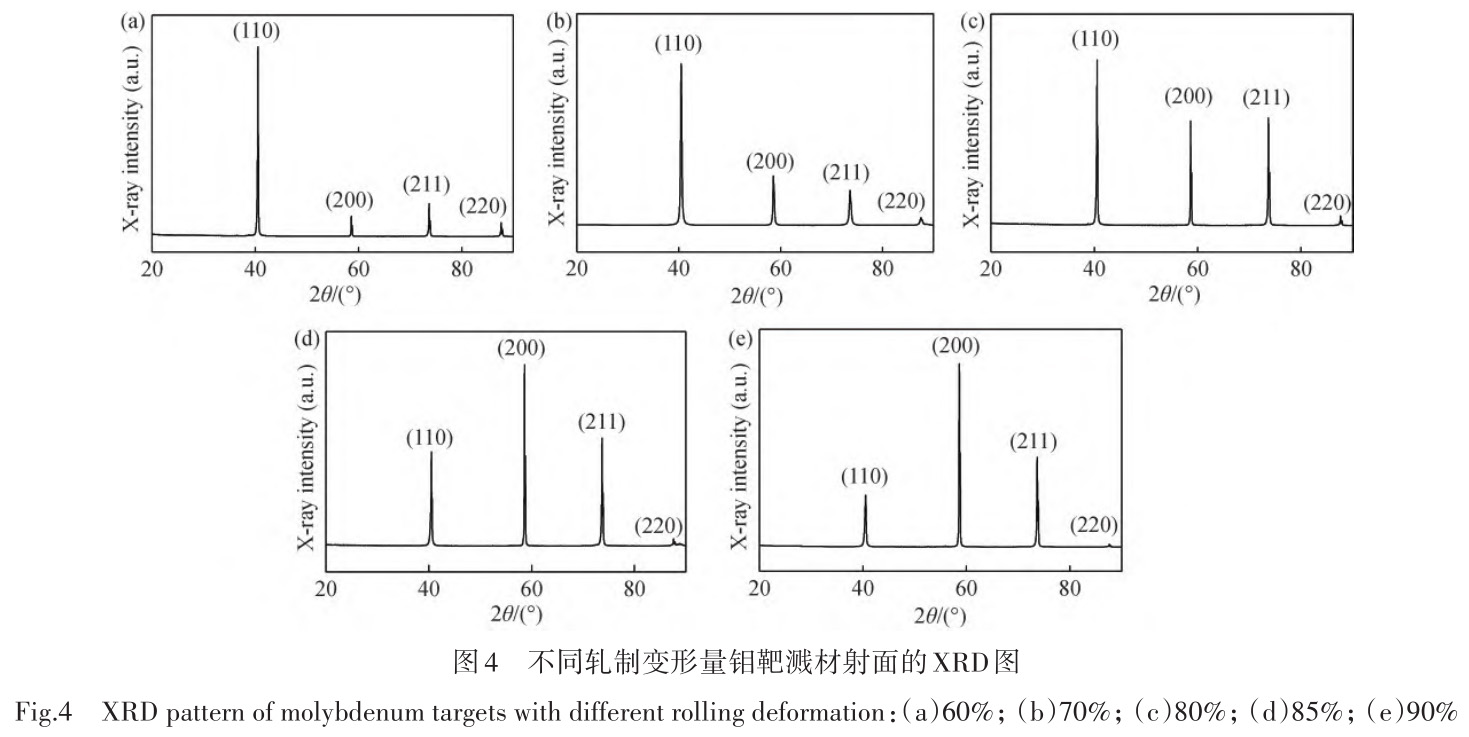
2.2 退火温度对显微组织的影响
钼是一种层错能较高的金属, 再结晶晶核的形成主要靠相邻亚晶粒的合并来实现, 但再结晶晶粒的长大必须通过晶界的迁移来完成。热处理温度的升高, 提高了钼原子的扩散系数, 使得晶界更易迁移, 促进了晶粒长大, 导致组织粗化。随着再结晶晶粒的长大, 晶粒之间会相互吞并。大的再结晶晶粒明显长大, 小的再结晶晶粒尺寸减小并逐渐消失, 使得晶粒间的尺寸差异变大, 尺寸分布更加不均匀。单向轧制的长条形钼靶材在再结晶退火后, 织构取向显现出其固有特征[14-16] 。
图5为退火态钼靶材通过EBSD获得的溅射面IPF 组织图, 图 6 为根据 IPF 图统计的晶粒尺寸。
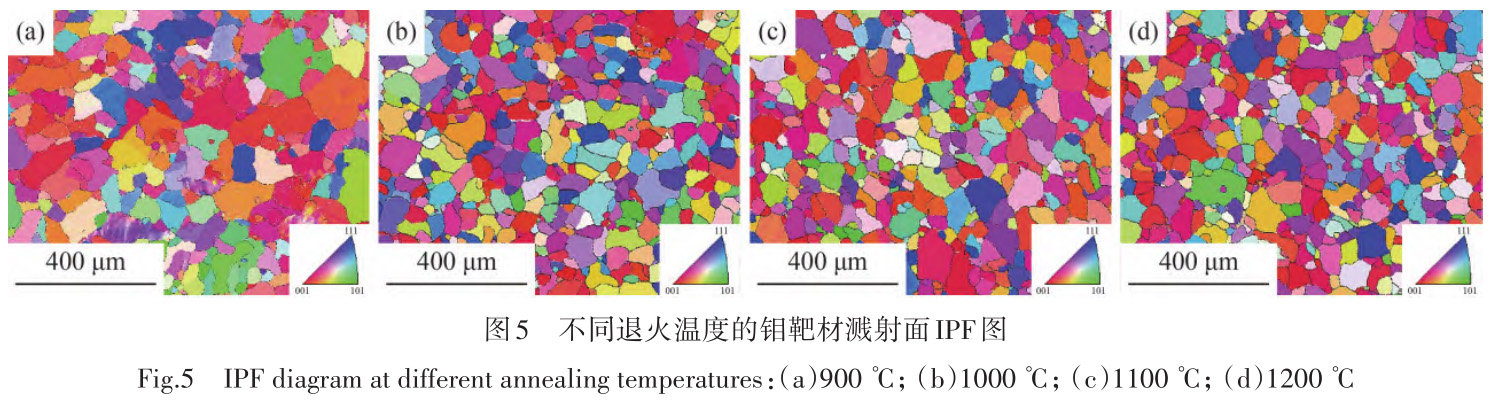
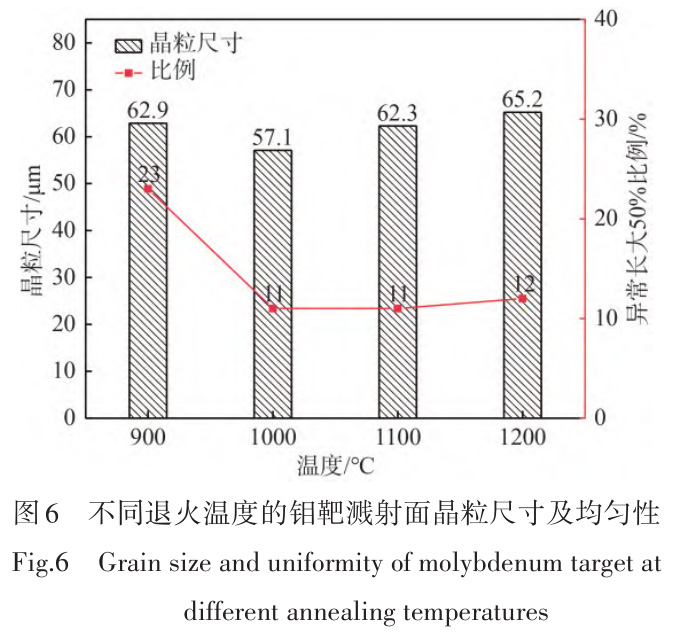
在 900~1200 ℃区间, 随着退火温度的升高, 晶粒尺寸先减小再增大, 在退火温度1000 ℃时晶粒尺寸最小。退火温度为900 ℃时, 溅射面晶粒从轧制变形态的晶粒逐渐开始回复再结晶, 部分晶粒保留了变形态的延展晶面, 部分晶界不明显, 内部夹杂了大量细小的碎晶, 平均晶粒尺寸为62.9 µm, 异常长大的晶粒占比23%, 表现为晶粒组织不均匀;退火温度升高至1000 ℃时, 溅射面晶粒回复再结晶程度增加, 等轴晶的晶界明显, 平均晶粒尺寸降低为 57.1 µm, 内部的细小碎晶被附近晶粒吞并,异常长大的晶粒占比11%, 晶粒组织均匀; 当退火温度进一步升高到1100 ℃时, 溅射面晶粒回复再结晶完全后, 晶粒开始均匀长大, 等轴晶的晶界明显, 平均晶粒尺寸增加至62.3 µm, 内部的细小碎晶较少, 异常长大的晶粒占比 11%, 晶粒组织均匀; 当退火温度达到 1200 ℃时, 等轴晶的晶界更为明显, 晶粒进一步长大, 平均晶粒尺寸增加至65.2 µm, 内部的细小碎晶较少, 晶粒组织均匀。
将轧制后的钼靶材进行热处理, 轧制态的钼靶材内部存在大量位错, 退火后, 钼靶材内部位错逐渐滑移甚至消失, 变形态的晶粒发生再结晶, 同时产生再结晶织构。靶材溅射面上原子排列方式越一致, 其织构越明显, 溅射离子束轰击到钼靶材表面时, 溅射面上的物质原子排布越规则, 则越有利于制备均匀一致的钼薄膜, 因此在钼靶材溅射面上获得特定的晶面织构将优化溅射薄膜均匀性。图5为不同退火温度的溅射面IPF图, 通过衬度可判断其织构程度, 图中红色为{001}面的晶粒, 绿色为{101}面的晶粒, 蓝色为{111}面的晶粒, 红色占比越高{001}面的晶粒越多, {001}织构越强。图7为不同退火温度的溅射面(即{001}晶面族)极图, 对应立方晶系标准投影图, 900~1200 ℃退火样品均存在{001}织构, 而退火温度为1000 ℃时, 信号最集中, 织构最强, 且为{001}织构。由于900 ℃退火低于0.4 T m , 属于较低温度退火, 其再结晶织构较低, 板织构和再结晶织构相互交错, 随着退火温度由 900 ℃升高至 1000 ℃, 在轧制态转变回复再结晶过程后织构更强。温度高于 1000 ℃(0.4 T m ), 钼靶材朝着完全再结晶转化, 随着温度升高, 完全再结晶程度增加, 随着晶粒长大,{100}织构和{110}织构均在减弱, 逐渐朝着{111}织构转变。85% 轧制变形量的钼靶材在温度为1000 ℃下退火, 其织构控制强度最高, 保留了大量轧制态的织构特征。因此,当退火温度为 1000 ℃时, 晶粒组织均匀且晶粒最细小, 织构性最强。
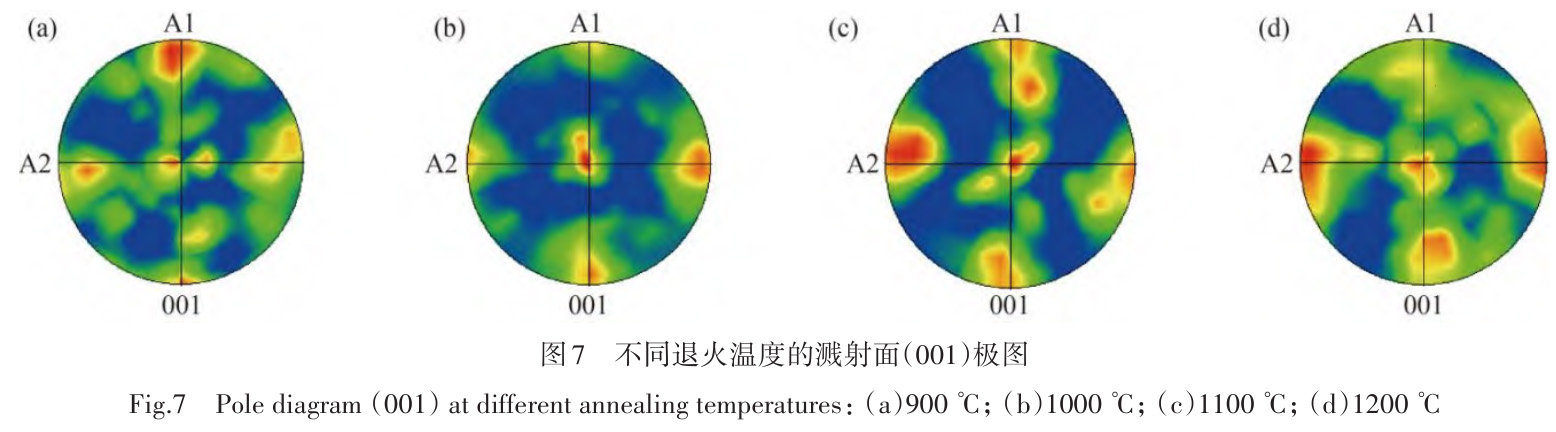
3、 结 论
1)钼靶材的密度随着轧制变形量增加而递增, 当轧制变形量增至 75%, 钼靶材的密度达到10.2 g/cm3 , 已逼近单质钼的理论密度, 不再继续随轧制变形量增加而增大。
2)通过金相显微镜和XRD衍射图谱表征, 当钼靶材的轧制变形量为80%~85%时, 其晶粒尺寸最佳, 表现为明显增强的{0 0 1}系列衍射峰。
3)通过一系列退火温度对照实验发现, 在900~1200 ℃区间, 随着退火温度升高, 晶粒尺寸先减小再增大。在退火温度 1000 ℃时, 晶粒尺寸最优。
参考文献:
[1] 赵宝华, 范海波, 孙院军. TFT-LCD制造用钼薄膜溅射及其靶材[J]. 中国钼业, 2011, 35(1): 7-11.
[2] 刘仁智, 孙院军, 王快社, 等. Mo靶材组织对溅射薄膜形貌及性能的影响[J]. 稀有金属材料与工程,2012, 41(9): 1559-1563.
[3] OERTEL C G, HÜNSCHE I, SKROTZKI W. Plastic ani-sotropy of straight and cross rolled molybdenum plates[J]. Material Science & Engineering A, 2008,483-484: 79-83.
[4] OERTEL C G, HÜNSCHE I, SKROTZKI W. Influence of cross rolling and heat treatment on texture and form⁃ing properties of molybdenum plates[J]. International Journal of Refractory Metals & Hard Materials, 2010,28: 722-727.
[5] 尤世武. 冷轧纯钼板的织构研究[J].理化检验(物理分册), 2000, 36(8): 342-344.
[6] 张希杰, 余斌, 刘羽飞, 等 . 轧制及退火工艺对C5100 铜带材组织性能的影响[J]. 铜业工程, 2023(2): 114-121.
[7] CHAUDHURI A, SARKAR A, SUWAS S. Investiga⁃tion of stress-strain response, microstructure and texture of hot deformed pure molybdenum[J]. International Journal of Refractory Metals & Hard Materials, 2018,73: 168-182.
[8] 邓自南, 刘竞艳. LCD溅射靶材用大尺寸钼板工艺、 组织、 织构与性能研究[J]. 中国钼业, 2013, 37(3):36-42.
[9] 张信钰. 金属和合金的织构[M]. 北京: 科学出版社,1976.
[10] 肖娟, 石志锋, 刘佳, 等. 样品质量控制对X射线衍射测量结果的影响[J]. 应用化学, 2023, 40(5):720-729.
[11] 姬耀鑫, 吴壮志, 王德志. 单向轧制纯钼板退火织构及其各向异性的研究[J]. 中国钼业, 2020, 44(1):37-41.
[12] 王友康. 同步辐射X射线衍射深度应力表征方法及应用研究[D]. 北京: 北京科技大学, 2023.
[13] 毛晶, 郭倩颖, 马利利, 等. 原位变温X射线衍射测试技术及其影响因素[J]. 分析测试技术与仪器,2023, 29(1): 111-116.
[14] 陈岩, 胡斐斐, 刘昆, 等. C5240铜合金加工过程的组织演变与力学性能[J]. 铜业工程, 2021(6): 1-5.
[15] 张国君, 马杰, 安耿, 等. 热处理温度对钼靶材微观组织和性能的影响[J]. 中国钼业, 2014, 38(5): 47-50,54.
[16] 陈文静, 胡平, 邢海瑞, 等.热处理工艺对钼金属板材组织和性能影响的研究进展[J]. 材料导报, 2021,35(3): 3141-3151.
相关链接