钛靶的国内外标准核心差异在于纯度等级、表面精度及认证体系。国内标准(GB/T、YS/T)已逐步与国际接轨,但在高端半导体领域仍需依赖SEMI/ASTM标准。企业应根据目标市场(如出口需符合SEMI)和终端应用(如核工业需EJ/T)选择适配标准。关于钛靶材在国内外的主要执行标准对比,凯泽金属按国家和地区分类列举。
一、国内执行标准
标准类型 | 标准编号 | 标准名称 | 适用范围与关键要求 |
国家标准 | GB/T 38976-2020 | 《钛及钛合金溅射靶材》 | 规定钛靶材的化学成分、尺寸公差、表面粗糙度(Ra≤0.8μm)、晶粒度(≤100μm)等要求。 |
行业标准 | YS/T 1497-2021 | 《高纯钛靶材》 | 适用于半导体用高纯钛靶(纯度≥99.995%),明确氧含量(≤300ppm)、金属杂质总量(≤50ppm)。 |
核工业标准 | EJ/T 20079-2014 | 《核级钛及钛合金靶材技术条件》 | 核反应堆用钛靶材的特殊要求,包括辐照稳定性、氢含量(≤0.015%)等。 |
二、国际执行标准
标准类型 | 标准编号 | 标准名称 | 适用范围与关键要求 |
美国标准 | ASTM F3049-14 | 《溅射靶材用钛及钛合金标准规范》 | 涵盖纯度(99.9%-99.999%)、密度(≥4.5g/cm³)、微观组织(无气孔/夹杂物)等指标。 |
半导体行业标准 | SEMI F104-0308 | 《半导体溅射靶材通用规范》 | 针对12英寸晶圆用钛靶,要求表面粗糙度Ra≤0.5μm,晶粒尺寸均匀性±10%。 |
日本标准 | JIS H 7801-2005 | 《溅射靶材一般要求》 | 规定钛靶的尺寸公差(±0.1mm)、翘曲度(≤0.1%)、绑定结合强度(≥30MPa)。 |
欧盟标准 | EN 10204-2004 | 《金属产品检验文件类型》 | 适用于钛靶材的质量认证,要求提供3.1B或3.2级材质证书,确保可追溯性。 |
三、国内外标准对比与关键差异
对比维度 | 国内标准(GB/T 38976) | 国际标准(ASTM F3049/SEMI) |
纯度要求 | 半导体级:99.995%(YS/T 1497) | 半导体级:≥99.999%(SEMI F104) |
表面粗糙度 | Ra≤0.8μm(通用) | Ra≤0.5μm(12英寸靶材) |
杂质控制 | 氧≤300ppm,铁≤100ppm | 氧≤150ppm,碳≤50ppm(高纯靶) |
晶粒尺寸 | ≤100μm(允许局部偏差±20%) | ≤50μm(SEMI要求),均匀性±5% |
认证文件 | 需提供化学成分报告、力学性能测试数据 | 需附加第三方检测报告(如SGS)、批次追溯文件(EN 10204) |

四、应用领域与标准选择建议
半导体行业
理想标准:SEMI F104(12英寸靶材)、ASTM F3049(高纯度)。
关键指标:纯度≥99.999%、晶粒均匀性、超低氧含量(≤100ppm)。
光学镀膜/装饰镀层
适用标准:GB/T 38976(国内)、JIS H 7801(出口日本)。
关键指标:表面粗糙度Ra≤1.0μm、成本控制。
核工业
强制标准:EJ/T 20079(中国)、ASTM B811(国际核级)。
关键指标:抗辐照性能、氢含量≤0.015%。
五、未来标准发展趋势
更高纯度要求:半导体先进制程(3nm以下)推动钛靶纯度向6N(99.9999%)发展。
尺寸大型化:12英寸以上靶材标准将细化,如SEMI F104修订版可能新增18英寸靶规范。
绿色制造:新增环保指标(如碳足迹追踪),符合欧盟《电池与废电池法规》等要求。
凯泽金属前面深度剖析了钛靶材的相关标准及应用差异,为不断提升公司靶材产品的应用深度,对于钛靶材的核心应用场景、技术要求及发展趋势,按主要领域整理如下:
一、半导体制造:铜互连与先进封装
1、核心作用
钛靶用于物理气相沉积(PVD),在硅片表面形成 铜互连阻挡层(Ti/TiN),防止铜原子扩散至绝缘层,保障电路可靠性。
技术需求:
超高纯度(≥99.999%):避免金属杂质(Fe、Cr)引起漏电;
晶粒均匀性(晶粒度≤50nm):确保薄膜厚度一致性(±2%);
低氧含量(≤100ppm):减少界面氧化导致的电阻升高。
挑战:
3nm以下制程要求靶材晶粒尺寸进一步缩小至20nm级;
EUV光刻工艺中,钛靶溅射需避免微粒污染(每片晶圆缺陷数<0.1个)。
2、代表企业:
国际:霍尼韦尔(美国)、东曹(日本);
国内:江丰电子、有研新材(已突破7nm节点靶材量产)。
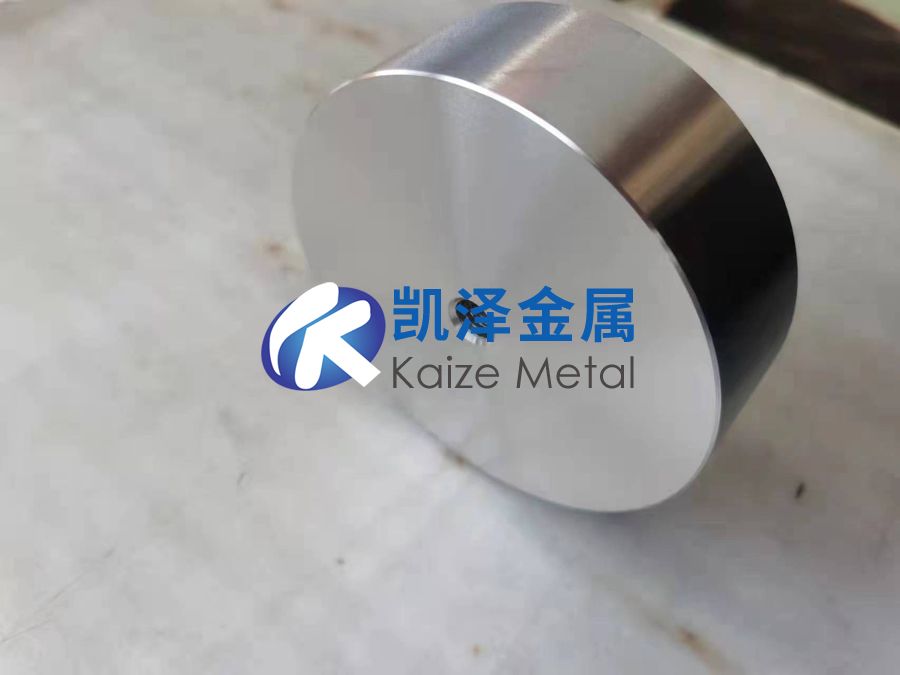
二、光学镀膜:AR/VR与精密光学
1、核心应用
钛靶用于沉积 增透膜(AR)、反射膜,应用于:
消费电子:手机镜头、VR头显光学模组;
高端仪器:天文望远镜镜面、激光器谐振腔。
技术需求:
膜层致密性(孔隙率<0.1%):防止水汽渗透导致膜层脱落;
成分可控性:通过Ti-Al、Ti-Si复合靶调节折射率(1.8-2.5);
大面积均匀性(Φ300mm靶材厚度偏差≤1%)。
2、案例:
蔡司镜头:采用Ti/TiO₂多层膜,实现可见光区透光率>99.5%;
Meta Quest 3:钛基纳米结构膜降低镜片反射率至0.2%以下。
三、装饰镀层:轻奢消费与工业设计
1、创新应用
通过调节溅射参数,钛靶可制备 多彩装饰镀层:
PVD离子镀:生成金色(TiN)、黑色(TiC)、蓝色(TiOxNy)等膜层;
微弧氧化:用于智能手表表壳、汽车内饰件,形成耐磨陶瓷层。
技术突破:
渐变色彩控制:通过多靶共溅射(Ti+Al+Si)实现虹彩效应;
环保替代:取代电镀铬工艺(避免六价铬污染),符合欧盟RoHS指令。
市场数据:
2023年全球装饰镀层用钛靶市场规模达12亿美元,年增长率15%;
苹果Apple Watch Ultra采用钛靶镀膜,良率提升至95%(传统工艺仅80%)。
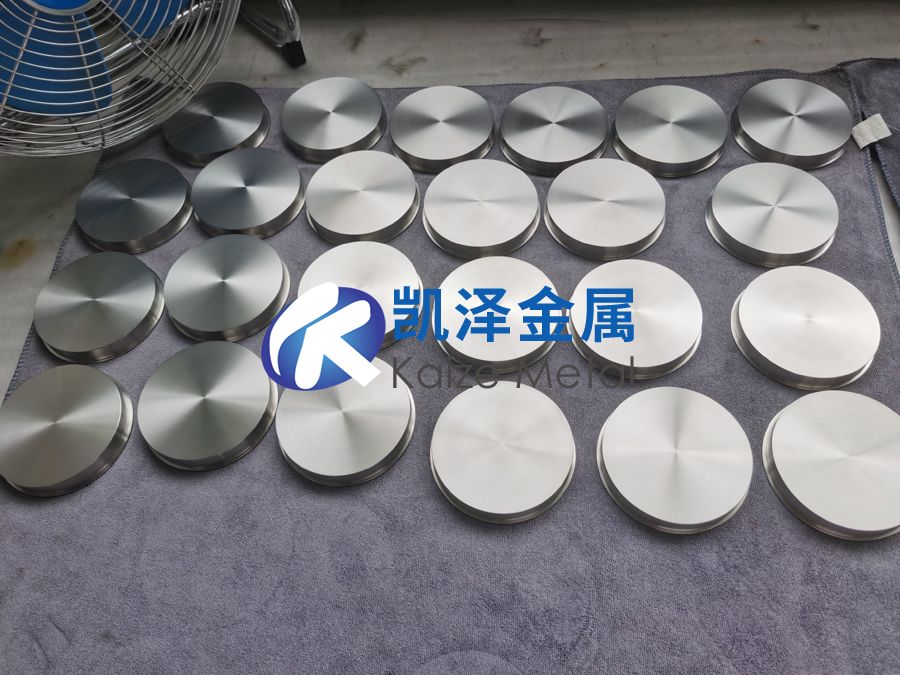
四、新能源领域:锂电与氢能
1、锂离子电池
集流体镀层:在铜箔表面溅射纳米钛层(≤50nm),提升电极-电解液界面稳定性,循环寿命增加30%;
固态电解质界面:钛靶沉积Li-Ti-O复合层,抑制锂枝晶生长(宁德时代专利技术)。
2、氢燃料电池
双极板防护层:钛基非晶碳膜(Ti-DLC)降低接触电阻至5mΩ·cm²,耐腐蚀电流<1μA/cm²;
质子交换膜(PEM):钛纳米粒子掺杂膜提升机械强度(>30MPa)和质子传导率。
痛点与趋势:
成本制约:钛靶占双极板制造成本20%,推动低成本钛铁合金靶研发;
卷对卷(R2R)溅射:开发柔性钛靶(厚度≤0.1mm),适应连续镀膜产线。
五、新兴领域:柔性电子与太空科技
1、柔性显示
透明导电膜:钛靶溅射超薄Ti(3-5nm)+Ag层,替代ITO,弯折10万次电阻变化<5%(京东方Fold 3应用);
可拉伸电路:Ti-Au纳米岛结构实现200%拉伸形变下导电性保持。
2、深空探测
卫星光学部件:钛基多层膜抵御太空紫外辐射(>5000小时性能无衰减);
核电池包壳:钛靶镀层(厚度≥10μm)阻隔钚-238辐射泄漏(NASA Perseverance火星车应用)。
六、国产替代与国际竞争格局
1、技术差距
高端市场:12英寸以上半导体靶材90%依赖进口(日美企业主导);
专利壁垒:东曹持有“高密度钛靶热等静压成型”核心专利(CN112958752A)。
2、突破路径
联合研发:中科院宁波材料所+江丰电子开发超高纯钛靶(6N级)熔炼技术;
标准升级:推动GB/T 38976-2020与SEMI F104对标,覆盖18英寸靶材参数。
3、政策机遇
中国“十四五”新材料规划:将高纯金属靶材列为“卡脖子”攻关目录;
欧盟《关键原材料法案》:钛被列为战略资源,倒逼本土供应链建设。
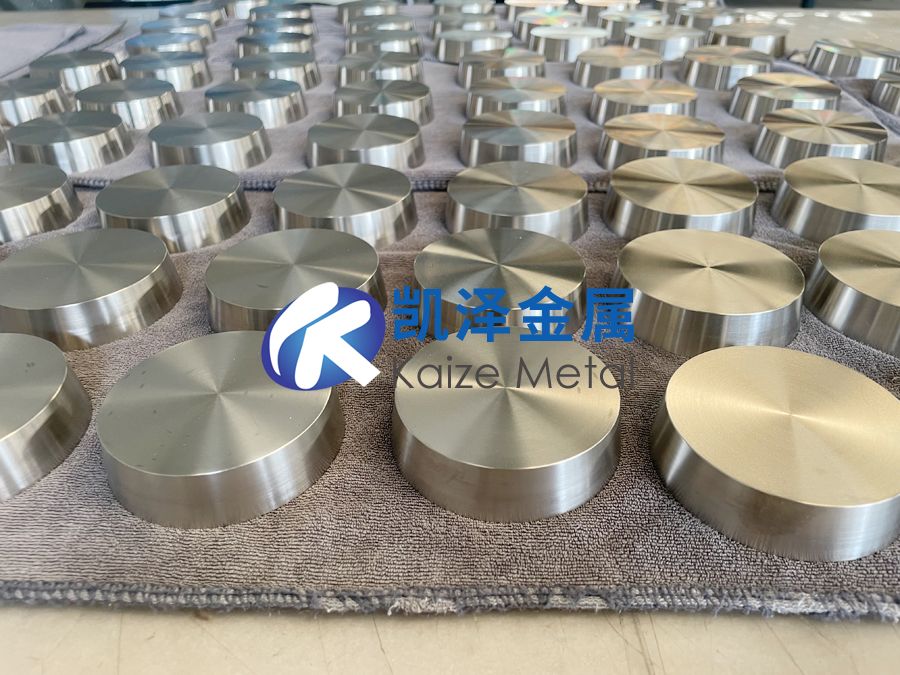
总结:钛靶材应用的三大升级方向
性能极致化:纯度从5N向6N突破,晶粒尺寸进入亚微米时代;
形态多元化:从刚性靶向柔性靶、异形靶(环形/管状靶)扩展;
相关链接