引言
管路构件作为起着介质传输和结构承载等重要作用的典型构件,被广泛应用于航空、航天、汽车、核电、医疗以及日常生活中等诸多领域,也被称为“工业动脉”[1,2]。特别是在航空航天等高端装备领域,管路构件被应用于液压、气动和燃油等核心系统中起流体动力传输等关键功效(如图 1 所示),材料和规格种类繁多且量大面广,被誉为航空航天飞行器的“血管类”零件和生命控制线[3,4]。这类构件在服役过程中往往长期处于高/低温、高压、振动或油气侵蚀等恶劣的环境当中,其性能的优劣将直接影响飞行器的安全和适航
性能。当前先进飞行器和发动机装备的换代发展,对高性能管材耐高压、高可靠和长寿命等提出了更高要求,迫切需要采用具有轻质高强、抗疲劳以及耐腐蚀优异特点的新型钛合金等材料并提升管材精确成形制造能力,从而全面提升飞行器的综合指标和性能。
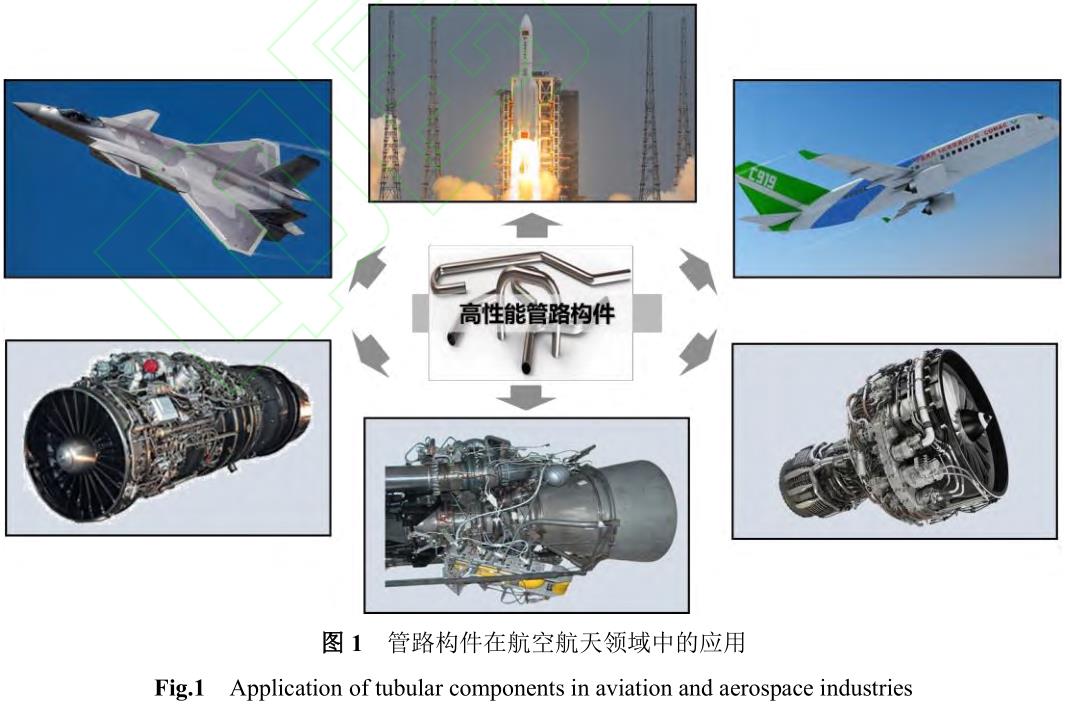
在众多管材制备工艺中,皮尔格冷轧过程中管材经历了压应力主导的增量局部加载作用,具有道次变形量大、尺寸精度高、表面质量好、生产效率高等优点,已成为薄壁难变形管材制造的优选工艺[5-7]。然而,皮尔格冷轧涉及局部加载下多行程和非稳态成形过程,管材在冷轧过程中经历了复杂的加载路径[8-10],同时对于钛合金和锆合金等难变形材料来说,成形过程往往要经历多道次冷轧结合中间和最终热处理来完成,加之此类材料密排六方非对称晶体结构特征,导致管材在冷轧中极易发生显著不均匀变形,使得管材微观织构演变规律复杂并导致分布的不确定性,进而严重影响管材的力学性能、后续成形性能以及最终服役性能[11,12],诸如管坯初始织构、道次变形分配、中间及最终退火工艺以及模具和工艺参数等设计稍有不慎都会严重影响冷轧过程微观织构分布,进而造成管材性能的波动,给管材形性精确调控带来严峻的挑战。因此,深入系统研究难变形管材皮尔格冷轧成形全过程微观织构演变规律与机理,建立微观织构有效调控方法,是实现其高性能精确成形制造的关键所在。
本文首先对无缝管材皮尔格冷轧成形技术进行概述,并对难变形管材多道次皮尔格冷轧成形全过程特点进行分析;详细综述分析了管材皮尔格冷轧成形过程宏观不均匀变形与微观织构演变预测建模及管材冷轧过程微观织构演变规律与调控方法方面的国内外研究现状,在此基础上针对目前研究中存在不足,探讨了难变形管材多道次冷轧全过程微观织构精准调控及高性能制备尚待解决的问题及未来可能的发展方向。
1、 管材多道次皮尔格冷轧成形特点
无缝管材的典型制备工艺主要包括挤压、拉拔和轧制成形,如表 1 所示。其中,挤压成形技术保证了管材在成形过程中受到压应力为主的作用,但是属于一次成形,而高强度管材成形过程中变形抗力极大,因此管材挤压成形普遍采用热挤压的方式进行,从而导致成品管材尺寸精度较低、成形过程材料损失严重以及组织性能不均匀等缺陷,热挤压主要应用于厚壁管坯的制备。拉拔成形得到的制品虽然尺寸精度高且表面质量好,但由于管材在成形过程中受到拉应力为主的作用且同样属于一次成形,导致其每道次加工率小、能量消耗较大以及生产效率较低,因此只适合制备强度低且直径很小的管材。周期式冷轧技术在 19 世纪 80 年代首次被提出并逐渐改进发展为现今的二辊皮尔格冷轧成形技术,与前述两种无缝管材成形制备工艺相比,整个二辊皮尔格冷轧过程中管材经历了以压应力为主导的增量局部加载作用,这也使得其具有道次变形量大、尺寸精度高、表面质量好、生产效率高等优点,是众多管材制备工艺中尤其是对于难变形薄壁管材最有效的一种高精度制备工艺[13-15]。
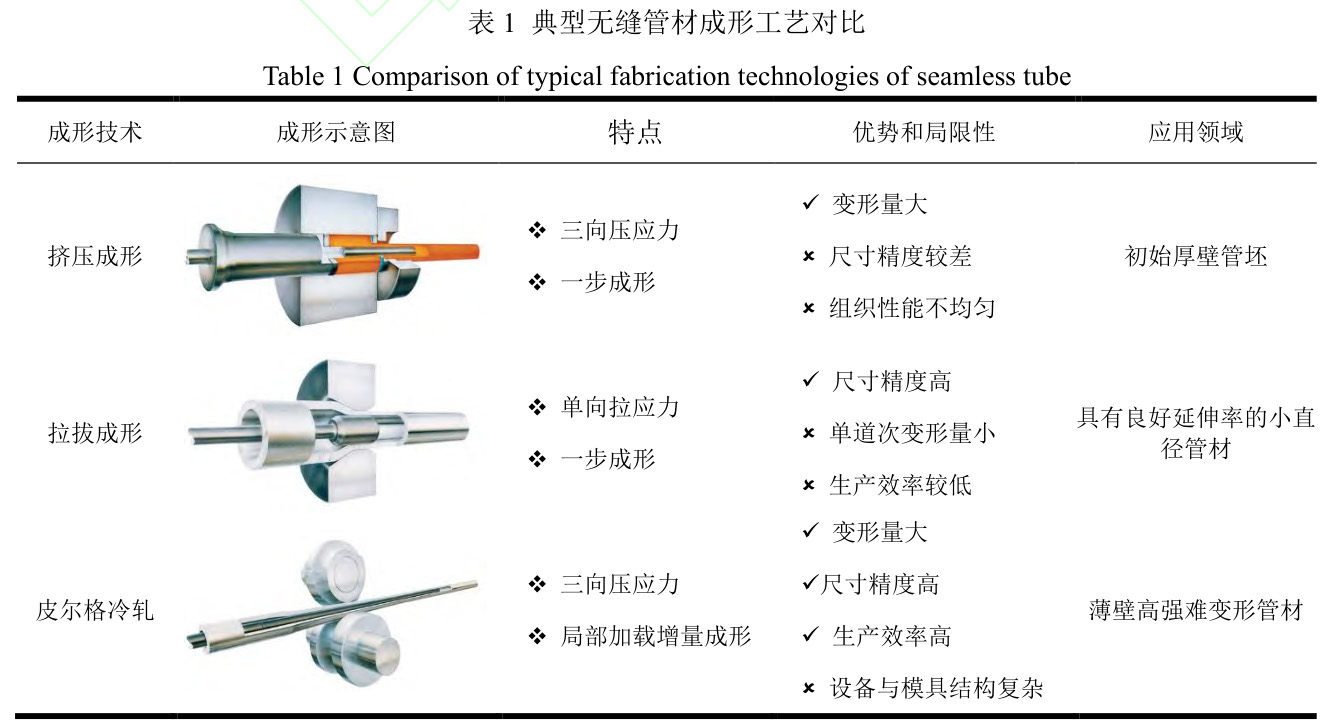
如图 2 所示,二辊皮尔格冷轧模具主要由上下轧辊和芯棒组成,轧辊圆周上开有截面直径不断变化的凹槽,芯棒直径沿轧制方向呈不断减小的趋势,轧辊凹槽与芯棒之间的环形间隙构成了轧制孔型,管材在上下轧辊和芯棒的作用下持续变形。在轧制过程中管材和芯棒在卡盘的限制下无法移动,轧辊从后极限位置移动到前极限位置的过程称为正行程,轧辊从前极限位置移动到后极限位置的过程称为反行程,轧辊如此重复往返从而实现管材周期轧制过程。皮尔格冷轧过程也可以分为前回转段、工作段(减径段和壁厚压下段)、定径段和后回转段四个不同的阶段,前、后回转段的作用主要是为了顺利实现管材的回转送进,在工作段管材发生减径减壁变形的同时长度伸长,而定径段主要对管材的内外径和圆度起到精整作用[16,17]。
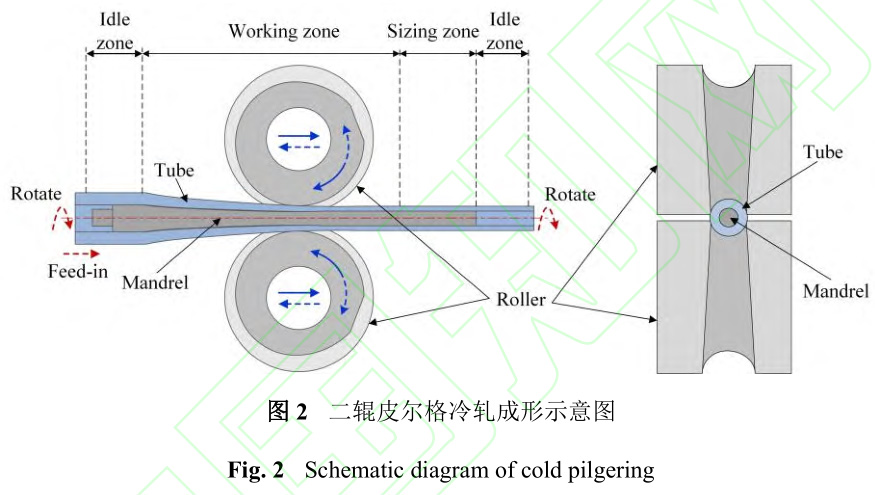
对于强度高且塑性相对较差的难变形管材来说,从初始管坯到目标规格的成品管材往往要经历多道次冷轧成形,并且在每道次冷轧中间需要对管材进行再结晶退火恢复管材塑性以便于下一道次轧制的进行,最终道次冷轧结束后还需要对管材进行去应力退火以消除内应力的同时保留冷作硬化效果。图 3 所示为难变形钛合金管材皮尔格多道次冷轧全过程示意图,冷轧过程中诸如初始管坯织构、道次轧制规格相关的冷轧变形模式与变形量、孔型与工艺参数、以及退火工艺都会对最终管材的织构分布带来显著影响。多道次冷轧过程中由于成形过程的复杂性以及工艺参数的波动将会显著引起管材微观织构分布的不确定性,进而严重影响管材力学性能、弯曲等成形性能以及疲劳等服役性能,这也是制约管路构件高性能制备的关键问题。
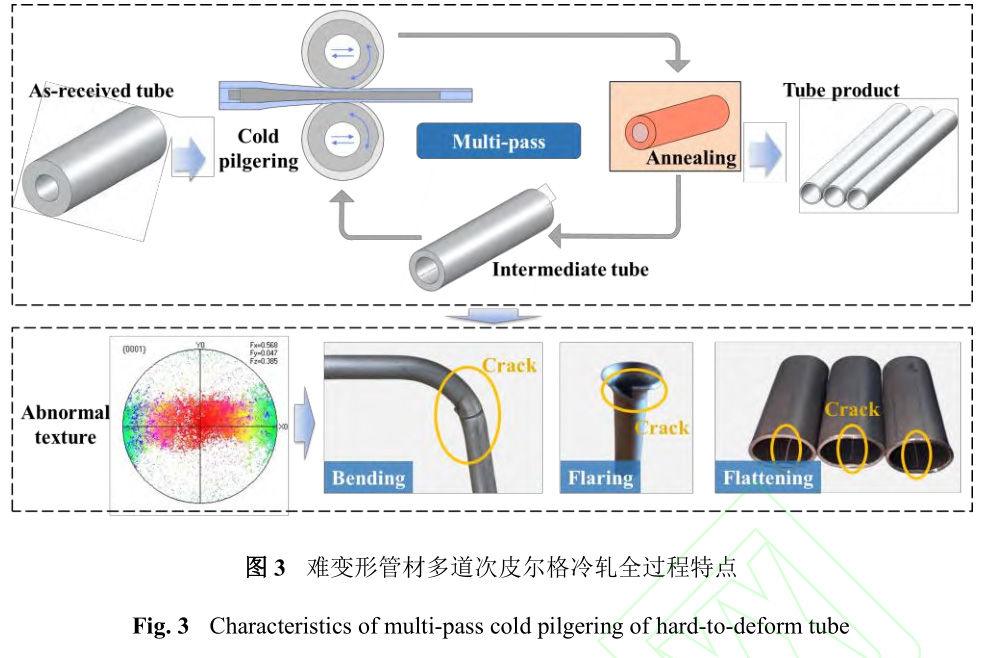
2 、管材冷轧过程变形与微观织构演变预测建模
2.1 管材冷轧过程宏观变形预测建模
由于皮尔格冷轧成形工艺以及模具孔型几何形状的复杂性,导致管材皮尔格冷轧实验成本高且周期长,同时实验研究难以准确全面的获得冷轧过程管材变形行为,而数值模拟可以获得丰富的信息,能够考虑多因素和复杂边界的影响,是皮尔格冷轧成形管材宏观变形行为研究重要的手段[18-20]。
Mulot 等[21]建立了锆管皮尔格冷轧过程的 3D 有限元模型,分析了一个轧制行程的应力和应变,得到了沿轧制方向的应力和应变分布状态。Montmitonnet 等[22]以 FORGE3 为平台,针对锆合金管皮尔格轧制建立了三维弹塑性有限元模型,该模型将周期循环运动直接作用在轧辊上,从而简化了管材皮尔格轧制中的曲柄-连杆-齿轮机构,分析了皮尔格轧制一个行程中管材的应力应变分布状态,并得到了皮尔格轧制多行程中管材上一点的应力应变变化规律以及材料流动轨迹,提出在皮尔格轧制过程中,管材上一点的应力变化规
律为正负应力交替循环,极易导致低周疲劳和产生表面裂纹,而管材上一点的流动轨迹为螺旋式前进。不同于单一行程的有限元模拟和分析,黄亮等[23]建立了钛合金管材多行程皮尔格轧制三维有限元模型,模型主要由管材、上下轧辊、芯棒以及推块构成,研究了管材冷轧过程不同方向应变变化规律。楚志兵等[24]以不锈钢管为对象,建立了一个道次完整轧制过程的三维有限元模型,并利用两辊轧机进行轧制试验验证了回弹预测模型的可靠性与正确性。
为了提高有限元模拟计算效率和精度,有关学者对皮尔格冷轧建模关键技术进行了改进,Lodej 等[25]以皮尔格冷轧锆管为研究对象,根据孔型曲线预制管材变形段并用于模拟计算,待少量几个轧制行程后管材变形即趋于稳定,并且认为此时的应力应变状态与实际结果基本吻合,从而提高了计算效率。Strickner 等[26]基于 SIMUFACT 有限元软件,建立了无缝不锈钢管冷轧的三维弹塑性有限元模型,该模型通过编写子程序并嵌入有限元软件中来精确控制轧辊周期式的循环运动,并且根据管材延伸率及送进量,计算出每一行程
轧辊运动的前极限位置,该方法简化了管材轧制运动过程,缩短了计算时间,提高了计算效率。Deng 等[27]以 Zr-4 管为研究对象,建立材料模型时考虑了应变速率和温度对材料硬化行为的影响,并对试验和模拟得到的轧制力和管材尺寸进行对比,结果验证了该模型的可靠性。Azizoglu 等研究发现轧辊的变形对接触区长度、轧制力以及成品管精度有显著影响,在有限元建模时将轧辊设置为弹性体并划分网格[28],此外,学者还通过充分考虑管材冷轧过程中与模具和空气之间的热辐射实现了不锈钢管冷轧过程温度演变的预测[29],所建立模型如图 4 所示,并通过试验对比验证了上述模型在皮尔格冷轧成形过程轧制力、应力应变、温度分布预测方面的准确性和可靠性。Chung 等[30]在建立不锈钢管冷轧仿真模型时考虑了管材初始壁厚的不均匀性以及芯棒的弹性变形,模拟结果表明冷轧过程显著的塑性变形可以明显改善管材厚度的均匀性,同时芯棒的振动是导致其末端产生疲劳裂纹的因素之一。
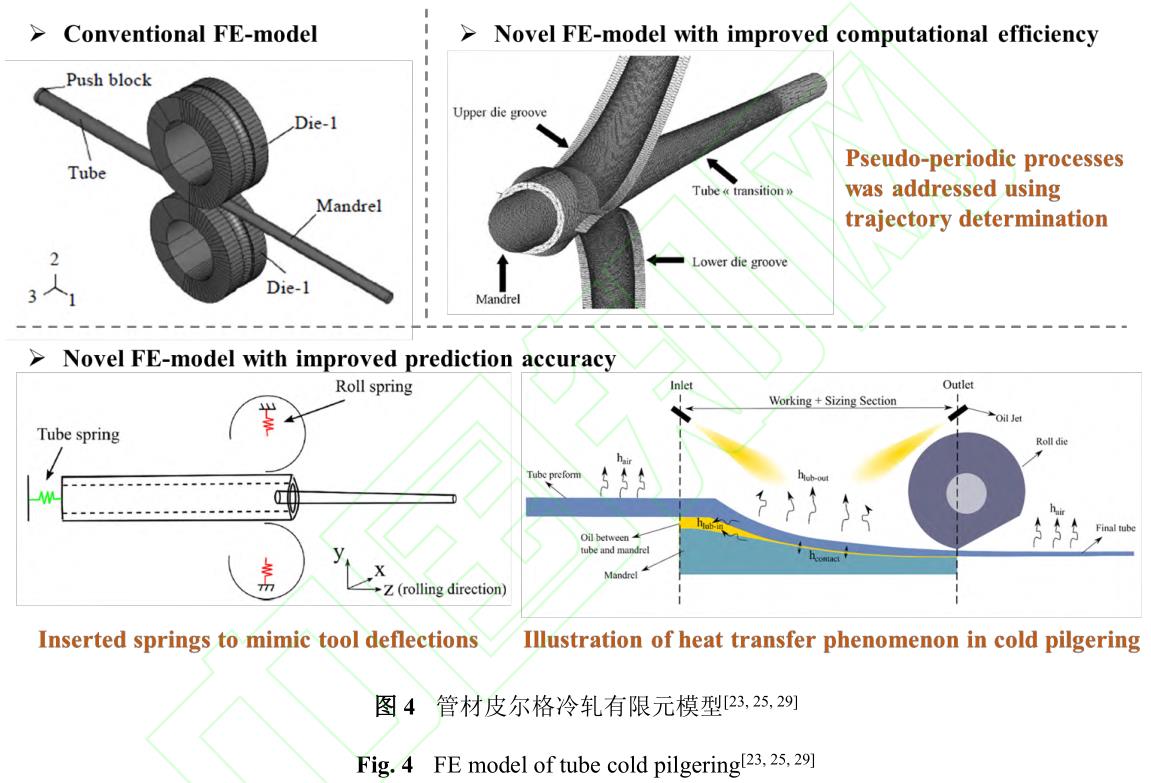
2.2 管材冷轧过程微观织构演变预测建模
成形过程中织构的产生对材料的各向异性以及成形性能等具有显著的影响,为了能准确预测材料成形过程中的织构演变,以及降低实验成本和提高效率,大量学者开始利用晶体塑性模型来模拟成形过程中的织构演变规律。Molinari 等[31]首次建立了多晶体自洽本构模型,并应用于金属的大塑性变形过程的织构模拟预测,在此基础上,Lebensohn 等[32]提出了粘塑性自洽(Viscoplastic Self-consistent, VPSC)模型,该模型考虑了材料的各向异性,引入滑移和孪生两种金属塑性变形机制,并采用了 PTR(Predominant Twin Reorientation)晶粒旋转计算方法和 VFT(Volume Fraction Transfer)晶粒取向体积分数计算方法,已经被广泛应用于定量预测材料塑性变形过程中晶粒取向的转变以及织构演变[33-45]。
Lebensohn 等[36]通过引入静态速度梯度,首次将 VPSC 模型用于 Zr-4 锆合金管材皮尔格冷轧成形的织构模拟预测,并与实验结果对比,两者吻合较好。然而,采用静态速度梯度无法表征整个轧制过程中的变形特征,因而无法揭示整个轧制过程中的织构演化规律。张海芹[37]和 Li 等[38]在前述研究基础上,通过耦合有限元模型和 VPSC 模型,建立了高强 TA18 钛管皮尔格两辊冷轧过程织构预测平台,研究了高强 TA18 钛管的在不同外部载荷下织构演化与变形机制的关联关系,分析了二辊皮尔格冷轧过程中管材的织构演变规律。Wei 等[39]以高强 TA18 钛管为研究对象,在管材再结晶退火过程微观织构遗传特性的基础上,采用 VPSC 模型迭代每道次模拟中管材力学性能,并耦合有限元模型和 VPSC 模型建立了高强 TA18 钛管多道次冷轧全过程宏细观数值预测模型,如图 5 所示,并通过 3 道次冷轧实验和表征验证了模型的可靠性。此外,VPSC 模型也被广泛应用于材料各向异性变形行为以及变形机制的研究[40-42],其中 Yang 等[41]结合实验与 VPSC 模拟,探究了纯钛材料热力加载条件下温度相关的各向异性与拉压非对称性变形行为及变形机制。Deng 等[42]基于 VPSC 模型,对皮尔格冷轧后的 Zr-4 锆合金管变形行为与织构演变进行了研究。
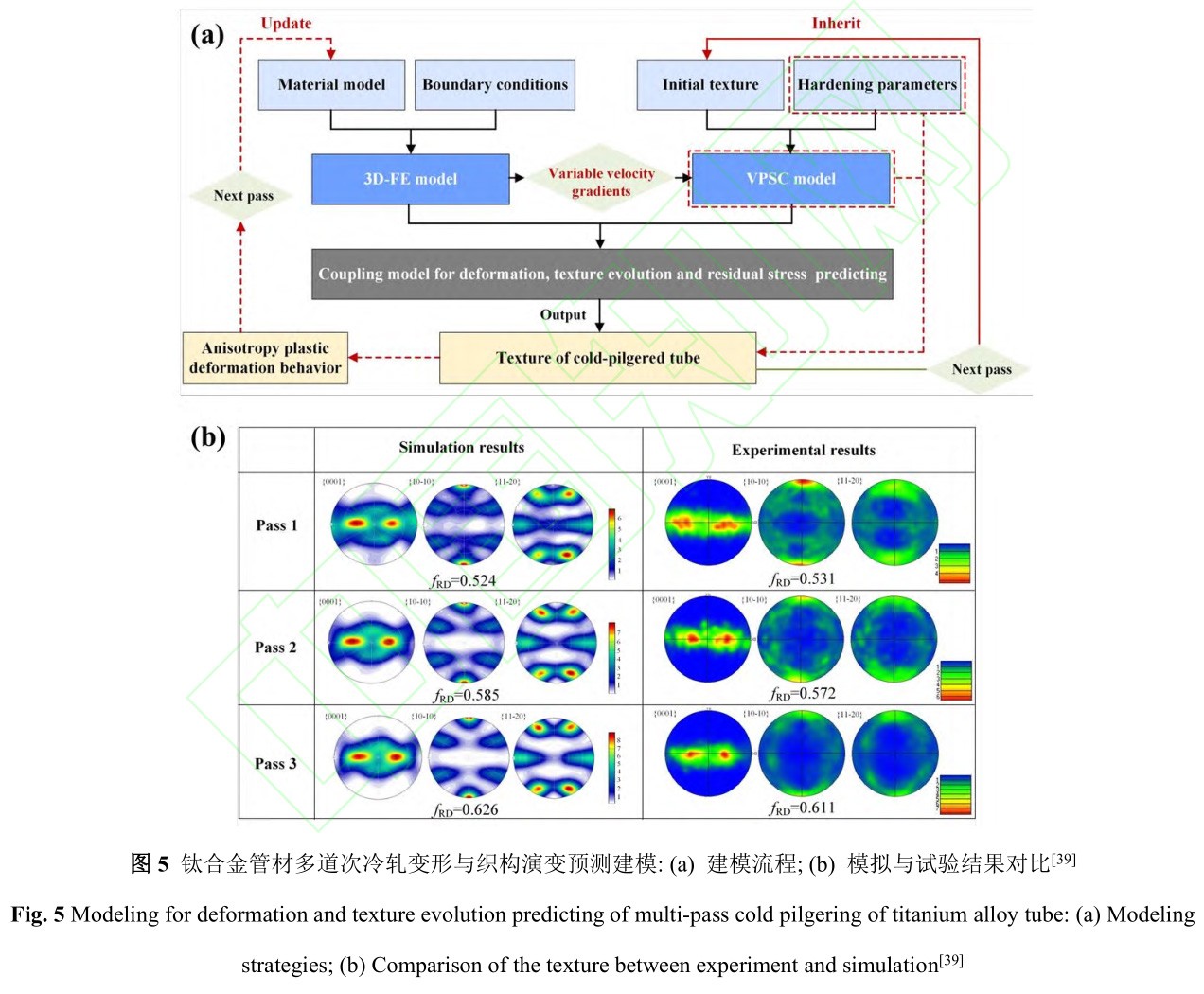
3 、管材冷轧过程微观织构演变机制与调控方法
3.1 管材冷轧过程微观织构演变规律与机制
由于管材皮尔格冷轧成形属于局部加载的增量成形过程,成形过程中应变路径的变化对管材织构的演变具有重要影响。基于数值模拟,国内外学者对管材皮尔格冷轧不同阶段管材变形特征进行了深入分析,图6(a)所示为钛合金管材冷轧过程不同变形阶段圆周应力分布特征,从图中可以看出冷轧不同变形阶段管材圆周同一位置应力状态基本是一致的,并且管材圆周应力呈中心对称分布。在孔型侧壁和孔型开口区域,管材主要受到三向压应力的作用,而在孔型开口区域,管材受到径向和周向压应力以及轴向拉应力的作用。冷轧
过程中管材在圆周不同位置应力大小具有显著差别,孔型侧壁区域所受到的径向和周向压应力相对较大,这主要是由于冷轧孔型为椭圆形,管材在上一行程轧制后被压扁,在下一行程轧制时经过回转工艺转到孔型侧壁区域,因此导致了侧壁区域的相对变形量较大。此外,也可以发现除圆周应力分布不均匀外,管材在壁厚方向应力也具有不均匀分布的特征。随着轧制的进行,管材在圆周以及壁厚方向变形逐渐趋于均匀,不同位置应力大小之间的差异也逐渐减小。图 6(b)为钛管冷轧过程不同变形阶段管材圆周应变分布特征,从图中可以明显的看出管材在皮尔格冷轧成形过程中经历了显著的不均匀变形。在减径段管材圆周方向为压应变,而径向和轴向均为拉应变,这里管材径向发生拉应变的主要原因是由于冷轧前期管材内表面与芯棒之间存在较大的间隙,当轧辊对管材外表面进行压下时,部分金属流向管材壁厚方向进而导致了管材壁厚的增厚。当冷轧进入到中后期,管材内壁与芯棒发生接触,管材呈现出了轴向为拉应变而径向和周向均为压应变的特征[44]。此外,冷轧过程包括 Q 值、送进量、回转角度及孔型开口大小等工艺参数的变化也被证实会
引起管材变形行为的差异[17, 20, 45]。
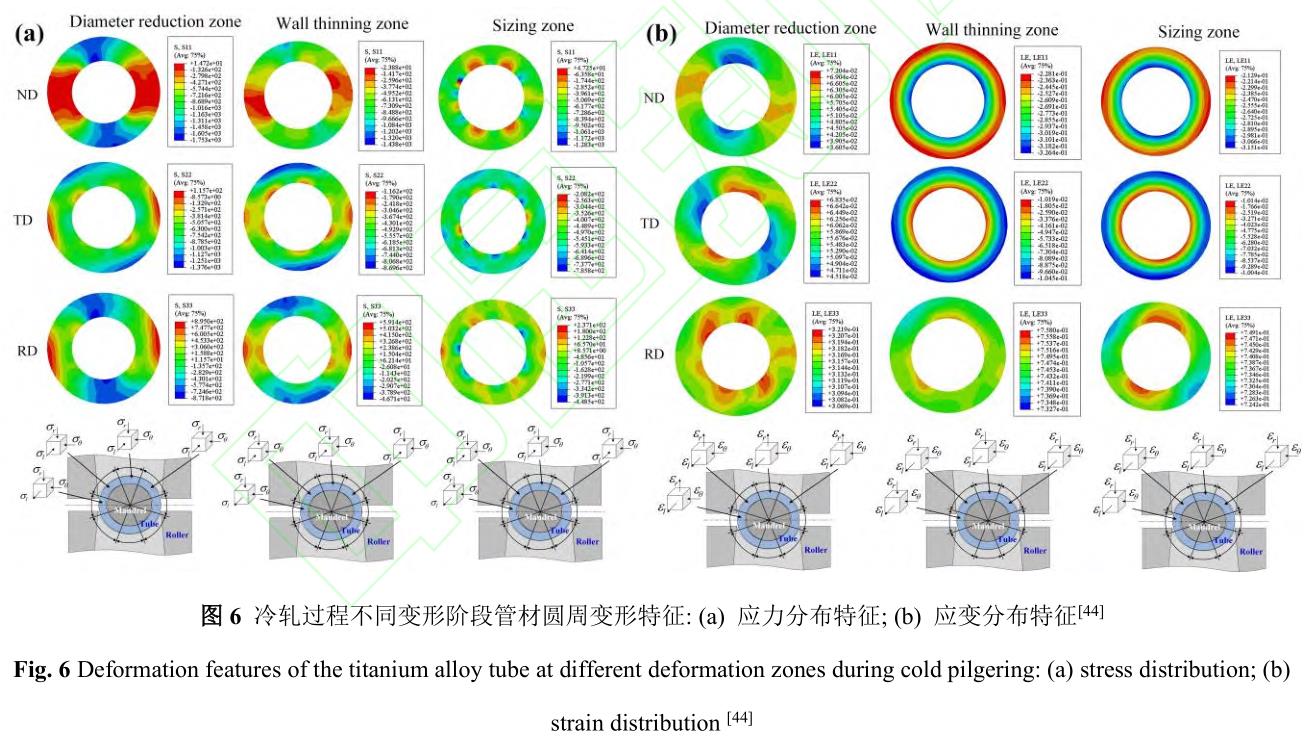
准确揭示和掌握冷轧过程中的微观织构演变规律,是冷轧工艺和模具优化设计以及织构调控的前提[45,46]。国内外学者对此做了大量的相关研究工作,Li 等[47]分析了高强钛管皮尔格冷轧过程中管材的织构演变规律,以应变比来表征管材在轧制过程中的变形模式并揭示了织构演变与应变比 α 之间的关系,其中应变比反映了管材周向与径向变形的差异,如图 7(a)所示,结果表明管材晶粒 c 轴在轧制过程中向最大压应变方向择优排列,管材在减径区、减径减壁区和定径区的应变比 α 的变化各不相同,在减径区应变比 α 约为-64º,在减径减壁区和定径区应变比 α 在 10º~64º 范围变化,管材经历了由周向织构向径向织构转变。Deng等[48]通过电子背散射衍射(Electron Back-Scattered Diffraction, EBSD)手段对 Zircaloy-4 管皮尔格冷轧不同变形阶段组织与织构演变进行了表征,如图 7(b)所示,并结合 VPSC 模拟对冷轧过程变形机制进行了分析,发现冷轧过程管材变形以{10-10}柱面滑移为主。Davies 等[49]采用 X 射线衍射(XRD)方法对不同送进量下钛合金管材皮尔格冷轧过程微观织构演变进行了测试对比,其中微观织构强度采用 Kearns-f 因子进行定量描述。
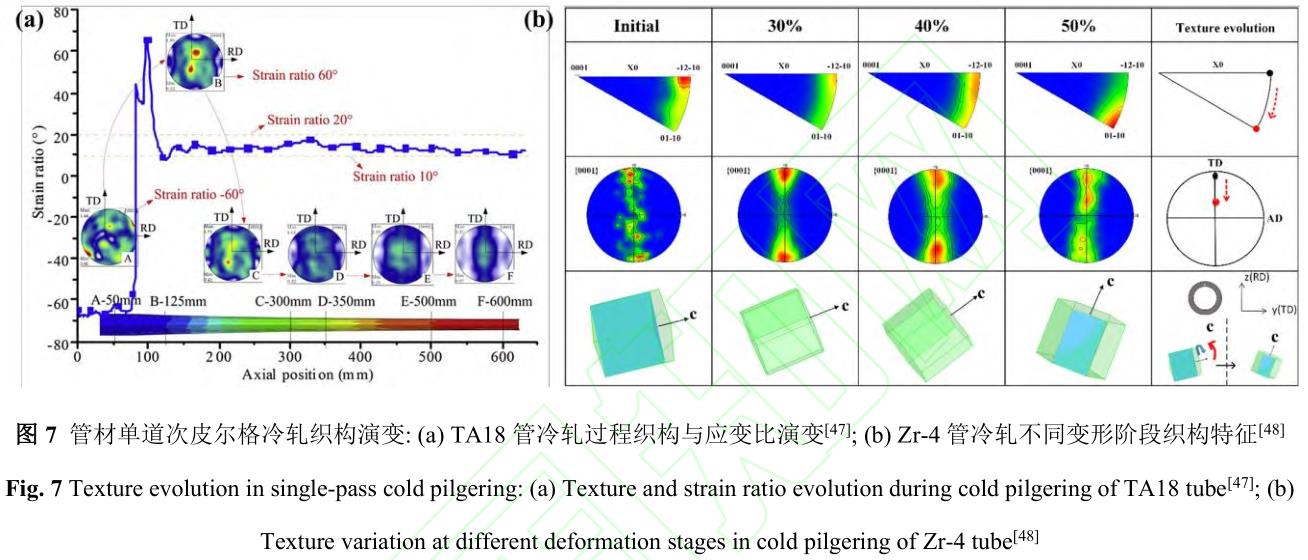
Wu 等[50]采用 EBSD 手段对不同 Ti-2Al-2.5Zr 钛管轧制过程不同变形阶段微观织构演变进行了表征分析,结果表明柱面滑移和{10-12}孪晶是最容易激活的两种变形机制,同时{10-12}孪晶的产生使得晶粒在轴向上的位向从<10-10>转向<11-20>。
上述研究均以管材某一层的织构作为反映管材整体织构分布的指标,并未考虑轧制过程管材沿壁厚方向显著不均匀变形及梯度织构分布特征。魏栋等[51]以不锈钢管冷轧过程为对象,基于有限元模拟分析了管材冷轧过程内外侧变形演变特征,结果表明冷轧不同阶段管材壁厚方向内外侧均表现出明显的变形程度差异。Kumar 等[52]结合实验表征和有限元模拟,揭示了锆合金管材冷轧过程微观组织与织构的梯度分布特征,同时表明管材壁厚不同位置的等效应变的差异引起管材壁厚方向梯度组织和织构形成的关键因素。Juarez 等
通过中子衍射和高能同步辐射 X 射线衍射的先进技术手段结合 VPSC 建模仿真,揭示了 Zircaloy-4 锆合金管材轧制过程局部织构演变规律与机理,如图 8 所示,结果表明管材在轧制全过程中管材壁厚方向均呈现出显著的梯度织构分布特征,且靠近内表面径向织构强度要明显高于外表面处径向织构强度,并且<11-20>//轴向的纤维织构得到增强同时晶粒 c 轴向管材径向偏转[53]。
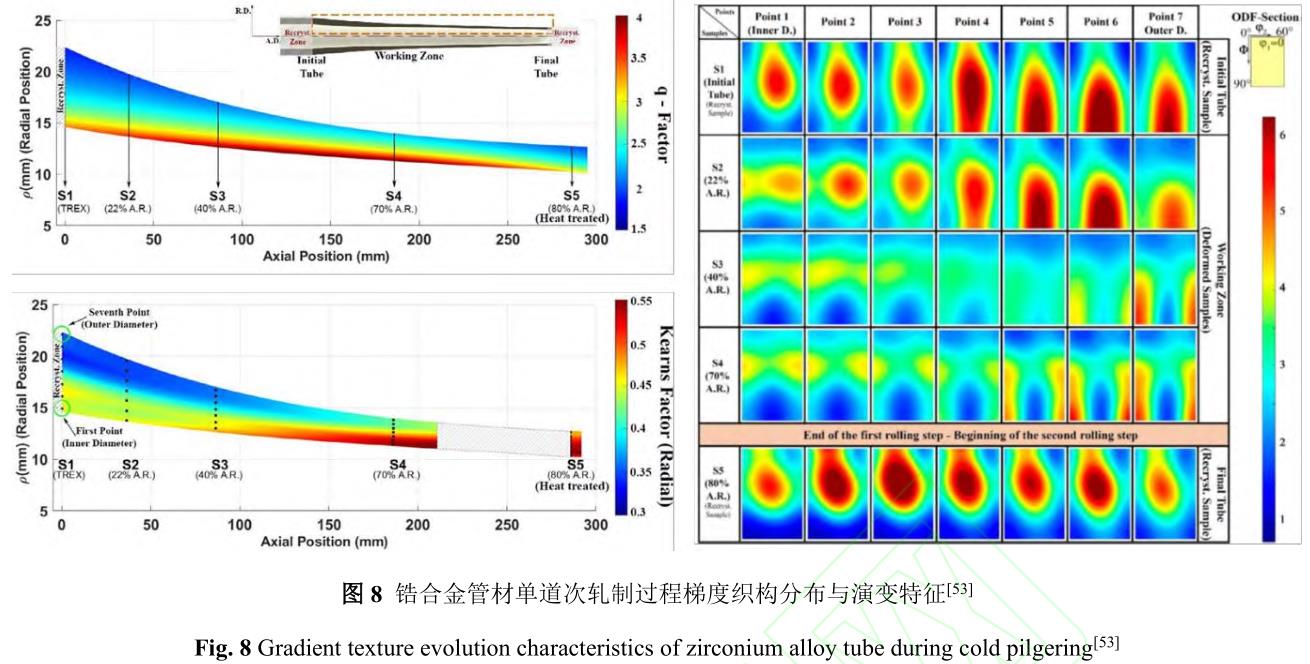
对于高强 TA18 等强度高且塑性相对较差的管材,往往需要进行多道次冷轧才能满足尺寸要求。为了揭示多道次冷轧过程中管材织构演变规律以及为织构预测和调控提供理论依据,Cook 等[54]以冷轧锆合金管为对象,发现在对轧后管材织构强度预测时,采用最后三道次的 Q 值的总和相比仅用最终道次的 Q 值在预测管材径向织构强度时更为准确。Saibaba[55]对比了三道次和二道次冷轧后锆合金管材织构强度,结果表明相比于三道次轧制,两道次轧制时由于每道次具有更大的变形量和 Q 值,使得轧后管材具有更高的径向织构强度。Krishna 等[56]研究揭示了 Zr-4 管在三道次冷轧过程中的织构演变,如图 9(a)所示,研究结果还表明相对较大的晶粒的取向在冷轧和退火过程中对织构演变的贡献也相对更大。Mukherjee 等[57]和 Gurao 等[58]均针对 Zr-4 管两道次冷轧过程中的织构演变进行了表征,研究结果发现冷轧过程中产生的残余应力对滑移变形与织构演变也具有一定的影响。Vakhitova 等[59]对比了 ODS 钢管两道次冷轧两种工艺方案对管材织构的影响,如图 9(b)所示,结果表明,增加中间去应力退火的方案最终管材<111>取向有一定增强,但晶粒细化效果不如无中间去应力退火的方案。邓偲瀛[60]通过对每道次初始管织构进行测试,基于 VPSC 模型模拟了锆管 3 道次和 4 道次冷轧过程织构演变规律。此外大量学者对于 HCP 结构金属退火过程织构演变进行了探究,结果表明再结晶退火并不能消除冷变形形成的织构,相反<10-10>和(0001)织构由于晶粒定向形核和长大的原因,导致其在退火过程中得到强化,而再结晶退火过程中材料仅发生完全再结晶但晶粒并未明显长大时,材料的织构特别是{0001}取向强度变化不显著[61-65]。
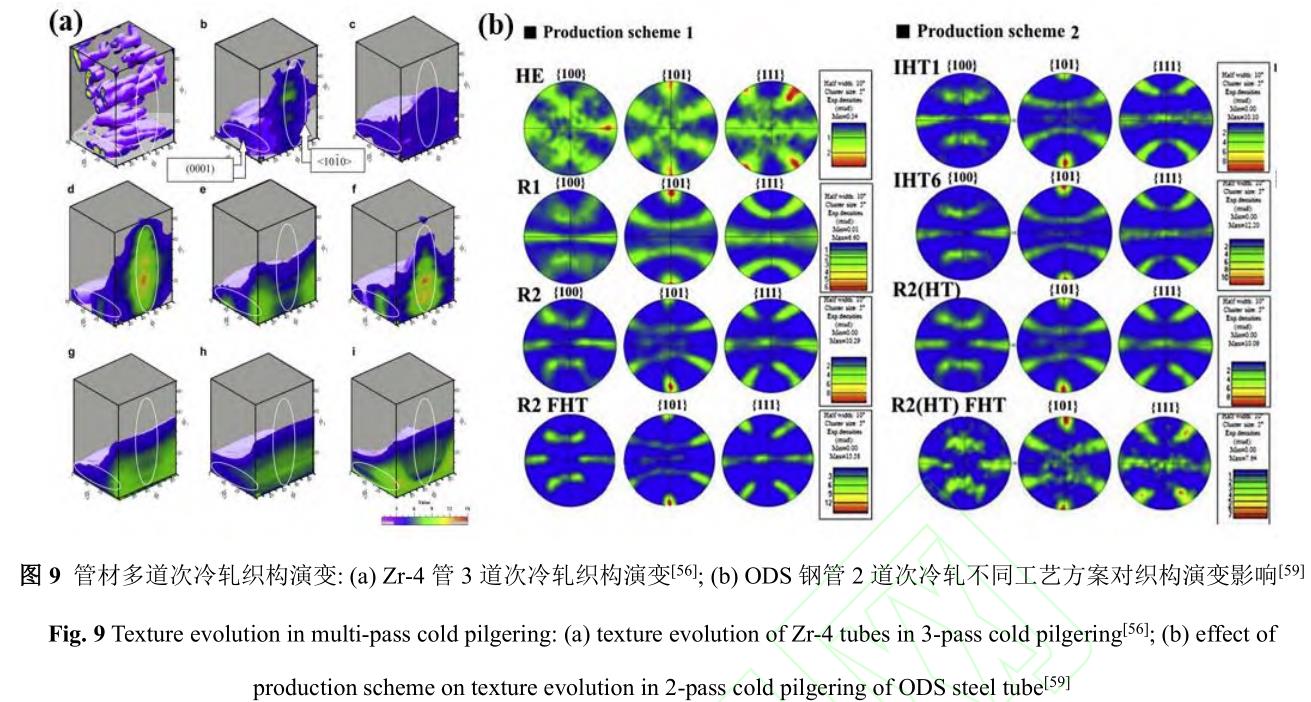
3.2 管材冷轧过程微观织构调控方法
针对管材冷轧过程微观织构调控,大量学者研究了成形参数对管材织构的影响。其中,Q 值被广泛认为是皮尔格冷轧过程中表征管材变形模式以及影响织构演变最重要的指标,其表示管材相对减壁量与相对减径量的比值。基于大量研究人员针对锆合金、钛合金等不同材料的管材皮尔格冷轧成形 Q 值对织构演变的影响规律研究结果[66-69],如图 10 所示,可以得出以初始随机管材织构为对象,当 Q>1 时,管材以减壁变形为主导,冷轧过程中大部分晶粒 c 轴向管材径向偏转从而使管材呈现径向织构,而当 Q<1 时,管材以减径变形为主导,大部分晶粒 c 轴向管材周向偏转从而使管材呈现周向织构。陈胜川等[70]通过研究不同 Q 值对小规格锆管织构和性能的影响,提出了 Q 值越大,晶粒纤维化和取向就越明显,当 Q 值在 1.54~2.46 的范围内,轧后管材具有良好的综合性能。
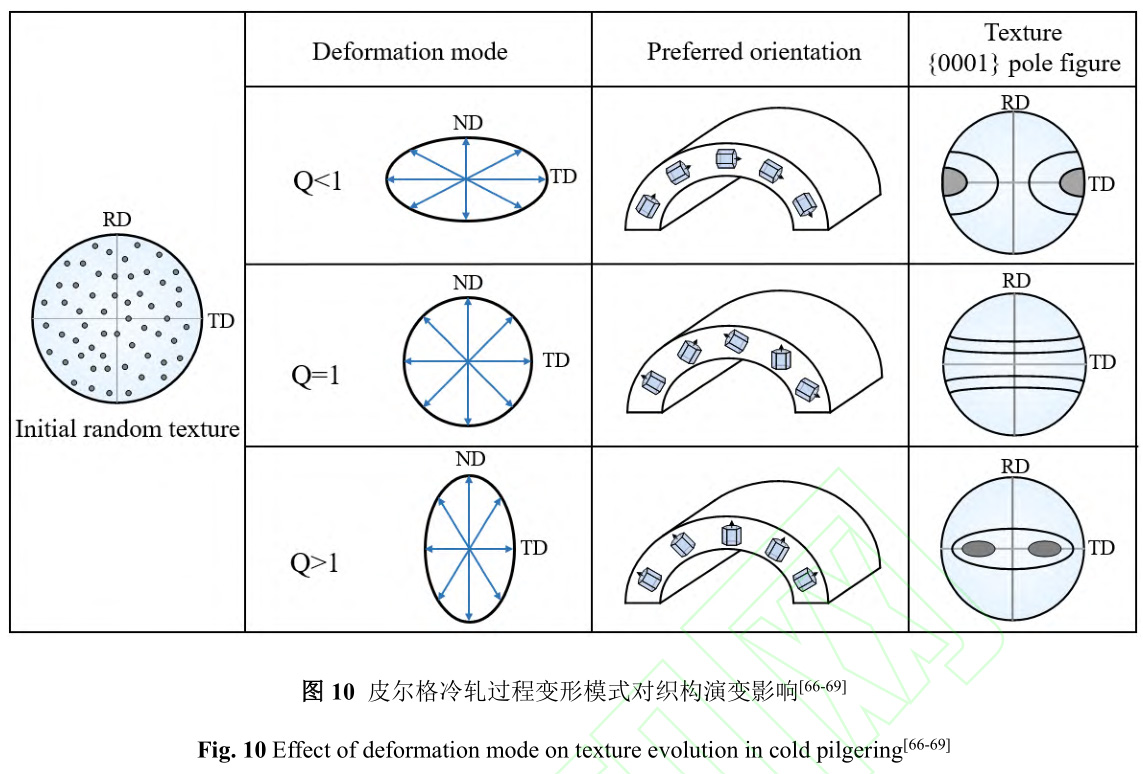
除变形模式之外,Girard 等[70]、廖强[72]和 Wang 等[73]以皮尔格冷轧 Zr-4 管、TA18 钛管和 GH4145 管为研究对象,发现变形程度即冷轧变形量对管材织构变化也具有重要影响。相比于轧制规格相关的整体变形模式与变形程度,由于皮尔格冷轧成形模具孔型的特殊性,其孔型设计对冷轧过程应变路径也具有显著影响[74,75],进而引起管材织构的波动。Zhang 等[76]以皮尔格冷轧锆合金为对象,针对不同的孔型设计方案对冷轧过程管材变形行为、瞬时 Q 值以及应变比 α 的变化进行了模拟分析,如图 11(a)所示,结果表明孔型曲线的变化对冷轧过程瞬时 Q 值和应变比 α 的演变具有显著影响,进而会引起管材织构的变化。Ubhi 等[77]通过改变减径量和减壁量的分配设计了不同的孔型曲线,分析了 TA18 钛管皮尔格冷轧织构演变规律,如图 11(b)所示,结果表明冷轧过程中可以通过改变模具设计来改变变形路径以增加径向织构密度。Wei 等[39]结合仿真模拟和实验研究阐明了初始织构、变形模式 Q 值和截面变形量对微观织构演变的交互作用机制,如图 12 所示,结果表明对于不同的初始织构管材,随着 Q 值与截面变形量的变化,拉伸孪晶 Tt 和锥面滑移 Py<c+a>激活程度的改变显著影响冷轧过程中管材的晶粒转动和取向变化;为提高轧后管材径向织构强度,Q 值和截面变形量存在对应的阈值,且该阈值随着初始管材 fND 值的升高不断增大,同时建立了高强 TA18 钛管冷轧成形参数与径向织构强度 Kearns-fND 值之间的定量关系,相比传统仅考虑 Q 值和变形量影响的 Kearns-fND值预测公式,其多元非线性回归结果 R 达到了 0.948。此外在多道次冷轧过程中,采用初始径向织构管坯以及 Q 值递增的道次变形分配设计方案,更有利于成品管材径向织构强度的提高。
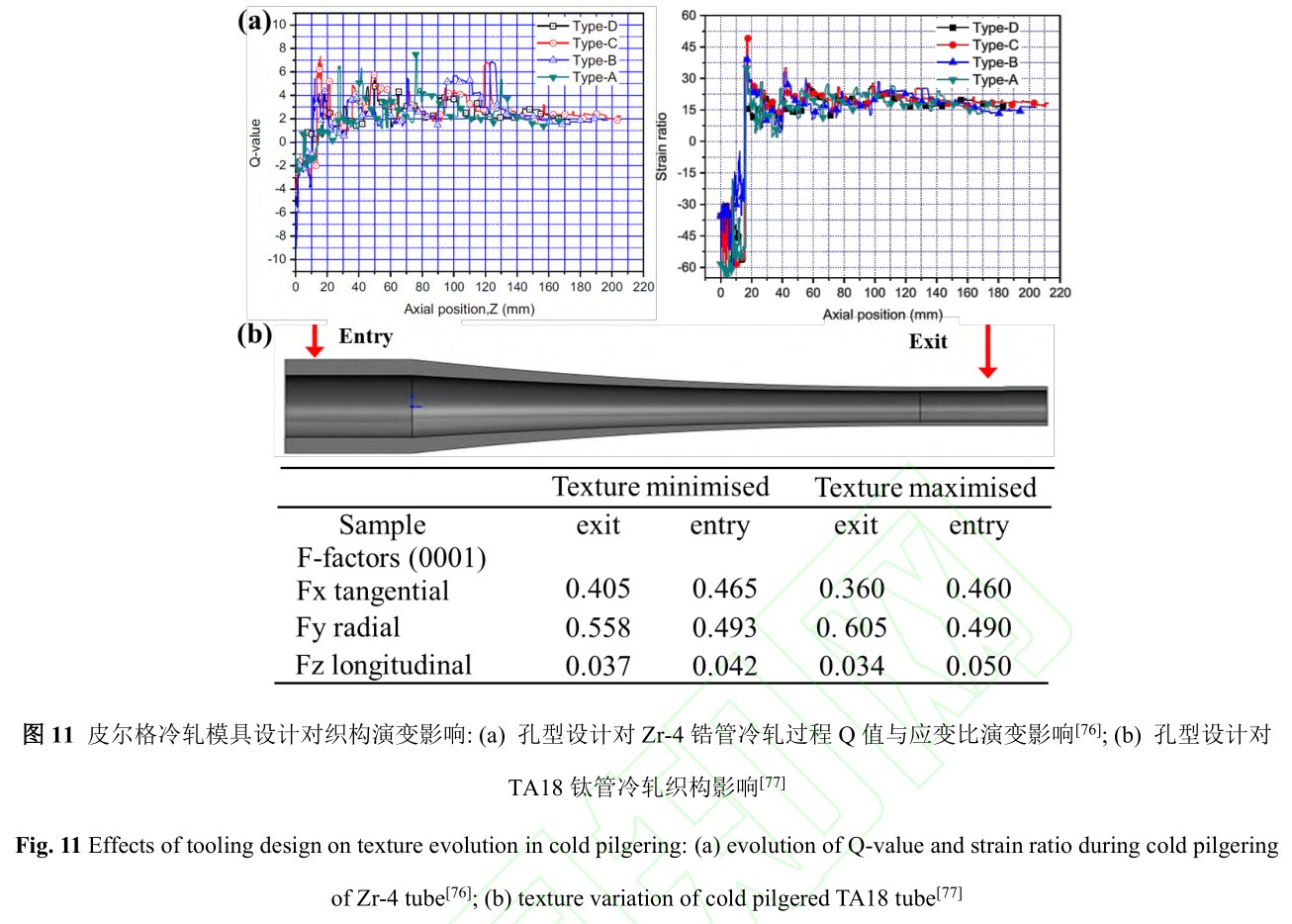
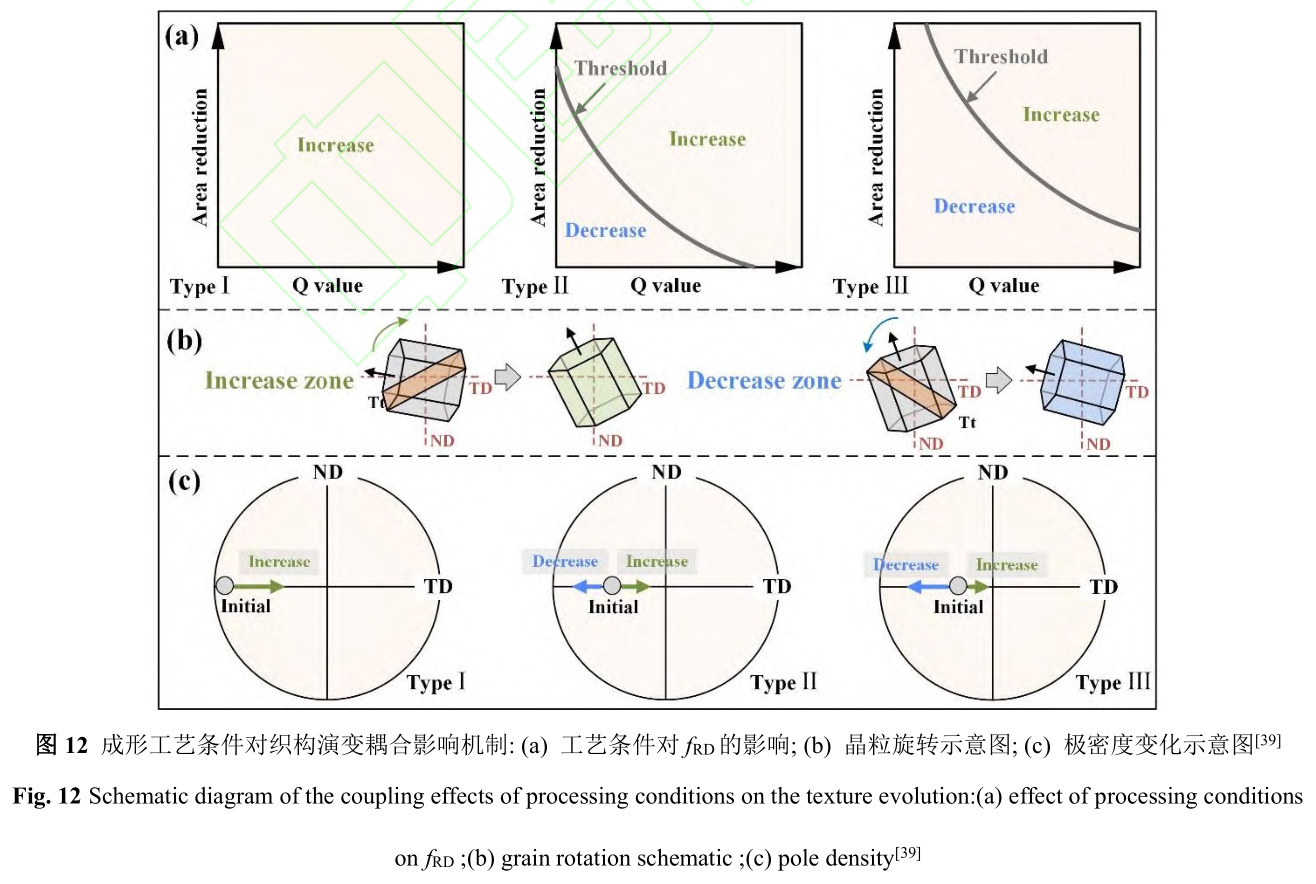
皮尔格冷轧后管材呈现出明显的微观织构分布从而导致管材表现出显著的各向异性,尤其对于密排六方(HCP)结构材料,织构对管材的后续成形性能和服役性能起着至关重要的作用[78, 79]。山特维克公司[80]对所生产的不同批次 TA18 管材进行了大量试验,并采用 CSR 值作为表征管材织构的指标,CSR>1.0 代表径向织构,而 CSR<1.0 则代表周向织构。He 等[81]以冷轧制备获得的近 α 钛合金管材为对象进行不同方向单向拉伸试验,发现管材轧后微观织构分布显著影响其在不同方向拉伸变形过程中各滑移机制的激活程度,进而导致管材表现出显著的各向拉伸变形行为。张旺峰等[82]对具有不同微观织构和 CSR 值的高强 TA18 钛管单向拉伸试验测试分析,结果表明具有径向织构管材在变形过程中趋向于缩径变形,而周向织构管材变形以壁厚减薄为主,CSR 值的增大对于管材屈强比和延伸率的提高具有促进作用。Wang[83]等研究也发现对于近 α 钛合金管材,径向织构强度的增强对于{10-10}<11-20>和{10-11}<11-20>滑移系 Schmid 因子的提升以及管材强度的增强起着至关重要的作用。此外,Wang 等[84]以具有初始周向微观织构分布特征的 Ti-2Al-2.5Zr钛管为对象,对压扁过程中管材不同变形区域复杂应力状态与变形行为进行了研究,并揭示了包括柱面和基面滑移以及拉伸孪晶在内的变形机制。Choi 等[85]通过试验发现锆合金管的抗腐蚀性能也取决于管材的织构分布情况,并且当径向织构具有一定程度的增强时,管材的抗腐蚀性能也相应的增强。此外,盛泽民等[86]利用 XRD 技术对轧制钛合金管材沿壁厚方向不同位置的微观织构进行了定量表征,结果表明轧后管材微观织构强度沿壁厚方向呈现出较为显著的梯度变化特征,并且非理想周向织构强度分布比例的增大将引起管材 CSR 值的下降。Li 等[87]结合试验与数值模拟,对比分析了高强 TA18 钛管不同微观织构分布特征对数控弯曲成形质量的影响,如图 13 所示,结果表明具有双峰织构分布特征的管材相比于近径向织构和近周向织构,包括壁厚减薄、截面畸变以及回弹在内的弯曲成形指标均更为优异。
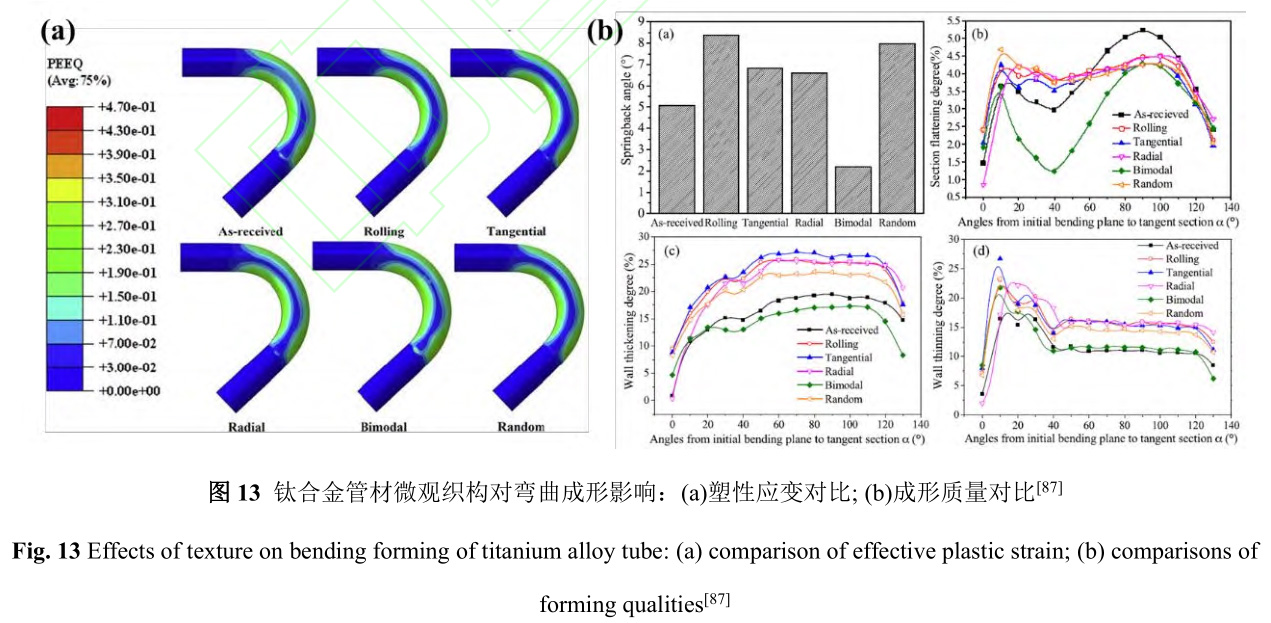
4、 结语与展望
高性能管材冷轧全过程复杂的外部加载路径、管材非线性力学响应以及显著的不均匀变形导致了管材微观织构演变规律复杂、难以精确控制,进而严重影响管材性能。目前针对高性能管材皮尔格冷轧成形过程微观织构预测建模、演变机制及调控方法等方面,国内外学者和相关企业已取得了重要的进展和成果。其中,基于有限元模型和晶体塑性模型的单道次冷轧宏细观数值模拟已取得了长足的发展,并且计算效率和预测精度也在随着模型的改进不断提高。此外,在先进数值模拟方法及试验表征手段快速发展的有利加持下,对管材冷轧全过程不均匀变形行为及整体微观织构演变规律与机制也有了更深入和准确的认识。在此基础上,明晰了管材冷轧过程包括初始织构、Q 值、变形量、孔型参数及退火温度等对微观织构演变的耦合作用规律,建立了有效的微观织构调控方法。但仍然存在一定的局限性和不足,面临以下问题需要解决:
(1) 目前关于管材冷轧成形宏观变形特征和微观织构演变数值预测模型主要针对于单道次冷轧过程,建立能够准确预测管材多道次冷轧全过程的宏细观数值模型,有望为深入探究冷轧全过程微观织构演变机制及其调控方法提供重要的定量分析手段。
(2) 当前对于管材冷轧过程织构演变与调控的研究主要考虑的是管材整体织构分布特征和强度,而冷轧过程中局部加载下壁厚方向显著不均匀变形诱导的变形机制的差别势必会引起梯度织构的形成,进一步明晰多道次冷轧中梯度织构的形成与演变机制,是实现织构与性能稳定控制的基础。
(3) 微观织构是引起管材各向异性和拉压非对称性力学行为差异的关键因素,进而影响管材的力学性能、后续成形性能及疲劳服役等性能。面向管材综合性能协同提升目标,阐明微观织构对管材性能影响并建立关联关系,为微观织构调控提供基础和依据对突破管材全流程形性一体化设计制造瓶颈具有重要意义。
参考文献
1 Cao C X. Rare Metals Letters, 2006, 25, 17-21. (in Chinese).
曹春晓. 稀有金属快报, 2006, 25, 17-21.
2 Li Y, Zhao Y Q, Zeng W D. Materials Reports, 2020, 34(S1), 28-282.
李毅, 赵永庆, 曾卫东. 材料导报, 2020, 34(S1), 28-282.
3 Zhang W F, Li Y, Wang Y H, et al. Materials Reports, 2011, 25(23), 133-137.
张旺峰, 李艳, 王玉会, 等. 材料导报, 2011, 25(23), 133-137.
4 Yang H, Li H, M J, et al. International Journal of Machine Tools and Manufacture, 2021, 166, 103742.
5 Furugen M, Hayashi C. Journal of Mechanical Working Technology, 1984, 10, 273-286.
6 Stinnertz H. Tube Pipe Technologies, 1988, 2, 27-31.
7 Ragger K S, Primig S, Daniel R, et al. Materials Characterization, 2017, 128: 257-268.
8 H. Abe, T. Nomura, Y. Kubota. Journal of Materials Processing Technology, 2014, 214, 1627-1637.
9 Wei D, Chen Y Y, Li H, et al. International Journal of Mechanical Science, 2022, 225, 107366.
10 Musazadeh M H, Vafaei R, Sharifi E M, et al. Metallurgical and Materials Transactions B, 2018, 49, 3030-3042.
11 Meredith S E, Schemel J H. International Journal of Fatigue, 1990. 12, 528-528.
12 Deng S Y, Wang S W, Chen S F, et al. Journal of Nuclear Materials, 2024, 589, 154846.
13 Li H, Fu M W. Elsevier, 2019, 307-311.
14 Hsiang S, Lin Y W. Journal of Materials Processing Technology, 2007, 192-193, 292-299.
15 Liu F, Chen C, Niu J, et al. Materials Science and Engineering C, 2015, 48, 400-407.
16 Chu Z B, Wei D, Jiang L Y, et al. Journal of Iron Steel Research International, 2018, 25, 398-408.
17 Chu Z B, Xue Z Y, Zhang D, et al. Journal of Iron Steel Research International, 2019, 26, 593-601.
18 Huml P, Fogelholm R. Journal of Materials Processing Technology, 1994, 42, 167-173.
19 Pociecha D, Boryczko B, Osika J, et al. Archives of Civil and Mechanical Engineering, 2014, 14, 376-382.
20 Liu J L, Zeng W D, Du Z L, et al. Titanium Industry Progress, 2015, 32, 21-25. (in Chinese).
刘江林, 曾卫东, 杜子龙, 等. 钛工业进展, 2015, 32, 21-25.
21 Mulot S, Hacquin A, Montmitonnet P, et al. Journal of Materials Processing Technology, 1996, 60, 505-512.
22 Montmitonnet P, Logé R, Hamery M, et al. Journal of Materials Processing Technology, 2002, 125, 814-820.
23 Huang L, Xu Z, Dai C, et al. Rare Metal Materials and Engineering, 2013, 42, 524-529.
黄亮, 徐哲, 代春, 等. 稀有金属材料与工程, 2013, 42, 524-529.
24 Chu Z B, Lv Y Y. Huang Q X, et al. Journal of Sichuan University (Engineering Science Edition), 2015, 47,165-171. (in Chinese).
楚志兵, 吕阳阳, 黄庆学, 等. 四川大学学报(工程科学版), 2015, 47, 165-171.
25 Lodej B, Niang K, Montmitonnet P, et al. Journal of Materials Processing Technology, 2006, 177, 188-191.
26 Strickner G, Ragger K S, Hatzenbichler T, et al. Steel Research International, 2012, 71-74.
27 Deng S, Song H, Zheng C, et al. International Journal of Material Forming, 2019, 12, 321-329.
28 Azizoglu Y, Gardsback M, Sjoberg B, et al. International Conference on the Technology of Plasticity, UK, 2017,2370-2375.
29 Azizoglu Y, Sjoberg B, Lindgren L. Journal of Manufacturing Processes, 2024, 112, 112-125.
30 Chung S H, Jeong S W, Chung W J, et al. Journal of Manufacturing Processes, 2023, 95, 217-228.
31 Molinari A, Canova G R, Ahzi S. Acta Metallurgica, 1987, 35, 2983-2994.
32 Lebensohn R A, Tome C N. Acta Metallurgica et Materialia, 1993, 41, 2611-2624.
33 Knezevic M, Lebensohn R A, Cazacu O, et al. Materials Science and Engineering A, 2013, 564, 116-126.
34 Zhang H, Sheng Z M, Zhang W F, et al. Journal of Materials Engineering and Performance, 2015, 24, 2312-2318.
35 Gupta A, Khatirkar R K, Dandekar T, et al. Journal of Alloys and Compounds, 2021, 850, 156824.
36 Lebensohn R A. González M I, Tomé C N. et al. Journal of Nuclear Materials, 1996, 229, 57-64.
37 Zhang H Q. Master’s thesis, Northwestern Polytechnical University, 2015. (in Chinese).
张海芹. 硕士学位论文, 西北工业大学, 2015.
38 Li H, Wei D, Zhang H Q, et al. Journal of Materials Processing Technology, 2020, 279: 116520.
39 Wei D, Chen Y Y, Yang H, et al. Journal of Alloys and Compounds, 2024, 997:174835.
40 Kaushik L, Kim M S, Singh J, et al. International Journal of Plasticity, 2021, 141, 102989.
41 Yang H, Li H, Ma J, et al. International Journal of Plasticity, 2020. 127, 102650.
42 Deng S, Song H, Liu H, et al. International Journal of Solids and Structures, 2021, 213, 63-76.
43 Wei D. P.h.D. Thesis, Northwestern Polytechnical University, 2022. (in Chinese).
魏栋. 博士学位论文, 西北工业大学, 2022.
44 Chu Z B, Wei D. Yang Y L, et al. Chinese Journal of Engineering, 2017, 39(5), 747-755. (in Chinese).
楚志兵, 魏栋, 杨彦龙, 等. 工程科学学报, 2017, 39(5), 747-755.
45 Abe H, Furugen M. Journal of Materials Processing Technology, 2012, 210, 1687-1693.
46 Singh J, Mahesh S, Kumar G, et al. Metallurgical and Materials Transactions A, 2015, 46, 1927-1947.
47 Li H, Zhang H Q, Yang H, et al. International Journal of Plasticity, 2017, 90, 177-211.
48 Deng S, Song H, Zheng C, et al. Materials Science and Engineering A, 2019, 764: 138280.
49 Davies R W, Khaleel M A, Kinsel W C, et al. Journal of Engineering Materials and Technology, 2002, 124,125-134.
50 Wu J, Wang L, Liu X, et al. Rare Metal Materials and Engineering, 2022, 51(04), 1145-1151.
51 Wei D, Chu Z B, Huang Q X, et al. Journal of Plasticity Engineering, 2016, 23(5), 89-95. (in Chinese).
魏栋, 楚志兵, 黄庆学, 等. 塑性工程学报, 2016, 23(5), 89-95.
52 Kumar G, Balo S, Dhoble A, et al. Metallurgical and Materials Transactions A, 2017, 48, 2844-2857.
53 Juarez G, Alvarez M A V, Santisteban J, et al. Journal of Nuclear Materials, 2022, 558, 153382.
54 Cook C S, Sabol G P, Sekera K P, et al. ASTM International, 1991, 80-98.
55 Saibaba N. Journal of Nuclear Materials, 2008, 383, 63-70.
56 Krishna K V M, Sahoo S K , Samajdar I, et al. Journal of Nuclear Materials, 2008, 383, 78-85.
57 Mukherjee P, Gayathri N, Chowdhury P S, et al. Journal of Nuclear Materials, 2013, 434, 24-30.
58 Gurao N P, Akhiani H, Szpunar J A. Journal of Nuclear Materials, 2014, 453, 158-168.
59 Vakhitova E, Sornin D, Barcelo F, et al. Journal of Nuclear Materials, 2017, 494, 20-28.
60 Deng S Y. P.h.D. Thesis, University of Science and Technology of China, 2020. (in Chinese).
邓偲瀛. 博士学位论文, 中国科学技术大学, 2020.
61 Haq A J, Banerjee S. Bulletin of Materials Science, 1992, 15: 289-296.
62 Zhu K Y, Chaubet D, Bacroix B, et al. Acta Materialia, 2005, 53(19), 5131-5140.
63 Gerspach F, Bozzolo N, Wagner F. Scripta Materialia, 2009, 60, 203-206.
64 Liu C, Li G, Chu L, et al. Materials Science and Engineering A, 2018, 719, 147-154.
65 Wang Y, He W, Liu N, et al. Materials Characterization, 2018, 136, 1-11.
66 Murty K L, Charit I. Progress in Nuclear Energy, 2006, 48: 325-359.
67 Hong Q, Qi L Y, Zhao B, et al. Titanium Industry Progress, 2016, 33, 16-19. (in Chinese).
洪权, 戚运莲, 赵彬, 等. 钛工业进展, 2016, 33, 16-19.
68 Singh J, Mahesh S, Roy S, et al. Journal of Materials Processing Technology, 2016, 237, 126-138.
69 Yang Q, Hui S, Ye W, et al. Materials. 2022, 15, 817.
70 Chen S C, Zhu B H, Yuan H J, et al. Titanium Industry Progress, 2016, 33: 25-29. (in Chinese).
陈胜川, 朱宝辉, 袁红军, 等. 钛工业进展, 2016, 33: 25-29.
71 Girard E, Guillen R, Weisbecker P, et al. Journal of Nuclear Materials, 2001, 294, 330-338.
72 Liao Q, Qu H L, Yang Y S, et al. Titanium Industry Progress, 2012, 29, 26-28. (in Chinese).
廖强, 曲恒磊, 杨亚社, 等. 钛工业进展, 2012, 29, 26-28.
73 Wang L, Liu J, Wang Z, et al. Materials Science and Engineering A, 2022, 832, 142464.
74 Lee S K, Lee K H. Applied Science, 2021, 11, 11265.
75 Wang Q, Huang P, Yin Y. The International Journal of Advanced Manufacturing Technology, 2021, 112, 803-818.
76 Zhang H Q, Wang X F, Wei B L, et al. The International Journal of Advanced Manufacturing Technology, 2017,92, 2169-2183.
77 Ubhi H S, Houghton A, Saithala J. Materials Science Forum, 2011, 702-703, 643-646.
78 Toualbi L, Cayron C, Olier P, et al. Journal of Nuclear Materials, 2013, 442, 410-416.
79 Guo W, Li G, Han F, et al. International Journal of Fatigue. 2022, 163, 107046.
80 Forney C E, Meredith S E. Sandvik Special Metals, 1990, 25-38.
81 He S, Zeng W, Zhao Z, et al. Journal of Alloys and Compounds. 2022, 909, 164785.
82 Zhang W F, Zhang H, Yan M Q, et al. Titanium Industry Progress, 2018, 35: 22-25. (in Chinese).
张旺峰, 张晖, 颜孟奇, 等. 钛工业进展, 2018, 35: 22-25.
83 Wang W R, Yuan L H, Zhang H, et al. Journal of Alloys and Compounds, 2023, 931, 167558.
84 Wang S, Jin G, Wu Y, et al. Journal of Materials Science and Technology. 2021, 90,108-120.
85 Choi Y, Shin E J, Inoue H. Physica B. 2006, 385-386, 529-531.
86 Sheng Z M, Zhang H, Zhang W F, et al. Rare Metal Materials and Engineering, 2017, 46(10), 3073-3076. (in Chinese).
盛泽民, 张晖, 张旺峰, 等. 稀有金属材料与工程, 2017, 46(10), 3073-3076.
87 Li H, Hu X, Yang H, et al. International Journal of Plasticity, 2016, 82, 127-158.
相关链接