传统工业金属材料的表面优化处理方法主要包括渗碳、渗氮、碳氮共渗等表面化学热处理方法,这些方法虽然可以通过改变金属材料表面的成份和组织,从而改善材料表面的机械性能,这些基于常规热扩散原理,往往处理温度较高,处理时间很长、能耗大,金属基底容易软化,不能作为最终热处理,而且效率很低。
上世纪中期开发的工具镀层主要着眼于提高镀层的耐磨性,往往将硬度作为一个最主要性能指标。应用比较广泛的刀具镀层主要有Ti基Cr基镀层,最典型的镀层有TiC、TiN、
CrTiAlN等镀层。
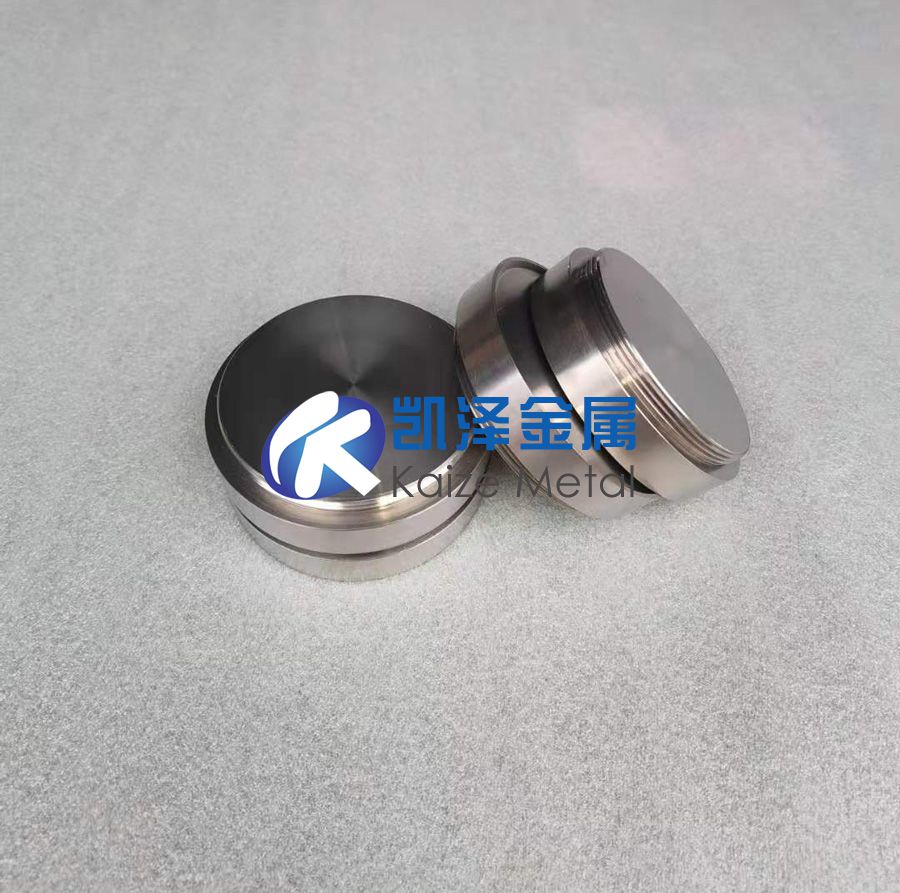
Ti基镀层以TiN为主,通过添加其它元素进一步改善镀层性能。TiN镀层是国内外刀具镀层研究最为成熟的代表之一,也是一种最为常用的硬质镀层。TiN镀层凭借其硬度高、摩擦系数低,而且红硬性好,韧性、高温抗氧化性也不错的优势而被广泛地应用到许多领域,其中最典型的应用就是切削刀具和仿金装饰镀层。在高速切削的条件下,TiN镀层的硬度、抗氧化、摩擦系数等性能仍然满足不了使用要求。TiC镀层硬度比TiN更高,但其脆性比较大,在使用过程中容易崩落。
在新型镀层的研发历程中,TiN和TiC通常被认为是第一代硬质镀层。应用和研究发现,TiN镀层的性能可以通过TiN与其他氮化物、碳化物、硼化物进行混合和复合,以及用其他金属元素部分或全部取代TiN中的Ti而得到改善,其中最为典型的两种镀层是Ti(C,N)和(Ti,A1)N,这些镀层又被誉为第二代硬质镀层。氮碳化钛Ti(C,N)被认为是TiN和
TiC的固溶体,硬度高于TiC和TiN,具有较低的摩擦系数和磨损率,具有TiC和TiN的综合性能,兼有两者的特性和优点,可以进一步提高切削刀具的生产效率和使用寿命,是一种
较理想的刀具镀层材料。Ti(C,N)镀层刀具性能的改善归因于Ti(C,N)和硬质合金刀具优异的结合力,但Ti.C-N的热稳定性和抗氧化性能不如TiN和TiC。如今,Ti(C,N)镀层己广泛用于切削工具、钻头、模具等机械、汽车制造和航天航空等领域。
随着复合镀层的进一步开发,人们仍以TiN为基本组元,采用其他金属元素,包括A1、Zr、Ta等替代或部分替代Ti;与N对应的元素则加入C成为C、N化合物,进而形成三元、
四元甚至多元镀层,以实现提高镀层的性能的目的,常见的镀层除了Ti—C-N之外,还有Ti.B-N、Ti.A1.N镀层等"·引。用多组元技术来改善PVD镀层的性能,以适应不同需要成为PVD技术发展方向之一。
含Cr元素的镀层常被用于高温下需要有好的抗腐蚀性能和高硬度的应用领域,与已经广泛应用的TiN镀层相比,Cr基镀层与铁衬底有更好的结合强度。如NCr-N系列镀层,因具有较好的膜基结合、良好的化学稳定性和抗腐蚀性的优点,被作为耐磨镀层用于工具和切削刀具的表面强化,在表面防腐和装饰业也有一定的应用。另外,’在PVD方法制备镀层
的过程中,Cr原子的溅射产额比Ti原子的溅射产额高,使得Cr-N系列镀层具有比T.N高的制备效率,有利于大批量的工业生产,Cr基镀层被视为一种具有发展潜力的刀具镀层。
实践中,在提高镀层硬度的同时往往脆性增大,然而某些受冲击的加工条件对切削刀具韧性要求高,单纯提高硬度不能满足使用要求。操作中往往通过制作多层膜的方法来改善镀层韧性,或增加过渡层、渗或注入层等措施提高镀层膜基结合力。Holleck等[把多层镀层分为三类:一类是低单层数的镀层,如TiN/TiC/TiN多层,TiC/(Ti,A1)N多层,
TiN/TiCN/TiC多层,因工艺相对容易,目前绝大多数多层镀层属于此类;第二类是由两种不同镀层组成的高层数镀层,如TiC/TiB2多层;第三类是超点阵镀层,由化学键和原子半径及点阵常数相近的镀层组成的高层数镀层,一般周期厚度为5.25nm。最早的超点阵结构镀层是TiNⅣN和TiN烈bN,这种结构的镀层较同种材料组成的匀质镀层具有更高的硬度和韧性。 Herranentl认为:多层结构镀层中增加了大量的界面并减小了晶粒尺寸,便于晶粒尺寸和结构的调整,降低残余应力,有利于提高镀层的结合强度,优化镀层的硬度和韧性比,实现镀层的多功能性能。
相关链接