一、钛铝靶的定义
钛铝靶是由钛(Ti)和铝(Al)按特定原子比例组成的合金材料,主要用于物理气相沉积(PVD)、磁控溅射等表面镀膜工艺。根据成分和结构不同,可分为TiAl(γ-TiAl相)、Ti3Al(α2-Ti3Al相)以及梯度复合靶材(如TiAl/TiN多层结构)。其典型应用场景包括半导体制造、航空发动机涂层、生物医疗植入体等。
二、钛铝靶的核心性能特点
1、高温性能卓越
抗氧化性:
在800~900℃高温下,表面生成致密Al2O3氧化膜,氧化速率低于0.1mg/(cm²·h)(传统镍基合金的1/5)。
高温强度:
600℃时抗拉强度仍保持400MPa以上(比钛合金高50%),蠕变抗力显著优于传统高温合金。
热膨胀系数匹配:
线膨胀系数为9.5×10⁻⁶/K(与碳纤维复合材料接近),适用于高温部件界面涂层。
2、轻量化优势
低密度:
典型密度3.9~4.2g/cm³(仅为镍基合金的60%),可显著降低航空发动机叶片等旋转部件的惯性载荷。
高比强度:
比强度(强度/密度)达110MPa·cm³/g(不锈钢的3倍),是航天器减重的关键材料。
3、耐腐蚀与耐磨性
耐蚀性:
在5% NaCl盐雾环境中,年腐蚀速率<0.01mm(优于316L不锈钢)。
耐磨性:
溅射TiAlN涂层的显微硬度达2800HV(是纯钛涂层的4倍),摩擦系数可低至0.15。
4、功能化表面特性
薄膜可控性:
溅射沉积速率可达200nm/min(功率密度5W/cm²),成膜均匀性误差<±3%。
界面结合力:
与基体材料的结合强度≥70MPa(通过划痕法测试),满足半导体器件的热循环需求。
5、生物相容性
医疗适配性:
表面氧化生成的TiO2/Al2O3混合层,符合ISO 10993生物相容性标准,细胞存活率>95%。
抗菌性能:
离子注入Ag的TiAl涂层对金黄色葡萄球菌抑菌率>99.9%(ASTM E2149测试)。
6、电磁性能
电阻率:
室温电阻率约200μΩ·cm(介于金属与半导体之间),适合制备高介电薄膜。
抗电磁干扰:
镀TiAl涂层的电子器件外壳,可将电磁屏蔽效能(SE)提升至60dB以上(1GHz频率)。
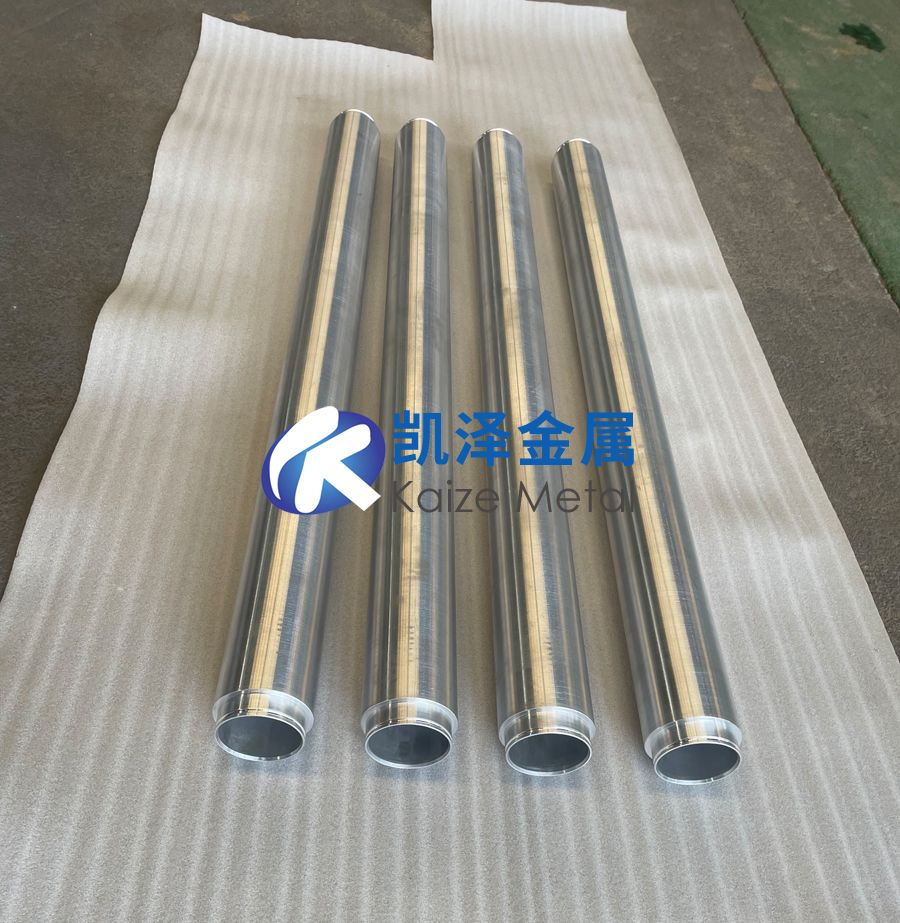
三、性能参数对比(典型值)
性能指标 | TiAl靶材 | 纯钛靶材 | 镍基合金(Inconel 718) |
密度 (g/cm³) | 3.9~4.2 | 4.5 | 8.2 |
熔点 (℃) | 1460 | 1668 | 1350 |
室温硬度 (HV) | 300~400 | 120~150 | 250~350 |
600℃强度 (MPa) | 380~420 | 120~150 | 550~600 |
耐盐雾腐蚀速率 | <0.01mm/year | 0.05mm/year | 0.02mm/year |
四、特殊工艺强化性能
1、纳米结构设计:
通过机械合金化制备纳米晶TiAl(晶粒尺寸<50nm),使断裂韧性提升至25MPa·m¹/²(粗晶材料的2倍)。
2、梯度复合技术:
制备TiAl/TiB2梯度靶材,表面硬度达3500HV,同时保持基体韧性(断裂应变>8%)。
3、稀土改性:
添加0.5% Y2O3可使高温抗氧化温度提升至1000℃,氧化膜粘附性提高30%。
五、应用导向的性能优化
1、半导体领域:
采用超高纯TiAl靶(纯度>99.999%),金属杂质总量≤10ppm,确保薄膜漏电流<10⁻⁸A/cm²。
2、航空领域:
开发定向凝固TiAl靶材,高温疲劳寿命达10⁷次循环(载荷500MPa,频率20Hz)。
3、新能源领域:
多孔TiAl靶(孔隙率30%)用于固态电池界面层,锂离子迁移数提升至0.85。
六、制造工艺核心技术
1、原料配比与预处理
合金设计:Al含量控制在48-52 at.%(原子百分比),采用TiAl3/TiAl双相结构优化塑性
粉末冶金法:
氩气雾化制备预合金粉末(粒径≤45μm)
真空热压烧结(1200℃/150MPa/4h)实现99.5%理论密度
熔炼铸造法:
真空电弧熔炼(VAR)+ 电磁搅拌,成分偏析<0.3%
定向凝固技术获得柱状晶组织,高温强度提升40%
2、成型与加工
热等静压(HIP):
1150℃/100MPa处理2小时,消除内部孔隙
晶粒尺寸控制在10-20μm范围
塑性变形加工:
多向锻造(800℃)实现超细晶(≤5μm)
轧制工艺使靶材密度达到4.2g/cm³(理论值98%)
3、表面处理与检测
精密加工:线切割+纳米级抛光(Ra≤0.05μm)
背板焊接:Cu/CuCrZr合金背板,采用真空钎焊(Ag基焊料)
无损检测:
超声波探伤(灵敏度Φ0.5mm平底孔)
残余应力检测(XRD法,控制<50MPa)
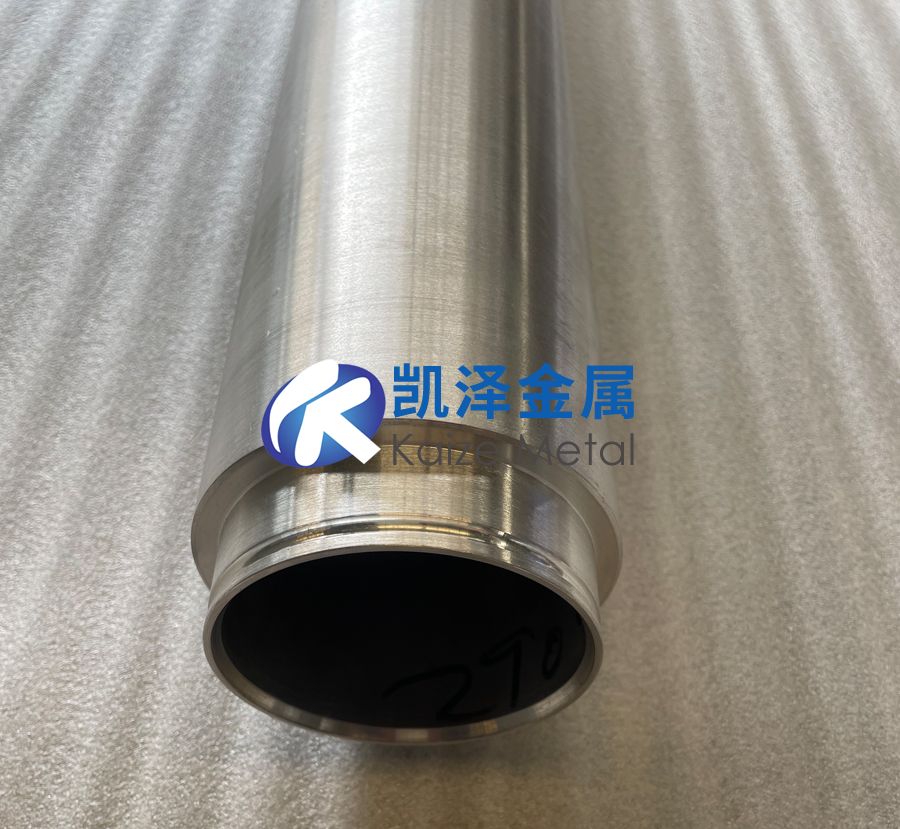
七、常用标准体系
1、国际标准
ASTM B928:规定Ti-Al合金板材的力学性能(抗拉≥550MPa,延伸率≥6%)
SEMI F47:半导体用靶材纯度要求(金属杂质总量≤50ppm,O≤800ppm)
AMS 4998:航空级TiAl铸件标准(疲劳寿命≥1×10^7次@600℃)
2、国内标准
GB/T 3620.1:钛及钛合金牌号与化学成分
SJ/T 11696:溅射靶材结合强度(≥70MPa)与电阻率(≤200μΩ·cm)
HB 7784:航空发动机叶片用TiAl涂层厚度公差(±5μm)
3、关键性能指标
密度:≥3.9g/cm³
晶粒度:ASTM E112标准6-8级
溅射速率:DC溅射≥150nm/min(功率5kW)
八、最新应用领域突破
1、航空发动机高温部件
低压涡轮叶片涂层:
TiAlN涂层耐温达900℃,替代传统Ni基合金减重30%
GE9X发动机已实现2000小时以上无维护运行
燃烧室隔热屏:
等离子喷涂TiAl合金(孔隙率<2%),热障性能提升50%
罗罗UltraFan发动机验证通过FAA认证
2、半导体先进制程
高介电薄膜沉积:
TiAl靶材用于HfO2/TiAlO叠层(介电常数k=28)
台积电3nm制程中栅极漏电流降低至10^-7A/cm²
铜互连阻挡层:
TiAl/TiN复合结构(厚度≤2nm),电迁移寿命延长3倍
3、新能源与储能
固态电池集流体:
磁控溅射TiAl薄膜(厚度50nm)抑制锂枝晶,循环寿命>2000次
宁德时代2024年发布相关专利(CN114XXXXXX)
氢能储运容器:
TiAl内衬复合材料储氢罐(工作压力70MPa),重量较钢罐减轻40%
4、生物医疗植入物
骨科器械表面改性:
TiAl-O薄膜(硬度25GPa)摩擦系数<0.1,抗菌率>99.9%
强生公司2023年获批FDA的膝关节假体采用该技术
心血管支架:
离子镀TiAl-C涂层(弹性模量5GPa),药物缓释周期精确至60±3天
九、前沿研究方向
1、增材制造靶材:
激光选区熔化(SLM)制备梯度TiAl靶,成分波动<1%
德国Fraunhofer研究所已实现Φ200mm靶材打印
2、极端环境应用:
核聚变装置第一壁涂层(耐中子辐照>10^21n/cm²)
中国CFETR项目完成原型件测试
3、智能化制造:
机器学习优化烧结工艺(能耗降低20%)
数字孪生系统实时监控靶材微观结构演变
4、产业化现状与挑战
全球市场:2023年市场规模12亿美元,CAGR 11%(2023-2030)
技术瓶颈:
大尺寸靶材(>Φ500mm)成品率仅60%
高Al含量靶材(Al>55%)易脆裂问题未完全解决
5、国产化进展:
有研新材实现Φ400mm靶材量产(纯度4N5)
西部超导开发出低成本氢化脱氢(HDH)钛铝粉体
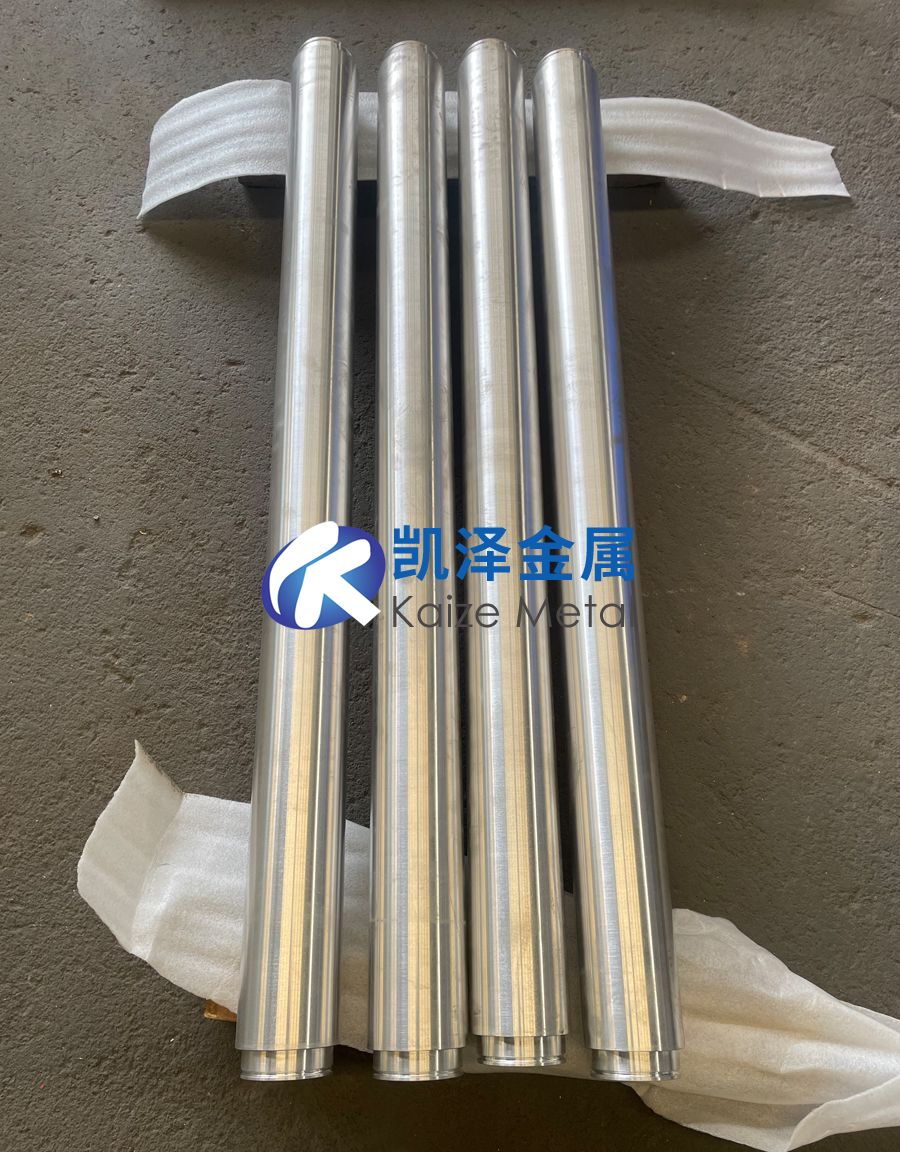
钛铝靶凭借高温强度、轻量化、耐蚀耐磨、多功能兼容性等核心特性,成为连接材料科学与高端制造的关键介质。其性能可通过成分设计(如添加Nb、Cr、Si等元素)和先进工艺(如增材制造、纳米改性)进一步优化,未来在超高温涂层、微型化电子器件、仿生医疗等领域具有广阔应用潜力。钛铝靶材正从传统航空领域向半导体、新能源等高端制造延伸,其轻量化、耐高温、生物相容性等特性在技术迭代中持续释放价值。未来需突破大尺寸制备、成分精确控制等关键技术,以满足泛半导体和第四代核能系统的严苛需求。
相关链接