前言
钛合金紧固件具有密度小、比强度高、抗腐蚀性好等优点,成为航空、航天领域的重要连接元件,获得
迅速发展[1-2]。然而,钛合金紧固件的摩擦因数较大且耐磨性能差,在装配和拆卸过程中,螺栓和螺母易
发生黏着,甚至造成紧固件“咬死”,严重影响了航天型号的可靠性,阻碍了钛合金紧固件在航空航天领域
的进一步应用[2-5]。因此,研究如何改善钛合金表面摩擦学性能、降低摩擦因数、提高其耐磨性成为航空
、航天紧固件的重要研究课题之一。
目前,通过表面工程技术在钛合金表面制备高硬度且抗磨损的涂层是改善其摩擦学性能的有效途径之一
[6-7]。常用的钛合金表面涂层制备技术包括表面氧化[8-9]、气相沉积[10-12]、高能喷涂[13-14]、激光熔
覆[15-16]等。脉冲阳极氧化可在钛合金表面形成致密的氧化膜,提高钛合金表面硬度和耐磨性,且工艺简
单成本低廉,因此成为一种应用广泛的钛合金表面涂层制备技术[17-20]。此外,脉冲阳极氧化可与其他工
艺进行复合,形成复合氧化涂层,可在提高钛合金硬度的同时降低其摩擦因数或提高其耐腐蚀性能。WU等
[17]使用阳极氧化法在钛合金表面制备了包含聚四氟乙烯(PTFE)纳米颗粒的复合阳极氧化膜,摩擦试验结
果表明,氧化膜和PTFE的协同作用提高了涂层整体的抗磨减摩性能。
ALIOFKHAZRAEI等[20]通过阳极氧化法制备了包含氮化硅(Si3N4)和氧化铝(
Al2O3)纳米颗粒的复合氧化膜,提高了钛合金整体的耐磨性。
二硫化钼(MoS2)作为一种常见二维层状材料,其较低的界面剪切强度使其具有优越的减
摩效果,被广泛用于固体润滑材料[21-25]。在钛合金紧固件表面涂敷MoS2,有望降低其表面摩
擦因数,减少黏着和咬死情况的发生。MU等[24]使用一步等离子电解氧化法在钛合金表面制备了含
MoS2的复合氧化涂层。摩擦测试表明,含MoS2的复合氧化涂层摩擦因数和磨损率均
低于不含MoS2的氧化涂层。
钛合金紧固件连接铝合金航空结构时,为了避免二者之间产生电偶腐蚀,常需要对钛合金紧固件进行镀
铝处理[26]。所镀铝涂层不仅能够阻隔紧固件基体与腐蚀介质相接触,而且可通过牺牲自身对周围构件起到
阳极保护作用,因此在钛合金紧固件中的应用日趋广泛。
综上,阳极氧化、涂MoS2以及涂铝技术对于改善钛合金紧固件表面耐磨性、润滑性和耐蚀
性具有良好效果,但这些技术的综合应用效果尚需进一步研究。本文以TC4钛合金为基体,分别对表面未处理(LT)、表面脉冲阳极氧化处理(PA)、表面脉冲阳极氧化和涂铝复合处理(PA-Al)、表面脉冲阳极氧
化和涂MoS2复合处理(PA-MoS2)四种表面状态样品进行了摩擦学性能综合分析,
对其摩擦因数、磨损率、磨损形貌进行测试,探究不同表面状态下钛合金摩擦副的摩擦特性和磨损机理。
1、试验准备
1.1试验材料
试验选用尺寸为φ12mm×5mm的TC4钛合金为试样,选用直径10mm的TC4钛合金小球为对磨副,所用TC4钛合金的化学成分如表1所示。
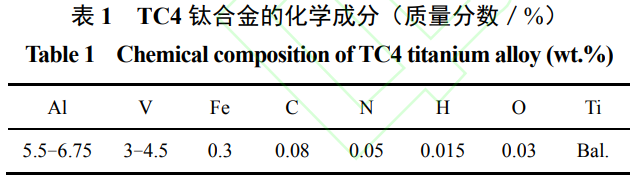
1.2表面涂层制备
首先对试样进行表面脉冲阳极氧化处理,以TC4钛合金试样为阳极,铅板为阴极。脉冲阳极氧化的溶液
组成为硫酸-磷酸混酸溶液,试验温度为0~10℃,试验时间为20min。试验主要工艺包括:化学除油、水洗
、阳极氧化、水洗干燥、检验等。采用手工喷涂的方法,分别对脉冲阳极氧化处理后的样品进行涂铝和涂
MoS2处理,得到脉冲阳极氧化-涂铝和脉冲阳极氧化-涂MoS2复合处理的试样。
1.3试验参数确定
采用摩擦磨损试验机(UMT-3)测试不同表面状态钛合金样品的摩擦学性能,上试样选用直径10mm的TC4
钛合金球,下试样分别为表面未处理(LT)、脉冲阳极氧化处理(PA)、脉冲阳极氧化和涂铝复合处理
(PA-Al)、脉冲阳极氧化和涂MoS2复合处理(PA-MoS2)四种表面状态的钛合金试
样。
分别选取1和4N作为测试载荷,依据赫兹接触公式计算球-盘间的赫兹接触应力,经计算载荷1和4N下的
赫兹接触应力分别为310和493MPa。试验模式为旋转模式,旋转半径为3mm,旋转速度为20r/min(线速度
6.28mm/s),测试时间20min。
1.4磨损形貌分析表征
试样表面磨痕和磨球表面磨斑的磨损形貌使用超景深显微镜(VHX-6000,日本)、三维白光干涉形貌仪
(Nexview,美国)以及聚焦离子束扫描电镜(LYRA3,捷克)进行表征;依据三维白光干涉形貌仪表征涂层表
面粗糙度,依据磨损形貌结果并计算样品的磨损体积及磨损率。使用扫描电镜配套的EDS能谱仪分析样品磨
损区域的元素组成。综合分析各种测试结果,探究不同表面状态试样的减摩耐磨机理。
2、结果及分析
2.1摩擦因数
试样表面脉冲阳极氧化处理后的镀层厚度在5~6.5μm范围内。图1为使用三维白光干涉形貌仪
(Nexview,美国)测量的四组试样的表面三维形貌,对每个样品分别取150µm×300µm区域测试其表面粗糙度
Sa。结果表明,未经过表面处理的钛合金试样表面平整,表面粗糙度约为0.2695µm,经脉冲阳极氧化后,表
面出现较多岛状凸起,表面粗糙度有所增加,约为0.5635µm。试样经过表面涂铝或涂MoS2后,
表面的凸起进一步增大,脉冲阳极氧化和涂铝复合处理样品的表面粗糙度约为0.6933µm,脉冲阳极氧化和涂
MoS2复合处理样品的表面粗糙度约为0.9515µm。
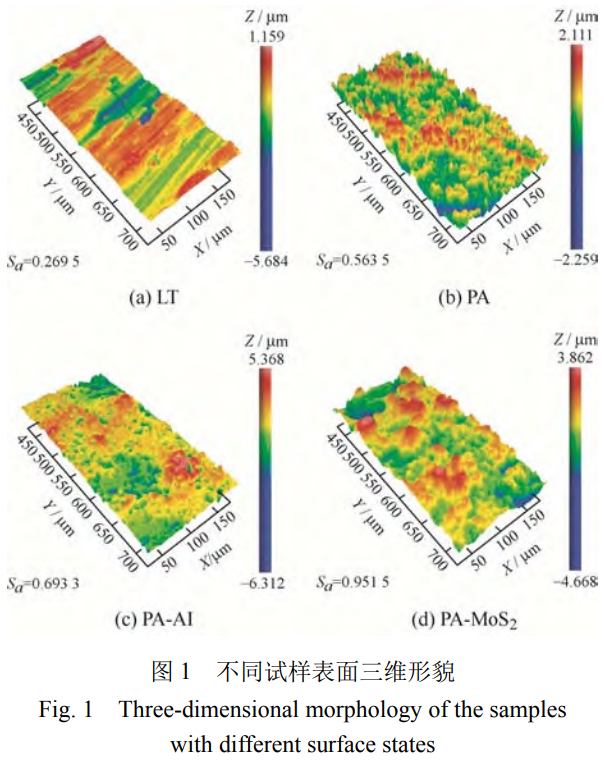
图2所示为不同表面状态试样在1和4N载荷下的摩擦因数变化曲线。经过跑合期后,样品的摩擦因数逐渐
趋于稳定,图3所示为摩擦因数趋于稳定后的平均摩擦因数。从图中可以看出,在1N载荷下,未经过表面处
理(LT)样品的平均摩擦因数约为0.53,且波动剧烈,这主要由于经过短暂的跑合后,钛合金和钛合金直接
接触,容易发生黏着磨损[27-28];经过脉冲阳极氧化处理(PA)样品的摩擦因数最低,约为0.16,且样品
跑合期短,摩擦因数波动小,这表明经过脉冲阳极氧化所形成的涂层具有一定的润滑效果,同时可以有效减
少与钛合金球发生黏着;经过脉冲阳极氧化和涂铝复合处理(PA-Al)样品的摩擦因数最高,约为0.58,且跑合期最长,摩擦因数整体波动较小,这表明表面涂铝后样品的润滑性能不佳,摩擦过程中虽不易发生黏着
,但也较难形成有效的固体润滑膜,整体摩擦因数较高。
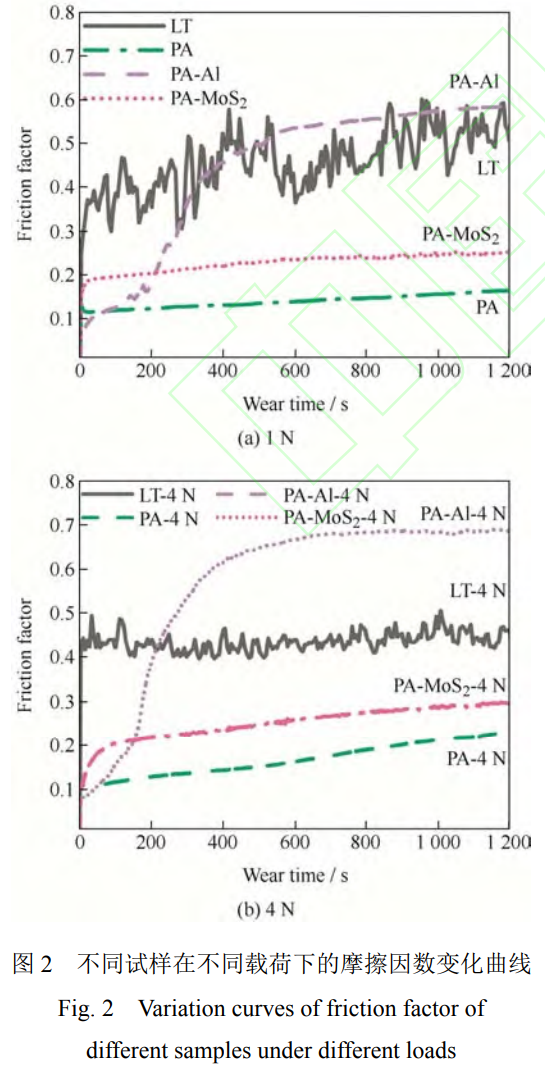
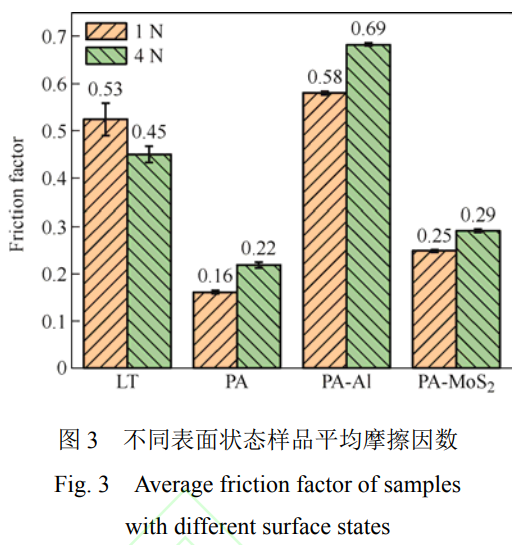
经过脉冲阳极氧化和涂MoS2复合处理(PA-MoS2)样品的摩擦因数较低,约为
0.25,摩擦因数整体波动小,跑合期短,表明样品表面可以在较短时间内形成有效的固体润滑膜,这主要归
功于MoS2优异的固体润滑性能,但由于与脉冲阳极氧化复合处理后样品的表面粗糙度较高,样
品的摩擦因数要高于单独进行脉冲阳极氧化的样品。在4N载荷作用下,不同表面状态样品的摩擦变化趋势基
本一致,即PA样品的摩擦因数最低且平稳,LT样品摩擦因数较高且波动剧烈,PA-Al样品摩擦因数最高且跑
合期长。对比不同样品在低载(1N)和高载(4N)下的摩擦因数,结果表明经过表面处理后样品在高载下的
摩擦因数均高于低载下的摩擦因数。由摩擦因数的测试结果可以得出,从减摩角度考虑,PA和PA-
MoS2两种表面处理技术对钛合金样品均有明显的减摩效果,其中以PA处理后样品的减摩效果最佳。
2.2磨痕宏观形貌及磨损率
图4为不同试样(LT、PA、PA-Al、PA-MoS2)在1N载荷下的磨痕和磨球磨斑形貌照片。从图
中可以看出,LT样品磨痕最宽、磨痕最深,同时磨球的磨斑也最大,磨损明显;PA样品磨痕较浅且最窄,同
时磨球的磨斑也最小;PA-Al样品磨痕为不连续黑色磨痕,磨球磨斑较大;PA-MoS2样品磨痕宽
度与PA-Al样品相近,磨痕连续,磨球磨斑较小。
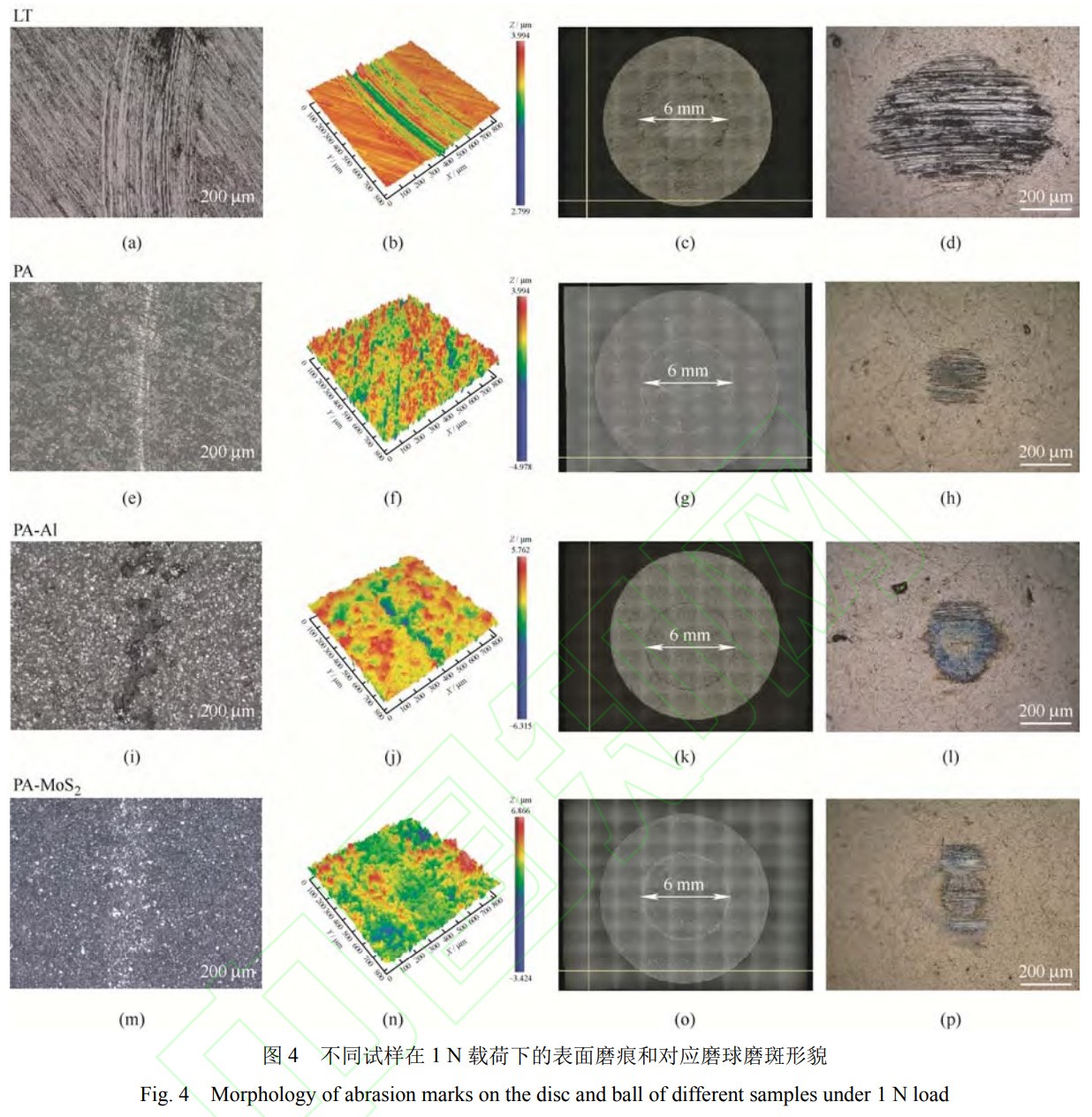
图5为不同试样(LT、PA、PA-Al、PA-MoS2)在4N载荷下的磨痕和磨球磨斑形貌照片。由于
载荷变大,因此磨损也有所加剧,各个样品的磨痕均宽于1N载荷下的磨痕[29],LT样品表面有着明显的犁沟
和黏着物,磨痕最宽,磨斑直径大于600μm;PA样品磨痕依然是最浅且最窄的,同时磨球的磨斑也最小,减
磨效果明显;PA-Al样品磨损剧烈,磨痕较深,相比于低载荷(1N)情况,黑色点状磨痕已连成整体,并且
在两边堆积较多磨屑,表明样品表面较难形成有效的固体润滑膜,这与摩擦因数曲线所得结果一致;PA-
MoS2样品磨损均匀,磨痕宽度较窄但磨痕较深,有减磨效果,但因质地较软导致磨损明显。
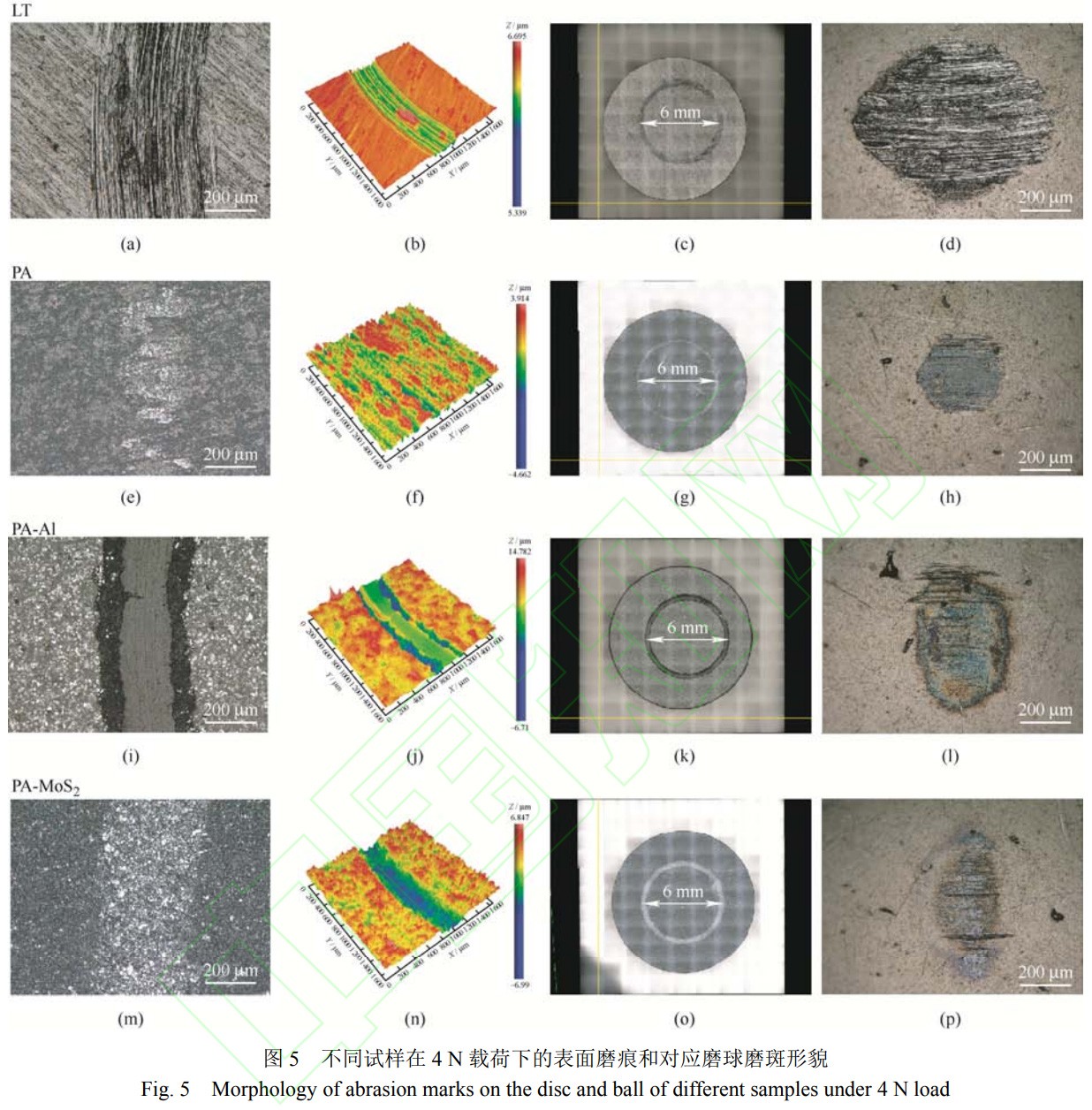
采用三维白光干涉形貌仪测试样品磨痕截面面积,每个磨痕取6个位置,计算截面面积平均值,并计算
样品的磨损体积和磨损率,结果如图6所示。在低载荷下(1N)PA样品的磨损率最低,约为
5.8×10−4mm3(N·m),这与该样品低的摩擦因数和短的跑合期结果相一致,表明
脉冲阳极氧化有较好的减磨效果;PA-Al样品的磨损体积与磨损率最大,甚至高于LT样品的磨损率,这是由
于脉冲阳极氧化和涂铝复合处理样品后,样品表面难以形成有效的固体润滑膜,因此样品磨损过程中跑合期
长且摩擦因数高;脉冲阳极氧化和涂MoS2复合处理后的样品磨损率与LT样品的磨损率相近,这
表明尽管涂覆MoS2后可用形成良好的润滑膜,使摩擦因数降低,但表面粗糙度增大且
MoS2硬度较低,易发生材料转移,因此磨损率比只进行脉冲阳极氧化的样品高。在高载荷下
(4N)PA样品的磨损率最低,约为5.7×10−4mm3(N·m),与低载荷下测得的磨损
率相近,其余三组样品的磨损率均高于其对应低载荷下的磨损率,其中PA-MoS2样品磨损率增加
幅度最大,约为35.2×10−4mm3(N·m),主要归因于所涂MoS2质地较
软且表面粗糙度高,虽可以形成润滑膜降低摩擦因数,但在高载荷下更容易被磨除。
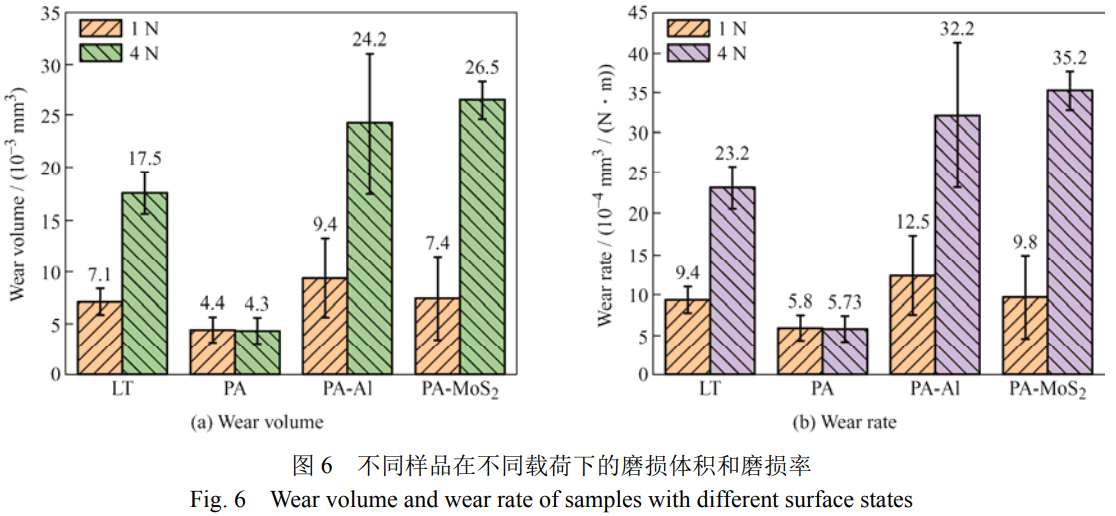
2.3磨痕微观形貌及磨损机理分析
通过SEM和配套的能谱仪对不同表面状态样品磨痕的微观形貌和元素组成进行分析表征,结果如图7所示
。对于LT样品,表面磨痕最宽,磨痕区域内沿着滑动方向分布犁沟,部分犁沟上有突起的黏着物,在更高倍
数的照片中可以看到,黏着物上有沿着滑动方向生成的撕裂裂纹,这表明LT样品摩擦过程中材料的主要去除
过程是表面塑性变形,然后形成犁沟,部分接触表面在压力下会形成黏着区并在后续的滑动中断裂,形成小
凸起。EDS结果表明,黏着区域的元素组成主要以Ti元素为主,并存在Al、V、O和C元素。
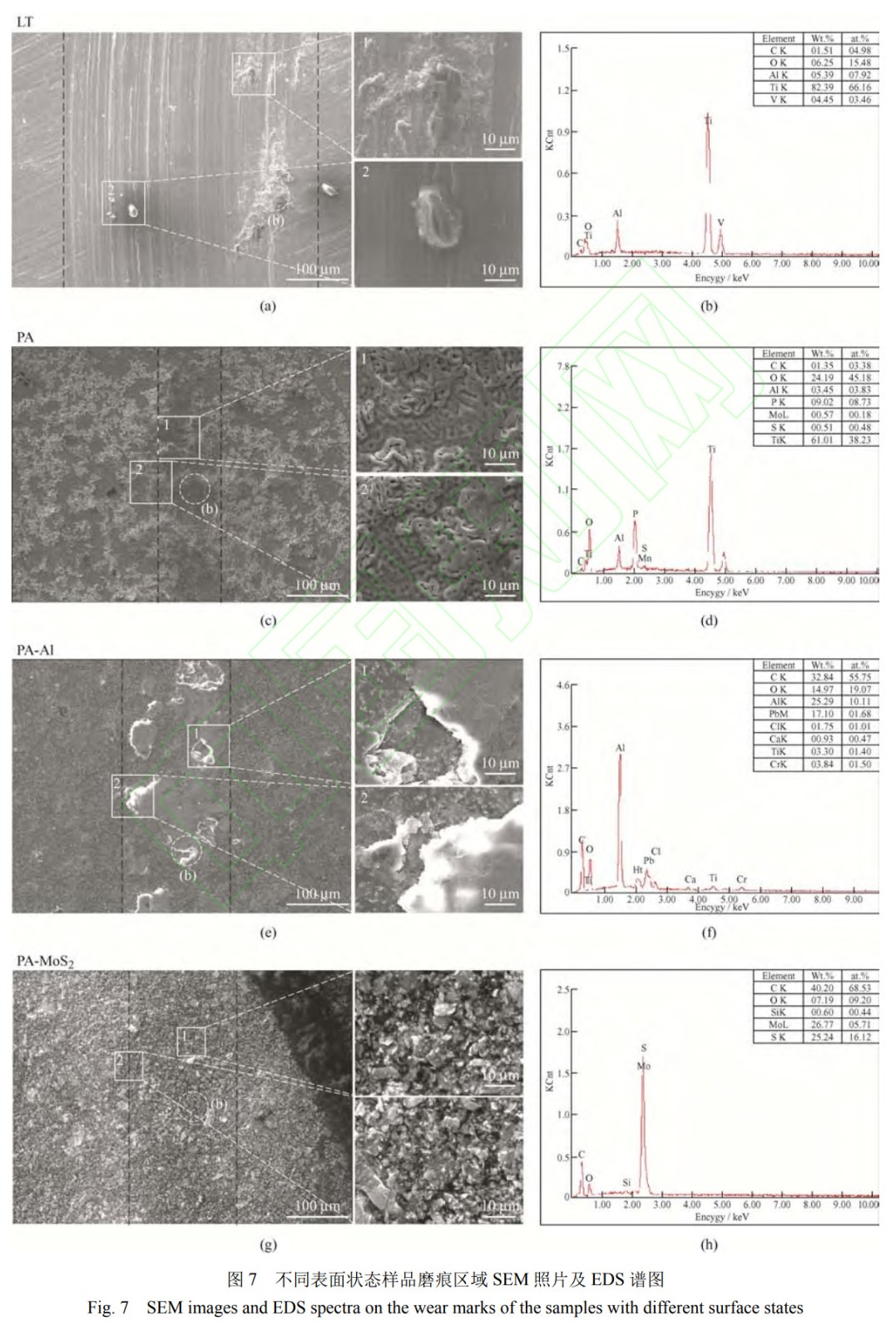
对于PA样品,表面形成的磨痕宽度最窄,深度较浅,表面未形成明显犁沟。高倍放大图显示,经过脉冲
阳极氧化后,元素表面形成了较为致密的氧化膜,组成元素以Ti和O为主,同时存在少量的Al、C、P、Mo元
素等。结果表明,通过脉冲阳极氧化在TC4表面形成较为致密的氧化膜,表面硬度增加,在摩擦过程中不易
由于挤压塑性变形而形成犁沟,同时所形成钛的氧化物具有一定的润滑作用,在材料表面形成了固体润滑膜
,不仅使材料具有低的摩擦因数,降低了磨损率,同时可以阻隔钛合金直接接触,减少黏着的发生。
对于PA-Al样品,表面形成的磨痕宽度居中,表面未形成犁沟,但有大块的剥落孔洞和块状物,局部放
大图可以看到剥落处为脆性断裂,表明在脉冲阳极氧化表面进行涂铝工艺后,表面有脆性相生成。EDS结果
表明,样品表面存在较多的Al和O元素,故推测有Al2O3陶瓷相生成,导致表面易发生脆性剥落。在摩擦过程
中,样品表面由于硬度增加,不易生成犁沟,但表面脆性较高易生成裂纹,裂纹扩展最终生成剥落坑,因此
样品表面较难形成有效的固体润滑膜,跑合期长且摩擦因数高,最终样品的磨损率较高。
对于PA-MoS2样品,表面形成的磨痕宽度比LT窄但高于PA样品。磨痕形貌较平整,未形成明
显的犁沟,同时与PA-Al样品不同,磨痕中未出现剥落坑,放大图能看出表面由许多不规则的块状物组成。
EDS结果表明,磨痕中主要元素以S和Mo为主,同时检测到少量的C、O和Si元素。
综合以上分析,总结了不同表面状态TC4钛合金与TC4摩擦时的磨损机理,如图8所示。未经过表面处理
(LT)的钛合金样品由于表面硬度低且易与同种材料的TC4发生黏着,因此磨损较为剧烈,摩擦因数的宽幅
上下波动和磨痕中的凸起黏着转移物均表明在摩擦过程中,对磨副表面发生了严重的黏着,其磨损机理如图
8a所示。在轴向压力和摩擦热作用下,TC4球和TC4盘之间发生塑性变形,随后发生黏着,因此在这种表面状
态下,主要磨损机理为犁削和黏着磨损;样品表面经过脉冲阳极氧化处理(PA)后,表面生成较为致密的
TiO2涂层,硬度提高,减摩性好,同时与基体具有较高的结合强度,因此大幅提高材料的耐磨性能[30],磨
损率和摩擦因数最低。同时,由于表面氧化膜的存在,样品表面不易产生塑性变形,也不易和TC4球之间形
成扩散,因此不易发生黏着,如图8b所示;经过脉冲阳极氧化和涂铝复合处理(PA-Al)后,样品表面会部
分生成Al2O3,Al2O3具有更高硬度,但韧性较差,摩擦过
程中容易发生脆裂,最终导致表面形成剥落坑[31],因此样品的跑合期长且摩擦因数高,而剥落的硬质磨屑
又会加剧样品的磨损,造成样品较高的磨损率,磨损机理主要表现为剥落和磨粒磨损,其机理如图8c所示;
经过脉冲阳极氧化和涂覆MoS2复合处理(PA-MoS2)后样品表面存在较多的
MoS2,在摩擦过程中,经过跑合期后会在表面生成润滑膜,因此样品表面具有较低的摩擦因数
,但由于MoS2易发生转移,因此样品的磨损率相对较高,其机理如图8d所示。
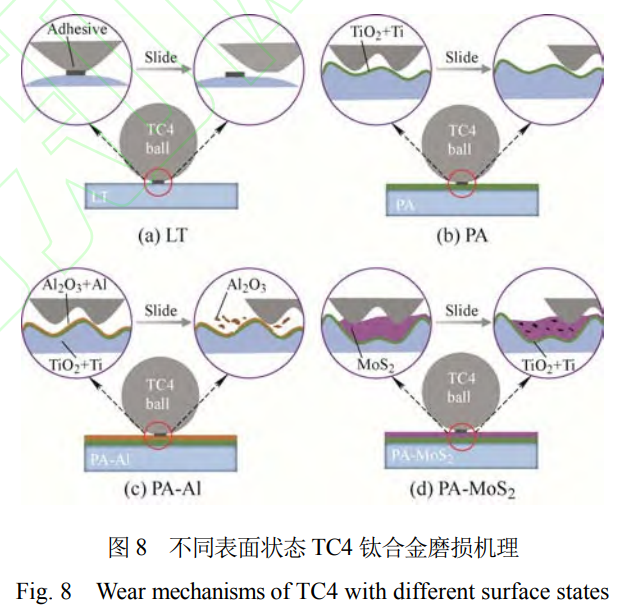
3、结论
TC4样品经过不同表面处理后其摩擦磨损性能差异明显。未经过表面处理的钛合金样品在摩擦磨损过程
中表面易发生黏着磨损,摩擦因数高且不稳定,约为0.53,这也说明未经过表面处理的钛合金紧固件发生“
咬死”现象的主要原因是其易与工件发生黏着。经过脉冲阳极氧化处理(PA)后样品表面会生成TiO2氧化层
,减摩(摩擦因数约为0.16)和耐磨特性(磨损率5.8×10−4mm3(N·m))最佳,
高载下依然稳定(摩擦因数约为0.22、磨损率5.7×10−4mm3(N·m)),且有明显
的抗黏着效果。经过脉冲阳极氧化和涂铝复合处理(PA-Al)的样品并未展现减摩耐磨特性,磨痕表面有大
块的剥落孔洞和块状物,摩擦因数和磨损率较未处理样品均有增高。经过脉冲阳极氧化和涂
MoS2复合处理(PA-MoS2)的样品表面未发现磨粒磨损和黏着磨损,样品表现出一
定的减摩(摩擦因数约为0.25)效果,但耐磨性(磨损率9.8×10−4mm3(N·m))
较差,且在高载下磨损率有较大幅度升高(磨损率35.2×10−4mm3(N·m))。
参考文献
[1] 李蒙,凤伟中,关蕾,等. 航空航天紧固件用钛合金材 料综述[J]. 有色金属材料与工程,2018,
39(4):49-53.
LI Meng, FENG Weizhong, GUAN Lei, et al. Summary of titanium alloy for fastener in
aerospace[J]. Nonferrous Metal Materials and Engineering, 2018, 39(4): 49-53. (in Chinese)
[2] 于建政,宁广西,林忠亮,等. 航空工业钛合金紧固件 失效分析研究进展[J]. 材料导报,2013,
27(z1):256-258,264.
YU Jianzheng, NING Guangxi, LI Zhongliang, et al. Failure analysis progress of titanium
alloy fastener used in aerospace industry[J]. Materials Reports, 2013, 27(z1): 256-258, 264.
(in Chinese)
[3] JHA A K, SINGH S K, KIRANMAYEE M S, et al. Failure analysis of titanium alloy
(Ti6Al4V) fastener used in aerospace application[J]. Engineering Failure Analysis, 2010, 17
(6): 1457-1465.
[4] 李新星,施剑峰,王红侠,等. Ti6Al4V 合金干滑动磨 损过程中摩擦层及摩擦氧化物的作用[J].
表面技术,2019,48(12):233-239.
LI Xinxing, SHI Jianfeng, WANG Hongxia, et al. Role of tribo-layers and tribo-oxides in
dry sliding wear process of Ti6Al4V alloy[J]. Surface Technology, 2019, 48(12): 233-239. (in
Chinese)
[5] 刘雨薇,吴霞,陈纪云,等. 钛合金摩擦磨损性能及减 磨方法研究进展[J / OL]. 表面技术,
2024,53(12):1-21[2024-05-29]. https://kns.cnki.net/kcms2/article/abstract?v=acR2UJ02Y
hTkNLsiQQZEpO5X6yk57ujmpDKWQL94QO79QobyP 2-KKQv7Sfy9LwUlq_uyIcP4_jwCX2G-b2Vsw3HlKbsS_
S1ukFZVjPRMkupDdYumufkV0h3_824NpusUB78uqO0S6qqEf0FFh8YxmE7Ud6pUcJdCerVarMpbj7eLSPVgp
KS6YQaqeMtgHxS&uniplatform=NZKPT&language=C HS. DOI:10.16490/j.cnki.issn.1001-
3660.2024.12.001.
LIU Yuwei, WU Xia, CHEN Jiyun, et al. Research progress on friction and wear properties of
titanium alloys and wear reduction methods[J/OL]. Surface Technology, 2024, 53(12): 1-21[2024
-05-29]. https://kns.cnki.net/ kcms2/article/abstract?v=acR2UJ02YhTkNLsiQQZEpO5
X6yk57ujmpDKWQL94QO79QobyP2-KKQv7Sfy9LwUl q_uyIcP4_jwCX2G-b2Vsw3HlKbsS_S1ukFZVjPRMkup
DdYumufkV0h3_824NpusUB78uqO-0S6qqEf0FFh8Yxm E7Ud6pUcJdCerVarMpbj7eLSPVgpKS6YQaqeMtgHxS
&uniplatform=NZKPT&language=CHS. DOI:10.16490/j. cnki.issn.1001-3660.2024.12.001. (in
Chinese)
[6] 吴彼,高禩洋,薛伟海,等. 钛合金表面 TiB2 涂层与 纯铝的高温黏着磨损行为[J]. 中国表面工
程,2022,35(3):64-72.
WU Bi, GAO Siyang, XU Weihai, et al. High-temperature adhesive wear behavior between TiB2
coating on TC4 substrate and pure Al[J]. China Surface Engineering, 2022, 35(3): 64-72. (in
Chinese)
[7] 付颖,张艳,包星宇,等. 钛合金表面耐磨涂层研究进 展[J]. 中国腐蚀与防护学报,2018,38
(2):117-123.
FU Ying, ZHANG Yan, BAO Xinyu, et al. Research progress on wear-resistant coatings for
Ti-alloy[J]. Journal of Chinese Society for Corrosion and Protection, 2018, 38(2): 117-123.
(in Chinese)
[8] 胡鹏飞. 钛合金紧固件蓝色阳极氧化影响因素分析与 优化[J]. 热加工工艺,2021,50(12):102
-103,108.
HU Pengfei. Influencing factors analysis and optimization of blue anodizing for titanium
alloy fastener[J]. Hot Working Technology, 2021, 50(12): 102-103, 108. (in Chinese)
[9] DIAMANTI M V, SEBASTIANI M, MANGIONE V, et al. Multi-step anodizing on Ti6Al4V
components to improve tribomechanical performances[J]. Surface and Coatings Technology, 2013,
227(25): 19-27.
[10] WILSON J C A, WU S J, GOTMAN I, et al. Duplex coatings with enhanced adhesion to Ti
alloy substrate prepared by powder immersion nitriding and TiN / Ti multilayer deposition[J].
Materials Letters, 2015, 157(15): 45-49.
[11] ASKARI S J. Tribological characteristics of nanocrystalline diamond films grown on
titanium[J]. Surface Engineering, 2009, 25(6): 482-486.
[12] GRABARCZYK J, BATORY D, KACZOROWSKI W, et al. Comparison of different thermo-chemical
treatments methods of Ti-6Al-4V alloy in terms of tribological and corrosion properties[J].
Materials, 2020, 13(22): 5192.
[13] 于坤,祁文军,雷靖峰. 钛合金表面再制造涂层的研究综述[J]. 热加工工艺,2020,49(12):6
-9.
YU Kun, QI Wenjun, LEI Jingfeng. Review of research on remanufacturing coatings on
titanium alloy surface[J]. Hot Working Technology, 2020, 49(12): 6-9. (in Chinese)
[14] ZHAO L, LUGSCHEIDER E. Reactive plasma spraying of TiAl6V4 alloy[J]. Wear, 2002, 253
(11-12): 1214-1218.
[15] 徐倩,刘艳,丁涛. 钛合金表面激光熔覆耐磨涂层材料 的研究进展[J]. 热加工工艺,2023,52
(14):24-29.
XU Qian, LIU Yan, DING Tao. Research progress of laser cladding wear resistant coating
materials on titanium alloy surface[J]. Hot Working Technology, 2023, 52(14): 24-29. (in
Chinese)
[16] 杨立军,文品,石丹玉,等. 钛基表面 CNTs / Ti 激光 熔覆层的摩擦磨损研究[J]. 功能材料,
2021,52(6):6133-6137.
YANG Lijun, WEN Pin, SHI Danyu, et al. Friction and wear of CNTs / Ti laser cladding layer
on titanium substrate[J]. Journal of Functional Materials, 2021, 52(6): 6133-6137. (in
Chinese)
[17] WU L, WEN C, ZHANG G, et al. Influence of anodizing time on morphology, structure and
tribological properties of composite anodic films on titanium alloy[J]. Vacuum, 2017, 140:
176-184.
[18] WU L, LIU J H, WU G L, et al. Growth behaviour of anodic oxide film on titanium
alloy[J]. Surface Engineering, 2015, 31(12): 904-911.
[19] 冯慧峤,张旭,师玉英,等. Ti-6Al-4V 钛合金脉冲阳极 氧化工艺[J]. 电镀与环保,2016,36
(5):40-42.
FENG Huiqiao, ZHANG Xu, SHI Yuying, et al. Pulsed anodizing process of TI-6Al-4V titanium
alloy[J]. Electroplating & Pollution Control, 2016, 36(5): 40-42. (in Chinese)
[20] ALIOFKHAZRAEI M, ROUHAGHDAM A S, SHAHRABI T. Abrasive wear behaviour of Si3N4 /
TiO2nanocomposite coatings fabricated by plasma electrolytic oxidation[J]. Surface Coatings
Technology, 2010, 205: 41-61.
[21] 李锡刚. 钛合金涂敷二硫化钼膜工艺[J]. 电镀与涂饰,2009,28(5):60-62.
LI Xigang. Process of coating MoS2 film on titanium alloys[J]. Electroplating
& Finishing, 2009, 28(5): 60-62. (in Chinese)
[22] 卢金德,韦春贝,林松盛,等. 磁控溅射 NiCrAlY / MoS2复合薄膜结构与性能研究
[J]. 表面技术,2021,50(5):198-207.
LU Jinde, WEI Chunbei, LIN Songsheng, et al. Structure and properties of NiCrAlY /
MoS2 composite films fabricated by magnetron sputtering[J]. Surface Technology,
2021, 50(5): 198-207. (in Chinese)
[23] 徐进,朱旻昊,陈建敏,等. 制备工艺对 MoS2粘结固 体润滑涂层微动磨损寿命的影
响[J]. 摩擦学学报,2003,23(2):95-98.
XU Jin, ZHU Minhao, CHEN Jianmin, et al. The influence of preparation processes on
fretting wear life of MoS2 bonded solid lubricating coating[J]. Tribology, 2003,
23(2): 95-98. (in Chinese)
[24] MU M, LIANG J, ZHOU X, et al. One-step preparation of TiO2 / MoS2 composite coating on Ti6Al4V alloy by plasma electrolytic oxidation and its tribological
properties[J]. Surface and Coatings Technology, 2013, 214: 124-130.
[25] SONG W, AN L, LU Y, et al. Friction behavior of TiN-MoS2 / PTFE composite
coatings in dry sliding against SiC[J]. Ceramics International, 2021, 47(17): 24003-24011.
[26] 徐良. 航空钛合金紧固件铝涂层性能规范研究[J]. 航 空标准化与质量,2012(1):32-36.
XU Liang. The specification of aluminum pigmented coating for aerospace titanium alloy
fasteners[J]. Aeronautic Standardization & Quality, 2012(1): 32-36. (in Chinese)
[27] 应扬,杜宇,李婷,等. 摩擦配副和摩擦参数对 TC29钛合金摩擦磨损性能的影响[J]. 有色金属
材料与工程,2021,42(3):30-34.
YING Yang, DU Yu, LI Ting, et al. Effect of friction pairs and friction parameters on
friction and wear properties of TC29 titanium alloy[J]. Nonferrous Metal Materials and
Engineering, 2021, 42(3): 30-34. (in Chinese)
[28] 李朝志,付彬国,刘金海,等. 钛合金干滑动摩擦行为 与磨损机理研究进展[J]. 材料导报,
2018,32(z1):410-414.
LI Chaozhi, FU Binguo, LIU Jinhai, et al. Research progress of wear behaviors and
mechanism of titanium alloys under dry sliding condition[J]. Materials Reports, 2018, 32(z1):
410-414. (in Chinese)
[29] 董思成,钟利,但敏,等. 不同载荷及转速条件下 MoS2涂层的摩擦磨损性能研究
[J]. 核聚变与等离子体物理,2023,43(1):99-104.
DONG Sicheng, ZHONG Li, DAN Min, et al. Study on the frictional wear performance of
MoS2 coatings under different load and speed conditions[J]. Nuclear Fusion and
Plasma Physics, 2023, 43(1): 99-104. (in Chinese)
[30] LI W, KONG D. Effects of TiO2 mass fraction on friction reduction and wear resistance
of laser-cladded CrNi alloy coating[J]. Journal of Materials Engineering and Performance,
2021, 30(3): 2280-2290.
[31] 宋洪源,乌日开西·艾依提,尹瀛月. 等离子喷涂 Al2O3涂层质量的研究现状[J]. 热加工工艺,
2017,46(12): 44-47.
SONG Hongyuan, WURIKAIXI Aiyiti, YIN Yingyue. Research status of quality of plasma sprayed
Al2O3 coating[J]. Hot Working Technology, 2017, 46(12): 44-47. (in Chinese)
作者简介:任小勇,男,1992 年出生,工学博士,副教授,硕士研究生导师。主要研究方向为机械装
备耐磨防护。 E-mail: xiaoyong_ren@sina.cn
程洁(通信作者),女,1990 年出生,工学博士,教授,博士研究生导师。主要研究方向为电子制造
摩擦学。 E-mail: jiecheng@cumtb.edu.cn
相关链接