航空制造产业是高度综合的战略性高新技术产业,是国家工业实力的重要体现之一。为了满足航空发动机设计和制造过程中高可靠性和大推重比的要求,航空发动机的结构设计已经向整体化方向发展,尤其是整体叶盘、叶环等已形成发展趋势。整体叶盘是将发动机转子的叶片和叶盘设计成一体,放弃使用传统的榫头和榫槽装置进行连接,从而减少零件数量和减轻发动机质量,显著提高发动机工作效率、工作寿命以及安全可靠性[1-2]。
整体叶盘需要在高温、高压、高负荷的复杂环境中服役[3],这决定了其对于制造材料的选择具有很高的要求,亟需耐高温、抗氧化和阻燃等优良性能的材料。钛合金具有密度低、比强度高、耐腐蚀性能好等优点,可在室温和中高温环境中服役,目前被广泛地应用于航空发动机整体叶盘的研发和制造领域[4-6]。
航空发动机工作时,整体叶盘各部位所承受的温度和应力区别较大。为了实现整体叶盘不同部位力学性能的最优配置,钛合金整体叶盘的“双性能”设计思路被提出,即通过锻造、焊接等方法使叶片和叶盘部位获得不同且特定的显微组织[7-9]。
叶片处需要承受高温流动气体和高频振动应力,且有受到外物损伤的可能性,因此要求叶片具有高强度和塑性、高周疲劳性能以及抗外物冲击能力,一般采用强度高和塑性好的双态组织材料[10-12];而叶盘处工作温度较低,需要承受多轴低频循环应力作用,因此要求叶盘具有高抗蠕变能力、低周疲劳性能和断裂韧性,一般采用强度高和断裂韧性好的网
篮组织材料[13-14]。
双性能整体叶盘常见的设计思路是使用两种合金,通过线性摩擦焊技术[15-16]将叶片焊接到盘体上来获得不同的组织,从而实现双性能的需求。
另外,也可以通过锻造和热处理等方法来控制单种合金获得不同组织。单种合金所产生的双性能往往会受到合金本身性能的限制,无法充分发挥双性能整体叶盘的结构优势[17],因此“双合金-双组织”型整体叶盘具有很好的发展和应用前景。目前,国内外的相关研究常采用具有双态组织的Ti-6Al-4V(TC4)合金作为叶片材料,叶盘材料则选择具有网篮组织的Ti-5Al-4Mo-4Cr-2Sn-2Zr(TC17)合金。TC17钛合金是一种综合性能良好的近β型钛合金,具有强度高、断裂韧性好和锻造温度范围宽等优点。TC17钛合金中的Mo和Cr元素为β相稳定元素[18],使合金既可以在β相区变形,也可以在α+β两相区变形,从而通过不同的热处理制度和锻造工艺来调控合金的力学性能。经过β锻造后的TC17钛合金获得细长板条状α相交错排列的网篮组织,具有高强度、高断裂韧性以及良好的疲劳性能和蠕变性能,被广泛用于航空发动机高性能整体叶盘、鼓筒等大型关键零部件的制造[19-20]。
TC4钛合金是一种α+β型钛合金,具有高比强度、耐腐蚀性能以及优良的高温力学性能[21]。TC4钛合金在α+β区锻造后经热处理可以获得双态组织,具有高的强度和塑性,常常被用于航空发动机叶片等关键零部件的制造。
国内外对于网篮组织TC17和双态组织TC4钛合金的力学性能进行了大量的研究,诸如强塑性、高/低周疲劳性能以及断裂韧性等。尤其是在准静态条件下的拉伸性能,是钛合金实际应用的重要数据支撑。王丹等[22]研究了两相区变形量对TC17钛合金的显微组织和拉伸性能的影响,发现两相区变形加速了网篮组织中板条状α相的球化过程,且拉伸强度和塑性与变形程度呈线性关系,均随变形量的增加而增大。王博涵等[23]在不同锻造温度和后续热处理作用下,对TC4钛合金分别进行α+β锻造、近β锻造和β锻造,得到了三种不同显微组织。其中等轴组织的强度低但塑性好,片层组织的强度最高但塑性较差,而双态组织有较高的强度和塑性,综合力学性能优良。
整体叶盘在服役过程中往往需要承受复杂的准静态载荷的作用,而目前有关应变速率对整体叶盘用钛合金锻件拉伸性能影响的研究,尤其是不同应变速率条件下大尺寸实验件的拉伸性能研究则相对较少。本工作旨在研究整体叶盘用TC17和TC4钛合金锻件在不同应变速率下的拉伸性能以及流变应力的应变速率敏感性,分析两种合金在不同应变速率下的变形组织和断口形貌,并进一步探讨微观组织形貌与合金强度和塑性的关系。
1、实验材料及方法
1.1实验材料
实验材料为TC17和TC4钛合金,化学成分如表1所示。通过β锻造和锻后热处理的方法制备具有网篮组织的TC17合金盘状锻件,使合金原始坯料加热到β相区后进行锻造,并在α+β相区完成终锻,锻造后在一定温度下保温并空冷处理。同样通过锻造以及后续热处理的方法制备具有双态组织的TC4合金块状锻件,使合金原始坯料加热到α+β相区进行锻造,锻造后在一定温度下保温并空冷处理。
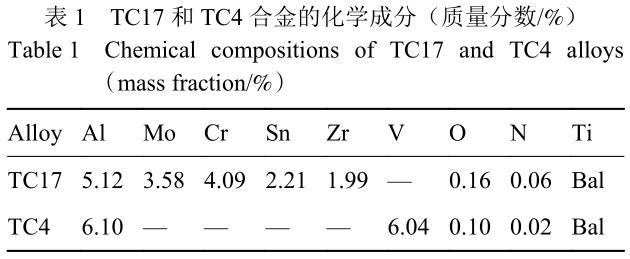
1.2原始组织表征
通过线切割的方式分别从两种合金原始锻件上取下10mm×10mm×8mm的块状试样并进行热镶嵌。利用240号和320号砂纸打磨掉试样的氧化皮后,依次用9μm和3μm粒径的金刚石抛光液以及SiO2和双氧水混合抛光液抛光,随后在去离子水∶HNO3∶HF=100∶3∶2(体积比)混合液中进行腐蚀。TC17和TC4合金样品的腐蚀时间分别为
13s和20s。采用LEICADMI8型金相显微镜(OM)观察合金原始组织。同样将试样磨抛成镜面后,在小压力下用SiO2和双氧水的混合抛光液进行30min的机械化学抛光来去除试样表面的残余应力,随后在去离子水下抛光10min。利用IT800-SHL型高分辨场发射扫描电镜(SEM)配备的电子背散射衍射(EBSD)技术对抛光后试样的微观组织进行表征,加速电压为20kV。
1.3力学性能测试
采用HVD-5IS型维氏硬度计测定两种合金的维氏硬度,测试位置各10个,所用的载荷为49N,加载时间为15s。通过线切割的方式从原始锻件上沿垂直于锻造方向切取拉伸试样,试样总长度为198.4mm,平行段长度为98.4mm,标距长度为75mm,平行段宽度为12.5mm,厚度为1mm,具体尺寸如图1所示。拉伸实验在UTM4204X型万能
实验机上进行,采用的应变速率为1×10−5、1×10−4、1×10−3s−1和1×10−2s−1,每种应变速率下进行3次实验,采用标距为25mm的引伸计,拉伸方向垂直于合金锻造方向。
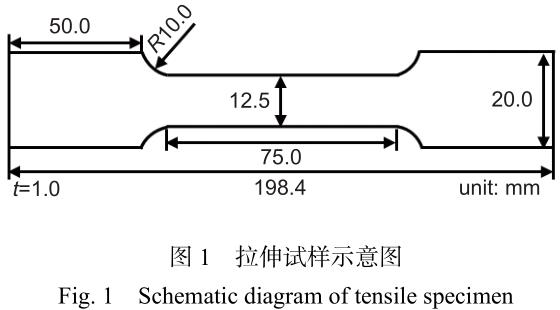
1.4变形组织和断口形貌表征
通过线切割的方式从拉伸试样断口附近切下长度为5mm的试样,对样品进行磨抛和腐蚀,采用OM观察断口附近变形组织,并结合EBSD技术对其进行研究和分析。另外从拉伸试样另一侧断口附近切下长度为5mm的试样,采用SEM对试样进行断口形貌观察。
2、结果与讨论
2.1合金的原始组织
图2(a)、(b)为TC17合金原始组织的OM图。TC17合金经过β锻造和热处理后得到网篮组织,低倍下由尺寸较大的β晶粒(图2(a))以及晶界处连续分布的α相组成,高倍下在β晶粒中观察到大量纵横交错的板条状α相(图2(b))。对合金的原始试样进行EBSD观察(扫描步长为0.1μm),结果如图2(c)~(e)所示,其中(c)、(d)、(e)分别为反极图、相图以及Kernel平均取向差(KAM)图。如图2(c)所示,β晶粒中的板条状α相具有不同的取向,纵横交错分布形成网篮结构。在板条状α相交错分布的空隙处还分布着大量的残余β相,如图2(d)所示。KAM图可用于反映不同位置的几何必须位错密度、晶格畸变以及残留应变等信息[24],图中不同颜色代表着不同的KAM值,红色代表高KAM值,蓝色代表低KAM值。从图2(e)中可以看出,合金的原始组织经过β锻造和热处理后还残留了一定程度的应变,其中板条状α相的KAM值较低,而残余β相的KAM值较高,即存在较大的残留应变。
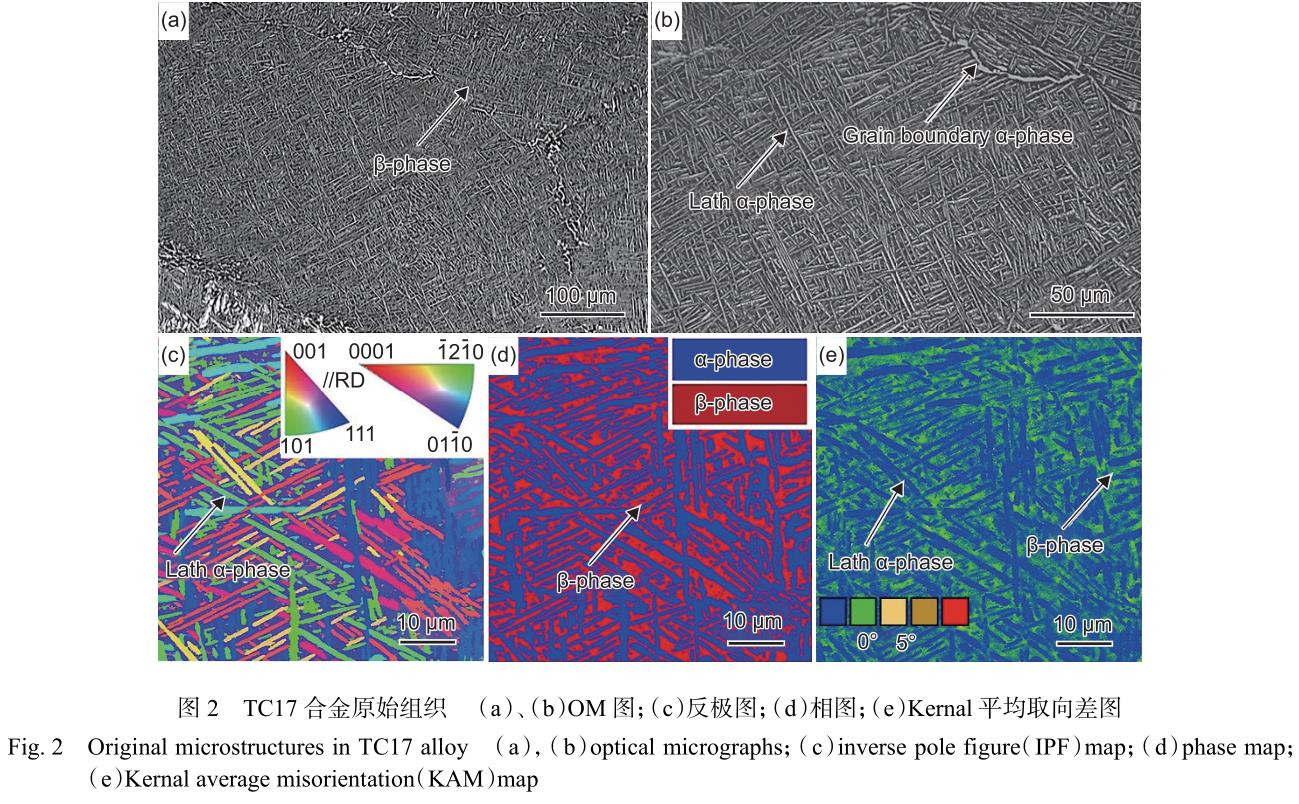
图3(a)、(b)为TC4合金原始组织的OM图。TC4合金经过锻造以及后续热处理获得双态组织,低倍下由等轴状的初生α相和β转变组织(图3(a)箭头所示)组成,高倍下在β转变组织中观察到大量片层状的次生α相(图3(b))。图3(c)~(h)为合金原始组织的EBSD反极图、相图以及KAM图(扫描步长为0.1μm)。初生α相和次生α相均较为清晰(图3(c)),而β转变组织中的残余β相在相图中的含量极少且尺寸较小(图3(d)),难以被很好地解析标定。如图3(e)所示,初生α相与β转变组织的界面处呈现出较高的KAM值,而β转变组织中KAM值较高处主要分布在次生α相的片层之间。为了对β转变组织中的次生α相和残余β相做进一步的分析,对图3(c)中方框区域进行扫描步长为0.01μm的EBSD观察,如图3(f)~(h)所示。与网篮组织中板条状α相的纵横交错排列不同,β转变组织中次生α相
的排列较为规则,在次生α相的片层之间分布着残余β相(图3(f)和(g))。另外,残余β相的KAM值较高,如图3(h)所示,存在较大的残留应变。

2.2合金的力学性能
从原始组织的硬度测量结果得知,TC17和TC4合金的维氏硬度分别为380HV和320HV,网篮组织的TC17合金比双态组织的TC4合金具有更高的维氏硬度。图4为两种合金在不同应变速率拉伸实验下所得到的工程应力-应变曲线、真应力-应变及加工硬化率曲线。如图4(a-1)、(b-1)所示,合金的屈服强度和抗拉强度均随应变速率增加呈现上升趋势,伸长率则随应变速率增加而下降,表现出应变速率强化效应。从图4(a-2)、(b-2)中可以看出,两种合金的加工硬化率在屈服之后逐渐下降,且随着应变速率的增加,其下降速度逐渐加快,加工硬化效应变差。在相同应变速率下,TC17相较于TC4合金在屈服之后的加工硬化率下降较慢,表现出更好的加工硬化效应。表2列出了
两种合金的屈服强度、抗拉强度和总伸长率,并对其进行了对比分析,如图5(a)、(b)所示。随着应变速率的增加,TC17合金的屈服强度从1036MPa增加到1128MPa,抗拉强度从1123MPa增加到1162MPa,上升幅度对比屈服强度略有降低。
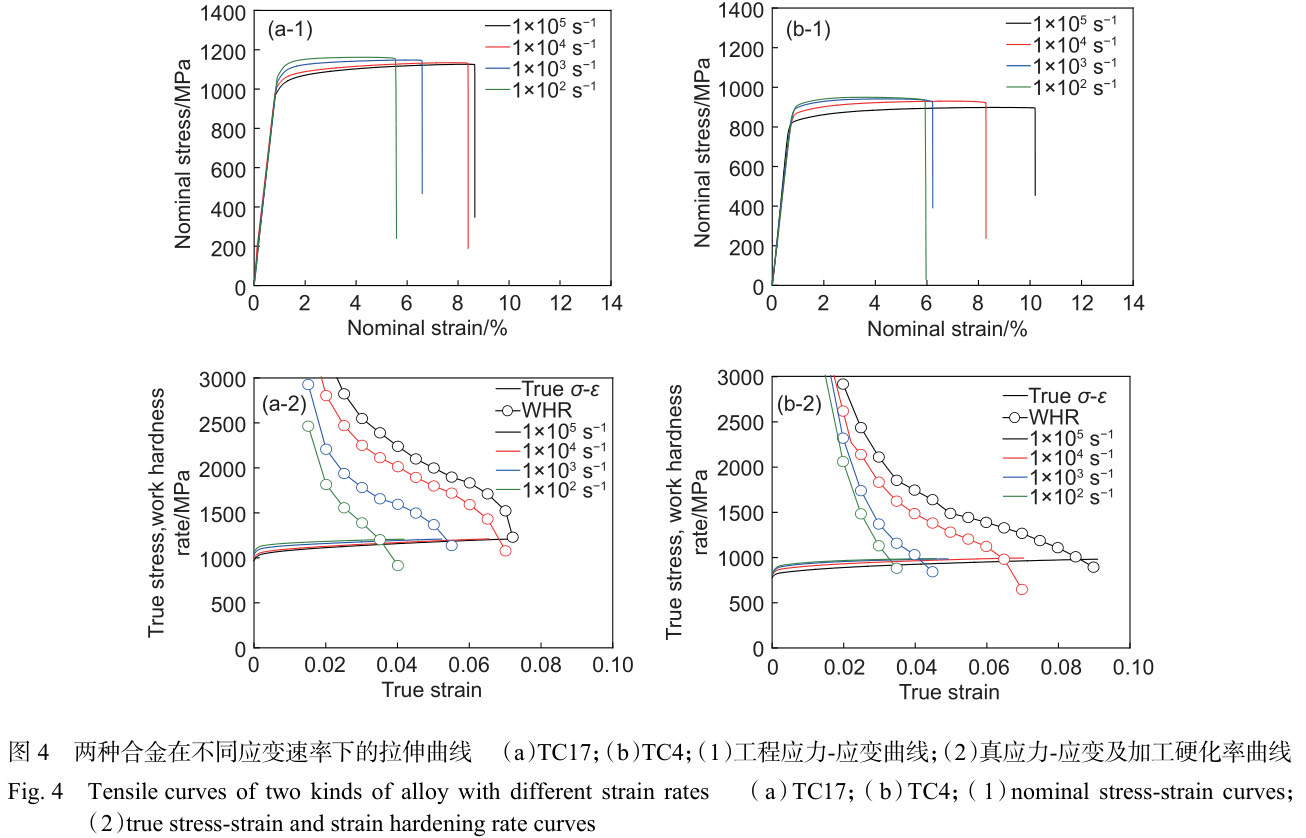
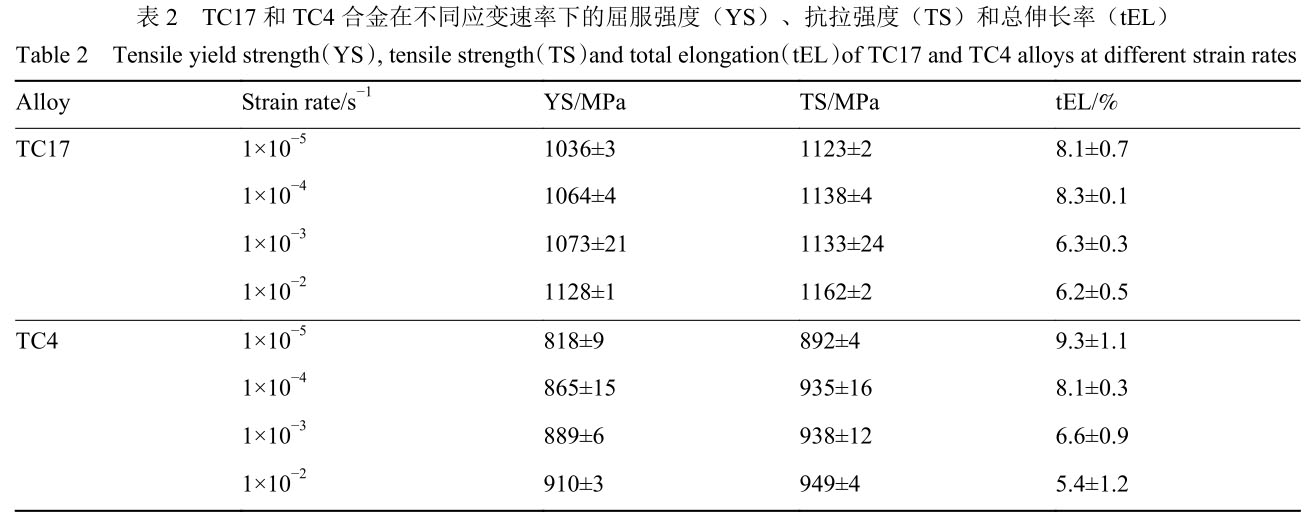
TC4合金的屈服强度从818MPa增加到910MPa,抗拉强度则从892MPa增加到949MPa。在相同的应变速率下,TC17合金的屈服强度和抗拉强度均比TC4合金高约200MPa。随着应变速率的增加,两种合金的总伸长率均呈现下降趋势,如TC17合金的总伸长率从8.1%下降到6.2%,而TC4合金从9.3%下降到5.4%,综合比较发现TC4合金的总伸长率略高于TC17合金,即其塑性较好。
应变速率敏感性系数(m)是反映塑性变形时合金的流变应力对于应变速率的敏感性程度,即反映了应变速率增加时合金的强化倾向,可通过式(1)
计算求得:m=dσ/dln˙ε(1)
˙ε式中:为应变速率;σ为流变应力。
图5为两种合金在不同应变速率下的强度、总伸长率和在不同真应变下的流变应力变化值(Δσ)、应变速率敏感性系数(m)。两种合金的Δσ均为正值,且随着真应变的增加而逐渐减小。
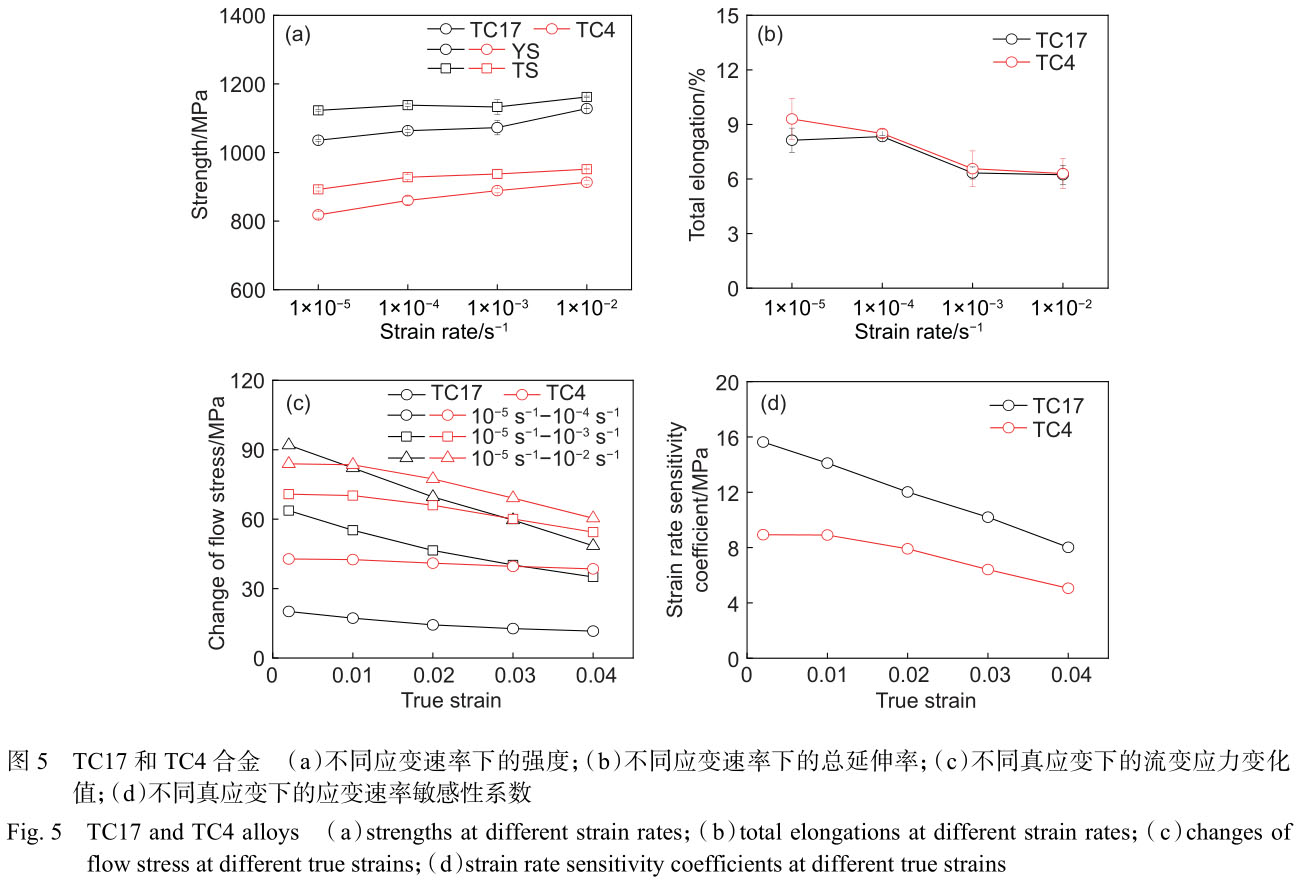
在相同的应变速率变化条件下,TC4合金的Δσ均高于TC17合金。基于不同应变速率下的屈服强度,计算得到TC17和TC4合金的应变速率敏感性系数(m)分别为15.6MPa和8.9MPa。此时m代表应变速率本身导致的流变应力增加,不需要考虑变形组织对流变应力的影响。随着应变的增加,流变应力的变化受到应变速率和变形组织的共同影响
[25],高应变速率下迅速增殖的位错在相界面处塞积而阻碍位错运动,造成应力集中,表现出正的应变速率敏感性。在真应变增加到0.04时,两种合金的m分别减小到8.02MPa和5.06MPa。在相同真应变下,TC17合金的m值更大,表现出更高的应变速率敏感性。依据位错热激活理论,应变速率对屈服强度的影响依赖于位错与短程障碍的交互作用,可以用位错热激活体积(ΔV)来表示,如式(2)所示:∆V=MkBT/m(2)
式中:M为泰勒常数(M=3.06);kB为玻尔兹曼常数(kB=1.38×10-23J/K);T为绝对温度(T=298K)。对∆V的值通过b3归一化处理,b为Burgers矢量。
在屈服点处,TC17和TC4合金的∆V分别为49b3和86b3,这与合金中固溶原子的强化作用和晶格阻力等因素对位错热激活行为的影响有关。随着应变的增加,位错热激活行为还与相界面处的几何必须位错密度有关[25]。
2.3合金拉伸试样的变形组织
图6为TC17和TC4合金拉伸试样断口附近变形组织的OM图。TC17合金的断口裂纹扩展路径不规则,裂纹起伏程度较大,不同应变速率下的试样断口处均观察到锐利峰(图6(a-1)、(a-2))。TC4合金在不同应变速率下的试样断口较为平整,断口处未出现锐利峰,裂纹起伏程度小(图6(b-1)、(b-2))。进一步使用ImageJ软件对断口裂纹扩展距离进行定量测量,结果如图7所示。同一种合金在不同应变速率下断口裂纹扩展距离差距较小,TC17和TC4合金分别为18mm和15mm,这说明应变速率对合金的断口裂纹扩展距离影响不大。在相同应变速率条件下,TC17合金的断口裂纹扩展距离大于TC4合金,这与断口处裂纹起伏程度有关。如图6(a-1)、(a-2)的局部放大图所示,在TC17合金的网篮组织中,交错排列的板条状α相容易使断口裂纹在扩展过程中发生偏转,从而导致断口形状不规则。裂纹在尖端应力集中的作用下扩展并穿过β晶粒,当裂纹遇到不同位向β晶粒时,裂纹扩展方向将发生偏离并沿晶界处连续分布的α相扩展。另外,板条状α相与残余β相形成了大量的相界面,微裂纹易在相界面处萌生并扩展,导致主裂纹分叉,进一步增加了裂纹的扩展距离[26]。裂纹扩展距离长,扩展过程中需要消耗更多的能量,提高了合金抵抗裂纹失稳扩展的能力。从图6(b-1)、(b-2)的局部放大图中可以看出,双态组织中的初生α相呈等轴状,具有较好的协调变形能力,当初生α相分布在β转变组织的晶界处时,会对微裂纹萌生过程产生抑制作用[12],因此在TC4合金的断口裂纹附近未观察到微裂纹。另外,β转变组织中次生α相排列较为规则,裂纹穿过β转变组织时难以随意偏转,从而使断口形状较为平整。裂纹在扩展过程中未出现较大的起伏,消耗的能量较少,阻碍后续裂纹失稳扩展的能力较弱。
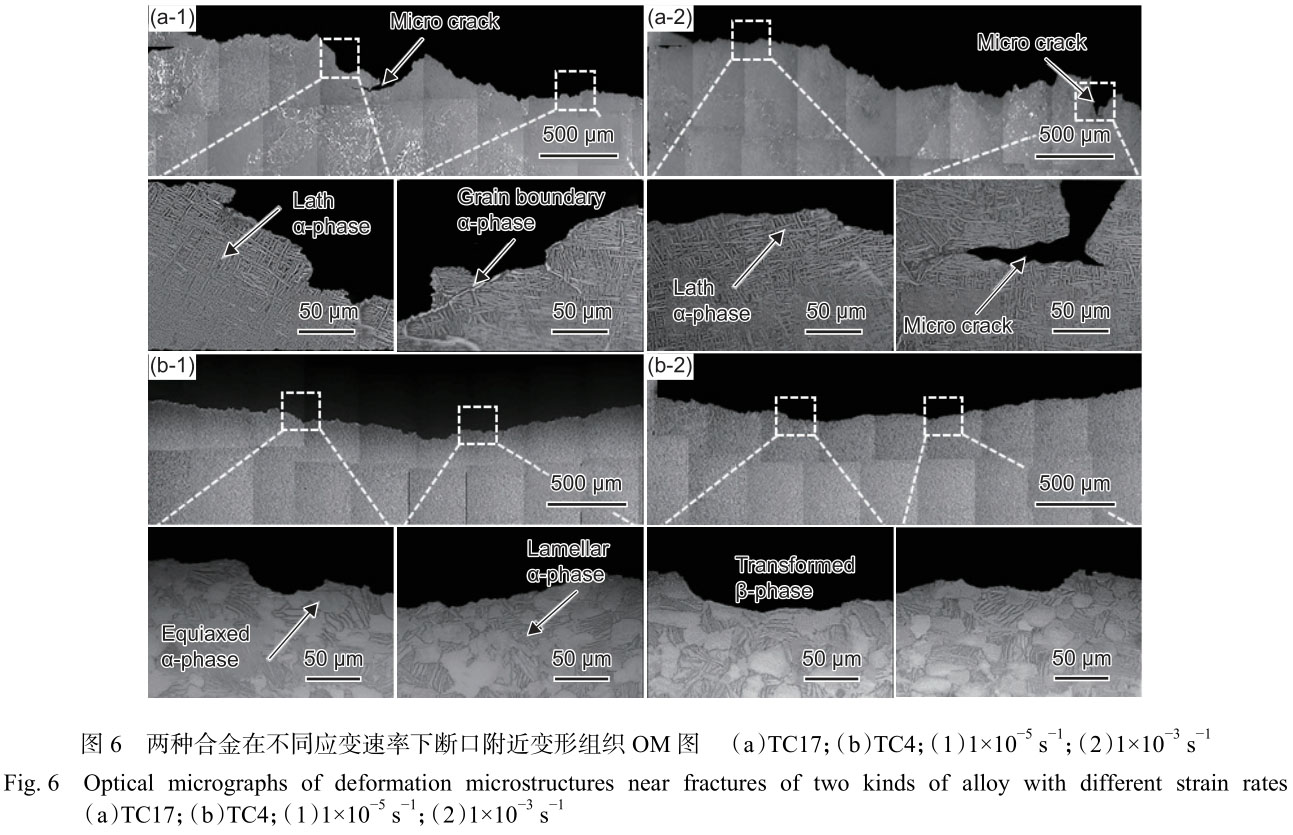
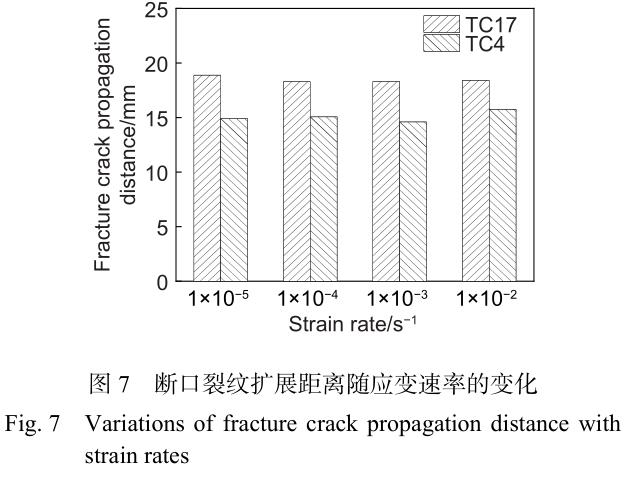
图8为两种合金在1×10−3s−1下断口附近变形组织的EBSD图。图8(a1-1)~(a1-3)为TC17合金在1×10−3s−1应变速率下的变形组织EBSD图(扫描步长为0.6μm)。断口处主裂纹在扩展过程中分叉形成微裂纹,微裂纹发生穿晶断裂,穿过大量的板条状α相继续扩展。为了分析微裂纹的扩展情况,对微裂纹尖端区域做了进一步的BSD分析(扫描步长为0.1μm),如图8(a2-1)~(a2-3)所示。微裂纹尖端区域有沿着α/β相界面继续扩展的趋势,且在β晶粒的晶界处再次分叉,形成更为细小的微裂纹(图8(a2-1))。板条状α相间分布着残余β相(图8(a2-2)),在微裂纹附近的残余β相发生了较大程度的变形,难以被很好地解析标定。相较于板条状α相,残余β相具有更高的KAM值,如图8(a2-3)所示。由于网篮组织中大量的板条状α相交错排列,导致α/β相界面较多,相界面容易对位错滑移产生阻碍作用,导致位错运动的平均自由行程短。同时,位错容易在α/β相界面处发生塞积,形成应力集中,也促进了相界面处的微裂纹萌生。
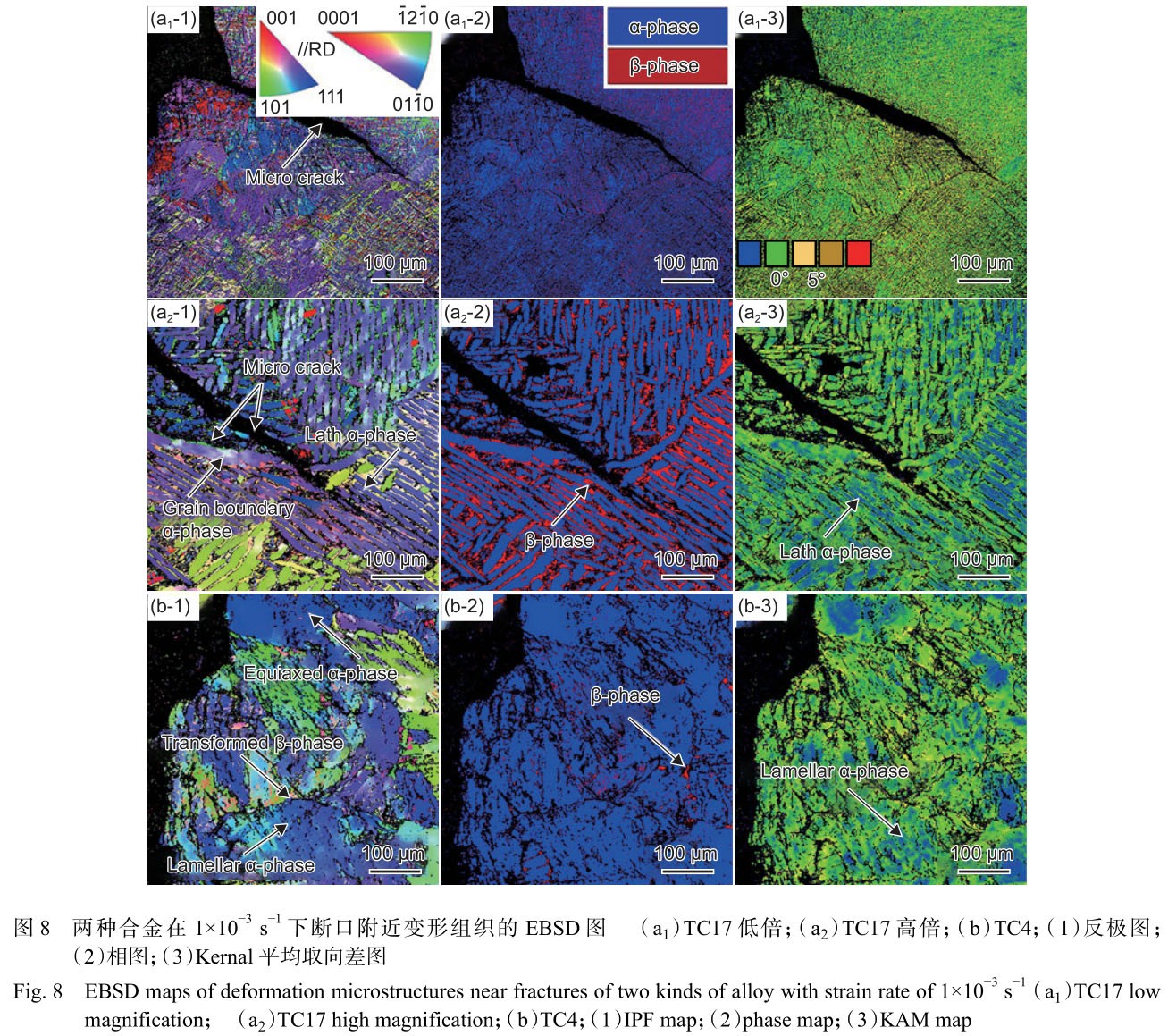
图8(b-1)~(b-3)为TC4合金在1×10−3s−1应变速率下的变形组织EBSD图(扫描步长为0.1μm)。
断口裂纹在扩展过程中发生了穿晶断裂,穿过片层状的次生α相(图8(b-1)),且未观察到微裂纹。图8(b-2)中只显示出少量的残余β相,且难以被很好地解析标定。从图8(b-3)中也可以看出,初生α相和片层状的次生α相具有较低的KAM值,而分布在α相间的残余β相的KAM值较高,变形程度更大。对于双态组织,初生α相呈等轴状,具有较好的协调变形能力,位错运动至初生α相时所受的阻碍作用较小,且位错运动的平均自由行程长。
另外,β转变组织中的次生α相排列方式导致α/β相界面减少,对位错运动的阻碍作用减弱。因此与网篮组织相比,双态组织的强度较低而塑性变形能力较好。
2.4合金拉伸试样的断口形貌
图9为TC17和TC4合金分别在1×10−5s−1和1×10−3s−1应变速率下的拉伸断口形貌SEM图。如图9(a-1)、(a-2)的局部放大图所示,TC17合金断口凹凸不平,断口表面观察到锋利的凸起峰和裂纹形貌。断口处包含大量尺寸较小的韧窝,大部分韧窝形状呈现椭圆形,韧窝周围分布着微孔。另外断口处裂纹较深,裂纹处呈现撕裂状台阶形貌,且裂纹附近存在拉长韧窝。从图9(a-1)、(a-2)的局部放大图中可以看出,与TC17合金相比,TC4合金的断口较为平整,断口处凸起少且较为钝化。断口表面存在着尺寸较大的韧窝,韧窝周围同样分布着大量的微孔。断口表面未观察到裂纹形貌,韧窝拉长的现象不明显。与TC17相比,TC4合金断口的韧窝和微孔的尺寸均有所增大。图10统计了两种合金在不同应变速率拉伸后断口处单位面积(100μm2)的韧窝数目。单位面积内的韧窝数目越多,表明单个韧窝的尺寸越小。从图10可以看出,随着应变速率的增加,两种合金单位面积内的韧窝数目均呈现出增多的趋势。在相同应变速率下,TC17合金单位面积内的韧窝数目多于TC4合金。位错在运动过程中容易在相界面处发生塞积而形成应力集中,促进微孔形核,微孔形核后长大并聚集形成韧窝[27]。相比于网篮组织,双态组织中α/β相界面较少,从而使微孔形核较少。微孔聚集形成的韧窝数目较少,单个韧窝尺寸更大,相对应的合金塑性较好。
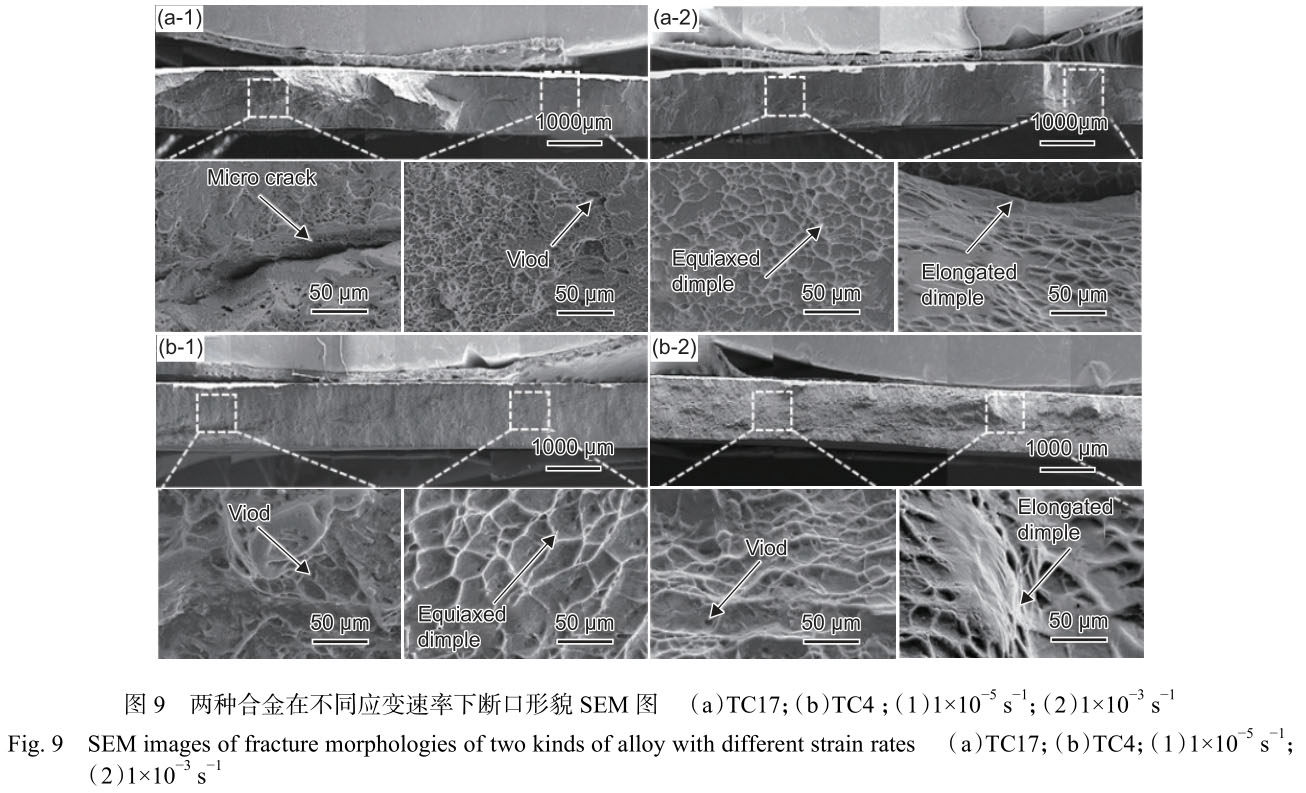
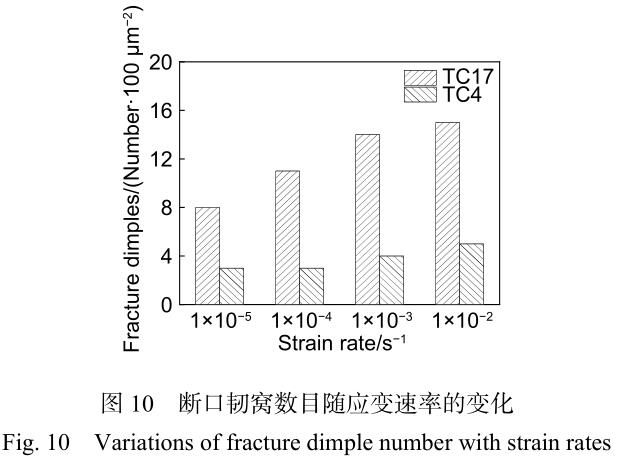
3、结论
(1)TC17和TC4钛合金锻件的屈服强度和抗拉强度随应变速率的增加逐渐升高,表现出应变速率强化效应,且两种合金的总伸长率呈现下降趋势。在相同应变速率下,TC17合金具有较好的强塑性匹配,而TC4合金强度较低且塑性较好。两种合金均表现为正流变应力的应变速率敏感性,且应变速率敏感性系数随真应变增加呈现减小的趋势。
(2)TC17和TC4合金的原始组织分别为网篮组织和双态组织,除合金元素的固溶强化外,网篮组织中由于板条状α相与残余β相交错排列,相界面较多,容易产生位错塞积,强度相对较高;而双态组织中初生α相具有较好的协调变形能力,且β转变组织中片层次生α相排列较为规则,对位错的阻碍作用较小,强度相对较低。
(3)TC17合金网篮组织中相界面较多,位错易在相界面处塞积,产生应力集中,促进微孔形核并长大聚集形成大量小尺寸韧窝,降低了合金塑性。TC4合金双态组织中相界面较少,微孔形核减少,导致断口处韧窝数目少且韧窝尺寸大,合金的塑性较好。
参考文献:
[1]王增强. 先进航空发动机关键制造技术 [J]. 航空制造技术,2015(22):34-38.
WANG Z Q. Key manufacturing technology of advanced aeroengine[J]. Aeronautical Manufacturing Technology,2015(22):34-38.
[2]FU Y Z, GAO H, WANG X P, et al. Machining the integral impeller and blisk of aero-engines: a review of surface finishing and strengthening technologies[J].Chinese Journal of Mechanical Engineering, 2017,30(3):528-543.
[3]蔡建明,弭光宝,高帆,等. 航空发动机用先进高温钛合金材料技术研究与发展 [J]. 材料工程,2016,44(8):1-10.
CAI J M,MI G B,GAO F,et al. Research and develop-ment of some advanced high temperature titanium alloys for aero-engine[J]. Journal of Materials Engineering,2016,44(8):1-10.
[4]黄张洪,曲恒磊,邓超,等. 航空用钛及钛合金的发展及应用 [J]. 材料导报,2011,25(1):102-107.
HUANG Z H,QU H L,DENG C,et al. Development and application of aerial titanium and its alloys[J]. Materials Reports,2011,25(1):102-107.
[5]ZHANG X S,CHEN Y J,HU J L. Recent advances in the development of aerospace materials[J]. Progress in Aerospace Sciences,2018,97:22-34.
[6]刘世锋,宋玺,薛彤,等. 钛合金及钛基复合材料在航空航天的应用和发展 [J]. 航空材料学报,2020,40(3):77-94.
LIU S F,SONG X,XUE T,et al. Application and devel-opment of titanium alloy and titanium matrix composites in aerospace field[J]. Journal of Aeronautical Materials,2020,40(3):77-94.
[7]蔡建明,田丰,刘东,等. 600 ℃ 高温钛合金双性能整体叶盘锻件制备技术研究进展 [J]. 材料工程,2018,46(5):36-43.
CAI J M, TIAN F, LIU D, et al. Research progress in manufacturing technology of 600 ℃ high temperature titanium alloy dual property blisk forging[J]. Journal of Materials Engineering,2018,46(5):36-43.
[8]蔡建明,李娟,田丰,等. 先进航空发动机用高温钛合金双性能整体叶盘的制造 [J]. 航空制造技术,2019,62(19):34-40.
CAI J M,LI J,TIAN F,et al. Manufacture of high tem-perature titanium alloy dual-property blisk used for advanced aero-engine[J]. Aeronautical Manufacturing
Technology,2019,62(19):34-40.
[9]李祚军,田伟,张田仓,等. 线性摩擦焊接钛合金整体叶盘研制与实验研究 [J]. 航空材料学报,2020,40(4):71-76.
LI Z J,TIAN W,ZHANG T C,et al. Development and experimental study on linear friction welding titanium alloy blisk[J]. Journal of Aeronautical Materials, 2020,40(4):71-76.
[10]GUO P, ZHAO Y Q, ZENG W D, et al. The effect of microstructure on the mechanical properties of TC4-DT titanium alloys[J]. Materials Science and Engineering:A,2013,563:106-111.
[11]LI C L,MI X J,YE W J,et al. A study on the microstruc-tures and tensile properties of new beta high strength titanium alloy[J]. Journal of Alloys and Compounds,2013,550:23-30.
[12]SHI X H,ZENG W D,LONG Y,et al. Microstructure evolution and mechanical properties of near-α Ti-8Al-1Mo-1V alloy at different solution temperatures and cool-ing rates[J]. Journal of Alloys and Compounds, 2017,727:555-564.
[13]LIANG R,JI Y P,WANG S J,et al. Effect of microstruc-ture on fracture toughness and fatigue crack growth beha-vior of Ti17 alloy[J]. Metals,2016,6(8):186.
[14]YAMABE- MITARAI Y, KURODA S, MOTOHASHI N,et al. Effect of microstructure on tensile properties of Ti-17 alloys forged using a 1500-ton forging simulator [J]. MATEC Web of Conferences,2020,321:04014.
[15]MATEO A,CORZO M,ANGLADA M,et al. Welding repair by linear friction in titanium alloys[J]. MaterialsScience and Technology,2009,25(7):905-913.
[16]李晓红,张彦华,李赞,等. 热处理温度对 TC17(α+β)/TC17(β)钛合金线性摩擦焊接头组织及力学性能的影响 [J]. 材料工程,2020,48(1):115-120.
LI X H,ZHANG Y H,LI Z,et al. Effect of heat treat-ment temperatures on microstructure and mechanical property of linear friction welded joints of titanium alloysTC17(α+β)/TC17(β)[J]. Journal of Materials Engineer-ing,2020,48(1):115-120.
[17]高峻,罗皎,李淼泉. 航空发动机双性能盘制造技术与机理的研究进展 [J]. 航空材料学报,2012,32(6):37-43.
GAO J,LUO J,LI M Q. Advance in manufacture techno-logy and mechanism of aero-engine dual property disk[J]. Journal of Aeronautical Materials,2012,32(6):37-43.
[18]JIAO L,QIAO S R,ZHANG C Y,et al. Fatigue proper-ties of Ti17 alloy strengthened by combination of electric spark treatment with ultrasonic surface treatment[J]. Rare Metal Materials and Engineering,2010,39(12):2091-2094.
[19]WU J F,ZOU S K,ZHANG Y K,et al. Microstructures and mechanical properties of β forging Ti17 alloy under combined laser shock processing and shot peening[J].Surface and Coatings Technology,2017,328:283-291.
[20]SUN J Z,LI M Q,LI H. Deformation behavior of TC17 titanium alloy with basketweave microstructure during isothermal compression[J]. Journal of Alloys and Com-pounds,2018,730:533-543.
[21]朱知寿,商国强,王新南,等. 航空用钛合金显微组织控制和力学性能关系 [J]. 航空材料学报,2020,40(3):1-10.
ZHU Z S,SHANG G Q,WANG X N,et al. Microstruc-ture controlling technology and mechanical properties relationship of titanium alloys for aviation
applications[J]. Journal of Aeronautical Materials,2020,40(3):1-10.
[22]王丹,赵兴东,徐建伟,等. 两相区变形对 TC17 钛合金组 织 及 拉 伸 性 能 的 影 响 [J]. 热 加 工 工 艺 , 2020,49(6):73-76.
WANG D,ZHAO X D,XU J W,et al. Effect of deforma-tion in two-phase region on microstructure and tensile properties of TC17 titanium alloy[J]. Hot Working Tech-nology,2020,49(6):73-76.
[23]王博涵,程礼,崔文斌,等. 锻造工艺对 TC4 钛合金组织和力学性能的影响 [J]. 热加工工艺,2021,50(23):17-21.
WANG B H,CHENG L,CUI W B,et al. Effect of for-ging process on microstructure and mechanical properties of TC4 titanium alloy[J]. Hot Working Technology,
2021,50(23):17-21.
[24]CAI M H,WEI X,ROLFE B,et al. Microstructure and texture evolution during tensile deformation of symmet-ric/asymmetric-rolled low carbon micro alloyed steel[J].Materials Science and Engineering A, 2015, 641: 297-304.
[25]YAO K, MIN X H. Abnormal strain rate strengthening and strain hardening with constitutive modeling in body-centered cubic {332}<113> TWIP titanium alloy[J].Acta Materialia,2022,226:117641.
[26]SHAO H,ZHAO Y Q,GE P,et al. In-situ SEM observa-tions of tensile deformation of the lamellar microstruc-ture in TC21 titanium alloy[J]. Materials Science and Engineering:A,2013,559:515-519.
[27]李静,林鑫,钱远宏,等. 激光立体成形 TC4 钛合金组织和力学性能研究 [J]. 中国激光,2014,41(11):109-113.
LI J,LIN X,QIAN Y H,et al. Study on microstructure and property of laser solid forming TC4 titanium alloy[J]. Chinese Journal of Lasers,2014,41(11):109-
113.
收稿日期:2022-11-10;修订日期:2022-12-12
基金项目:辽宁省航空发动机冲击动力学重点实验室开放基金 项 目 ( JC36021050017) ; 国 家 自 然 科 学 基 金 项 目(52071051)
通讯作者:闵小华(1974—),男,博士,教授,主要从事高性能钛合金研究,联系地址:辽宁省大连市大连理工大学材料科学与工程学院(116024),E-mail: minxiaohua@dlut.edu.cn
相关链接