一、前言
集成电路产业是信息技术领域的核心产业,是事关经济社会发展和国家安全的战略性、基础性、先导性产业。随着第五代移动通信、物联网、人工智能等信息技术的迅速发展,集成电路的重要性更加凸显,相关产业持续高增长。材料是集成电路产业链的上游环节,对集成电路制造业发展与创新起着至关重要的支撑作用[1];一代技术依赖一代工艺,一代工艺依赖一代材料。在后摩尔时代,无论是延续摩尔定律,还是扩展摩尔定律,集成电路性能提升主要依赖新材料、新工艺、新器件、新集成技术[2,3]。为了制造具有更高运转速度、增强性能特征、更低功耗的新器件,需要开发高性能新材料。
高纯金属溅射靶材是集成电路金属化工艺中采用物理气相沉积方法制备薄膜的关键材料。早期的集成电路主要使用铝及铝合金、钛及部分贵金属等作为靶材;随着集成电路先进逻辑、先进存储、先进封装以及其他新器件技术的发展,使用靶材拓展至铜、钽、钴、镍、钨、钼、钒、金、银、铂、钌、钪、镧等有色金属及合金材料[4~6]。与平面显示、太阳能等领域相比,集成电路对靶材的技术要求最高,集成电路用靶材的制备技术突破难度最大[7~9]。为了提升靶材的综合性能,在高纯金属冶金提纯、熔铸成型、粉末烧结、微观组织调控、异质焊接,靶材结构优化设计、分析检测、应用评价等方面开展了系统研发[4~9]。随着集成电路 7 nm 及以下先进逻辑器件、新型存储器件、三维集成等先进器件及技术的创新突破[3],靶材技术性能提升方面的需求更显迫切,同时下游应用验证的难度进一步增大。
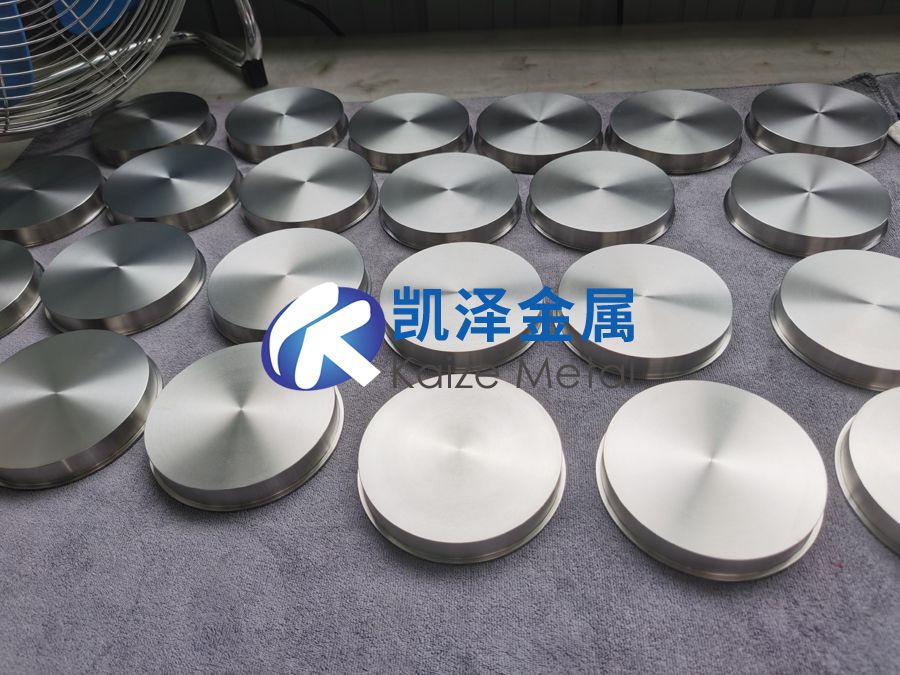
客观来看,目前全球集成电路用高纯金属溅射靶材市场由美国、日本企业占据主导地位;虽然我国有色金属行业具有规模优势,但在电子信息领域的高纯金属新材料开发方面滞后于下游产业的发展需求,有关材料亟待突破并实现自主可控。当前,国家级发展规划已将高纯金属和溅射靶材列为新一代信息技术产业发展的重要材料类型。在此背景下,本文针对集成电路用高纯金属溅射靶材,分析需求、梳理现状、剖析问题,进而明确重点方向、提出保障建议,以为高纯金属溅射靶材的科技进步、行业升级以及相应材料基础研究提供参考。
二、集成电路用高纯金属溅射靶材应用需求分析
(一)材料功能需求
高纯金属溅射靶材在集成电路前道晶圆制造、后道封装的金属化工艺中有着广泛应用,主要用于制作互连线、阻挡层、通孔、接触层、金属栅以及润湿层、黏结层、抗氧化层等薄膜[4,6]。
在晶圆制造中,对于逻辑器件,互连、接触、栅极等所需关键薄膜材料,随着技术节点的缩小而在不断演变。① 早期的铝互连工艺,铝及铝合金用作互连线材料,钛用作对应的阻挡层材料;在90 nm节点后,铜互连工艺成为主流,铜及铜合金用作互连线材料,钽用作对应的阻挡层材料;对于7 nm及以下节点,晶体管结构的变革使得钴、钌、钼、钨等金属及合金等成为更具潜力的互连线或阻挡层材料[10~12]。② 关于晶体管源、漏和栅极与金属连线之间的接触层材料,随着技术节点的缩小也从早期钛、钴的硅化物逐渐发展为以镍(掺铂)为主的硅化物[13]。③ 在晶体管缩小的过程中,自 45 nm节点引入高介电金属栅极后,采用钛、钽等金属及氮化物材料取代多晶硅制作金属栅极,获得了合适的有效功函数和高的热稳定性[6]。
存储器件包括动态随机存取内存、闪存等主流存储芯片,磁性随机存储器、相变随机存储器等新型存储芯片;除了技术节点缩小带来的互连、接触等材料演变外,在存储功能方面对材料提出了新的更高要求,因而钨及钨合金、镧、钴铁硼、锗锑碲等金属及合金材料在栅极层、磁性层、相变层等功能薄膜构建方面将发挥重要作用[3,6]。
对于后道封装,随着集成电路先进封装技术的发展,在凸点下金属层、重布线层、硅通孔等工艺中,铝、钛、铜、钽、钨钛、金、银、镍钒等材料广泛用于薄膜制备,实现芯片与芯片、芯片与基板之间的高密度可靠互连[6,7]。
高纯金属是制备靶材的原材料,化学纯度是影响薄膜材料性能的关键因素之一。集成电路用高纯金属靶材纯度通常在 4N5 以上,对碱金属、碱土金属、放射性金属元素、气体杂质等都有严格控制要求。随着技术节点的缩小,金属靶材的纯度对薄膜材料性能及品质的影响突显,如 14 nm用铜靶材纯度要求超过 6N5。高纯金属材料提纯制备技术主要分为物理提纯法、化学提纯法,通常采用多种物理、化学方法联合提纯来制备集成电路用高纯材料。
集成电路用高纯金属溅射靶材在密度、晶粒尺寸、织构、焊接结合率、尺寸精度、表面质量等方面有一整套严格的标准。集成电路工艺越先进,对金属靶材品质的要求也越高。随着晶圆尺寸的增加,金属靶材尺寸随之增大,材料的组织均匀性控制、高精度成型加工等技术难度也在提升。为了进一步提高金属靶材的使用性能,还需对靶材外型结构进行优化设计。因此,从微观品质、宏观规格来看,高纯金属溅射靶材面临着越来越高的技术要求。
(二)产业发展需求
“核心电子器件、高端通用芯片及基础软件产品”“极大规模集成电路制造装备及成套工艺”国家科技重大专项的实施,确立了集成电路产业的技术基础,在关键装备、材料产业方面实现了重要突破。2014 年设立了国家集成电路产业投资基金,保持了对集成电路产业的扶持力度。我国集成电路市场规模达到 10 458 亿元(2021 年),年均复合增长率为
19.3%[14]。2021 年,我国集成电路产量为 3594 亿块(同比增长 33.3%),进口量为 6355 亿块(同比增长16.9%)[15]。我国集成电路产业发展较快,但因制造技术滞后于国际先进水平,高端芯片、重大装备、关键材料的进口依存度居高不下,亟待自主创新发展。
集成电路市场的旺盛需求、产业自主可控发展需求等,推动了高纯金属溅射靶材行业发展,相应市场规模从 8.4 亿元(2015 年)增长到 18.2 亿元(2022 年)[14]。在数字经济驱动下,半导体行业的长期高景气度,国产化替代进程加速,使得集成电路产业对各种高纯金属材料及溅射靶材的需求量将持续增长,从而为高端有色金属材料行业发展提供宝贵机遇和广阔空间。
三、集成电路用高纯金属溅射靶材的发展现状
(一)集成电路用高纯金属溅射靶材行业的整体情况
1. 国际情况
工业发达国家在集成电路用高纯金属溅射靶材方向的开发与应用,时间久、基础好、系统性强、积累深厚,相关的产业技术水平很高。尤其是美国、日本,较早开展高纯金属溅射靶材的研发工作,积极布局核心专利,具有完备的技术垂直整合能力(从金属材料的高纯化制备到靶材制造生产),在高端靶材市场占据优势地位。
日本在半导体材料方向全球领先,从事高纯金属研制的企业有日立金属株式会社、住友化学株式会社、三菱综合材料株式会社、日矿金属株式会社等,可工业化生产铝、钛、铜、镍、钴、钽、钨等高纯产品(最高纯度在 6N以上)。美国作为半导体大国,大量生产和消耗高纯金属材料,如霍尼韦尔国际公司可提供除铝之外的集成电路用高纯金属材料。海德鲁公司(挪威)、普莱克斯有限公司(法国)在高纯铝市场具有优势,世泰科公司(德国)、攀时公司(奥地利)在高纯钨、钼、钽等难熔金属市场具有优势,优美科公司(比利时)在高纯稀贵金属生产与回收方面具有优势。集成电路用高端溅射靶材的主要研制和生产企业有日矿金属株式会社、霍尼韦尔国际公司、普莱克斯有限公司等[16]。例如,
日矿金属株式会社作为世界最大的集成电路靶材供应商,在铜、钽、钴、镍铂、钨等高纯靶材方向占据着较高的市场份额,与集成电路制造企业合作广泛。
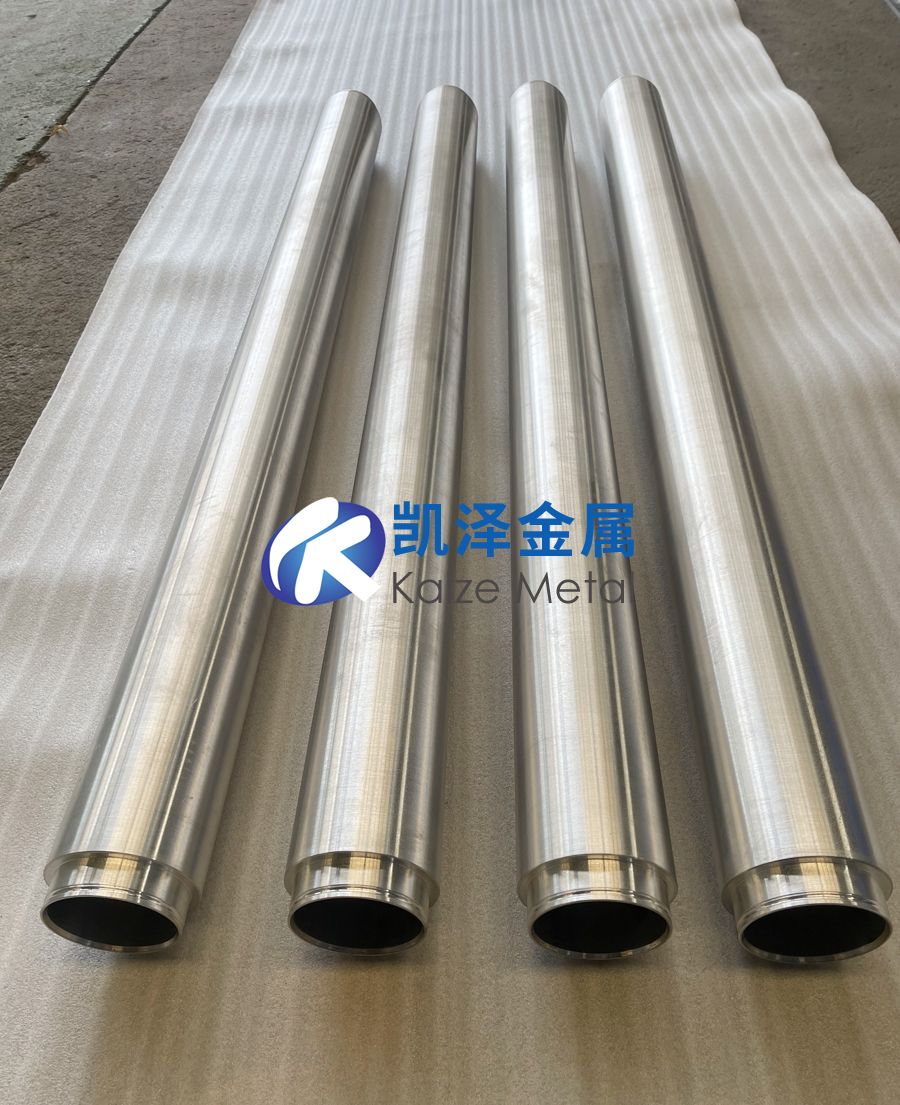
2. 国内情况
在我国,集成电路用高纯金属溅射靶材行业起步较晚、基础薄弱,近年来受益于国家支持及自身成长,突破关键制备技术并形成高纯金属原料和溅射靶材研发制造体系,在产品性能方面逐步缩小与世界水平的差距。
在高纯金属方面,国内企业围绕集成电路用靶材需求,共同推动高纯金属材料行业发展;代表性的企业有新疆众和股份有限公司、有研亿金新材料有限公司、宁夏东方钽业股份有限公司、金川集团股份有限公司、宁波创润新材料有限公司、厦门钨业股份有限公司等。整体来看,国内企业掌握了多种高纯金属制备技术并实现产业化:严格控制有害杂质元素
含量,实现金属纯度从工业级向电子级提升;完成高纯铝、铜、钛、钽、镍、钴、贵金属等材料的国产化 (铝纯度>5N5,铜纯度>6N,钽纯度>4N5,钛、镍、钴、金、银、铂、钨等金属纯度>5N),制备了大尺寸、低缺陷、高纯度的金属坯料用于溅射靶材生产。
在溅射靶材方面,国内企业以有研亿金新材料有限公司、宁波江丰电子材料股份有限公司为代表,已在国际市场占有一席之地。针对不同种类高纯金属的加工特性,相关企业制定了专有的微观组织控制策略并不断优化工艺,突破了晶粒细化与取向可控、高质量焊接、精密加工与检测等关键制备技术;联合产业链的上下游企业,在涵盖靶材设计及制备、
薄膜性能测试评价在内的全技术链条上开展合作,驱动技术迭代创新。目前,高纯铝及铝合金、钛、铜及铜合金、钴、镍铂及贵金属等靶材技术取得突破,产品性能达到国外同类水平,通过了国内外集成电路企业验证,实现批量生产和稳定供应。
(二)集成电路用高纯金属溅射靶材的细分方向研制情况
1. 高纯铝及铝合金靶材
铝具有易于沉积、刻蚀性能与加工性能好、电导率高、导热性能好、与衬底之间的附着性及结合性能好、成本低廉等特点,在90 nm技术节点以上是主要的互连线材料,在先进封装方面也有广泛应用。
纯铝用作互连金属材料会产生“铝穿刺”“电迁移”问题,可添加铜、硅以有效抑制铝单晶颗粒移动,从而改善铝金属互连线导致的半导体结构漏电现象,同时有效控制铝金属互连线之间的接触电阻[6]。
在铝靶材方面,国内外的技术水平整体相当,主要的靶材供应商都能制备多种型号的铝靶材产品。海德鲁公司、普莱克斯有限公司、住友化学株式会社是国外主要的高纯铝原材料供应商。新疆众和股份有限公司、南通泰德电子材料科技有限公司研制的铝最高纯度达到 6N,在集成电路领域实现国产材料应用。未来需要在大尺寸、细晶低缺陷高纯铝及铝合金铸锭方面继续提升,实现更高水平的性能一致性与稳定性。
2. 高纯铜及铜合金靶材
铜相比铝具有更低的电阻率、更高的导热性、更好的抗电迁移能力。铜及铜合金作为 90~7 nm技术节点集成电路互连材料,不仅可以降低延迟、提高运算效率,还能提高集成电路的可靠性[12]。在90 nm工艺节点,采用高纯铜靶材制备铜互连线籽晶层,但因铜线容易与 SiO2基底发生互扩散而导致器件失效。在 65~1X nm 工艺节点,可通过合金化提高铜籽晶层的稳定性,如采用 Cu-Al、Cu-Mn 等合金材料来抑制线宽减小带来的电迁移及电阻电容延迟等问题。在 14~7 nm工艺节点,采用更高纯度的铜靶材制备集成电路互连线籽晶层。此外,铜磷阳极通常配合铜及铜合金靶材用于互连线制备。
日矿金属株式会社、霍尼韦尔国际公司在高纯铜原材料提纯、高端铜及铜合金靶材方面具有完备的生产线,是世界高纯铜及铜合金靶材的主要供应商。有研亿金新材料有限公司成为世界第三家拥有完整的超高纯铜提纯、超高纯铜及铜合金靶材产品制备技术并实现批量应用的公司,生产的高纯铜材料最高纯度达到 7N。随着国内 90 nm 以下 300 mm晶圆厂的陆续投产,市场对高纯铜及铜合金靶材的需求量快速增长,可进一步升级生产线设备以扩充产能并提升产品的稳定性。为了避免靶材溅射过程中出现异常放电导致的颗粒化问题,确保超高纯铜及合金原材料的纯净度至关重要[17];特别是对于28 nm以下工艺,国产原材料内夹杂缺陷稳定控制水平还需进一步提升,用于制备Cu-Mn合金靶材的5N以上高纯锰提纯技术有待突破。
3. 高纯钛靶材
钛具有良好的抗腐蚀性及黏附性,钛靶材用于溅射沉积纯钛膜或反应溅射沉积TiN 膜,主要用作铝互连的扩散阻挡层、钛硅化物接触层及抗反射层,在先进封装方面也有广泛应用[6]。钛 / TiN 膜用作铝互连中铝线与硅衬底间的扩散阻挡层、钨塞的底线层及黏附层,纯钛膜用作底线层、黏附层、盖帽层、抗反射层等,纯TiN 膜用作铜互连硬掩膜层和保护镍铂化合物膜层的盖帽层。
在钛靶材方面,国内外技术水平整体相当;国内多家靶材企业能够批量供应大部分型号的集成电路用高纯钛靶材,但在长寿命 / 高效率设计、细晶高强度扩散等方面与国际先进水平存在一定差距。在高纯钛制备方面,针对钛材质活性强、提纯难度高的特点,宁波创润新材料有限公司采用熔盐电解+电子束熔炼方法实现了 4N5、5N高纯钛的国产化;5N5 高纯钛提纯工艺、钛锭坯料品质一致性等还需提升。
4. 高纯钽靶材
钽是一种过渡族稀有难熔金属,具有较高的熔点、密度、抗腐蚀性以及优异的延展能力,因其独特的物理化学性质可防止铜向硅基底扩散。在90 nm以下铜制程集成电路中,钽 / TaN膜开始用作铜互连的扩散阻挡层,还可作为集成电路后道封装工艺中铝或铜衬垫层外侧的阻挡层。近年来,采用溅射方法,钽还用于制备高介电栅介质层的氧化物薄膜,有助于进一步缩小晶体管的关键尺寸、有效改善晶体管的驱动能力[18]。
在集成电路用靶材市场上,钽靶材占比最高,也是技术难度最高的类型之一,需要严格控制钽靶材内部的晶粒尺寸及取向,确保晶粒均匀分布。日矿金属株式会社、世泰科公司(钽靶坯业务被美题隆公司(美国)收购)的钽靶材制备技术最为先进。国内企业在大尺寸、高纯度钽靶材的组织均匀性控制及取向分布等方面存在差距,导致溅射薄膜均匀性不佳,需要在高均匀变形、取向调控等关键技术点上进行深化研究。
在高纯钽原材料方面,日矿金属株式会社、世泰科公司、环球卓越金属有限公司(澳大利亚)都能提供 4N5 以上高纯钽;宁夏东方钽业股份有限公司掌握了高纯钽提纯制备的全套工艺方法,生产的4N5 高纯钽填补了国内空白,在 5N钽锭的个别杂质元素稳定控制、大锭型钽锭制备方面还需进一步提升。目前,国内高端钽靶材(或板坯)依赖进口,国产化自给率远低于铝、铜、钛等靶材,有关高纯钽靶制备以及钽提纯等技术有待研发升级。
5. 高纯钴和镍铂靶材
钴、镍铂具有优异的铁磁性和良好的导电性,通过溅射制备薄膜再反应生成钴、镍的硅化物,用于集成电路源极、漏极、栅极等与金属之间的接触。钴、镍铂靶材分别用于 130~90 nm、65~20 nm逻辑器件工艺;随着线宽的减小,可增加镍铂合金中的铂含量,以进一步提高镍铂硅薄膜的高温稳定性并改善界面形貌[13]。鉴于存储器件工艺要求低于逻辑器件,钴、镍铂靶材还可应用于1X nm存储工艺中。当技术节点发展到7 nm技术时,钴的电阻率低、抗电迁移性能优异,开始替代铜成为新的互连线材料[11]。
由于钴、镍铂均具有较强的磁性,在磁控溅射时会一定程度上屏蔽磁场而导致起辉或维持放电困难;为了保证溅射性能及薄膜均匀性,需调控靶材相结构、再结晶状态来提升透磁性[19]。通常,接触层厚度非常薄(<10 nm)、均匀性要求高,靶材透磁率过低或均匀性差都会导致薄膜厚度及均匀性无法满足要求。7~5 nm先进制程对高纯钴靶材的纯度、磁性能、均匀性等都提出了更高要求。
高纯、低氧、高透磁的钴靶材供应商主要是日矿金属株式会社,霍尼韦尔国际公司有部分200 mm晶圆用钴靶供应能力。有研亿金新材料有限公司掌握了铁磁性靶材微观组织、透磁性能均匀调控技术,在 200~300 mm 晶圆用钴靶材方面实现突破 ,成为高透磁钴靶产品市场的有力竞争者。在高纯钴生产方面,日矿金属株式会社、霍尼韦尔国际公司具有产业链集成优势,有研亿金新材料有限公司、金川集团股份有限公司能够通过深度除杂电解制备5N以上钴板。目前,国内针对 7 nm及以下制程的钴靶材制备技术有待提升,主要涉及材料纯度提升、透磁率及波动性能改善,以更好满足先进制程对薄膜的严苛要求。
高纯镍铂靶材主要分为 Ni-5at%Pt、Ni-10at%Pt等,国际市场的主要供应商有日矿金属株式会社,霍尼韦尔国际公司、东曹株式会社(日本)等。有研亿金新材料有限公司攻克了系列镍铂靶材制备关键技术,通过了国内外知名半导体制造企业验证并实现批量供货。镍铂合金材料含有贵金属,纯度通常在 4N5 以上,除了对靶材内部缺陷、微观组织均
匀性、透磁性能、表面质量等提出严苛要求外,相关成本控制较为关键。随着镍铂靶材需求量的增加,除了批次稳定性、一致性的要求外,开展铂的综合回收利用以及提高生产效率等也显迫切。
6. 高纯钨及钨合金靶材
钨及钨合金是集成电路存储芯片制造用关键材料。存储器工艺技术节点通常在 65~1X nm,钨及钨硅合金因其电导率高、电子迁移抗力高、高温稳定性优良、与硅衬底接触良好,在金属栅中用于制备高纯钨 / 氮化钨金属堆垛膜层及硅化钨栅极层,在字线层中用于制备金属互连层及金属间通孔、垂直接触的填充物。
高纯钨及钨合金靶材市场由日矿金属株式会社、东曹株式会社、世泰科公司等主导,而高纯钨及钨合金靶材的国产化程度极低,相应产品依赖进口[14]。传统钨加工工艺制备出的高致密、高纯靶材溅射薄膜均匀性差,无法达到先进制程芯片的高品质要求;国产钨靶材在高纯降氧控制、均匀合金化、大尺寸烧结成型、高均匀变形、取向调控等方面存在一定差距[9]。在高纯钨原材料方面,日矿金属株式会社、世泰科公司可生产满足要求的 5N高纯钨粉;厦门钨业股份有限公司、崇义章源钨业股份有限公司等公司具备 5N高纯钨粉生产能力,但粉体的一致性和稳定性需要提升。
7. 其他高纯金属及合金靶材
在集成电路晶圆制造以外,先进封装领域还需金、银、镍钒、钨钛等高纯金属及合金靶材。这些靶材主要关联先进封装中的凸块、重布线、硅通孔、共形屏蔽等工艺技术,用于制造阻挡层、润湿层、黏附层、抗氧化层、屏蔽层等[6]。优美科公司是先进封装领域靶材的主要供应商之一。国内靶材企业实现了先进封装类靶材从高纯原材料到终端产品的全过程性能控制,在靶材的大尺寸、高纯化、高均匀性、高稳定性、长寿命性能控制等方面形成了一定的技术优势;低成本、高品质的靶材产品广泛供应国内外市场。
四、我国集成电路用高纯金属溅射靶材发展挑战分析
(一)部分靶材产品和关键原材料依赖进口
铝、钛、铜、钴、镍等高纯金属及合金溅射靶材已实现国产化;但在钨、钽、其他高纯特种金属及合金溅射靶材方面,因制备加工技术难度大或者下游尚未形成大规模应用需求,未能全面突破靶材制备核心技术。国产靶材与进口产品相比,性能品质存在一定差距。相关靶材所用的高纯原材料尚未完全实现国产化,如高纯铝、钛、钽、锰、钒等原材料在杂质元素与缺陷控制上难以满足高端应用需求,进口依赖度依然较高。靶材焊接所需的背板材料也没有完全实现国产化,国产铜镍硅铬、铜锌锡等合金背板材料的产品质量有待提升,仍需进口以弥补应用需求。
(二)材料性能一致性和稳定性不高、智能化制造水平待提升
集成电路用靶材除了技术指标要求高外,对产品一致性、批次稳定性也有极高的要求。在高纯金属溅射靶材从研制到产业化、产品由样件到量产的过程中,加工工艺的一致性及可重复性与关键装备水平、人才队伍能力密切相关。靶材加工的生产流程长,纯度、内部缺陷、微观组织性能、表面质量等在生产过程中易受多种因素影响,也难以进行在线实时监测。相关靶材企业未能积累足够的技术储备、市场批量验证反馈的经验,多品种、小批量的生产特点也不利于智能化制造水平提高。以上因素共同导致了靶材生产质量管控困难,产品性能的一致性、可重复性不高,低良率与高成本共存。
(三)面向前沿的新材料验证机会少、验证周期长集成电路先进制程落后于国际约两代水平,因而面向前沿领域的新材料开发距离先发企业有较大差距;对靶材与薄膜的组织性能关系理解不深刻,与溅射工艺相结合的靶材优化设计能力相对欠缺,先进制程以及新型器件所需的关键靶材缺乏验证机会。薄膜性能(膜厚、应力、电阻率、粗糙度、片内均匀性、片间均匀性)及器件的电性能、可靠性评估等,均与靶材密切相关,而下游客户通常倾向于采用国外成熟机台及配套靶材以确保快速进入量产,导致国产靶材应用机会少、迭代改进慢、验证周期长,也就制约了靶材技术创新和新品开发能力。
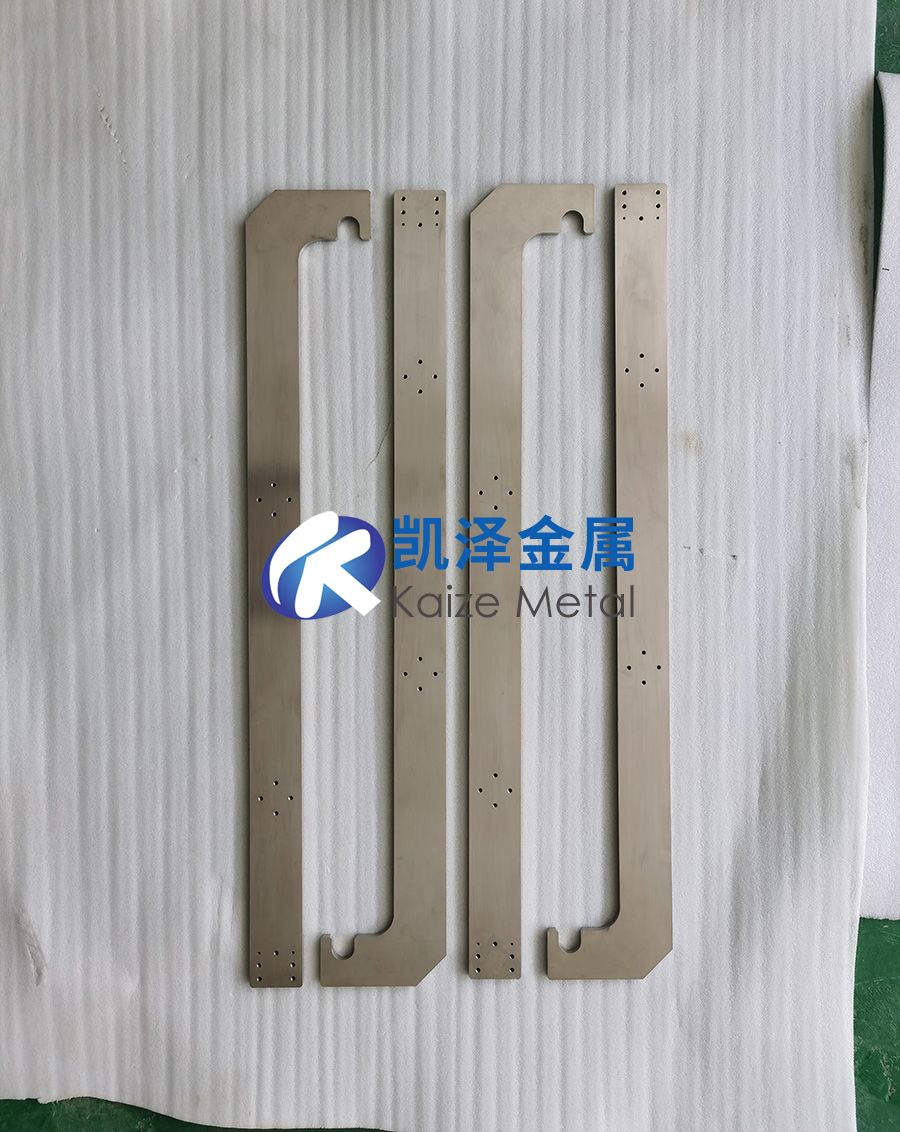
(四)加工和检测环节的关键设备不满足需求从高纯材料提纯到高性能靶材制备,都需要性能稳定、高可靠性的加工和检测设备。熔铸、压力烧结、焊接等关键环节都存在国产设备技术指标不匹配要求、设备稳定性及可靠性偏低等问题,相关的电子束熔炼炉、热等静压机、热压烧结炉、电子束焊机等高端装备亟待提高技术水平。纯度、气体杂质元素、微缺陷、微观组织与织构取向相关的分析检测仪器设备,对于靶材新品研制、成熟产品质量管控不可或缺。国产的分析检测设备距离应用需求差距较大,导致等离子体质谱仪、碳硫分析仪、氮氧氢分析仪等高精度设备较多依赖进口,而辉光放电质谱仪完全依赖进口。
五、我国集成电路用高纯金属溅射靶材的重点发展方向
突破高端靶材制备关键技术并实现工程化,保持先进工艺关键配套材料的自主可控,是支撑集成电路产业安全和可持续发展的关键内容。集成电路工艺的提升,带来了靶材纯度、多元化材料、精细化微观组织等方面的新需求,对靶材的可靠性、一致性也有更高要求。为了提高薄膜材料的综合性能,微观组织均匀可控、高强度、高稳定性、长寿命的高效能溅射靶材是发展重点,涉及强塑性变形控制、高强度焊接、靶材结构优化设计等关键环节[8,20];高纯度、高洁净的金属原材料是减少溅射过程中异常放电、颗粒缺陷等问题的前提,需要持续提升高纯材料精炼提纯技术及分析检测能力。合理加大高纯金属溅射靶材技术研发及产业升级的支持力度,力争在 2030 年前后使我国成为世界高纯金属溅射靶材的主要供应国之一。
(一)提升高纯金属材料制备技术水平,实现批量稳定生产
针对集成电路用靶材对高纯原材料的需求,开发成套提纯工艺及设备,全面实现铝、钛、铜、钽、钴、钨、钼、镍、钒、锰、金、银、铂、钌、钪、镧等高纯金属的自主生产,切实保障原材料供应安全[21]。
对于已有一定产业基础能力的高纯铝、铜、钛、钽、钴、镍、钨、金、银、铂等材料,着重针对国产高纯材料个别杂质元素含量超标、产品一致性差、批次之间性能不稳定等问题,立足现有提纯制备技术基础,进行技术提升与智能化改造,深度净化和去除有害杂质元素以提升纯度等级;开展工艺 ‒ 设备耦合试验及稳定性验证,优化工艺结构,以连续化、自动化设备应用为主要形式来提升高纯材料的产能。
对于当前技术基础薄弱、市场亟需或者未来前景良好的高纯锰、钒、钌、钪、镧等金属,探明杂质元素去除机理,开发提纯新工艺新设备,制备满足集成电路需求的高纯金属,在技术成熟的基础上控制成本并扩大生产规模。
(二)攻克高性能靶材制备关键技术,驱动靶材智能化生产
针对集成电路先进逻辑器件、先进存储器件、先进封装等薄膜沉积制备需求,开发全系列高端靶材产品。加强智能化生产线建设,实现铝及铝合金、钛、铜及铜合金、钽、钴、镍铂、钨及钨硅、镍钒、钼、金、银等高纯金属及合金靶材的规模化供应。
对于已量产的高纯铝及铝合金、钛、铜及铜合金、钴、镍铂、金、银等靶材,在现有技术基础上进一步优化工艺,整体达到国际先进水平。针对靶材品种多、门槛高、专用性强的特点,建设柔性、敏捷的智能化生产线,提升生产能力、产品稳定性、成本控制水平,形成具有国际市场竞争力的高纯金属溅射靶材产品体系。
对于当前技术成熟度低、尚未完全国产化的高纯钽、钨等金属及合金靶材,对标国际先进水平,集中力量突破核心技术;优化工艺能力,推动在下游集成电路企业的考核验证,满足当前应用亟需;在产品合格、技术成熟的基础上,扩大生产规模,积极开拓市场。
(三)瞄准电子信息技术前沿需求,开发高端新材料
面向第五代移动通信、人工智能、物联网、云计算等电子信息技术领域中的新兴应用场景,把握纳米逻辑器件、新型存储器件、高频移动通信滤波器、智能传感器、芯粒异质集成等新型器件及先进技术对新材料的需求。推动集成电路产业领先的研发机构、设备制造商、芯片制造商密切合作,有序开展钌及钌合金、铝钪合金、多元相变合金、钴基特种合金、陶瓷化合物等高纯材料靶材的研发。
着力开发原创技术和产品,实现新领域技术能力的国际同步发展。关注基于新材料、新原理、新结构的颠覆性技术创新,跟踪非硅基半导体材料的发展,针对相关领域所需薄膜材料进行提前布局。
(四)提升分析检测与应用评价能力,完善材料标准及评价体系建设
针对靶材性能分析测试与应用验证需求,建立完善的电子材料分析测试和应用研发平台。① 根据集成电路先进器件和工艺对高纯金属溅射靶材的严苛要求,在材料的痕量 / 超痕量元素分析、微缺陷分析、晶粒尺寸、织构取向等方面建立或完善检测标准、工艺标准、产品质量标准,研制集成电路用高纯金属标准物质并进行推广应用。② 针对薄膜沉积需求进行靶材测试验证,明确靶材的关键性能控制指标、应用性能评价指标,提出靶材验证操作规范、工艺标准,构建完整的评价体系。
提升检测能力、完善评价体系,支持打通集成电路用高纯金属溅射靶材“性能 ‒ 制备 ‒ 应用”完整流程,为靶材开发提供包括材料性能分析检测、产品应用评价在内的综合解决方案。合理降低材料企业创新应用门槛,实质性提高研发效率、缩短研发周期,加速集成电路材料体系的技术创新与国产化进程。
六、集成电路用高纯金属溅射靶材发展建议
(一)以应用为牵引,加强“产学研用”体系建设
着眼集成电路高端芯片需求,坚持应用牵引,采取“产学研用”协同创新模式,由靶材企业牵头,联合上下游优势企业和科研院所,发展靶材全流程组织、结构、工艺一体化的集成设计与调控理论,突破制约集成电路及新兴产业发展的高端靶材关键制备加工技术;为集成电路产业提供关键战略基础材料保障,通过技术创新带动高纯金属溅射靶材行业各环节协同发展。加强基础技术研究,注重与下游客户的紧密合作,推动靶材性能验证和快速迭代;优化并提升高纯金属及靶材制备技术,开发更高性能的靶材产品并实现量产,促进高纯金属溅射靶材行业的可持续发展。
(二)解决关键设备国产化问题,实现智能化生产
系统开发高纯金属溅射靶材用关键设备及仪器,如电子束熔炼炉、热等静压设备、电子束焊机、智能热处理装备、智能加工机床,高精度辉光放电质谱仪、等离子体质谱仪、碳硫分析仪、氮氧氢分析仪。应用信息化、智能化、数字化技术,实现高纯材料及靶材制造全流程的智能控制与检测分析能力,提高生产能力与效率,降低原材料损耗率与能耗,提升产品性能与质量稳定性,全面增强市场竞争力。
(三)加大优势团队支持力度,加强人才队伍建设
建议给予集成电路材料研发与产业化优势团队的连续稳定支持,建立高水平、开放性的科技创新平台,促进材料冶金、加工、分析检测和半导体技术的交叉融合,切实提升高纯金属溅射靶材的工艺技术水平。完善人才培育和培养模式,构建包括领军人才、创新创业人才、工程技术人才在内的高水平专业队伍,积极引入具有国际化背景的制造、管理、生产技术专家;加强青年人才培养,合理落实人才激励措施,为高纯金属靶材行业健康发展提供源动力。
(四)掌握自主知识产权,开展标准体系建设
开展高纯金属溅射靶材的专利布局规划,着重突破高纯原材料、靶材加工工艺及装备关键技术,支持高纯金属靶材全产业链国产化和自主创新;稳步形成相关技术的自主知识产权,逐步积累技术优势,建立具有竞争力的专利池,争取核心知识产权的国际地位。开展集成电路用高纯金属溅射靶材上下游系列产品、检测方法的标准化建设,完善评价体系,保障高纯金属溅射靶材产业发展质量。
(五)加强国际合作交流,做好全球化布局
稳健加强并对外合作,积极融入世界集成电路产业生态圈,提升国际合作层次及水平,构筑互利共赢的产业链、供应链利益共同体。支持具有优势的靶材企业与国际半导体制造企业及科研机构的深度合作,鼓励新材料、新技术联合开发。着眼世界集成电路技术前沿,发挥我国有色金属企业的加工优势及成本优势,面向国际市场开展高纯金属溅射靶材产业布局,尽快跻身全球高端靶材供应商行列。
参考文献
[1] “先进半导体材料及辅助材料”编写组. 中国先进半导体材料及辅助材料发展战略研究 [J]. 中国工程科学, 2022, 22(5): 10‒19.
Writing Group of Advanced Semiconductor Materials and Auxiliary Materials. Strategic study on the development of advanced semiconductor materials and auxiliary materials in China [J] .Strategic Study of CAE, 2022, 22(5): 10‒19.
[2] 吴汉明, 吴关平, 吴金刚, 等. 纳米集成电路大生产中新工艺技术现状及发展趋势 [J]. 中国科学: 信息科学, 2012, 42(12): 1509‒1528.
Wu H M, Wu G P, Wu J G, et al. The status and trend of novelprocess and technology in nano-IC manufacturing [J]. Scientia Sinica Informationis, 2012, 42(12): 1509‒1528.
[3] 卜伟海, 夏志良, 赵治国, 等. 后摩尔时代集成电路产业技术的发展趋势 [J]. 前瞻科技, 2022, 1(3): 20‒41
Bu W H, Xia Z L, Zhao Z G, et al. Development of integrated circuitindustrial technologies in the post-Moore era [J]. Science andTechnology Foresight, 2022, 1(3): 20‒41.
[4] Rossnagel S M. Sputter deposition for semiconductor manufactur‐ing [J]. IBM Journal of Research and Development, 1999, 43(1‒2):163‒179.
[5] 冯黎, 朱雷. 中国集成电路材料产业发展现状分析 [J]. 功能材料与器件学报, 2020, 26(3): 191‒196.
Feng L, Zhu L. Analysis of the development status of integratedcircuit material industry in China [J]. Journal of Functional Materialsand Devices, 2020, 26(3): 191‒196.
[6] Sarkar J. Sputtering materials for VLSI thin film devices [M].Norwich: William Andrew Publishing, 2014.
[7] 田民波. 薄膜材料与薄膜技术 [M]. 北京: 清华大学出版社,2006.
Tian M B. Thin film technologies and materials [M]. Beijing:Tsinghua University Press, 2006.
[8] 何金江, 贺昕, 熊晓东, 等. 集成电路用高纯金属材料及高性能溅射靶材制备研究进展 [J]. 新材料产业, 2015, 17(9): 47‒52.
He J J, He X, Xiong X D, et al. Research status of high purity metals and high performance sputtering target used in integratedcircuit [J]. Advanced Materials Industry, 2015, 17(9): 47‒52.
[9] 刘文迪. 集成电路用钨溅射靶材制备技术的研究进展 [J]. 中国钨业, 2020, 35(1): 36‒41
Liu W D. Research progress of preparation technology of tungstensputtering targets for integrated circuits [J]. China TungstenIndustry, 2020, 35(1): 36‒41.
[10] Bourzac K. Cobalt could untangle chips’ wiring problems chipmakers are replacing some copper connections [J]. IEEE Spectrrum,2018, 55(2): 12‒13.
[11] Nogami T, Zhang X, Kelly J, et al. Comparison of key fine-lineBEOL metallization schemes for beyond 7 nm node [C]. Hsinchu:2017 Symposium on VLSI Technology, 2017.
[12] 李亚强, 马晓川, 张锦秋, 等. 芯片制程中金属互连工艺及其相关理论研究进展 [J]. 表面技术, 2021, 50(7): 24‒43.
Li Y Q, Ma X C, Zhang J Q, et al. Research progress of metal interconnection technology and related theory in chip fabrication [J].Surface Technology, 2021, 50(7): 24‒43.
[13] 屠海令, 王磊, 杜军. 半导体集成电路用金属硅化物的制备与检测评价 [J]. 稀有金属, 2009, 33(4): 453‒461.
Tu H L, Wang L, Du J, et al. Preparation and characterization ofmetal silicides used for semiconductor integrated circuits [J]. ChineseJournal of Rare Metals, 2009, 33(4): 453‒461.
[14] 中国半导体行业协会半导体支撑业分会, 集成电路材料产业技术创新联盟. 中国半导体支撑业发展状况报告(2022 年编) [R].北京: 中国半导体行业协会半导体支撑业分会, 集成电路材料产业技术创新联盟, 2022.
Semiconductor Support Industry Branch of China SemiconductorIndustry Association, Integrated Circuit Materials Industry Technology Innovation Alliance. Report on the development of China’ssemiconductor support industry(2022) [R]. Beijing: SemiconductorSupport Industry Branch of China Semiconductor Industry Association,Integrated Circuit Materials Industry Technology InnovationAlliance, 2022.
[15] 中华人民共和国工业和信息化部. 2021 年电子信息制造业运行情况 [EB/OL]. (2022-01-28)[2022-08-15]. https://www.miit.gov.cn/gxsj/tjfx/dzxx/art/2022/art_0997d192aa6f46fa8d76549f20b4e5d6.html.
Ministry of Industry and Information Technology of the People’sRepublic of China. Operation of electronic information manufacturingindustry in 2021 [EB/OL]. (2022-01-28)[2022-08-15]. https://www.miit.gov.cn/gxsj/tjfx/dzxx/art/2022/art_0997d192aa6f46fa8d76549f20b4e5d6.html.
[16] 张卫刚, 李媛媛, 孙旭东, 等. 半导体芯片行业用金属溅射靶材市场分析 [J]. 世界有色金属, 2018, 12(10): 1‒3.
Zhang W G, Li Y Y, Sun X D, et al. Market analysis of metal sputteringtarget materials used in semiconductor chip industry [J].World Nonferrous Metal, 2018, 12(10): 1‒3.
[17] Bian Y J, Cha M Y, Chen L, et al. Correlation between the formation of particle defects on sputtered Cu seed layers and Cu targets [J].Micro & Nano Letters, 2019, 14(10): 1079‒1082.
[18] 陈林, 黄峰. 一种半导体器件及其制造方法: 201611075036 [P].2018-06-05.
Chen L, Huang F. A semiconductor device and its manufacturingmethod: 201611075036 [P]. 2018-06-05.
[19] Luo J F, Fang Y Y, Xu G J, et al. Development of ferromagnetic sputtering targets with high performance [J]. Materials ScienceForum, 2020, 930: 820‒825.
[20] Boydens F, Leroy W P, Persoons R, et al. The influence of targetsurface morphology on the deposition flux during direct-current magnetron sputtering [J]. Thin Solid Films, 2013, 531: 32‒41.
[21] 干勇, 彭苏萍, 毛景文, 等. 我国关键矿产及其材料产业供应链高质量发展战略研 [J]. 中国工程科学, 2022, 24(3): 1‒9.
Gan Y, Peng S P, Mao J W, et al. High-quality development strategyfor the supply chain of critical minerals and its material industryin China [J]. Strategic Study of CAE, 2022, 24(3): 1‒9.
相关链接