锻件是制造各种机械设备、压力容器及受压元件毛坯的原材料,在电力、机械、核工业、交通、石油天然气、化工等领域的应用非常广泛。在锻造过程中经常会出现一些宏观缺陷,这些宏观缺陷在产品使用中可能会导致产品失效,影响设备的使用,甚至会引发重大事故,造成不可挽回的损失。因此,必须在锻件制造过程中发现缺陷,及时处理,以排除安全隐患,保证产品质量符合使用要求。[1~2]无损检测技术是控制产品质量必不可少的技术之一。借助科学设备和技术手段,可以在不破坏产品本体的基础上,对锻件表面及内部性能和结构进行检测,以判断其内部组织的连续性、完整性和安全性。如今,无损检测技术已广泛应用于经济建设的各个领域。[1~2]超声检测是五大常规无损检测技术中应用最广泛,检测工件内部宏观缺陷最有效的无损检测方法。超声检测也是产品制造中实现质量控制,节约原材料的重要手段之一[1~2]。因此,对锻件,尤其是大型件和重要件进行超声检测是锻件质量的必要保证手段。几乎所有法规产品锻件都要进行超声检测。宝鸡凯泽金属,作为钛法兰、钛方块、钛饼等钛锻件生产厂家,对锻件的生产工艺,有深入的理解,结合相关资料,对锻件超声检测时机、探头角度、锻件超声回波信号的研判,锻件超声DGS曲线法的使用等问题进行讨论,以利于检测人员能够及时发现锻件缺陷,确保产品质量。
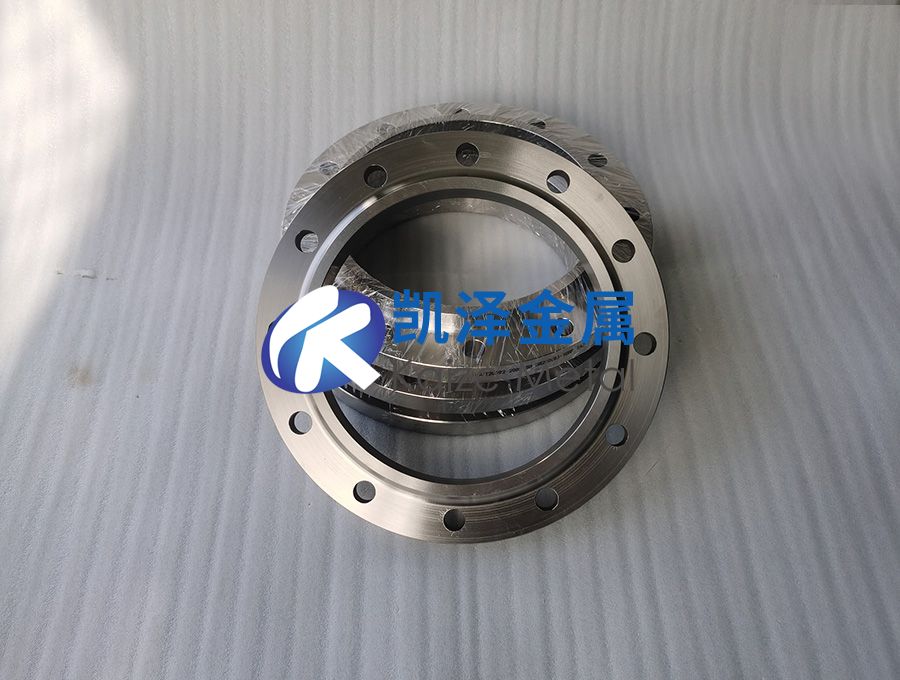
1、 检测时机
锻件超声波检测可分为原材料检测、制造过程中的检测、产品检测,以及在役检测。原材料检测和制造过程中检测的目的是要尽早发现锻件内部缺陷,以便能够及时采取措施,避免缺陷扩大导致锻件报废;产品检测的目的就是要保证产品的最终质量。在役检测的目的是要监督投入使用后产品内部可能产生的缺陷,主要是疲劳裂纹。
一般来说,锻件中的缺陷主要有两个来源:一是铸锭中的缺陷引起的;另一种是在锻造、热处理及机械加工等制造过程中产生的。锻件的超声波检测一般应安排在交货状态进行,或在锻件的最终热处理之后,槽、孔、台阶等的加工之前进行。为防止不合格产品进入下一道工序,节约制造成本,提高生产效率,尤其是避免热处理后的锻件形状不适合超声检测的问题,则一般应在热处理或粗加工之前进行超声波检测,但热处理后还要对锻件的可检测区域作100%检测。
我公司生产的大型转子超声波检测时间:淤粗加工后的超声波检测是为了在转子有较大余量时尽早发现缺陷,以便通过轴向借位、径向借心等手段将部分缺陷去除掉。此时工件还有较多处的黑皮。
于调质前超声波检测时转子已经加工成最简单的几何形状,离成品尺寸还有较大余量,但外表面已经没有黑皮,精加工后各台阶的圆角R处现在还是直台,超声探头的始脉冲在工件外表面形成的盲区会在精加工阶段被加工掉。调质前的材料晶粒比较粗大,导致超声波的衰减较大(但一般小于4 dB/m);此时超声波的检测可覆盖精加工后的全部工件。
盂调制后超声波检测是在去掉调质黑皮后进行的超声波检测。此时除材料晶粒较细,草状波和衰减小于调质前外,其它状态与调质前相同。
榆精加工后超声波检测时转子已经加工成交货状态。部分区域受几何形状限制已经无法进行超声波检测。对于电机转子主要是各台阶的圆角R 处;对于气轮机转子,除了圆角R 处之外,还有轴身上的开槽处。
2、 探头角度
锻件检测一般采用单晶直探头。对于尺寸较小的锻件,由于单晶直探头存在盲区和受近场区影响,改用双晶直探头检测。部分锻件超声检测标准甚至规定用先单晶直探头进行全体积检测,再在近表面补充双晶直探头检测。
有时为了检测与检测面成一定倾角的缺陷,也可以采用一定探头角度的横波斜探头进行检测,例如筒形和环形锻件。横波斜探头的折射角按相关标准的规定选择。
针对特殊结构的锻件,应根据结构和易产生缺陷的位置,按照相关标准选择角度合适的探头。如检测大型转子时通常采用单晶直探头,并用7毅和14毅的小角度斜探头做辅助检测,以便保证产品质量。
3、缺陷反射波性质判别
在锻件超声波检测中,不同缺陷的反射回波是不同的,实际检测过程中,可根据显示屏上的缺陷反射回波来分析缺陷的性质和类型。
(1)单个缺陷反射回波
锻件超声波检测中,显示屏上单独出现的缺陷反射回波称为单个缺陷反射回波,一般单个缺陷回波是指与邻近缺陷间距大于50mm,回波高不小于准2mm的缺陷,如锻件中单个夹层、裂纹等缺陷。检测到单个缺陷时,要测定缺陷的位置和大小。当缺陷较小时,用当量法;当缺陷较大时,用6dB法。
(2)分散缺陷反射回波
锻件检测中缺陷较多且较分散,缺陷彼此间距较大时,这种缺陷的反射波称为分散缺陷反射回波。一般在边长为50mm的立方体内少于5个,或在更大的范围内存在几个反射波,如分散性的夹层缺陷。分散缺陷一般不太大,常用当量法定量(见表1)。
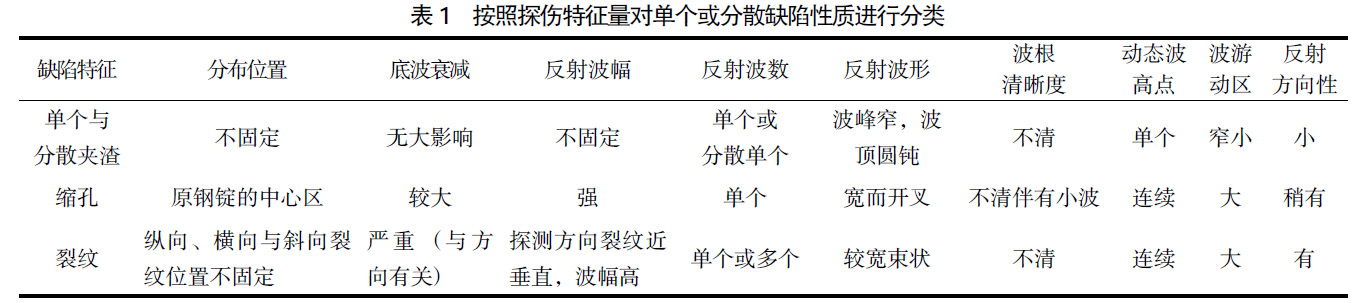
(3)密集缺陷反射波
锻件检测中显示屏上同时显示的缺陷反射回波很多,且波与波之间的间距很小,有时波的下沿连成一片,这种缺陷的反射回波称为密集缺陷反射回波。
密集缺陷可能是疏松、非金属夹杂物、白点或成群的裂纹等(见表2)。

(4) 游动反射回波
在圆柱形轴类锻件超声检测过程中,当探头沿着轴的外圆周向移动时,显示屏上的缺陷波会随着该缺陷检测声程的变化而游动,这种游动的动态波形称为游动反射回波。
游动反射回波的产生是由于不同声束射至缺陷形成反射引起的。当声束轴线射至缺陷时,缺陷的声程小,反射回波高。当沿圆周方向移动探头,使扩散声束射至缺陷时,缺陷声程变大,反射回波降低,致使同一缺陷反射回波的位置和高度随探头的移动发生游动(见图1)。
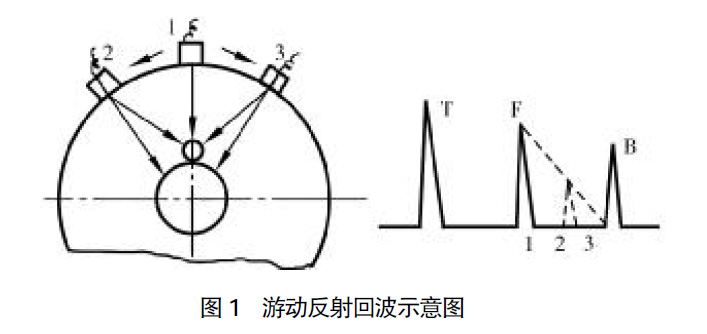
选择不同超声检测灵敏度时,同一缺陷反射回波的游动情况也不同。一般可根据基准灵敏度和反射回波的游动距离来鉴别游动的反射回波。通常缺陷反射回波的游动范围达到25mm时才被认为是游动反射回波。根据缺陷游动反射回波包络线的形状,可粗略地判别缺陷的形状。
(5)底面反射回波判定
锻件超声检测时,可根据底面回波变化来判别锻件中的缺陷情况。
当无缺陷反射回波,而只有底波的多次反射(较薄工件) 或1耀2次底面回波反射,且反射回波较高时,说明工件中无缺陷。
当无缺陷反射回波,而底面回波很低甚至消失时,说明锻件中存在倾斜的大面积缺陷或在检测面的附近有大缺陷。
锻件检测时,在局部区域底面回波很低甚至消失,此时若降低探头频率重新检测该区域,则底波又出现,说明该区域为晶粒粗大造成声波衰减较大而引起的底波消失。
4、锻件DGS法
DGS曲线是描述规则反射体的距离(D)、回波高度(G)及当量尺寸(S)之间关系的曲线,德文缩写为AVG。DGS曲线可用于对缺陷定量和灵敏度的设置。利用DGS曲线可减少超声对比试块的使用,提高锻件超声检测的效率。根据适用性可以将DGS曲线具体分为通用DGS曲线和实用DGS曲线。其中,通用DGS曲线采用归一化距离和归一化缺陷当量大小,所以通用性良好,适用于不同晶片尺寸的探头。但在实际锻件超声检测时,一般使用探头或超声探伤仪厂商提供的适用于特定探头型号的实用DGS曲线。在使用实用DGS曲线时应注意其对应的探头晶片尺寸和探头频率。根据探头不同,DGS曲线又可分为直探头DGS曲线和斜探头DGS曲线。
在实际超声检测中应按照相关技术条件和标准规定使用DGS曲线,其中存在部分锻件超声标准不允许使用DGS曲线法进行检测的情况。如法国核电规范标准协会编制的《法国压水堆核岛机械设备设计和制造规则》RCCM(2002版及2002补遗)中就规定锻件直探头和斜探头检测时均采用对比试块法,不管是针对低合金钢还是奥氏体不锈钢锻件,均不允许使用DGS 曲线法。但同时需要注意的是,RCCM(2007版)及其FM1061修订与RCCM(2002版及2002补遗)相比出现了很大的变化,引进了锻件DGS曲线法检测。针对低合金钢锻件,直探头检测时可采用对比试块法或DGS曲线法,斜探头检测时可采用DGS曲线法;针对奥氏体钢锻件,直探头检测时可采用对比试块法或DGS曲线法,斜探头检测与直探头类似,可采用对比试块法或DGS曲线法。因此,在使用DGS曲线法调整灵敏度和对缺陷定量时应注意相关标准或技术条件的规定。
5、结语
终上所述,在进行锻件超声检测时,应充分考虑被检锻件的尺寸和特性,充分理解检测规范和检测技术要求,充分了解所要检测的缺陷类型,结合具体的制造和检测能力,充分利用好超声检查手段,保证锻件的质量。
参考文献
[1] 郑晖,林树青.超声检测[M] .北京:中国劳动社会保障出版社,2008
[2] 郑中兴.材料无损检测与安全评估[M] .北京:中国标准出版社,2003
相关链接