硬质涂层用溅射靶材对靶材的纯度、内部组织结构、力学强度、外观尺寸要求较高,同时靶材的成分和制备工艺对膜层的各项性能有着决定性影响。
钛铝合金(Ti-Al)作为一种硬质涂层用镀膜靶材,其涂层具有硬、脆、耐磨、抗氧化等优异性能,在刀具、磨具等易损件方面应用较为广泛。但是Ti-Al合金靶材的制备比较困难,在合金化过程中极易产生气泡、缩孔、疏松现象,导致合金的孔隙率高,无法满足靶材致密性的要求。Ti-Al合金靶材的制备工艺成为人们研究的热点,各种新的制备工艺不断涌出,目前常用的制备方法有熔炼法、强电流加热法和烧结法[7-9]。本文主要研究了烧结法中常压烧结和热压烧结两种靶材制备工艺对涂层性能的影响。
1、实验
1.1主要原料及设备
采用Ti粉(粒径不大于45gm,纯度不低于99.8%,质量分数)、Al粉(粒径不大于30μm,纯度不低于99.9%,质量分数)、丙酮(分析纯)、无水乙醇(分析纯)为实验原料。
主要设备包括:球磨机(米淇,MITR-YXQM-1L)、马弗炉(德国Nabertherm,L5/13-LT15/13)、热压烧结炉(上海皓越,VHSgr-20-1600)、磁控溅射镀膜机(德国NSC-4000Suptter)、金相电子显微镜(上海万衡,MM-7C)、扫描电子显微镜(日本电子JEOL,JSM-IT500HR)、X射线衍射仪(荷兰帕纳科,Aeris)、维氏硬度计(苏州南光,HV-l000)。
1.2常压烧结制备TiAI合金靶材
将Ti粉和AI粉按照质量比1:1的比例混合得到TiAl混合粉料,然后将混合粉料和乙醇按照质量比2:3的比例加入球磨混料机,设定好球磨参数(球料质量比为10:1~15:1、大小球比为2:1、氩气保护、转速360r/min),湿磨12h后,在100℃烘干2h,过100μm筛,取小于100μm的粉料压制成形。最后,将坯体置于箱式马弗炉中于1200℃保温5h进行烧结(升温速率:100℃/h),烧结完成后得到TiAI合金靶材。
1.3热压烧结制备TiAI合金靶材
按照1.2中所述的粉料配比和球磨工艺对粉料进行预处理,然后取小于100μm的粉料装入表面涂有BN的石墨模具中。将装有粉料的石墨模具置于真空热压炉中,抽真空至5×10-3Pa后,按照表1中的热压烧结工艺制备得TiAI合金靶材。
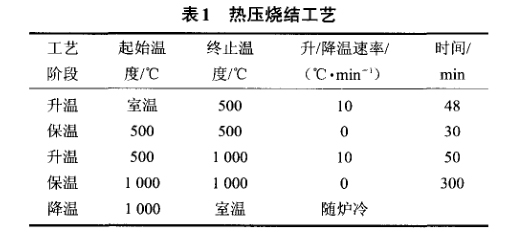
1.4溅射镀膜法制备硬质涂层
采用低碳钢作为基体材料,基体经过抛光、丙酮清洗、乙醇清洗、烘干处理后置于磁控溅射仪真空室内,对系统进行预抽真空至压力为0.1Pa,设置沉积温度为500℃,溅射镀膜功率为100W,Ar气流量为30mL/min。充入Ar作为气体放电载体至气体压力为3.5Pa,对基体进行溅射沉积镀膜15min。图1为溅射镀膜示意图。TiAI靶材经过Ar离子轰击,靶材表面的TiAl离子与加速的Ar离子进行动能交换,并且离开靶材固体,进而沉积在低碳钢基体表面。待真空室内温度降至70℃时,取出试样,得到表面沉积有TiAI硬质涂层的低碳钢材。
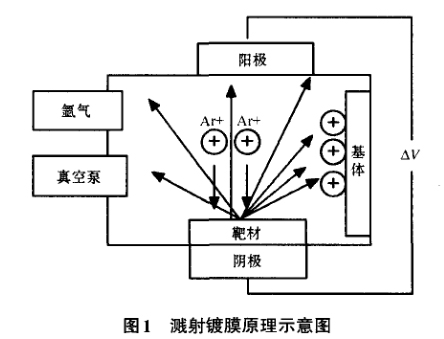
1.5硬质涂层性能测试
采用金相显微镜和扫描电子显微镜分别观察涂层表面;采用x射线衍射仪分析基体表面硬质涂层的物相组成;采用氧化增重法测试涂层的抗高温氧化性能,方法为:试样在1000℃的静态空气中氧化5h,每隔1h取出一组试样,冷却至室温后称取试样的质量,计算单位面积氧化增重,绘制氧化动力学曲线。采用显微维氏硬度计,在载荷为100g,保压15s的条件下对基体表面硬质涂层相邻0.5mm距离的两点取样测试,每个试样采用5点作平均值,测定涂层表面显微硬度值。
2、结果与讨论
2.1金相电子显微镜分析
图2为硬质涂层表面的金相显微照片。其中灰色部分为TiAI硬质涂层,黑色部分为低碳钢基体。
可以看出,常压烧结靶材制备的涂层中出现了部分较密集的TiAI,分散不均匀。这种团聚容易造成应力集中,导致硬质涂层内部出现裂纹,影响涂层的使用性能。热压烧结靶材制备的涂层中,TiAI分布较为均匀,而且涂层组织较为致密。
2.2扫描电子显微镜分析
图3为硬质涂层表面的扫描电子显微镜照片。可以看出,涂层与基体之间存在残渣和气孔等缺陷,并未完全覆盖基材的表面。这种残渣和气孔可能是靶材飞溅到正在沉积生长的涂层表面所造成的,也有可能是当前处理不当导致基体表面不平整造成的。而这缺陷会成为涂裂纹的介质通道,从而影响涂层的使用寿命。热压烧结靶材制备的涂层中,涂层覆盖基体较为完全,残渣和气孔量均比常压烧结靶材制备的涂层减少,且表面更为光滑,这说明热压烧结的靶材溅射效果好。
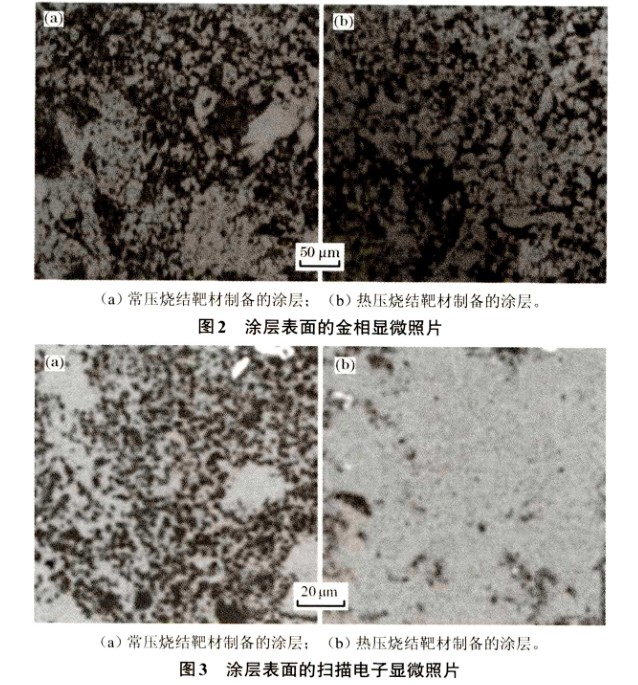
2.3X射线衍射分析
图4为硬质涂层的X射线衍射。可以看出,常压烧结靶材和热压烧结靶材制备的涂层的图谱出峰位置和强度基本一致,在30~50(°)之间有较明显的衍射峰。常烧结和热压烧结的靶材经溅射涂膜之后,其成分一致,晶体相同,说明热压烧结并没有破坏TiAI合金靶材的组成成分,保持了常压烧结成分稳定的优势。
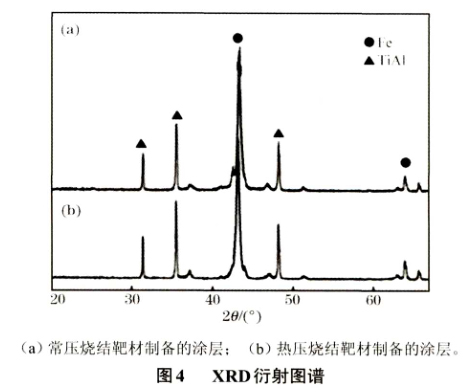
2.4耐高温氧化性分析
图5为不锈钢基硬质涂层在1000℃条件下高温氧化过程中的质量增量随时间的变化曲线。可以看出,常压烧结靶材和热压烧结靶材制备的涂层的氧化质量增加都呈现相同的变化趋势:起始阶段质量增量较大,随着时间的延长,变化率开始减少,最后趋于稳定。说明两种类型涂层的抗氧化机理相似:初始阶段,氧化过程的关键步骤为氧气和表面金属离子间的化学反应,表现为空气中氧气被涂层表面的原子吸附,氧原子与涂层表面的金属离子间的结合力由范德华力转为化学键,其变化过程速率较快;随着氧化反应进行,氧化反应由化学吸附转向氧化膜的形成,此时的氧化速率降低,主要是因为表面形成的氧化膜能够有效地阻碍氧离子向内扩散,并且随着氧化过程的进行,氧化膜厚度增加,离子的扩散距离越来越大,扩散越来越困难。
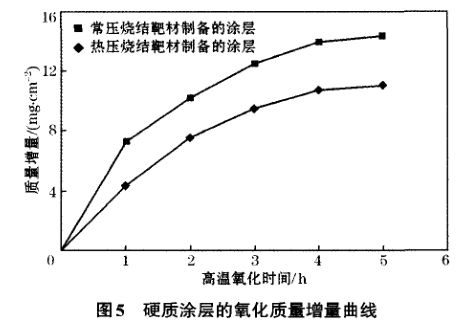
从图中可看出,两种涂层都具有一定的耐高温氧化性能。但是常压烧结靶材涂层的氧化速率更快,而热压烧结靶材涂层的氧化速率相对较慢,这主要是因为热压烧结所形成的涂层致密性更好,氧气扩散速率较慢所致。
2.5显微硬度测试分析
常压烧结靶材制备的涂层的显微硬度值为1798HV,而热压烧结靶材所制备的硬质涂层硬度高达3165HV,提高了76%。涂层的相结构、晶粒尺寸、表面致密性及缺陷等因素都会影响涂层的硬度。从涂层的微观结构对比可知,由于常压烧结靶材所制备的涂层表面致密性较差、颗粒团聚等因素导致了涂层硬度降低。而热压烧结靶材所制备的涂层致密性较高,孔隙率低,削弱了应力集中的现象,有效地阻止了低碳钢基体承受外力时的变形程度,从而使涂层的硬度得到有效提高。
结论
(1)通过对涂层表面显微结构的表征,热压烧结的TiAI合金靶材溅射涂层比常压烧结的要致密均匀,表面覆盖完全,溅射效果好。
(2)通过XRD分析发现,常压烧结和热压烧结的TiAI合金靶材经溅射涂膜之后,其成分一致,晶型相同。
(3)在1000℃同等高温氧化条件下,热压烧结的TiAI合金靶材所形成的涂层比常压烧结靶材涂层的氧化速率慢,耐高温氧化性更好。
(4)热压烧结TiAl合金靶材所制备的硬质涂层显微硬度高达3165HV,比常压烧结TiAl合金靶材制备的硬质涂层显微硬度提高了76%。
参考文献:
[1]梁俊才,穆健刚,张风戈,等.硬质涂层用镀膜靶材的研究[J].粉末冶金工业,2014,24(2):38.
[2]罗俊锋,丁照崇,董亭义,等钌金属溅射靶材烧结工艺研究【J].粉末冶金工业,2012,22(1):28.
[3]贾国斌,冯寅楠,贾英.磁控溅射用难熔金属靶材制作、应用与发展[J].金属功能材料,2016,23(6):48.
[4]陈希,黄蓉,邬晔.钛铝合金溅射镀膜靶材的研究进展[J].湖南有色金属,2O12,28(1):51.
[5]陈利.Ti—A1一N基硬质涂层的热稳定性能/微结构及其力学/切削性能的研究[D].长沙:中南大学,2009.
[6]童洪辉.物理气相沉积硬质涂层技术进展[JJ.金属热处理,2008,33(1):91.
[7]董亭义,小勇,章程,等.磁控溅射钛靶材的发展概述【J】金属功能材料,2017,24(5):57.
[8]董亭义,户赫龙,于文军,等.集成电路用钛靶材和铜铬合金背板扩散焊接技术研究『J1.金属功能材料,2017,24(6):23.
[9]BarshiliaHC,AcharyaS,GhoshM,eta1.Performanceevalu.ationofTiAICrYNnanocompositecoatingsdepositedusingfour-cathodereactiveunbalancedpulseddirectcurrentmagne-tronsputteringsystem[J].Vacuum,2010,85(3):4l1
相关链接