1、引言
光纤在通信、传感和医疗等领域应用广泛,其表面改性是提升性能或实现特定功能的关键。表面改性主要通过涂覆层实现,其中金属涂层因其优异的导电性、导热性和化学稳定性而备受关注。在应用层面,金属涂层光纤能够实现光通信系统中光纤与器件的精准焊接封装,显著增强系统的抗干扰能力,还可以为光纤传感器提供增敏效果,从而拓展其在光纤传感、电信以及光学器件等领域的应用范围[1]。因此金属涂覆层光纤的实现与应用已成为研究热点。
Albert等[2]通过化学气相沉积在光纤表面制备纳米级金和铜镀层,极大地增强光纤的灵敏度。黄博等[3]通过化学镀金-银双金属锥形光纤表面增强拉曼散射探针。张飞翔等[4]通过化学镀在光纤布拉格光栅(FBG)表面制备铜涂层。饶春芳等[5]通过优化化学镀和电镀条件减小应力以改善FBG的传感精度。Li等[6]通过磁控溅射和电镀制备了镍-钛FBG,提高了热敏感稳定性。姚文历等[7]采用化学镀镍再电镀铜制备的FBG温度灵敏系数是普通光纤光栅的1.7倍。Rostami等[8]通过电镀制备了银涂覆层的FBG传感用于实时检测尿素的缓慢释放。Wang等[9]通过磁控溅射和Cu电镀相结合的方法制备的镀铜FBG传感器灵敏度得到提高。
除柱形光纤的金属化外,还有研究者探索异形光纤的金属化以提升传感器性能[10-11]。
多数研究关注金属涂层在光纤传感的应用,但金属涂层光纤的机械性能对光纤焊接封装至关重要。朱月红等[12]改进了光纤表面的化学镀镍工艺,制备的镀镍光纤光栅的抗拉强度达到6.5N(135.65MPa)。Miller等[13]通过化学镀法制备的Ni涂覆层光纤抗拉强度达到22N(3500MPa)。宋启良等[14]优化制备化学镀Ni-P金属镀层工艺,获得光纤最大抗拉强度平均为2783MPa。赵劲凯等[15]通过熔融涂覆法制备了最大8.248N(672MPa)抗拉强度的镀锌光纤。杨珂等[16]在化学镀镍后的光纤表面电镀镍,抗拉强度达到877.20MPa。
金属涂层制备技术主要分为化学方法与物理方法两类。化学方法包括化学镀和电镀,具有一定的局限性,如环境污染风险和工艺复杂性。鉴于此,一些新兴企业更倾向于选择物理方法,如熔融涂覆和磁控溅射。其中熔融涂覆也存在一些限制,只有熔点相对较低(<1400℃)的金属(Pb,Al,Ag,Cu,Au,Ni)才能应用,不适用于Cr、Ti等金属[17]。磁控溅射具有制备过程简单、反应速度快、镀层致密均匀等优点,而目前缺乏磁控溅射制备金属涂层光纤机械性能的相关研究。由于磁控溅射会施加一定的热量和机械应力于光纤表面[18-19],这可能对光纤的机械性能产生影响。因此,本文旨在通过磁控溅射工艺制备金属化光纤,系统性地探究磁控溅射工艺对金属化光纤机械性能的影响机理,并优化光纤金属化磁控溅射工艺。
2、试验
2.1试验步骤
如图1所示,磁控溅射制备光纤金属涂层主要包括以下4个步骤:去涂覆层、装入夹具、等离子清洗、磁控溅射镀膜。其中,光纤组的具体装载流程如图1虚线框所示。首先将待金属化的光纤逐根置入光纤托板的半圆凹槽内(有多个凹槽,可同时放置多根光纤,凹槽尺寸略大于光纤);然后上下调整光纤位置,使待金属化段处于光纤托板空隙处;最后盖上光纤掩膜板确保非镀膜段不会受到污染。
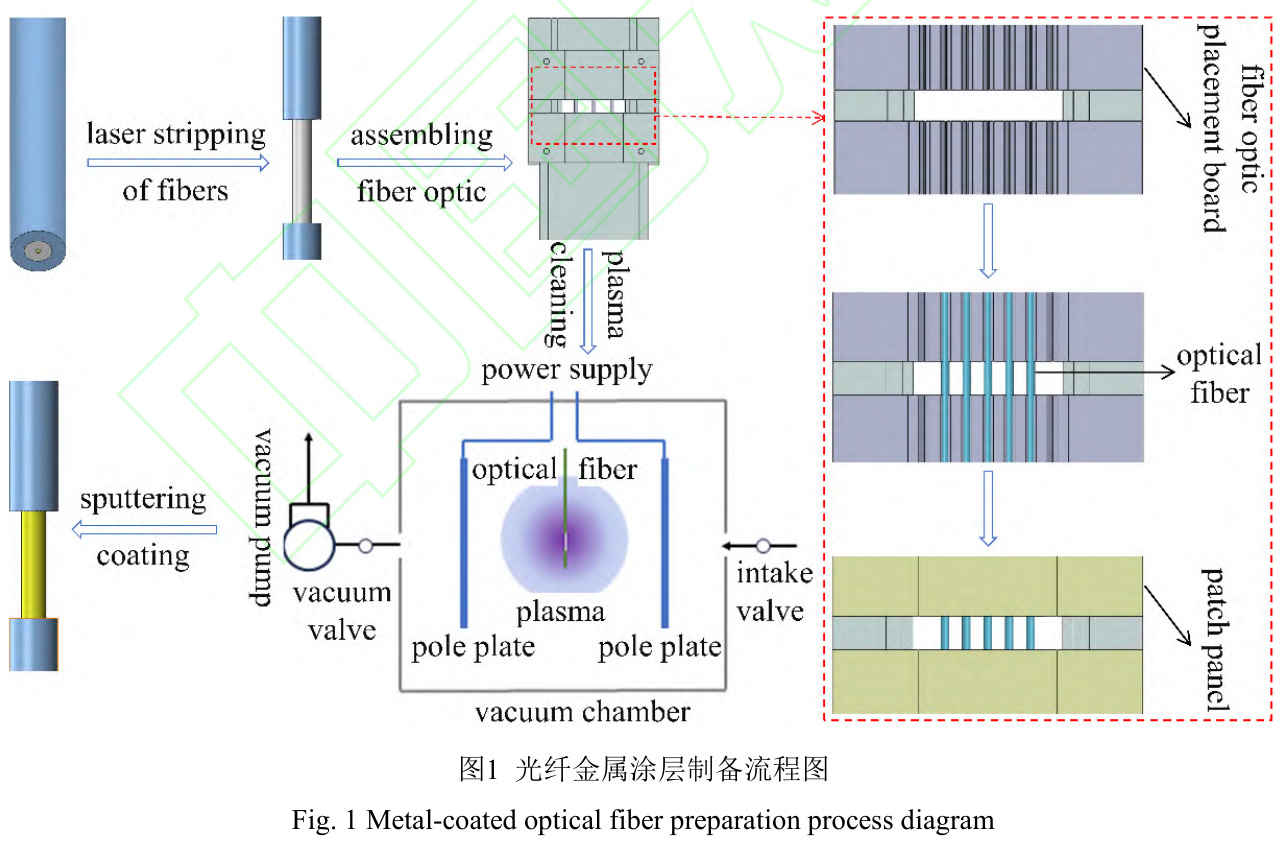
2.22去涂覆层
市售的光纤通常采用丙烯酸酯或聚酰亚胺等聚合物作为涂覆层。在制备金属涂层时,需先将聚合物涂覆层去除一段,以暴露出光纤的裸露段供金属化处理。目前,去除聚合物涂覆层的主流方法包括化学剥离法、机械剥离法和激光剥离法。然而,这些方法各有其局限性。
机械剥离法由于与光纤存在直接物理接触,极易对纤芯造成损伤。化学剥离法则可能在光纤表面残留剥离剂,不仅需要进行繁琐的后续清洗过程,还可能在剥离剂使用不当或剥离过程控制不当时,对光纤的表面质量和性能产生负面影响,如引入表面缺陷或降低光纤强度[14]。
相对而言,激光剥离法采用非接触式加工方式,既无机械应力也无切痕,对纤芯无损伤。因此,我们选用LMT-C30F2型号激光剥纤机进行光纤去涂覆层操作,以确保光纤的完整性和性能稳定。
2.33装配光纤
在磁控溅射镀膜过程中,为确保样品的稳定放置,我们针对特定需求设计了一款专用的光纤夹具。这款夹具采用非挤压式设计,旨在最大程度上避免在装配过程中对光纤造成任何形式的物理损伤,确保光纤的完整性和性能稳定。通过精心设计的夹具结构,我们成功地实现了对光纤的稳固固定,同时保障了其安全无损,为磁控溅射镀膜过程的顺利进行提供了有力支持。
2.44等离子清洗
经过批量激光剥除涂覆层处理的光纤,为避免裸光纤段表面残留微量聚合物,以及在后续操作与保存过程中可能吸附的灰尘或其他杂质,我们需对光纤进行严格的清洗。传统的清洗方法主要分为湿法和干法两大类。湿法清洗通常涉及液体媒介,包括蒸汽、溶液浸泡以及旋转喷淋等方式,然而这些方法均涉及化学处理,这与我们研究的初衷相悖。另一方面,干法清洗则通过压力、抽吸或气体媒介等手段去除污染物,包括机械清洗、超声波清洗和等离子清洗等方法[20]。其中,机械清洗虽可行,但效率较低且成本较高,还可能对光纤造成损伤;超声波清洗虽有效,但需配合溶液使用,同样不符合我们的研究需求。综合考虑,等离子清洗方法最为符合我们的清洗要求,其能够在不引入化学物质的情况下有效去除光纤表面的残留物和污染物。我们采用CPC-A等离子清洗机,等离子清洗机由真空腔室、抽真空泵、控制系统三部分组成,通过抽真空泵将真空腔室抽至50Pa,随后通入氩气,待气压稳定至60Pa后开始进行等离子清洗,等离子溅射功率15W,清洗时间3min。
2.55磁控溅射镀膜
使用MS560B1型镀膜设备,该设备由腔室、真空系统、电源系统、循环水冷系统以及控制系统组成,在真空腔室内部,靶材位和样品架均设有精确定位,以确保镀膜过程的准确性和稳定性。真空系统由机械泵和分子泵组成,实现了高效的两级抽真空机制。在镀膜流程中,首先利用机械泵将系统抽至较低真空,随后分子泵将系统抽至所需的高真空水平,通常在10-4Pa数量级。接着,通入氩气等工作气体,当气压稳定至预设水平后,通过控制系统启动射频电源,并精确调节溅射功率,以开始溅射镀膜过程。
试验所用靶材分别为:纯金属Cr靶、Al靶、Ti靶、Ni靶,靶材纯度均为99.99%,尺寸统一为Φ50mm×3mm。试验所用光纤直径约245μm,裸纤直径约125μm。光纤经去涂覆层处理、装配夹具和等离子清洗后,将装有光纤的夹具安放于样品架,随后进入磁控溅射镀膜流程。在正式沉积金属涂层前,系统需抽真空至2×10-4Pa以确保良好的镀膜环境,通入气体为纯度为99.999%的氩气,并采用室温沉积方式。此外溅射功率、溅射气压和沉积时间为试验变量,以探究它们对薄膜质量和光纤抗拉性能的影响。
2.66微观表征及力学性能测试
采用型号为FESEMSU8000的扫描电子显微镜观察光纤的金属涂层观察的微观形貌。
通过紫外线固化胶水将光纤两端粘在两铁片平面上,采用使用JX-240单芯光纤热剥钳剥除光纤两端非金属化段涂覆层获得两段裸光纤,将裸光纤段放置于两铁片平面上,使用点胶机将紫外线固化胶水打在位于铁片上裸光纤上,使用omnicures1500UV设备将胶水固化,最后使用ZQ-990A型号万能试验机测试光纤的抗拉强度。测试拉伸速度设置为1.5mm/min,由于镀层为纳米级,光纤拉断的截面面积统一为裸光纤截面积0.0123mm2。
3、结果与讨论
3.1预处理对光纤拉力的影响
预处理阶段涵盖了激光剥纤、光纤装配以及等离子清洗等多个关键步骤。为了准确评估磁控溅射工艺对光纤抗拉强度的影响,并排除预处理可能产生的干扰,本研究首先对原始光纤(仅进行了激光剥纤)和预处理后(不包括磁控溅射镀膜过程)光纤的抗拉强度进行了测试。在光纤拉力测试过程中,随着拉力荷载逐步增加,光纤最终只会呈现两种失效模式:拉断或拉脱。拉断模式表现为光纤在裸光纤段(需预处理并后续进行金属化的区域)或粘胶段(光纤与固化胶的粘接部位)发生断裂;拉脱模式则表现为光纤在拉力作用下脱胶而未断裂。光纤若发生拉脱,即认为该金属化光纤的抗拉强度已经达到标准。因为拉力加大至光纤拉脱时,光纤主体仍保持完整,未发生断裂,这说明其断裂拉力要高于脱胶拉力。若光纤在拉脱荷载下未发生拉脱,则测试拉力将继续增大直至光纤正常拉断。因此,拉脱样品的抗拉强度实际要高于测试值。此外,拉脱样品的拉力测试值基本大于拉断样品。基于以上测试标准及实验结果,我们将拉脱样品称为达标样品,通过对比原始光纤与预处理光纤的达标率以及断裂于裸光纤段的拉力值,可以评估预处理工艺对光纤抗拉强度的影响。如图2所示,我们分别对原始光纤和预处理后的光纤进行了16组系统的拉力测试,并详细记录了光纤在测试过程中断裂的模式及具体位置。图2(b)和(c)展示了光纤的断裂模式和位置,原始光纤与预处理光纤的达标率存在一定差异。图2(a)进一步对断裂于裸光纤段的样品的抗拉强度进行对比分析,结果显示,原始光纤与预处理光纤的断裂拉力平均值无显著差异。综合分析上述实验结果,我们可以得出结论:预处理过程对光纤的抗拉强度并未产生显著影响。
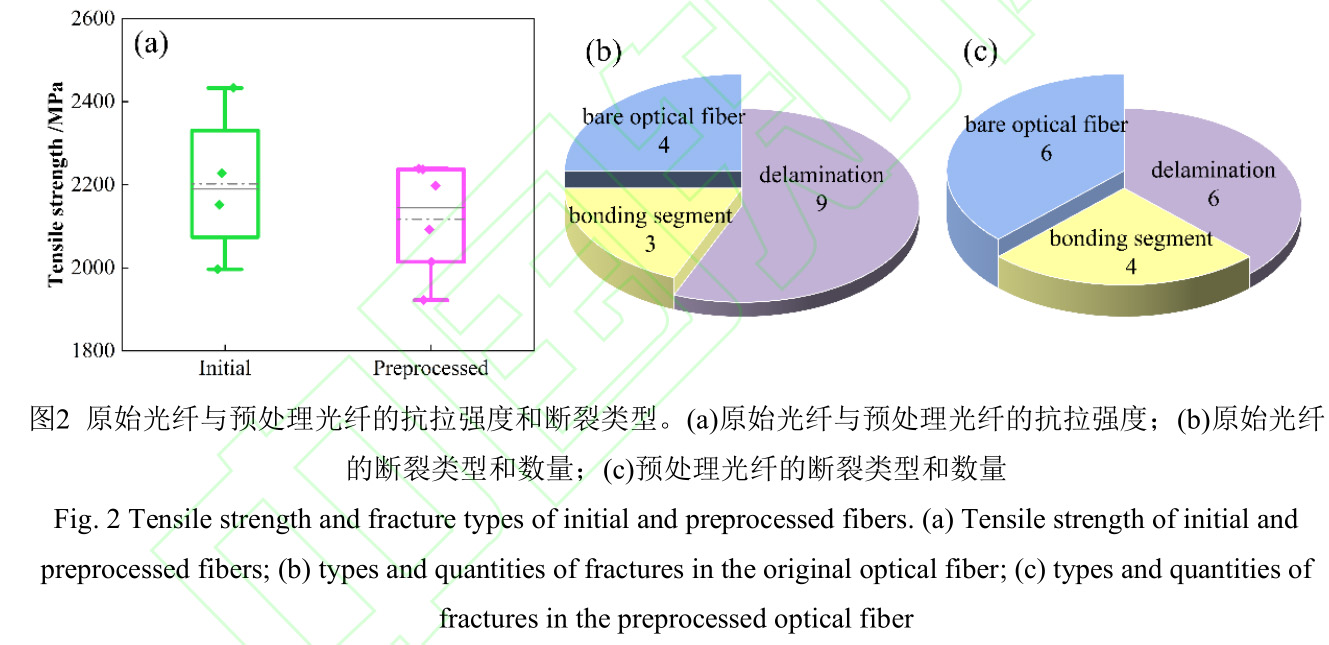
3.2磁控溅射对金属涂层光纤拉力的影响
磁控溅射沉积薄膜的原理是通过电子在电场的作用下加速飞向基片,在这个机制中与氩原子发生碰撞,导致大量的氩离子和电子的电离释放。电子持续与氩原子碰撞,进一步释放更多的氩离子和电子。随后,这些氩离子受电场的作用加速并轰击靶材,溅射出大量的靶材原子。这些中性的靶原子(或分子)沉积在基片上,形成薄膜。溅射过程即为入射离子通过一系列碰撞进行能量和动量交换的过程,在磁控溅射沉积金属涂层的过程中,不同的工艺参数会直接改变氩离子以及靶原子的动量,导致靶原子到达光纤表面的能量不同,进而影响金属涂层光纤的抗拉强度。
1)溅射功率对金属化光纤拉力的影响
图3(a)展示了四组不同溅射功率制备的Cr金属涂层光纤的抗拉强度箱线图,每组包含4个数据点。附图所示为抗拉强度平均线最近点的时间-拉力曲线,图中可见曲线在某一点拉力瞬间下降,这是由于光纤在此刻发生了断裂。此断裂现象直接导致了拉力的急剧降低,这一突变明确表明了光纤的机械强度已经达到了其极限,无法继续承受更大的拉力。从图3(a)中可以观察到,在30W溅射功率下制备的金属涂层光纤表现出最高的抗拉强度,平均抗拉强度为575.29MPa。随着溅射功率的增加,金属涂层光纤的抗拉强度呈现下降趋势。值得注意的是,由于30W溅射功率是氩气电离起辉的最小功率,因此无法探究更低功率下制备的金属涂层光纤抗拉强度。溅射功率的增加会提高溅射过程中离子的能量和动量,从而增加离子轰击靶材表面的能量。这使得靶材原子具有更高的初始动能,增加了靶材原子接触裸光纤表面的能量,从而对光纤造成一定的损伤。
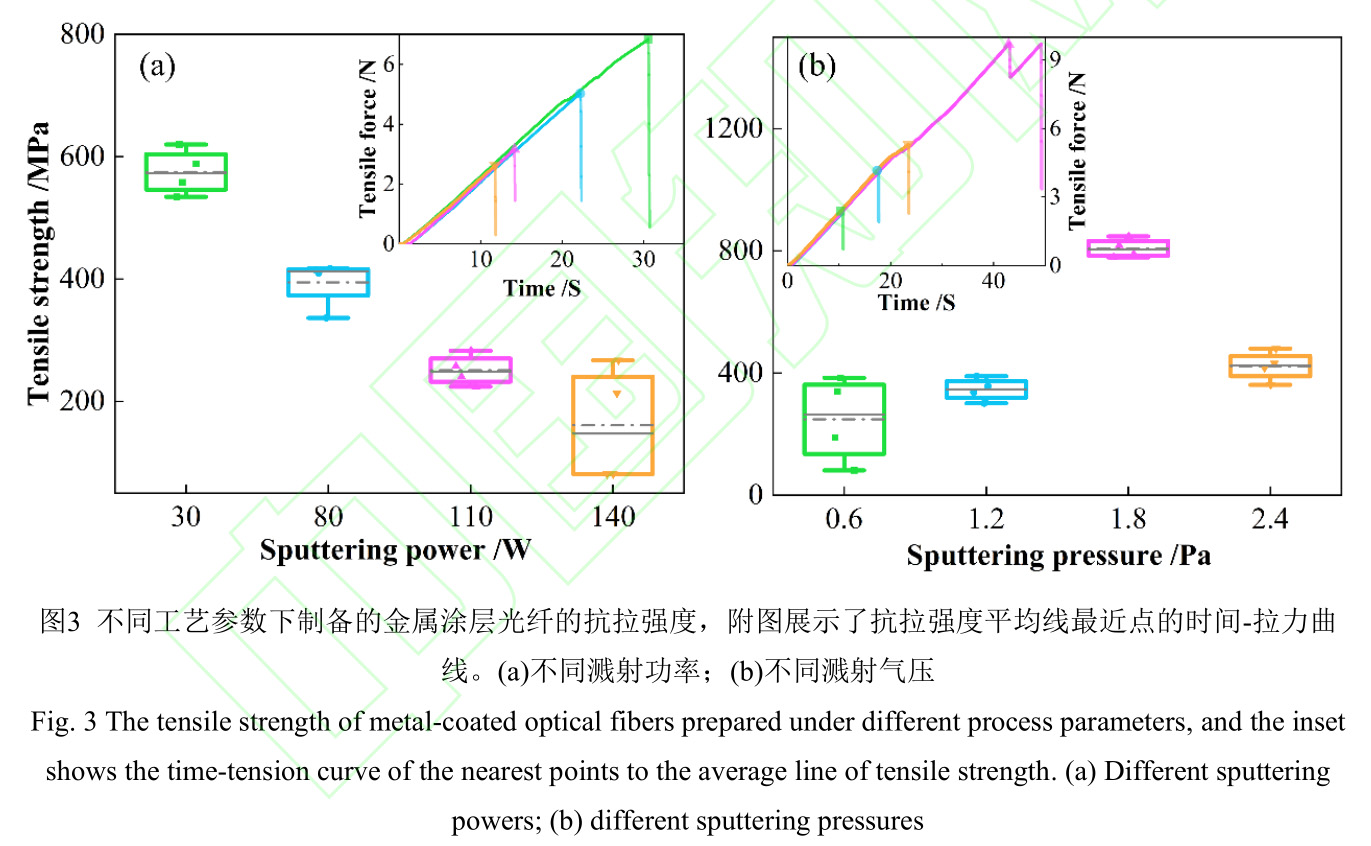
2)溅射气压对金属涂层光纤拉力的影响
在进行了溅射功率对Cr金属涂层光纤抗拉强度的实验后,由于30W功率时氩气电离不稳定,后续试验均选择了80W。图3(b)展示了四组不同溅射气压制备的Cr金属涂层光纤的抗拉强度箱线图,每组包含4个数据点。在附图中所展示的,于1.8Pa条件下所制备的金属涂层光纤的时间-拉力曲线,在高拉力段呈现出明显的波动特征。这可能是由于紫外线固化胶存在一定的塑性形变或光纤在固化胶中出现微量滑移导致的。当荷载拉力增大至一定值,固化胶可能会沿受力方向变形,拉力值在短时间内有所降低。当塑性形变逐渐饱和,荷载拉力会逐渐增大,光纤可能会被拉断(如图3(b)中1.8Pa样品所示)。其次,微量形变了的固化胶也有可能继续产生新的形变,拉力时间曲线表现为重复抖动。在高荷载拉力的情况下,光纤也有可能在微观上挣脱固化胶的形变束缚,在固化胶内产生微量的滑移,在拉力时间曲线上表现为高拉力段的波动,幅度或大或小。另外,形变和滑移状态也可能与点胶方式及胶体与裸纤接触面积相关(人工误差)。从图3(b)可以观察到,在0.6Pa到1.8Pa范围内,金属涂层光纤的抗拉强度与溅射气压呈正相关关系,因为随着溅射气压的逐步增加,气体分子的平均自由程逐渐缩短。溅射气压的上升显著提高了靶材原子在飞行至基体过程中与气体分子碰撞的概率。这种碰撞导致靶材原子的能量损失,从而减弱了它们对光纤基体的作用效果。在溅射过程中,气压增加会导致更频繁的气体分子与溅射出来的Cr原子之间的碰撞,从而减小了Cr原子到达光纤表面的能量。在1.8Pa下金属涂层光纤的平均抗拉强度达到了808.34MPa,然而当溅射气压提升至1.8Pa至2.4Pa之间的某个特定临界值时,更多的氩原子在溅射过程中被电离成氩离子和二次电子。氩离子以更高的能量飞向靶材,有效溅射出靶材原子。同时,这些二次电子在飞向基片的过程中,由于磁场的作用,被限制在辉光区域内运动。这些电子与靶材原子的碰撞不会降低靶材原子的能量,反而会增加。当由二次电子贡献的能量增量超过气体分子碰撞带来的能量减小时,靶材原子的能量会增强。这种增加的能量加剧了靶材原子对光纤基体的损伤对光纤基体的质量和性能产生更显著的影响。
3)沉积时间对金属涂层光纤拉力的影响
在确定了磁控溅射功率和气压后,对沉积时间和金属涂层厚度对金属涂层光纤拉力的影响进行了研究,图4为三组不同沉积时间制备的Cr金属涂层光纤的抗拉强度箱线图,每组包含4个数据点,附图展示了每个样品抗拉测试的时间-拉力曲线。可以看出金属涂层光纤的抗拉强度与沉积时间成反比,在沉积时间为5min时其平均抗拉强度达到1006.35MPa。首先,较短的沉积时间可能导致金属涂层光纤的金属层较薄,这可能导致拉伸时的应力分布更加均匀,从而使得金属涂层光纤的抗拉强度相对较高。而较长的沉积时间可能导致金属层较厚,应力分布可能更不均匀,可能出现局部应力集中现象,从而降低了金属涂层光纤的抗拉强度。其次,在磁控溅射过程中,金属原子在沉积到光纤表面时可能带有一定的动能,这会在涂覆层内部产生内应力。随着沉积时间的增加,内应力可能逐渐积累,导致涂覆层在受到外力时更容易发生破坏。
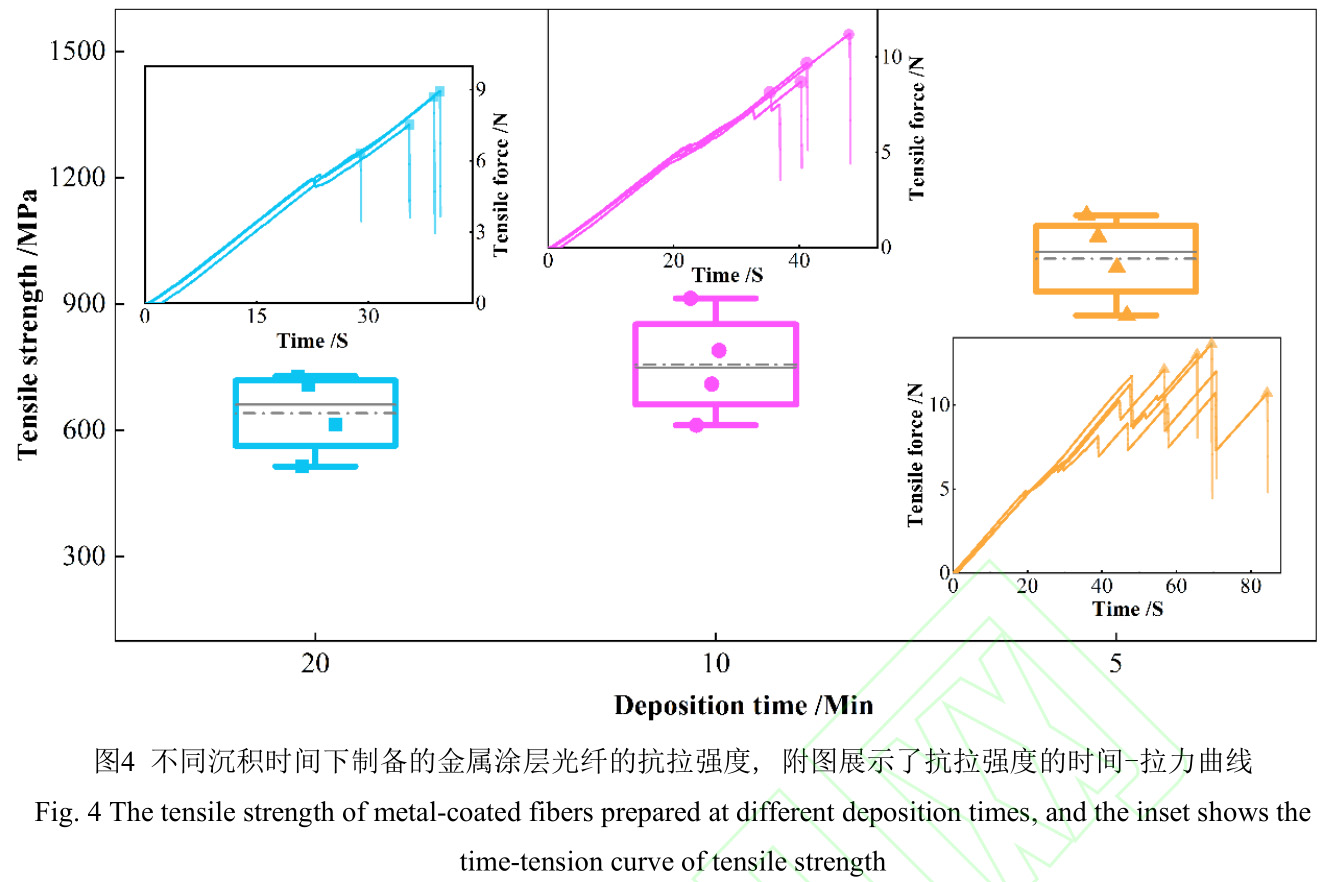
3.3金属涂层的微观形貌
图5为5min沉积时间的Cr金属涂层光纤的微观表征。由图5(a)和(b)可以观察到,Cr金属镀层表面光滑平整,看不到明显晶粒或裂纹,证明了在此磁控溅射工艺下Cr金属涂层的形成是均匀且致密的,且表面质量良好。图5(c)为Cr金属涂层光纤的截面图,可以观察到Cr金属镀层与石英光纤结合紧密,镀层厚度为纳米级。
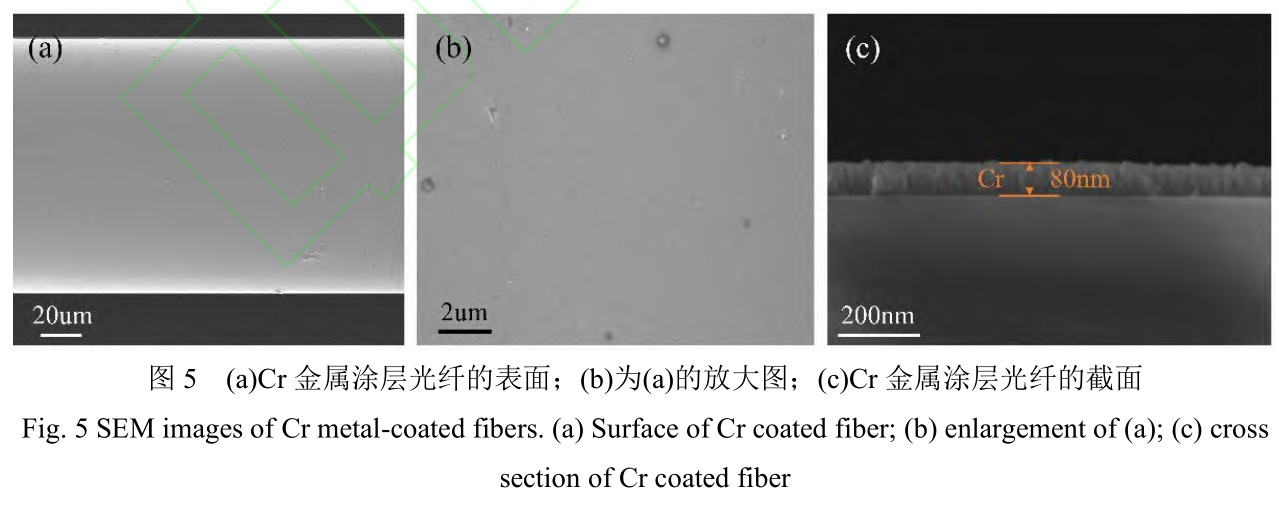
3.4不同金属涂层对光纤拉力的影响
在研究磁控溅射工艺对金属涂层光纤拉力的影响后,我们通过相同的制备工艺,通过磁控溅射用4种金属靶材制备了4种金属涂层光纤,探究不同金属材料对金属涂层光纤拉力的影响。图6(a)展示了这4组金属涂层光纤的抗拉强度箱线图,其中Al涂层光纤的抗拉强度最高,平均抗拉强度达到1174.21MPa,而Ti、Ni的平均抗拉强度都在770MPa左右。当两种材料的弹性模量相近时,它们之间的应力传递会更加均匀,减少了因材料性质差异导致的应力集中现象。表1列出了SiO2和几种金属的弹性模量,其中Al和SiO2的弹性模量最为接近,将Al作为涂覆层沉积在石英光纤上时,应力在界面上的传递会更加连续和平稳,减少了由于材料之间的不匹配导致的应力集中,其他金属的弹性模量都相对较高,在拉伸时容易导致应力集中,光纤更易断裂。针对Al涂层金属化光纤,我们做了进一步的研究,如图6(b)所示,我们分析了不同沉积时间下Al涂层金属化光纤的抗拉强度性能。结果表明,随着沉积时间的增加,Al金属化光纤的抗拉强度逐渐减小,这与其他金属的演变规律相同。但相比于其他金属,Al涂层所表现出的抗拉强度依然具有明显的优势。这进一步证实了Al涂层确实可以有效地提高金属化光纤的抗拉强度。
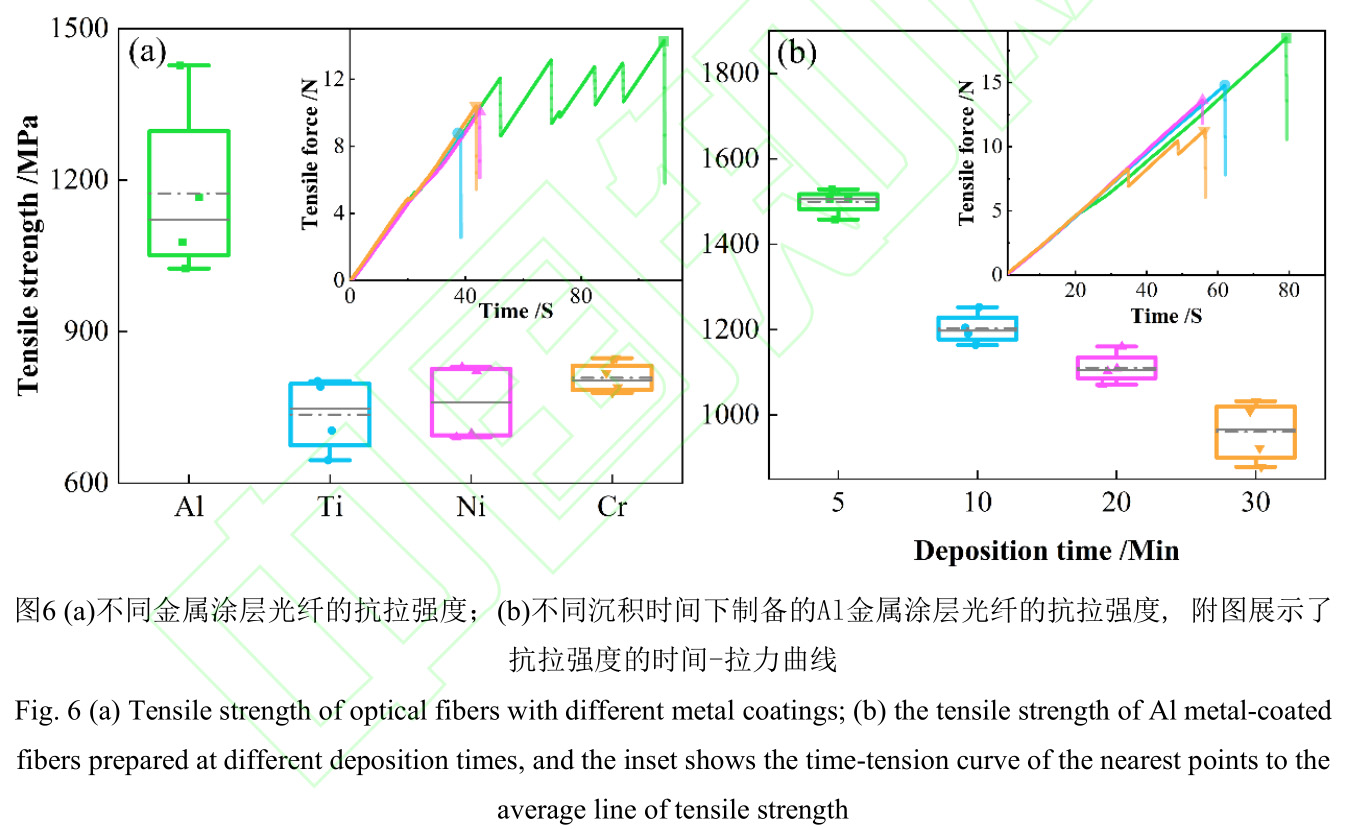

3.4结论
经过系统研究,我们发现磁控溅射工艺中的参数设定与金属材料的选用对金属涂层光纤的抗拉强度与性能具有显著影响。实验结果表明,激光剥纤、光纤装配以及等离子清洗的预处理对光纤抗拉强度的影响并不显著。而在磁控溅射过程中,溅射功率、溅射气压以及沉积时间均成为影响抗拉强度的关键因素。具体而言,当溅射功率越低时,所制备的金属涂层光纤展现出最高的抗拉强度,随着功率的增加,抗拉强度逐渐降低。此外,溅射气压与抗拉强度呈正相关关系,但过高的气压将导致抗拉强度下降。沉积时间同样对抗拉强度有显著影响,较短的沉积时间可能提高抗拉强度,而长时间沉积则可能导致强度降低。最后,不同金属材料对光纤抗拉强度的影响也有所不同,其中Al涂层光纤展现出最高的抗拉强度。这些结论为优化金属化光纤的磁控溅射工艺提供了重要依据。
参考文献
[1] 庄园, 周次明, 范典. 光纤金属涂覆方法研究综述[J]. 激光与光电子学进展, 2022, 59(5):0500002.
Zhuang Y, Zhou C M, Fan D. Review of Metal-Coated Methods for Optical Fiber[J]. Laser & Optoelectronics Progress, 2022, 59(5): 0500002.
[2] Albert J, Liu F, Marquez-Cruz V. Hypersensitivity and applications of cladding modes of optical fibers coated with nanoscale metal layers[J]. Sensors, 2018, 18(5): 1518.
[3] 黄博, 汪正坤, 朱永, 等. 双金属锥形光纤表面增强拉曼散射探针拉曼增强特性[J]. 光学学报, 2023, 43(21): 2106003.
Huang B, Wang Z K, Zhu Y, et al. Raman Enhancement Characteristics of Bimetallic Tapered Optical Fiber Surface-Enhanced Raman Scattering Probe[J]. Acta Optica Sinica, 2023, 43(21):2106003.
[4] 张飞翔,钟良,廖宴平.光纤 Bragg 光栅表面化学镀铜工艺及特性研究[J].现代化工,2014,34(07):96-99.
Zhang F X, Zhong L, Liao Y P, et al. Electroless copper plating process for fiber bragg grating and its characteristics[J]. Modern Chemical Industry, 2014, 34(07): 96-99.
[5] 饶春芳, 张华, 冯艳, 等. 光纤布拉格光栅金属化保护中的应力[J]. 激光与光电子学进展, 2012, 49(6): 060601.
Rao C F, Zhang H, Feng Y, et al. Stress in Metal Coating Fiber Bragg Grating[J]. Laser & Optoelectronics Progress, 2012, 49(6): 060601.
[6] Li C , Liu M , Song H ,et al. Study of temperature sensing performance of bimetallic layer MFBG[J]. Sensors and Actuators, A. Physical, 2023:359.
[7] 姚 文 历 , 管 从 胜 , 王 静 , 等 . 光 纤 光 栅 金 属 化 工 艺 及 特 性 研 究 [J]. 光 电 技 术 应用,2012,27(06):46-50+54.
Yao W L, Guan C S, Wang J, et al. Research on Surface Metallization of Optical Fiber Grating and Characteristic[J]. Electro-Optic Technology Application,2012,27(06):46-50+54.
[8] Rostami A, Soleimani H, Samavati Z, et al. Real-time monitoring of urea slow release through fiber Bragg grating sensors[J]. Measurement, 2023, 221: 113464.
[9] Wang Y L , Tu Y , Tu S T .Development of Highly-Sensitive and Reliable Fiber Bragg Grating Temperature Sensors with Gradient Metallic Coatings for Cryogenic Temperature Applications[J].IEEE Sensors Journal, 2020, PP(99):1-1.
[10] 曾丽珍, 欧泽涛, 杨宏艳, 等. 石墨烯-金属纳米线阵列增敏等离子体光纤传感器[J]. 光学学报, 2022, 42(19): 1906002.
Zeng L Z, Ou Z T, Yang H Y, et al. Sensitivity Improvement of Plasmonic Optical Fiber Sensors with Graphene-Metal Nanowire Array[J]. Acta Optica Sinica, 2022, 42(19): 1906002.
[11] 陈思, 武京治, 王艳红, 吴倩楠. 基于 Au-TiO2 涂层凹槽的 D 形光子晶体光纤的等离激元红外传感器设计[J]. 激光与光电子学进展, 2023, 60(7): 0706006.
Chen S, Wu J Z, Wang Y H, et al. Design of Plasmonic Infrared Sensor Based on D-Shaped Photonic Crystal Fiber with Au-TiO2 Coating Grooves[J]. Laser & Optoelectronics Progress,2023, 60(7): 0706006.
[12] 朱月红, 文继华 . 光纤光栅表面化学镀镍及影响镀层性能的因素[J]. 表面技术, 2018,47(7): 241-245.
Zhu Y H, Wen J H. Electroless nickel plating of fiber Bragg gratings and influence factors of coating properties[J]. Surface Technology, 2018, 47(7): 241-245.
[13] Miller M N. Selective fiber metallization: US6355301[P]. 2002-03-12.
[14] 宋启良,胡振峰,梁秀兵,等.无损石英光纤表面 Ni-P 镀层的制备及性能[J].中国表面工程,2019,32(06):90-97.
Song Q L, Hu Z F, Liang X B, et al. Preparation and Properties of Ni-P Coating on Quartz Fiber Surface[J]. China Surface Engineering,2019,32(06):90-97.
[15] 赵劲凯,汪洪,贾金升等.涂覆温度对镀锌石英光纤在线制备及抗拉性能的影响[J].硅酸盐通报,2023,42(08):2976-2984.
Zhao J K, Wang H, Jia J S, et al. Research Progress on Preparation Method and Property of Metal Coated Optical Fibers[J]. Bulletin of the Chinese Ceramic Society, 2023,42(08):2976-2984.
[16] 杨珂,李玉龙,李学文.镀镍光纤抗拉强度及其影响因素[J].激光与红外,2018,48(06):769-774.
Yang K, Li Y L, Li X W. Tensile strength and its influencing factors of the Ni-coated optic fiber[J]. Laser and Infrared, 2018,48(06):769-774.
[17] Inada K, Shiota T. Metal coated fibers[C]. Optical fiber characteristics and standards. SPIE,1986, 584: 99-106.
[18] Abermann R. Measurements of the intrinsic stress in thin metal films[J]. Vacuum, 1990, 41(4-6): 1279-1282.
[19] 刘明智,梁康,熊巍,等.沉积参数对磁控溅射镀金膜膜层残余应力与微观形貌的影响[J].导航与控制,2020,19(06):98-104+73.
Liu M Z, Liang K, Xiong W, et al. Effect of De position Parameters on Residual Stress and Microstructure in Magnetron Sputtering Au Thin Films[J]. Navigation and Control,2020,19(06):98-104+73.
[20] 周 彤 , 李 鹏 , 曹 宏 利 , 等 . 某 石 英 器 件 内 部 封 闭 孔 道 的 等 离 子 清 洗 技 术 [J]. 真空,2023,60(05):51-54.
Zhou T, Li P, Cao H L, et al. Plasma Cleaning Technology of Closed Channel Inside a Quartz Device[J]. Vacuum, 2023,60(05):51-54.
相关链接