引 言
磁控溅射是一种先进的薄膜制备方法,具有溅射速率高、成膜均匀性好、薄膜厚度可控、与基片结合力较强、无污染等优点 [1-5 ] 。溅射靶材是磁控溅射制备薄膜的关键原材料,其质量是决定薄膜性能的主要因素之一。近年来,随着镀膜技术突飞猛进的发展,溅射靶材市场规模急剧扩张。根据恒州博智电子及半导体研究中心公布的《 2021-2027 全球与中国溅射靶材市场现状及未来发展趋势》统计数据,2020 年全球溅射靶材市场规模达到了 248 亿元,预计 2027 年将达到 416 亿元,年复合增长率为 7.7% 。
溅射靶材的主要应用领域为半导体、平面显示、记录媒体和太阳能薄膜电池,其中半导体领域的芯片产业是对靶材技术要求最高的产业之一,该领域靶材制造技术主要由日本、美国和德国 3 国控制。日本的日矿金属、东曹以及美国的霍尼韦尔、普莱克斯是国际上制造靶材的 4 大巨头,占据了全球半导体芯片用靶材约 90% 的市场份额。我国靶材市场起步
较晚,但技术进步较快,特别是近年来面对高端芯片需要全面进口的现状,在国家一系列政策支持下国内龙头企业开发出了一批能适应高端领域应用的靶材。目前,我国与掌握靶材制备先进技术国家的差距主要集中在靶材上游超高纯原材料制备和靶材产品更新换代 2 个方面。
贵金属(金、银、铂、钯、铑、铱、钌、锇)具有优异的物理和化学性能,用其制造的靶材广泛应用于半导体和信息记录媒体领域的高性能薄膜制备中;贵金属溅射靶材的特性直接关系到薄膜质量以及溅射镀膜的成本,是溅射薄膜生产厂商关注的重点。但是,由于贵金属资源有限、价格昂贵、回收难度大,其应用受到很大局限。贵金属靶材包括纯金属靶材和合金靶材 2 种,形状有圆形、矩形和异型(如三角形、碗状等),还有实心和空心(即旋转靶材)等类型。按结构形式,贵金属靶材可分为单体和复合靶材 2 种。
复合型靶材通常使用机械连接、钎焊、胶黏接、扩散焊、电子束焊和爆炸焊等 [6 ] 方法将靶材与背板连接形成。在实际应用中,应根据需求选择不同形状不同类别的靶材、背板及连接方式。
随着半导体及信息记录媒体向高密度化、小型化和低成本化发展,贵金属靶材的需求量越来越大。为了给广大研究人员、生产厂商提供参考,作者从制备工艺、技术要求、应用领域等方面对贵金属靶材的研究进展进行综述,并对未来研究方向进行了展望。
1、制备工艺
贵金属靶材的制备工艺主要包括熔炼 + 热机械处理法和粉末冶金法。金、银、铂及其合金靶材主要采用熔炼 + 热机械处理法制备,而难熔贵金属钌及其合金或者熔点和密度相差很大的 2 种或 2 种以上贵金属复合的靶材,由于采用普通熔炼法难以使成分均匀,一般采用粉末冶金方法制备 [7 ] 。
1.1 熔炼 + 热机械处理法
熔炼 + 热机械处理法是常用的贵金属靶材制备方法,其基本工艺流程为熔炼铸造靶坯 → 热机械处理 → 机加工 → 表面处理。熔炼主要包括电弧熔炼、感应熔炼等方法。用熔炼方法制备的靶材杂质含量(特别是气体杂质含量)较低,致密化程度高,尺寸大。为降低铸锭中杂质元素含量特别是氧含量,冶炼和浇铸需在真空或保护性气氛下进行,并选用由还原性材料制造的坩埚、内浇道和铸模 [8 ] 。但是,过高的真空度会导致熔融状态的贵金属过度挥发,增加贵金属的损耗;考虑到贵金属的高成本,应当对熔炼时的真空度进行适度控制,以减少熔炼损耗。热机械处理法通常指轧制、锻造等塑性加工 + 热处理的方法,其主要作用是调整靶材微观结构,目的是获得细小均匀的等轴晶组织。
1.2 粉末冶金法
粉末冶金法制备靶材的基本工艺流程为混粉 →烧结成形 → 机加工,其中烧结成形方法包括热压烧结、真空热压烧结、热等静压烧结和放电等离子体烧结等;该方法无需将原料粉末加热到完全熔化,所以烧结温度远低于金属熔点。在采用粉末冶金法制备贵金属靶材时,要求选用高纯、超细的贵金属粉末,并通过物理混合方法充分均匀混合,并选择能实现快速致密化的烧结成形技术,以保证靶材的低孔隙率并控制晶粒度,同时还需严格控制杂质元素含量 [5 , 9-10 ] 。粉末冶金法的优点是容易获得均匀细晶结构、节约原材料、生产效率高等,缺点是工艺不当容易造成靶材孔隙率较高。以粉末冶金制备钌靶材为例,当原料钌粉的平均粒径在 50μ m 以下,且为等轴晶粒时,采用球磨混粉 + 真空热压烧结方法,可以获得相对密度较高的钌靶材 [11 ] 。
一些贵金属靶材可采用以上 2 种制备工艺进行生产,在实际生产中应根据靶材性能、制造成本等要求选择合适的制备工艺。
2、技术要求
溅射薄膜的质量与靶材显微组织及其均匀性、缺陷率和纯度等内在品质息息相关。通过控制靶材品质以提高靶材质量、设计靶材的外形尺寸以与溅射机台的规格相匹配、改善溅射参数等方法即可获得性能优异的薄膜 [12-13 ] 。贵金属靶材的技术指标主要包括纯度、晶粒尺寸及晶面取向、磁透率、致密性能、焊接性能和表面质量等。
2.1 纯 度
不同领域对不同类型贵金属靶材的纯度要求各不相同。总体而言,靶材纯度越高(杂质元素总含量越低),溅射薄膜性能越好 [14 ] 。杂质的存在会造成金属靶材在溅射过程中的异常放电,降低元器件性能。另外杂质元素的存在容易使靶材内部产生夹杂物,当夹杂物数量较多时,靶材在溅射过程中易在晶圆上形成微粒,导致互连线路异常,严重影响溅射薄膜的性能。典型的危害主要包括:碱金属元素如锂、钠、钾等易在绝缘层形成可移动离子,降低元器件绝缘性能 [10 ] ;放射性元素如铀、钍等因释放射线会造成半导体器件软击穿 [10 ] ;过渡性金属元素如铁、镍、铬等离子会导致界面漏电,增加氧元素含量 [10 ] ;气体元素如氧、氮等不利于薄膜的稳定,会造成薄膜电阻增大 [15 ] 。因此,在靶材制备过程中应控制杂质元素的种类和含量 [8 ] 。贵金属靶材的纯度一般要求达到 4N ( 99.99% )以上。
半导体行业的发展主要体现在两个方面:一是芯片的特征尺寸不断缩小,从微米级逐步缩减至纳米级,目前已达到 7nm ;二是晶圆直径不断增大,目前逐步向 450mm 发展[ 12 , 16 ] 。不断增大的晶圆面积和细小的芯片特征尺寸对溅射薄膜的均匀性提出了更高的要求,这就要求靶材具有更高的纯度。目前,半导体芯片行业用贵金属靶材的纯度要求在 5N( 99.999% )甚至 6N ( 99.9999% )以上 [14 ] ,并且氧元素质量分数通常要求小于 200×10-6 。
2.2 晶粒尺寸及晶面取向
一般而言,靶材的晶粒尺寸在微米量级到毫米量级范围内;贵金属靶材的晶粒尺寸通常需要控制在 100μ m 以下。细小晶粒靶材的溅射速率比粗晶粒靶材快,晶粒尺寸均匀的靶材沉积的薄膜厚度偏差较小,即晶粒越细小越均匀,其溅射薄膜质量越好。同一成分的靶材在不同晶面上的溅射速率会有所差异,通常原子会倾向于沿着最紧密排列方向优先溅射 [
15 , 17 ] 。在溅射过程中,不同晶面溅射速率的差异会导致靶材表面粗糙度增加,使得靶材的后续溅射过程不稳定,最终影响薄膜的质量。因此,靶材表面的结晶取向应保持一致。钌靶材的最佳结晶面是( 112 )面、(002 )面和( 004 )面中的任意一面[ 18 ] 。
熔炼铸造的贵金属靶材主要通过热机械处理方法调整和控制其晶粒尺寸及晶面取向,通常采用的是施加变形量不小于 80% 的塑性加工 + 后续热处理工艺。而对于粉末冶金方法,则主要通过调整烧结工艺来实现对靶材显微组织的控制 [7 ] 。
2.3 磁透率
一些贵金属靶材有磁性,在溅射时容易使磁场分流,导致靶材起辉或难以维持放电以及薄膜厚度不均等问题,故要求靶材具有较高的磁透率。减小靶材厚度或在靶材上刻槽可以提高靶材磁透率,但会缩短其使用寿命并降低利用率。磁透率与磁导率呈反比关系,可以通过调整其加工工艺降低靶材的磁导率,从而提高靶材的磁透率 [19 ] 。镍含量较高的镍铂合金磁性较强,可通过调整轧制、锻造等塑性加工工艺,添加无磁性的金属元素,改变靶材外形设计(刻槽等)或在溅射时使工作温度高于其居里温度等 [20 ] 方法来提高其磁透率。此外,在靶材的使用过程中还可以通过采用强磁体使靶材表面获得需要溅射的磁场强度,从而达到提高磁透率的目的;但强磁体比较昂贵,并且需要对设备进行改动,成本较高。
综上可知,提高磁透率的方法很多,在应用时需要根据实际条件选择合适的方法。
2.4 致密性能
若贵金属靶材孔隙率较高、致密性较差,在溅射过程中会出现微粒飞溅和放电现象,影响溅射速率和溅射薄膜的性能。对于脆性合金靶材,当靶材内部气孔较多时,在搬运、摆放和使用过程中还容易发生碎裂。通常可通过改进制备工艺来提高靶材的致密性能:对于粉末冶金法,一般通过提高原料粉末纯度,并采用等离子烧结、微波烧结等快速致密化技术来降低靶材孔隙率 [21 ] ;对于熔炼 + 热机械处理法,可通过改进铸造工艺以减少冒口等缺陷来提高其致密性能。
2.5 焊接性能
当靶材的形状复杂、尺寸大或强度低、导电导热性差、难加工、原料成本昂贵时,可通过将靶材与背板进行连接以达到固定装夹、提高强度、提升导电导热性和节约成本的目的 [
3 ] 。贵金属中常用的背板材料为铜材料,常用的连接方法是钎焊。在实际应用时,需要考虑贵金属的性能及实际应用条件选取合适的背板材料及可靠的连接方法。脆性金属及合金
靶材需考虑其与背板间因物理性能差异大而产生变形甚至开裂的风险,因此应选择与靶材物理性能差异较小的背板材料进行焊接 [22 ] 。
为确认焊接的可靠性和有效性,防止在预溅射过程中脱靶带来的风险,钎焊连接后必须采用超声检验钎焊面积。作者在实际操作中发现,当靶材焊合率不低于 90% ,单个最大未焊合面积占比不超过5% 时,焊接质量合格。目前靶材厂家通常采用超声C 扫探伤系统进行疏松、分层、空洞、夹杂等缺陷和焊合效果的测试 [23 ] 。
2.6 表面质量
贵金属靶材对表面质量如表面平整度、加工精度、表面粗糙度等有较高要求。表面平整度及加工精度直接影响靶材的装配性能和溅射设备抽真空的效果,进而影响整个镀膜的溅射效率。靶材表面粗糙度较大时表面的尖端或凸起会发生尖端效应,导致电势大幅提高并击穿介质放电,表面粗糙度过大会造成溅射过程的不稳定。通常要求贵金属平面靶材的平整度小于 0.3mm ,表面粗糙度小于 2μ m ;半导体行业的要求更高,靶材的表面粗糙度需小于 0.5μ m 。
3、应用情况
对靶材需求量较大的领域包括半导体领域、信息储存领域和显示领域 [7 ] 。贵金属靶材主要应用在磁记录领域和半导体领域。表 1 列出了贵金属靶材的应用情况。
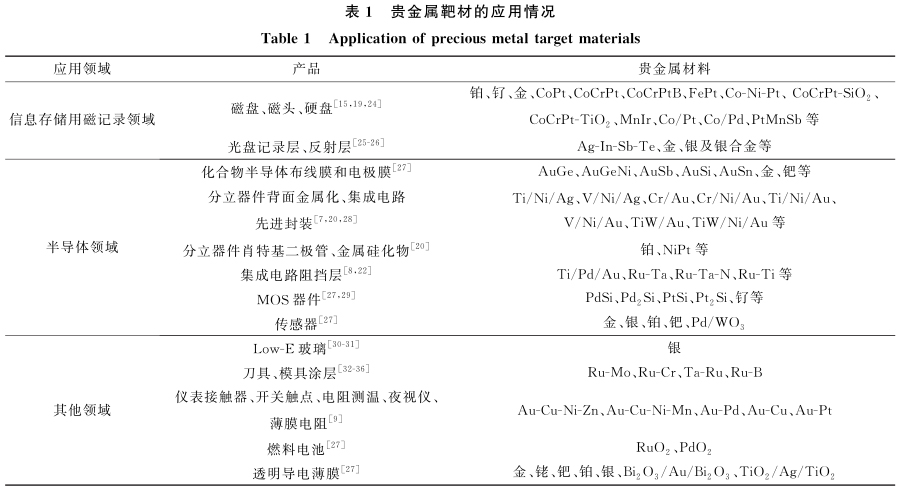
3.1 信息存储领域
随着电子信息技术的发展,信息存储和读取量与日俱增。以光盘为代表的光记录领域媒介的市场份额逐渐萎缩,以硬盘为代表的磁记录设备因具有高密度、高稳定性、低价格等优点而得到了广泛的应用。硬盘片为多层膜结构,从基底向上依次为籽晶层、底层、中间介质层、磁性层、中间层、磁性层、顶层和表层。其中,籽晶层、底层和磁性层都需要通过磁控溅射贵金属靶材制备得到。钌及铂合金、钯合金在硬盘中应用较多。 CoCrPt 合金具有良好的磁性和热稳定性,是磁记录层(其核心层为磁性层)常用的材料,其晶粒之间的磁交换耦合作用可降低磁记录介质的信噪比。在 CoCrPt 合金中添加 SiO 2 可以起到包覆或隔开 CoCrPt 铁磁颗粒的作用,获得细晶粒结构,该结构与垂直磁各向异性耦合的绝缘良好,可满足垂直磁记录磁介质叠层所需的低介质噪声和高热稳定性要求。 FePt 系合金、 CoPd ( Pt )系合金靶材也常用于溅射多层膜介质硬盘中的磁性层。钌在垂直磁记录镀层膜结构中也是不可或缺的材料,可作为底层用来控制晶粒尺寸,使沉积于其上的膜层获得高质量的织构。在中间介质层与单层CoCrPt 记录层之间加入钌底层,通过改变其层厚可调节 CoCrPt 记录层的矫顽力。此外钌层还可以减小上下层之间晶格失配应力,提高热稳定性,降低复式结构的剩磁面密度 [15 , 19 , 25-26 ] 。
3.2 半导体领域
靶材在半导体材料市场中占比仅约为 3% ,但是其质量的好坏直接影响整个半导体行业的进步。半导体可以分为集成电路、光电子器件、分立器件和传感器等 4 类产品,其中集成电路规模最大。金和银系靶材常用于制备集成电路先进封装中的凸点下金属化层,对于封装密度及效率有极大的提升作用,常 见 的 体 系 包 括 Ti / Ni /Ag、 Cr / Au 、 Cr / Ni / Au 、TiW / Au 、 TiW / Ni/ Au 等。由于性能稳定、导电导热性能好、电阻低以及焊接性能好,金和银材料也常用于分立器件背面金属化系统中的导电层。镍铂合金具有良好的高温稳定性,可作为势垒金属,通过调整铂含量可调整势垒的高低。铂含量的增加还可以改善界面形貌,减少侵占缺陷。镍铂硅化物常用于制备肖特基二极管势垒层以及超大规模集成电路微
电子器件中源、漏、栅极与金属电极间的接触。 NiPt合金是制备 65nm 节点以下低电阻和高热稳定性接触薄膜的最优选择。高熔点铂族金属及其合金能够与硅反应形成性能优异的硅化物,逐渐替代金、银等成为半导体常用的材料 [7 , 20 , 27-28 ] 。超大规模集成电路是集成电路发展的方向,其关键在于特征尺寸的减小和芯片面积的增大;铜凭借较低的电阻率和自扩散率以及较高的可靠性,成为了超大规模集成电路互连线产品的关键材料。目前,世界上几乎所有公司都在使用铜工艺(半导体行业中,铜用作互连材料的工艺)生产 130
nm 线宽逻辑器件。随着铜工艺中通孔横向尺寸和界面面积的缩小,铜互连采用的扩散阻挡层变得极薄,传统的钽扩散阻挡层的性能已不能满足要求;目前铜互连采用的阻挡层金属材
料主要为 Ru-Ta 、 Ru-Ta-N 和 Ru-Ti 等合金 [8 , 22 ] 。钌主要用作 PMOS 器件(指 n 型衬底、p 沟道,靠空穴的流动运送电流的 MOS 管)的栅电极材料 [29 ] 。
3.3 其他领域
3.3.1 低辐射玻璃行业
低辐射玻璃是指表面镀有多层金属或其他化合物的玻璃,具有高透光性和隔热性。银具有反射率高、消光系数低、热导率高、电阻率低、表面平滑作用好等优良性能,常用于低辐射玻璃的生产 [30-31 ] 。随着低辐射玻璃单片尺寸的增大,银靶材尺寸也越来越大,总长度可达 3000mm 以上,厚度也由原来的18mm 向 22mm 以上发展。随着靶材尺寸的增大,其组织均匀性难以保,制备难度变大。此外,靶材的长度或直径也会超过机加工设备可加工的最大量程。为解决此问题,可将靶材分解成 2 块或 2块以上进行加工,使用时再拼接成需要的大尺寸形状;单块靶材的长度可达 600mm 以上。
3.3.2 刀具模具行业
部分发达国家的不重磨刀具有 30%~50% 涂覆了耐磨涂层 [32-36 ] ,部分耐磨涂层采用TiC 、 TiN 靶材溅射制备。 Ru-Mo 、 Ru-Cr 、 Ta-Ru 等合金具有高硬度和良好的热稳定性,可用作硬质和超硬涂层材料应用在刀具、模具等表面防护领域。采用磁控溅射制备此类薄膜时可使用与合金相对应的单金属靶材进行双靶溅射,并通过热处理来提高薄膜的耐磨
性和硬度。此外,这类薄膜还可应用于玻璃成型模具(模具材料一般为 SiC 和 WC )上层,以提高模具力学性能、延长使用寿命。采用钌和硼金属靶进行双靶溅射制备的 Ru-B 合金涂层,也可用作刀具的超硬涂层。
3.3.3 其他行业
贵金属靶材在其他行业也有广泛的应用。 Ag-B 合金薄膜可以优化激光辐射场特性,降低激光辐射场中的拉曼散射和布里渊散射,在激光惯性约束可控核聚变中起着关键作用。快速响应 Pt-Rh 薄膜热电偶能快速响应并在高温下进行高精度测试,解决了武器装备壁面高温快速测量的问题。金基合金薄膜在保持纯金原有的抗氧化、耐腐蚀等优异性能的同时还大幅提高了再结晶温度,在燃料电池、透明导电薄膜、仪表接触器、开关触点、测温电阻、夜视仪、薄膜电阻等方面得到应用。含金纳米粒子梯度涂层可以提高材料的耐磨性和耐腐蚀性,延长材料的服役寿命 [9 , 27 , 37-39 ] 。
4、结束语
近年来,我国贵金属靶材制备技术发展迅速,生产的贵金属靶材已成功应用于各行业领域。但是,我国靶材企业起步较晚,特别是由于贵金属成本较高,普通的微小企业难以承担其巨大的流动资金成本,因此国内从事贵金属靶材生产的厂家一般是规模较大的企业或享受国家扶持的高新技术企业,全面、专业生产贵金属靶材的厂家较少。与国际先进靶材企业相比,靶材制造技术与产业化水平还存在较大差距,高端市场仍然被国外靶材生产商所垄断。
由于高价值的原因,贵金属溅射靶材比其他靶材在利用率方面要求更高。通常采用将贵金属靶材与铜背板连接以减小靶材厚度、对溅射后的靶材进行贵金属回收等方法来降低贵金属靶材的制备成本 [40 ] 。
靶材的使用寿命主要由两方面决定:一是靶材溅射消耗后的厚度不能小于自身的安全剩余厚度;二是靶材溅射制备的薄膜性能应满足指标要求。一般靶材的安全剩余厚度都控制在 2
mm 以上,但考虑到贵金属靶材成本,在保证溅射薄膜满足要求的条件下可以使用到不被击穿为止。国内贵金属靶材生产商需要考虑市场需求及自身发展,开展技术垂直整合,实现贵金属提纯、靶材生产及溅射镀膜一体化的发展。未来,贵金属靶材的研究重点集中在以下几个方面。
( 1 )在半导体芯片行业等尖端领域,随着半导体芯片的小型化发展,贵金属靶材的纯度要求会越来越高。未来应从贵金属原料着手研究原料的提纯方法,并且采用合适的制备加工方法保证靶材的超高纯度要求。
( 2 )除了低辐射玻璃,其他各个领域如半导体芯片、信息存储、平面显示等都要求贵金属靶材朝着大型化方向发展,这对靶材成分及显微组织的均匀性提出了更高要求。未来应加强对贵金属靶材制备及塑性加工工艺的研究,保证靶材成分及微观结构的均匀性。同时还要严格控制不同批次靶材制造过程及加工参数的一致性,保证多批次靶材组织和性能的一致性,进而保证溅射镀膜的一致性、均匀性。
( 3 )贵金属价格昂贵,因此提高靶材利用率是生产厂家密切关注的问题。未来应从改善磁控溅射工艺、改进磁控溅射设备、优化靶材结构形式等方面提升靶材利用率。例如当将实心靶材设计成旋转空心管型靶材后,靶材的利用率可从 20%~30% 提升到 80% 。这需要靶材制造厂与溅射镀膜设备生产厂的共同合作。
( 4 )获得高品质薄膜是改善靶材质量的根本目的,脱离开溅射工艺和薄膜性能,单纯地研究靶材是没有意义的。因此,应根据薄膜的性能要求,加强靶材制备工艺、微观结构、性能以及溅射工艺等与溅射薄膜性能之间关系的研究。
相关链接