1、引言
导孔是飞机制造工程中最常见的结构特征之一,大量存在于框、梁、壁板等各类飞机结构件上,主要用于飞机零部件之间的装配连接。飞机结构件上的导孔数目庞大,据统计,一架大型飞机的各类结构导孔数量多达300万种以上,某些单个零件上就有上千个导孔。因此,导孔加工技术是零件制造过程中的一项关键技术,可靠的加工技术是导孔质量优劣的有效保证。
2、导孔加工方法
2.1 钛合金材料
钛合金具有比强度(强度/密度)高、热强度高、热稳定性好和抗蚀性好等优点,但其难加工性造成了实际生产中加工效率低、加工成本高及加工质量不稳定等问题。钛合金材料的难加工性往往会导致铣削过程中刀具的快速磨损及失效,降低加工效率及加工稳定性,具体原因包括:切屑变形系数小;导热系数小,切削温度高;化学活性大;单位面积上的
切削力大;粘刀现象严重等。
2.2 导孔加工方式
长期以来,常采用人工手动制导孔和使用数控机床加工导孔两种方式。
(1)人工手动制孔
工人手动钻导孔的加工方式一直存在于航空结构件的加工中。
钻孔主要依据按样板或明胶板划线、按尺寸划线、制造钻模或者钻模板等。图1为钻模加工示意。
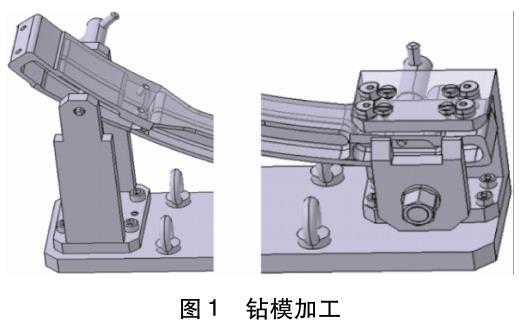
工人主要根据零件结构特点、导孔精度、孔数量和加工表面的平整度等来选用钻导孔。
大型的框、梁、壁板等零件导孔数量较多,多达上千个,工人的钻制依据是样板或者明胶板。根据尺寸划线钻导孔主要针对尺寸较小、导孔数量很少、零件表面较规则的零件,否则对于划线工人来说难度太大,操作适用性较差。当导孔的位置精度或尺寸精度要求较高时,特别是位置精度要求小于0.3mm时,可采用钻模或者钻模板钻导孔。因为采用样板或划线的方式均无法确保导孔的位置精度在0.3mm以内,而钻模可以准确设计定位基准和稳定的装夹,以保证位置精度。但钻模仅适用于较少的孔,且还需设计并制造工装,经济性较差,准备周期长。
工人手工钻制导孔劳动强度大,效率低,而且导孔质量得不到保证,孔径和孔位的精度完全依靠工人的操作熟练度,加工质量问题频现,导致零件超差甚至报废。导孔的加工质量是影响飞机寿命和飞行安全的重要因素,如果导孔的孔径或孔位有偏差,将影响连接功能,若强行装配会导致扭曲变形,影响装配精度及零件性能,甚至可能引起飞行质量事故。
(2)数控制孔
意识到导孔制造问题的重要性,国内外均在研究和试用先进的导孔制造技术,精密制孔技术应运而生,例如:角度头钻孔、机器人自动钻孔、柔性导轨自动制孔、多轴数控制孔等。
其中数控多轴制孔在航空结构件的加工过程中因适用性较强被广泛应用。
数控制孔是依据数字化模型制定加工方案,设计装夹定位方式,编制数控加工程序,在多轴数控机床上进行导孔加工。数控机床制造导孔,不仅可使加工效率提高数倍甚至数十倍,而且导孔质量较高,导孔的孔径和位置精度均可以保证在0.1mm以内,加工精度较高的机床可达到0.02mm。人工制孔与数控制孔相关因素的比较见表1。
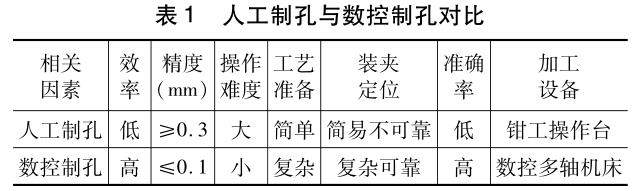
2.3 导孔检测
导孔的检测主要采用通用量具塞规、卡尺等检测孔径,采用专用样板、明胶板、检模等检测导孔的位置,属于人工对比式检测。
因人工检测操作工作量大,操作人员技能水平不同,检测结果差异性大。受检测精度和效率的影响,传统的检测方式已不能满足质量检测要求,行业内也在探究高效精准的检测方式,新的检测方式层出不穷,如测量机检测和影像检测等。
3、数字化导孔加工方法
以某梁类零件为例研究数字化加工导孔方法。
加工工艺方案制定主要包括定位装夹方式、加工流程、刀具及参数选择和数控程序编制等。
3.1零件简介
实验零件为典型的细长钛合金梁类零件,材料牌号TA15M,双面槽腔,外形为复杂双曲面,缘条厚度最小处为3.5mm,最大处为20mm。
该零件存在较多的配合关系,在零件上遍布不同规格的导孔共432个,尺寸精度及表面质量要求严格。零件导孔如图2所示。
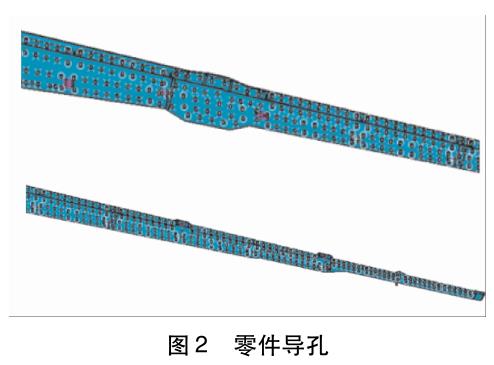
对零件导孔进行工艺性分析,结果如下:导孔直径分别为φ3.1,φ4,φ5,φ7,φ8,φ10;导孔分布于零件的缘条及筋条上;导孔的法向垂直于导孔所在表面,其95%以上为变角度曲面;零件为长梁类零件,材料为模锻件,缘高均为斜面;加工公差要求孔位±0.2、孔径0.20、孔距±0.2;导孔所分布的壁厚从3.5~20mm不等。
根据上述信息分析出该零件导孔的加工难度主要集中在以下几点:导孔数量较大;导孔种类较多;导孔分布广泛;导孔法向方向难以确定;装夹定位难度大;导孔精度较高;导孔深度不均。从保证导孔精度和加工效率两方面分析,该零件如果采用人工制导孔方式几乎无法实现,只有采用数控多轴制孔才能保证导孔的法向和精度,并显著提高加工效率。
3.2定位装夹方式
实验零件长且细,97%导孔集中在缘条,针对现有加工资源,采用缘条定位是较好的选择。
由于该零件的缘条为斜缘条,采用斜缘条直接定位会大幅降低定位面的精度,对零件加工质量影响较大。
因此在缘条高度上设置工艺凸台来进行定位,用以保证定位基准精度。
确定定位面后,还需选择两个孔参与定位。
确定定位基准后,根据定位基准设计装夹压紧的工装。定位方式尽量要与正反两面加工时的定位方式一致,以保证数控导孔位置的准确度。
然后需要考虑工装的形式,该工位工装压紧零件的方式较难,因为在零件的缘条上每一个位置都有导孔,压板的位置会干涉导孔的钻制。因此既要确保零件装夹的稳定性,还要考虑操作简单便捷、不干涉。该零件在腹板上有较多大直径减轻孔,利用该特点,可在工装上采用穿螺栓、压紧腹板的方式对零件进行压紧,不仅起到压紧零件的作用,并有效避免了在钻导孔时钻头与压板的干涉,去除了工人在加工过程中倒压板的工作,降低了劳动强度。工装设计见图3。
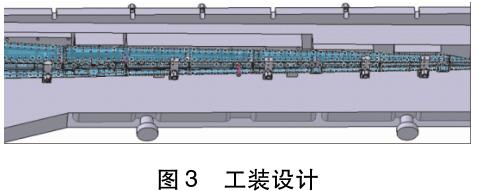
3.3 确定加工流程
加工流程的合理安排是零件导孔加工的重要环节,合理的加工流程是导孔加工质量和加工效率的有效保证。根据某梁类零件的结构特点及现有的加工资源,采用数控导孔加工设计两个工位,正反两面加工,装夹定位方式基本一致。
数控加工导孔采用中心钻点孔位,避免钻孔时钻头偏滑导致孔位置偏移或孔形状椭圆。特别是斜面或变角度曲面必须在钻孔前进行点孔位,以便在使用钻头钻孔时起定心作用。导孔的加工顺序设定的主要原则是:加工精度高;防错级别最高;加工效率高;操作难度最小。
该零件的导孔钻制顺序是由少至多,相近规格交叉加工。
3.4刀具及切削参数选择
数控加工中刀具的选用至关重要,刀具种类及切削参数直接影响零件的尺寸精度和加工效率等。由于零件结构特异,且材料为难加工材料,因此对刀具的要求较高。某梁数控加工导孔的刀具均选用整体合金专用刀具,加工参数依据现有参数库及零件实际加工情况来确定。加工参数选择见表2。
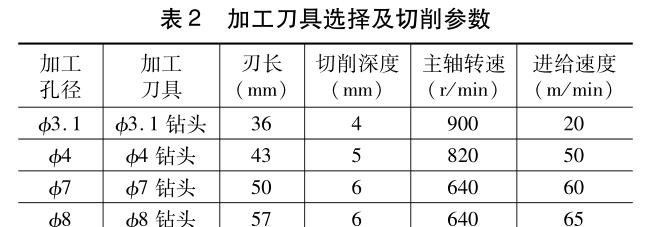
3.5 程序编制
数控导孔程序的编制使用CATIA软件,零件在加工过程中尽可能地释放应力以及降低切削力,减小了零件粗加工后的变形量。在数控钻导孔程序编制过程中,要考虑走刀方式、切削深度、接近方式等。由于导孔一般较小,钻头较细,所以在加工过程中容易折断,折断时会打伤零件,导致零件超差或报废。有的钻头会折断在零件内部,难以取出,并伤及零
件。接近零件方式不正确、加工速度过快、退刀方式错误和积屑等因素都会导致钻头折断,所以在数控程序编制过程中需要全面考虑。
4、结语
通过研究适用于钛合金航空结构件导孔的多轴数控加工方法,解决了生产的实际问题。
以本文试验零件为例,缘条最厚处达到20mm,如采用传统方法,常规钳工钻制约需35~40h,加工难度较大,费时费力,产品质量也不易保证。
采用数控加工导孔时间仅需10.4h,既省时省力,又提高了产品质量。
特别是对于批量化生产的零件,加工优势更加显著。该方案已通过实际加工验证,生产零件质量合格,加工过程稳定。
参考文献
[1]王欢.钛合金螺旋铣孔试验研究[D].大连:大连理工大学,2015.
[2]赵鹏飞.孔加工切削参数优化系统的研究与开发[D].南京:南京理工大学,2013.
第一作者:孙丽敏,航空工业沈阳飞机工业集团有限公司数控加工厂,110850沈阳市First
Author:Sun Limin,Shenyang Aircraft Industrial (Group)Co.,Ltd.,Shenyang110850,China
相关链接