钴基合金具有优异的耐磨性、耐蚀性、耐高温、生物相容性,被广泛应用在航空航天、军民工业等领域[1-4]。目前国际上对于钴基合金的研究主要集中在成分组成、制备工艺及其显微缺陷组织等方面[5-9]。钴基合金中通常添加铬、钼、镍、钨或钛等合金元素来获得高性能或特殊性能[10-12]。铬和钼能稳定hcp相、降低基体的堆垛层错能[13-15],且铬和钼使钴基合金表面形成表面氧化膜可极大提高合金的耐蚀性能[16]。而镍则可以稳定fcc相,使钴基合金的硬度降低[13-16]。钴铬镍体系合金作为钴基合金的重要体系分支,即司太立21,由于具有较高的耐高温腐蚀、耐热冲击、高温强度和较好的延展性能,常用于燃气涡轮叶片等重要工程领域。传统钴基合金的制备方法采用铸造工艺,铸态钴基合金中存在组织粗大、疏松缩孔等铸造缺陷,这些缺陷显著降低了合金的塑性和疲劳特性。铸造合金植入材料的过早破坏和失效通常是由这些铸造缺陷引起的[17]。铸造过程中冷却速率对钴基合金的组织结构有明显影响,在低冷却速率下铸造组织形成粗大树枝晶,枝晶间通常分布有碳化物;冷却速率提高则形成等轴晶结构,杂质和缺陷分散分布,大部分碳化物在等轴晶晶界沉淀析出,形成连续的晶界碳化物沉淀[18-21],然而快速冷却工艺对设备条件要求苛刻。如何在现有的基础上提高冷却速率、避免连续的晶界碳化物对组织的割裂作用,是提高铸造钴铬镍合金性能的重要途经。亚快速凝固是一种介于近平衡低速生长和远离平衡快速生长的非平衡凝固过程,又被称为准快速凝固或近快速凝固,凝固冷却速率在102~103K/s之间[22]。亚快速冷却过程中元素的微偏析时间短,有利于产生细小均匀的微观组织[23],且对设备的要求低。因此,进一步详细研究钴铬镍合金的亚快速凝固工艺具有较大的理论意义。
采用粉末冶金工艺制备的烧结合金通常具有均匀的组织结构和稳定的性能。且烧结合金不具有类似铸造合金的疏松疏孔、夹杂、偏析、组织粗大等缺陷,因而相对于铸造合金具有较高的性能优势[6]。
Rodrigues等[24]采用粉末冶金方法制备了钴铬钼合金,其组织内也存在较高比例的不连续碳化物和较高的孔隙率。本课题组的前期研究曾采用粉末冶金工艺制备了钴铬镍合金,表明Cr,Ni含量对烧结合金的组织组成、孔隙缺陷及其力学性能具有显著的影响[25]。因此,本工作进一步采用亚快速凝固和真空烧结两种工艺方法制备钴铬镍合金,对两种工艺过程中合金的组织演变、组织缺陷及Cr,Ni含量的影响规律进行对比研究,为钴铬镍合金材料制备方法的优化、缺陷和性能控制提供理论指导。
1、实验材料与方法
1.1混合料方法
实验用粉末均为市售粉末原料,改变铬、镍成分含量分别配置两组混合料A和B,混合料原始配比如表1所示。按配比称取粉末进行混料,采用XQM-4L型行星式球磨机均匀混合原始料,转速200r/min,磨球采用ϕ10mm的不锈钢球,球磨介质为无水乙醇,球磨混料时间为60h。混合浆料于80℃干燥箱干燥、过100目筛得到混合料。混合料粉末采用模具成型方法获得压坯,压坯尺寸为39.2mm×6.6mm×6mm,双向压制,压制力600MPa、保压1min,压坯试样分别采用真空烧结和亚快速凝固方法制备获得。
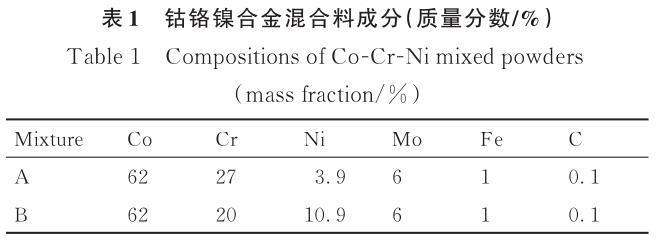
1.2铸造合金工艺方法
利用DHL-300型非自耗真空钨极电弧熔炼炉进行电弧熔炼铸造工艺研究。在熔炼室真空度为10-3Pa后通入高纯氩气,炉内氩气压力保持在0.05MPa,引燃电弧熔炼试样,翻转试样熔炼3次获得合金锭。采用200A电流熔融后将电流提高至500A继续熔炼30s,打开吸铸阀,合金液在自身重力和上下压力差的耦合作用下被吸入紫铜模具进行冷却,得到阶梯状钴铬镍铸造合金,阶梯状铸造合金的结构如图1所示。
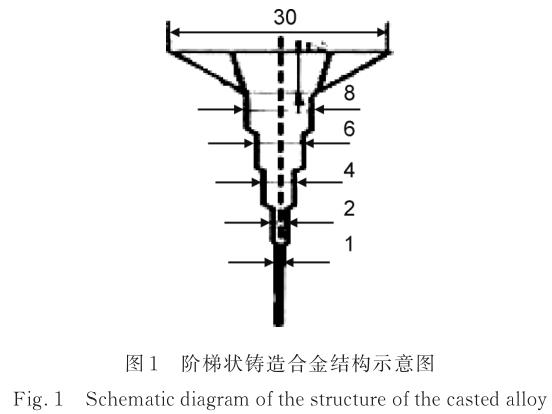
1,2,4mm阶梯合金的冷却速率分别为120,84,64K/s。同时,制备尺寸为ϕ4mm×40mm的圆柱力学拉伸合金试样,冷却速率64K/s。铸造合金的冷却速率为亚快速冷却速率范围,冷却速率的获得方法在本课题组的前期研究中有明确的分析[26]。
1.3粉末冶金真空烧结工艺方法
利用DN900压力烧结炉,压坯试样在1300,1320,1350,1370℃4个温度下真空烧结成型,真空度保持在10-2~102Pa,烧结温度保温时间为1h。升温过程采用步进式方法以保证压坯温度的均匀性,采用充气冷却方法获得烧结合金,冷却载气为高纯氩气,真空烧结工艺曲线如图2所示。
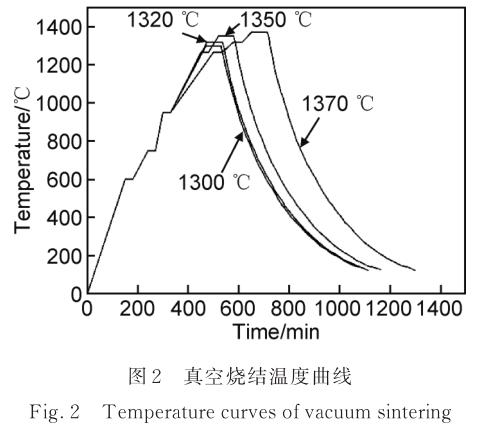
1.4测试分析方法
混合料的粒度分布采用JL-1177型激光粒度仪进行测试。铸造合金沿浇注轴向中间剖开取样,分别观察其纵向及横断面组织。烧结合金切取截面试样观察组织形貌。显微组织观察分别采用光学显微镜(OM,LEICADM2700M)、扫描电子显微镜(SEM,Quanta250FEG)进行测试,利用扫描电镜自带的能谱仪(EDS,Quanta250FEG)测定组织微区成分。合金物相利用XRD分析方法,采用PHILIPSAPD-10X射线衍射仪,Cu靶,管流40mA,管电压40kV,扫描角度为30°~100°,扫描速率2(°)/min。烧结合金的显微缺陷组织采用透射电子显微镜(TEM,TecnaiG2F30)进行观察,制备ϕ3mm的薄膜试样机械抛光后,进行-20℃双喷减薄,双喷液为体积分数6.0%的高氯酸酒精溶液,电压45V,电流30mA。对X射线衍射峰进行高斯单峰拟合,采用的公式为[27]:
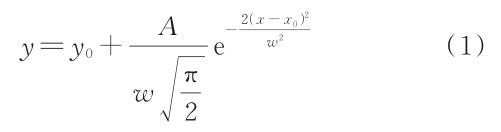
式中:y为衍射峰峰值;y0为衍射峰基线;A为衍射峰的积分强度;w为峰宽;x为衍射峰对应的扫描角度;x0为最高峰对应的扫描角度。高斯单峰拟合后得到衍射峰半峰宽(fullwidthathalfmaximum,FWHM)数值,FWHM主要反映了位错密度的变化,位错密度越大,FWHM越大。
铸造合金力学拉伸试样采用ϕ4mm×40mm圆柱试样。烧结合金力学性能试样采用非标准拉伸试样,试样沿烧结样品的长轴取样,标距长度10mm,截面尺寸为2mm×2mm,采用自制的钢制夹具,在室温下进行等轴拉伸实验。拉伸实验标准依据GB/T228—2002,应变速率0.01mm/min。取拉断后的试样截面,利用维氏硬度计(MicroMet2104)测量试样的硬度。采用二值分割法对金相和扫描图片进行处理,计算两相体积分数。
2、实验结果与分析
2.1混合料的混合粉体形貌
图3给出了两成分试样的原始混合粉(混合时间10min)与球磨混合60h后的混合料的粉末形貌。由图3可见,混合粉的起始形态为球形粉末形貌,混合料A,B的原始混合粒度分别为11.03µm和10.10µm;经过60h的球磨混合后,混合料形貌皆转变为层片状结构形貌,可以断定金属粉末在球磨过程中发生了明显的塑性变形、加工硬化、焊合和断裂的行为。图4给出了混合料A和B的粉体粒度统计分布曲线。由图4可见,混合料A和B的粉末平均粒度分别为1.77µm和1.80µm,粉末粒度分布呈现单峰分布规律。图5给出了混合料A和B的起始混合料和球磨后混合料的XRD图谱。由图5可以看出,球磨后主要合金元素Co,Cr,Ni,Mo的衍射峰都呈现不同程度的降幅和宽化,其中Co的主峰(100)和(101)衍射峰、Ni的主峰(200)衍射峰呈现出显著的降幅和宽化,Mo和Cr的主峰也可以直观地分辨峰形的降幅和宽化。与混合料A相比,混合料B中(100)Co和(101)Co衍射峰的降幅更加显著,2个衍射峰趋于消失。2θ位于44.8°的最强衍射峰为(002)Co,(110)Cr和(111)Ni衍射峰的叠加峰,A,B混合料中此峰的降幅接近但混合料B中峰形宽化明显。A,B混合料中Co为溶剂元素,质量分数占比高达62%,由此判定2θ位于44.8°的最强衍射峰的降幅和宽化主要是(002)Co衍射峰的降幅和宽化所引起,同时推断A,B混合料中并未发生明显固溶。粉末的X射线衍射峰FWHM值主要反映了合金粉末的畸变程度,即其加工硬化程度,可见球磨混料行为使得混合料产生了明显的加工硬化。混合料中各成分的塑性变形与加工硬化则加剧了其晶体弹性的各向异性,引起衍射谱的各向异性应变宽化,而衍射谱的各向异性应变宽化与衍射面指数相关[28]。采用混合料XRD图谱中的2个最强峰,即2θ位于44.8°的(002)Co衍射峰和2θ位于40.5°的(110)Mo衍射峰来表征混合料的加工硬化状态。经计算可知,混合料A的(002)Co衍射峰的FWHM值较原始粉末增加120%,混合料B的(002)Co衍射峰的FWHM值较原始粉末增加了203%;混合料A和B的(110)Mo衍射峰的半峰宽FWHM值较原始粉末分别增加了196%和261%。Ni为fcc结构,Co为hcp结构,而Cr和Mo为bcc结构,与Co,Mo和Cr相
比,Ni具有较高的塑性。可见,合金混合粉末成分中Cr含量的降低和Ni含量的增加可以降低粉末的塑性抗力[29],因此明显增大混合料的储能和加工硬化程度,特别是对于溶剂Co的影响显著。
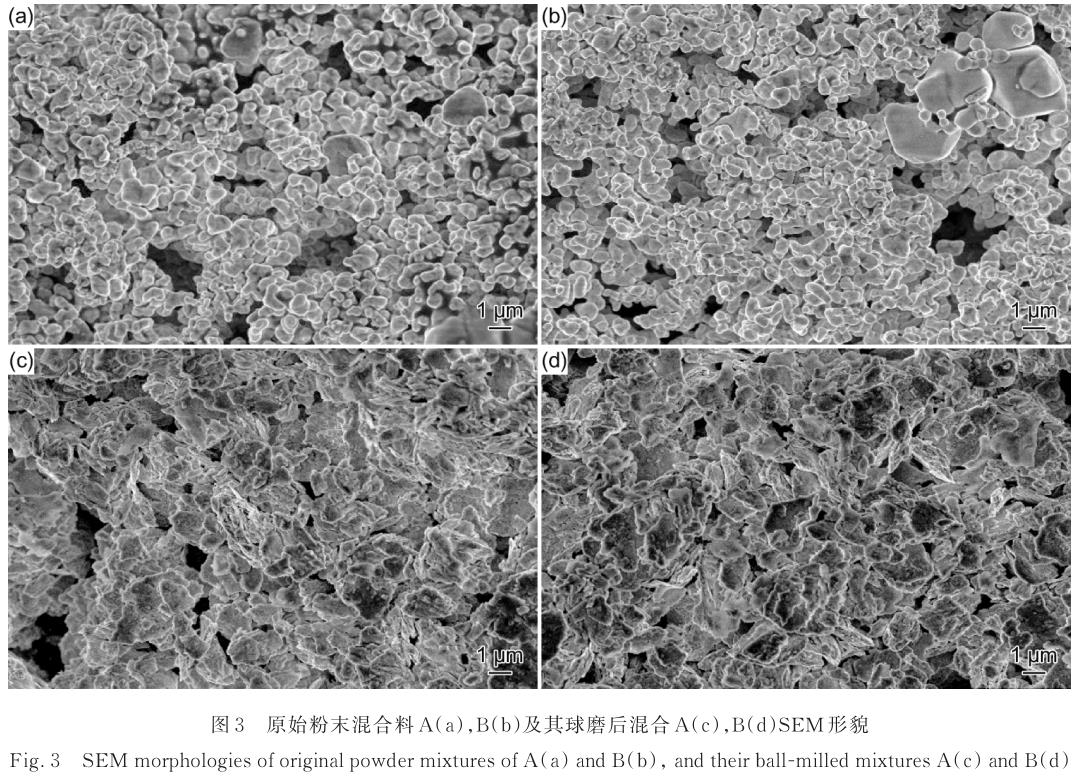
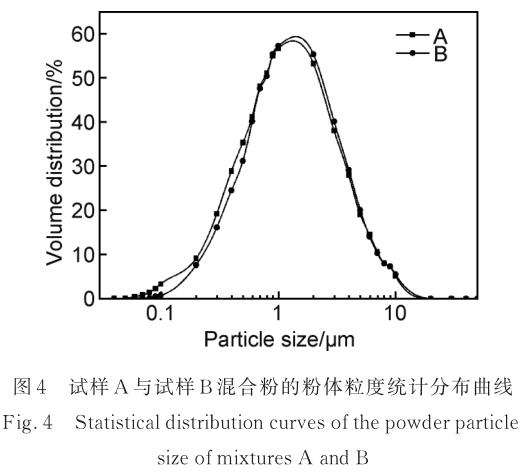
2.2铸造合金的组织演变规律
图6给出了铸造冷却速率分别为120,84,64K/s时两种成分的钴铬镍铸造合金的金相组织形貌。从金相组织可以看出,合金A和B的铸造组织皆呈现胞状树枝晶结构,枝晶随冷却速率的降低而粗化。利用铸造合金的SEM组织,采用三角法测量二次枝晶间距,将3个相邻枝晶晶体中心连线,每一条边长均作为间距数据,在铸造合金试样的横截面中心区域选取100组数据,通过ImageProPlus软件测量获得二次枝晶的平均间距数据。图7给出了铸造合金A,B的SEM组织(冷却速率为120K/s)及二次枝晶间距(sec-ondarydendritearmspacings,SDAS)测量示意图。A,B合金的二次枝晶间距测试结果见表2,数据结果进一步表明随铸造冷却速率的降低,二次枝晶间距增大。另外,合金B的二次枝晶间距明显大于合金A的二次枝晶间距。由此表明,Cr含量降低、Ni含量的增加,促进了铸造合金枝晶的粗化。
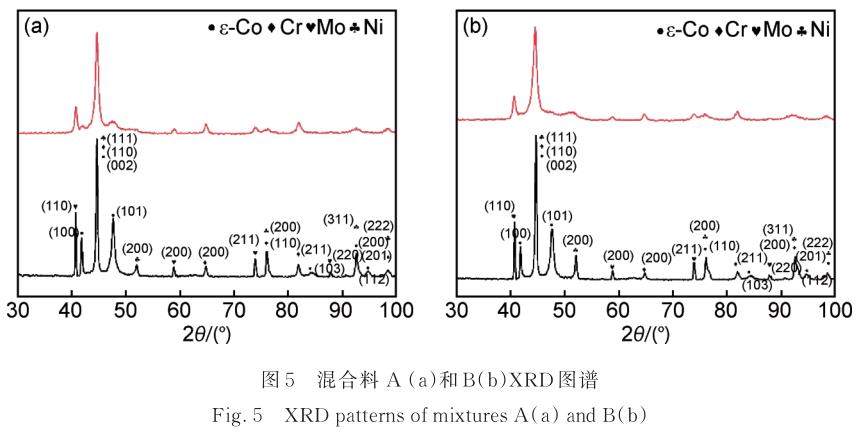
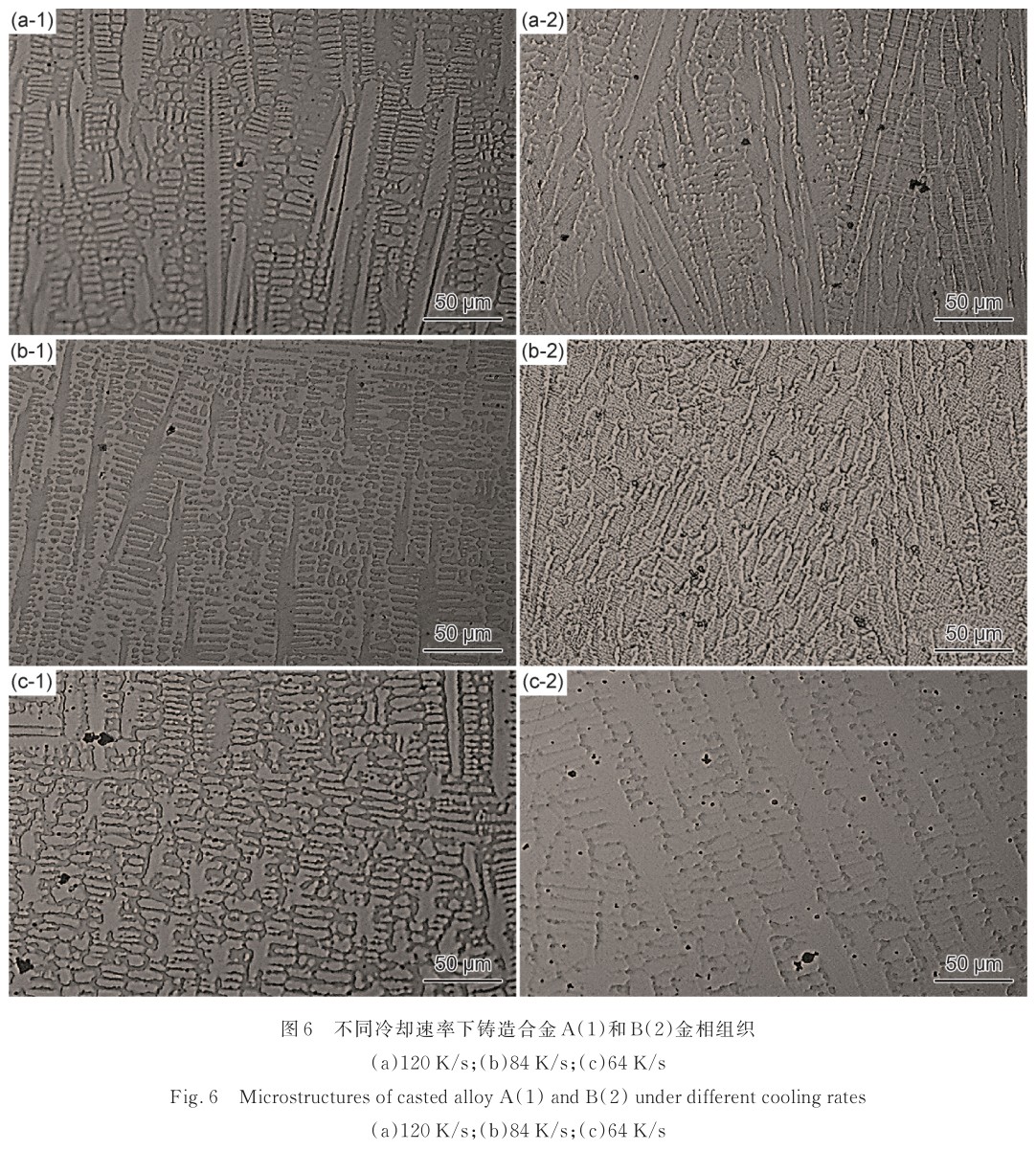
由图7可见,钴铬镍铸造合金的枝晶干为浅灰色组织结构,枝晶间区域为亮白色组织结构,组织内并没有发现碳化物。图8给出铸造合金A,B的物相XRD分析图谱,结果表明合金A和B的铸造组织皆为面心立方(γ-fcc)和密排六方(ε-hcp)钴的两相组织,未发现其他析出相的存在。对SEM组织的枝晶间和枝晶干区域进行EDS分析(以合金A为例,如图9所示),结果表明枝晶间富Cr而枝晶干区域富Ni,由此判断钴铬镍合金铸造成形过程中存在合金元素的枝晶偏析,枝晶间硬度384.5HV高于枝晶干的硬度347.2HV,由于Cr为ε-hcp相元素,Ni为γ-fcc相元素,ε-hcp相的硬度通常高于γ-fcc相,由此断定枝晶间为ε-hcp相,枝晶干为γ-fcc相。
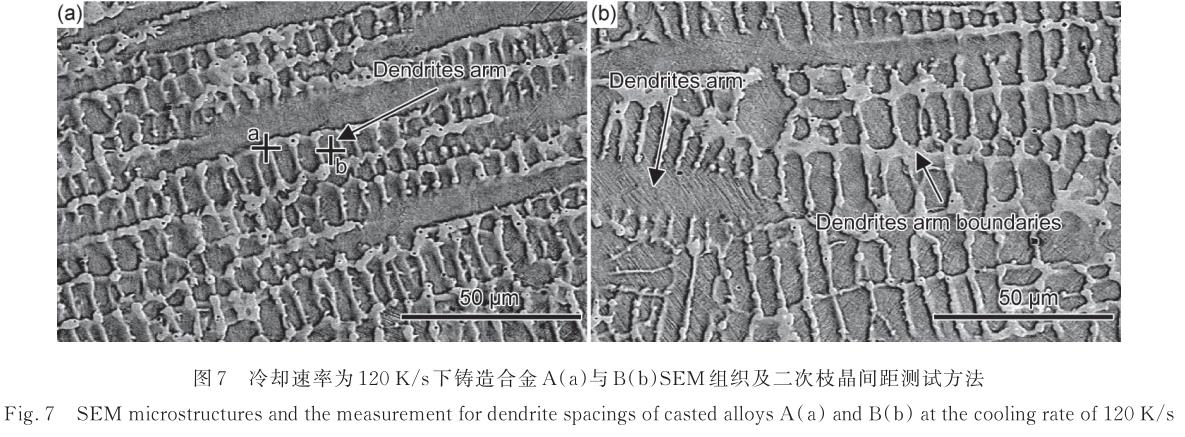
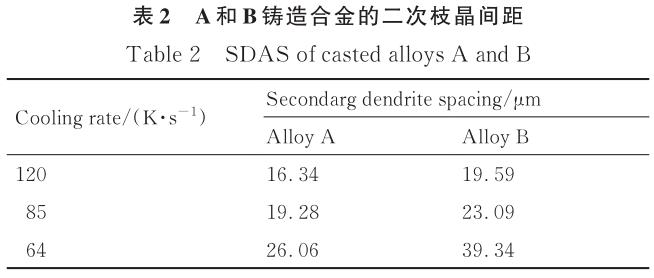
钴铬镍合金铸造凝固过程中,溶剂为Co,其他合金元素为溶质,随液态合金凝固过程的进行,溶质元素在溶剂内发生扩散和偏析。在本工作所研究的合金A和B中,主要考虑Ni和Cr的偏析,采用EDS能谱分析结果计算元素的偏析系数(=枝晶间元素平均成分/枝晶干元素平均成分),取5个分析数值结果的平均值。经计算,Ni=0.88<1,Cr=1.06>1,这说明Ni元素为负偏析元素,Cr元素为正偏析元素,Ni元素易偏聚于枝晶干而Cr元素偏聚于枝晶间。表3给出了铸造合金两相的体积分数,结果表明Ni含量增加,γ-fcc相的体积分数增大,即枝晶干的体积分数增加。
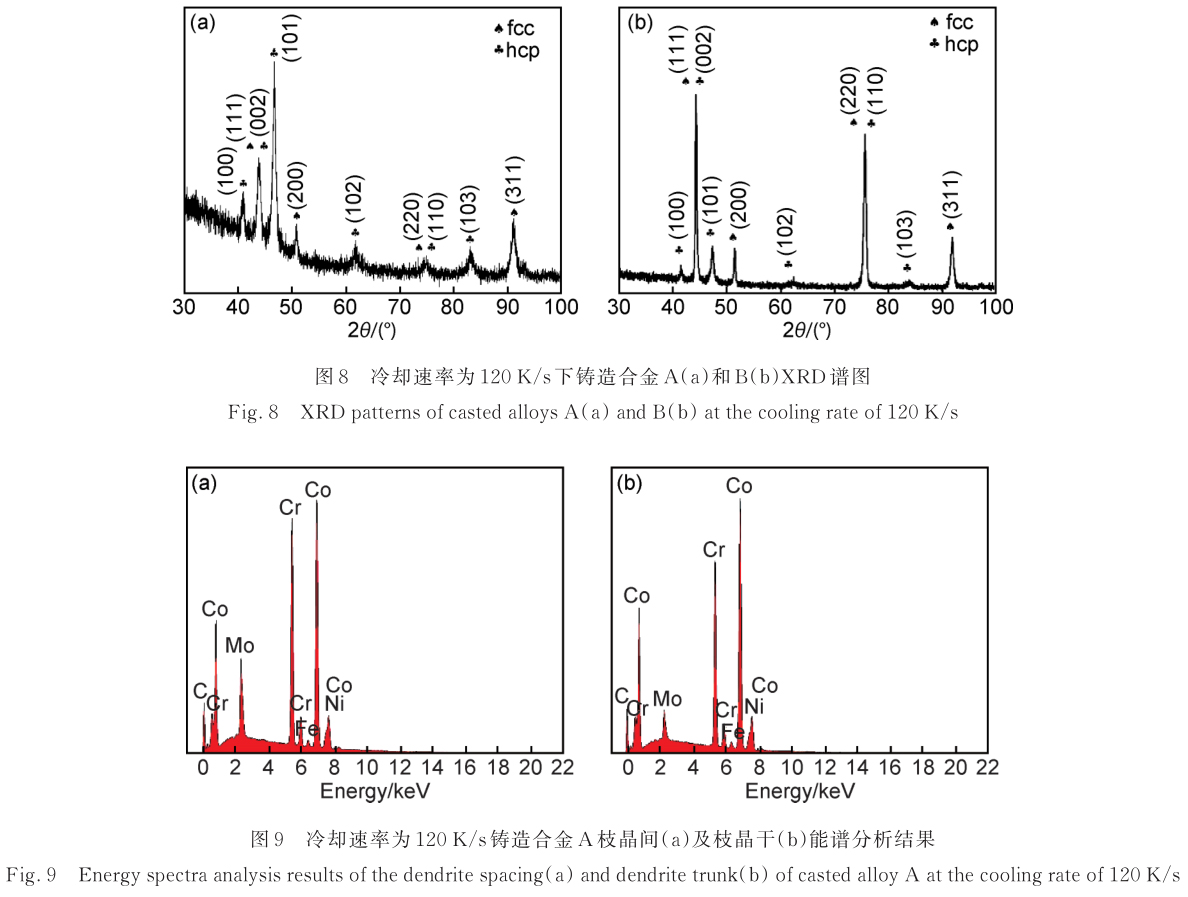
由此断定Ni含量的增加促进γ-fcc相的形成,对ε-hcp相有一定的抑制作用。
2.3钴铬镍烧结合金的组织演变
图10给出了合金A和B经过不同烧结温度真空烧结后的金相组织,可以看出,烧结合金A和B显示出不同的组织形貌特征。合金A烧结试样的晶粒粗大不规则,随烧结温度的升高急剧长大;合金B烧结试样的晶粒为细小、规则的等轴晶,随烧结温度的升高只是略有粗化。分别测量烧结合金A,B的200个晶粒尺寸,计算得到平均晶粒尺寸。合金粒径随烧结温度的变化关系如图11所示,可以看出,烧结合金A的晶粒尺寸大约是烧结合金B的晶粒尺寸的4倍,且随烧结温度升高呈现显著粗化趋势。可见,两成分由于Ni含量的不同,导致混合料的储能变化及加工硬化不同,对于烧结合金的晶粒度产生了较为显著的影响。基于本课题组的前期研究,烧结合金A为ε-hcp单相组织,烧结合金B为γ-fcc+ε-hcp双相组织[25]。随着烧结温度的升高,ε-hcp单相合金的晶粒具有较高的合并与长大趋势,而γ-fcc+ε-hcp双相组织中由于γ-fcc相的出现,阻止了ε-hcp相晶粒的合并与长大,因此烧结合金B具有较小的晶粒尺寸。
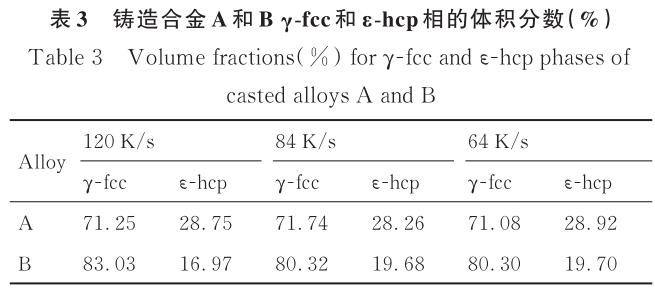
如图10所示,合金A和B烧结试样的组织内都不可避免地形成了孔隙缺陷,烧结合金A内的孔隙缺陷同时分布在晶内和晶界,1320℃以下温度烧结的合金B的孔隙缺陷亦同时分布在晶内和晶界,1350℃以上温度烧结的合金B的孔隙缺陷则主要出现在晶界。采用图像法获得的烧结合金A和B的孔隙缺陷的体积分数(V)及其等效直径(D)列于表4。烧结合金A内的孔隙分布特征不随烧结温度和晶粒大小变化,孔隙率和孔隙直径随烧结温度的升高逐渐增大。而烧结合金B随烧结温度升高和晶粒的粗化,孔隙趋于晶界分布,且孔隙尺寸随之明显增大。
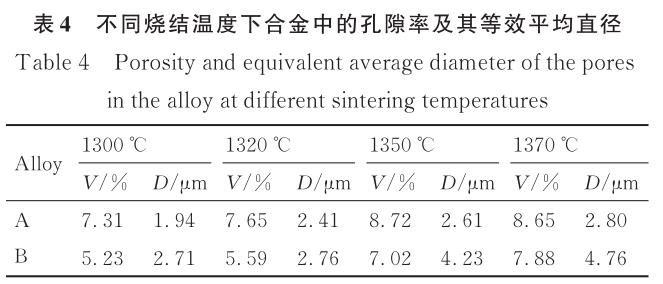
在4个烧结温度下随烧结温度的升高,烧结合金A和B的致密度分别从93.08%,92.96%,92.84%降低到92.49%和从94.95%,94.60%,93.90%降低到93.78%。烧结体内的孔隙及其所导致的致密度随烧结温度的变化规律,与合金成分、相组成及其显微结构、烧结温度下的表面能变化有关。一般情况下,随着烧结温度的升高,烧结体的致密度升高。而本工作中出现的现象,推断是随着烧结温度的升高,碳与氧的还原反应加剧,未反应的氧对粉末颗粒或晶粒的表面张力影响降低,造成颗粒和晶界间的表面张力升高,碳与氧还原反应形成的一氧化碳气体难以排出而引起。另外,粉末成型时采用了600MPa的压力,粉末颗粒间过早紧密咬合,封闭了部分气体流动排出通道;烧结过程中随烧结温度的升高,封闭在坯体内的气体急剧膨胀,从而导致了随烧结温度升高烧结体致密度下降的结果。然而,详细的机制仍不清晰。
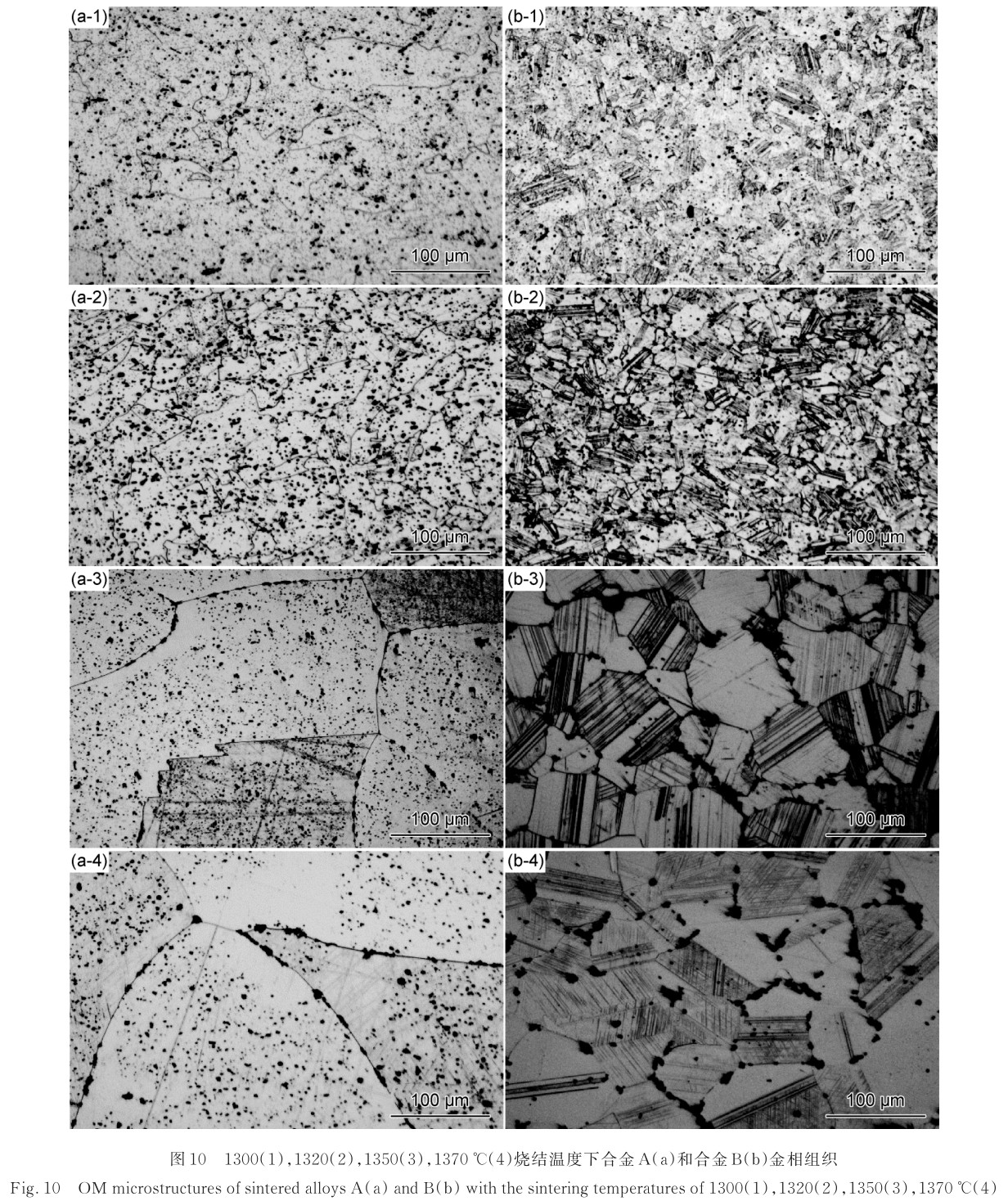
从图10还可以看出,烧结合金B的组织内分布有明显的条纹结构,由前期研究可知,这些条纹线为fcc-Co相中的孪晶和层错[25]。图12给出了烧结温度为1300℃合金烧结试样A,B的TEM组织,可以看出,烧结合金A中主要的亚结构为位错,位错在晶界上聚集和缠结;烧结合金B中的亚结构则是层错和孪晶。钴有两种同素异构体,γ-Co层错能为18.5×10-7J·cm-2,ε-Co层错能为20.5×10-7J·cm-2[30]。镍含量的增加促进了γ-fcc相的形成[23],γ-fcc相的层错能低,烧结过程中γ-fcc相的形成过程伴随着大量的层错和孪晶的形成。由此可以推断,γ-fcc相组织的强化方式为层错和孪晶,ε-hcp相组织的强化方式则主要是位错。与熔炼合金相比,烧结合金内出现了大量的组织缺陷,位错、层错与孪晶的出现与固相烧结机制有关,其形成机制需要进行更深入的分析和另文报道。
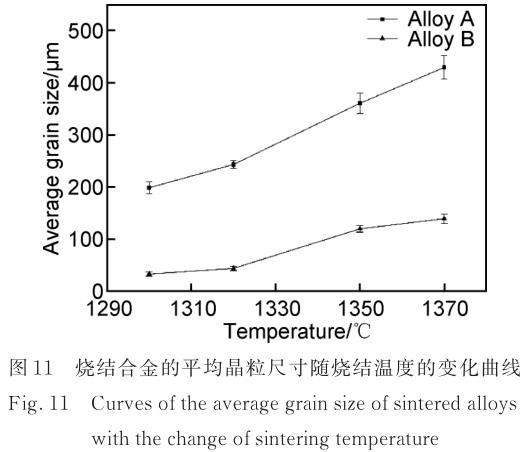
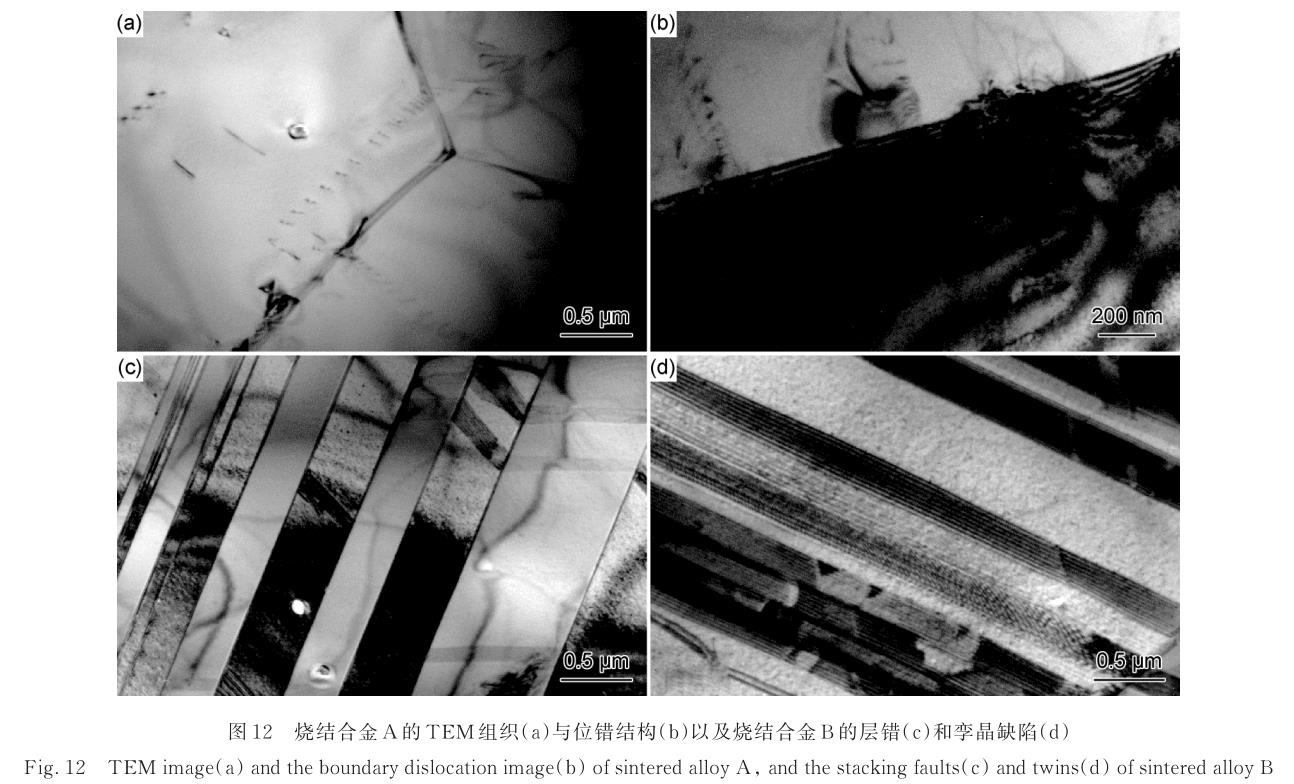
2.4铸造/烧结钴铬镍合金的力学性能
图13为铸造及烧结合金A,B(烧结温度1300℃)的工程应力-应变曲线示例。如图13所示,铸造合金A,B的工程应力-应变曲线呈现脆性特征,而烧结合金的工程应力-应变曲线呈现塑性特征,具有明显屈服现象;烧结合金相对于铸造合金呈现出更高的性能,尤其是更高的塑性。以烧结温度为1300℃的烧结合金为例:烧结合金A,B的抗拉强度较铸造合金A,B分别提高147.24MPa和148.03MPa,断后伸长率分别提高3.74%和11.2%;相对于合金A,合金B的铸造和烧结试样皆表现出更为明显的塑性变形过程,铸造和烧结合金B较铸造和烧结合金A的断后伸长率分别增加12.53%和19.99%。然而,合金A,B的铸造及烧结试样断口均没有出现明显的颈缩,类似情况在哈德菲尔德(Hadfield)钢中同样存在[31-32]。这表明,合金相组成及其显微组织缺陷是决定合金塑性变形行为的主要因素。ε-hcp相为硬相,具有较高的强度和硬度,γ-fcc相为塑性相,可以提高组织塑性。两相组织内γ-fcc相体积分数的升高会明显提高组织的塑性,但由于γ-fcc相在拉伸过程中的加工硬化特征及其向ε-hcp相的诱发相变过程,造成组织强化进一步提升了抗拉强度[22]。ε-hcp相的(0001)〈11-20〉基面滑移系的临界分切应力值为204MPa,{1-100}〈11-20〉柱面滑移系临界分切应力值为272MPa,都远高于γ-fcc相{111}〈11-2〉滑移系的临界分切应力值54MPa[33],因此,组织中γ-fcc相体积分数的提高会降低组织的屈服强度。由此,合金B的屈服强度总是低于合金A。由此断定,烧结合金A中ε-hcp相的位错是造成其具有较高性能的主要因素,烧结合金B中γ-fcc相的孪晶和层错则是γ-fcc+ε-hcp双相组织性能提升的主要因素,尤其是塑性提升的决定性因素。表5给出了铸造合金和各烧结温度下烧结合金的力学性能。可见,随着烧结温度的升高,晶粒尺寸的粗化和晶界上较高的孔隙率缺陷,降低了烧结合金的强度和塑性。
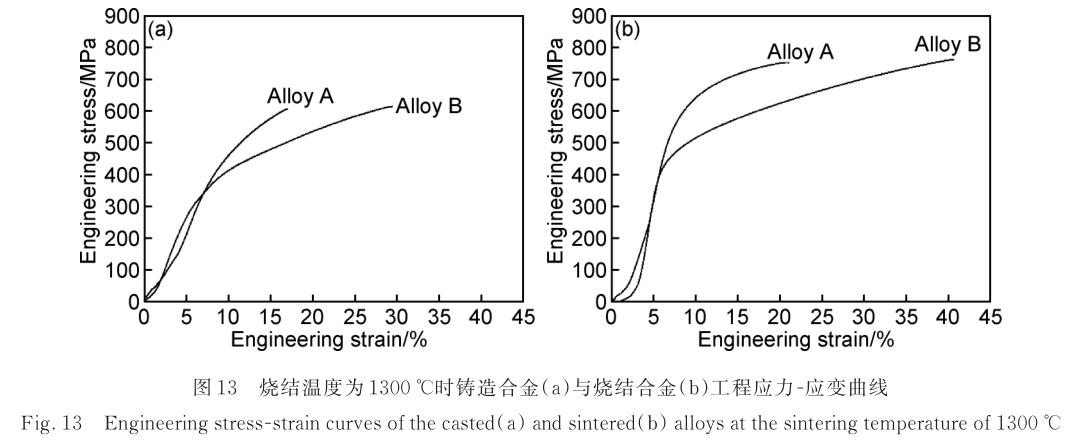
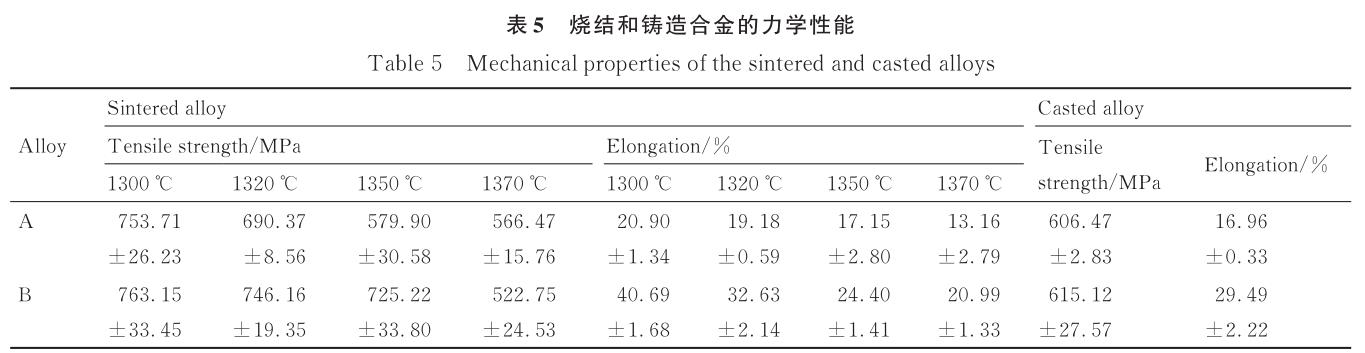
3、结论
(1)钴铬镍合金铸造冷却过程中存在Cr,Ni元素的偏析,Ni元素为正偏析元素在枝晶干富集,Cr元素为负偏析元素在枝晶间富集。由此可知,Ni含量增加会促进γ-fcc相的形成和铸造枝晶粗化。铸造冷却速率的降低会加大二次枝晶间距。
(2)混合料的储能与加工硬化及Cr,Ni含量会显著影响固相烧结合金的显微缺陷组织。随Cr含量的降低、Ni含量的增加,合金由ε-hcp单相组织转变为γ-fcc+ε-hcp双相组织,且Ni含量增加会显著降低烧结合金的晶粒度及其随烧结温度的粗化趋势。烧结合金γ-fcc相中形成层错和孪晶缺陷。
(3)烧结合金的力学性能,尤其是塑性,较铸造合金有明显的升高。随合金原始成分中Cr含量降低、Ni含量升高,塑性γ-fcc相体积分数增加,铸造和烧结后合金均呈现塑性增长趋势。位错是烧结ε-hcp单相合金性能提升的主要因素,孪晶和层错则是烧结γ-fcc+ε-hcp两相合金性能提升的主要因素。
参考文献
[1]PATTNAIK S, KARUNAKAR D B, JHA P K.Developments in investment casting process-a review[J].Journal of Materials Porcessing Technology, 2012, 212(11): 2332-2348.
[2]PONCIN P, MILLET C, CHEVY C, et al.Comparing and opti-mizing Co-Cr tubing for stent applications[C]∥ Proceedings of the Materials and Processes for Medical Devices Conference.Califor-nia: Metallurgical Solutions,2004: 279-283.
[3]HIROMOTO S, ONODERA E, CHIBA A, et al.Microstruc-ture and corrosion behaviour in biological environments of the new forged low-Ni Co-Cr-Mo alloys [J].Biomaterials, 2005,26(24): 4912-4923.
[4]LASHGARI H R, KONG C, ASNAVANDI M, et al.The ef-fect of friction stir processing (FSP) on the microstructure, nano-mechanical and corrosion properties of low carbon CoCr28Mo5 al-loy[J].Surface and Coatings Technology, 2018, 354: 390-404.
[5]CAI S, DAYMOND M R, REN Y.Stress induced martensite transformation in Co-28Cr-6Mo alloy during room temperature de-formation[J].Materials Science and Engineering: A, 2013, 580:209-216.
[6]NOVA K, NOVAK P, DVORSKY D.Influence of alloying ele-ments on the mechanical properties of a cobalt-based alloy pro-duced with powder metallurgy[J].Materiali in Tehnologije, 2017,51(3): 443-447.
[7]乔镇, 贺娟, 黄永玲, 等 .钴铬钼多孔关节烧结工艺的研究[J].材料工程, 2011(6):48-51.
QIAO Z, HE J, HUANG L Y, et al.Study on sintering process of porous Co-Cr-Mo alloy for artificial joint [J].Journal of Materi-als Engineering, 2011(6):48-51.
[8]DONG X, LI N, ZHOU Y N, et al.Grain boundary character and stress corrosion cracking behavior of Co-Cr alloy fabricated by selective laser melting[J].Journal of Materials Science & Tech-nology, 2021, 93: 244-253.
[9]苗文卷, 曹睿, 车洪艳, 等 .Stellite12 钴基合金的疲劳性能及其断裂机理研究[J].材料工程, 2021,49(1):153-159.
MIAO W J, CAO R, CHE H Y, et al.Fatigue properties and fe-acture mechanism of Stellite12 cobalt-based alloy [J].Journal of Materials Engineering, 2021, 49(1): 153-159.
[10]WANG W L, YIN F C, ZHANG M H, et al.Experimental in-vestigation and thermodynamic calculation of the Co-Cr-Mo sys-tem[J].Journal of Phase Equilibria and Diffusion, 2014, 35(5):544-554.
[11]MORAVCIK I, CIZEK J, KOVACOVA Z, et al.Mechanical and microstructural characterization of powder metallurgy CoCrNi medium entropy alloy[J].Materials Science and Engineering:A, 2017, 701: 370-380.
[12]ZHUANG X L, ANTONOV S, LI L F, et al.Effect of alloy-ing elements on the coarsening rate of γʹ precipitates in multi-component CoNi-based superalloys with high Cr content[J].Scripta Materialia, 2021, 202:114004.
[13]MORI M, YAMANAKA K, SATO S, et al.Tuning strain-induced γ -to- ε martensitic transformation of biomedical Co-Cr-Mo alloys by introducing parent phase lattice defects[J].Journal of the Mechanical Behavior of Biomedical Materials, 2019, 90:523-529.
[14]TAYLOR R N J, WATERHOUSE R B.A study of the ageing behaviour of a cobalt based implant alloy[J].Journal of Materials Science, 1983, 18(11): 3265-3280.
[15]MAREK I, NOVÁK P, MLYNÁR J, et al.Powder metallurgy preparation of Co-based alloys for biomedical applications[J].Acta Physica Polonica A, 2015, 128(4): 597-602.
[16]MATKOVIĆ T, MATKOVIĆ P, MALINA J.Effects of Ni and Mo on the microstructure and some other properties of Co-Cr dental alloys[J].Journal of Alloys and Compounds, 2004, 366(1/2): 293-297.
[17]JOHN K R S.Particulate debris from medical implants: mecha-nisms of formation and biological consequences[C]∥ASTM.Pennsylvania:ASTM committee F-4 on Medical and Surgical Materials and Devices, 1992.
[18]GIACCHI J V, MORANDO C N, FORNARO O, et al.Micro-structural characterization of as-cast biocompatible Co-Cr-Mo al-loys[J].Materials Characterization, 2011, 62(1): 53-61.
[19]GIACCHI J V, FORNARO O, PALACIO H.Microstructural evolution during solution treatment of Co-Cr-Mo-C biocompat-ible alloys[J].Materials Characterization, 2012, 68: 49-57.
[20]ZHUANG L Z, LANGER E W.Effects of cooling rate control during the solidification process on the microstructure and me-chanical properties of cast Co-Cr-Mo alloy used for surgical im-plants[J].Journal of Materials Science, 1989, 24(2):381-388.
[21]JOIAS R M, TANGO R N, DE ARAUJO J E J, et al.Shear bond strength of a ceramic to Co-Cr alloys[J].The Journal of Prosthetic Dentistry, 2008, 99(1): 54-59.
[22]LIU Z T, WANG B Y, WANG C, et al.Microstructure and mechanical properties of Al-Mg-Si alloy fabricated by a short pro-cess based on sub-rapid solidification[J].Journal of Materials Sci-ence &Technology, 2020, 41:178-186.
[23]YAMANAKA K, MORI M, CHIBA A.Influence of carbon ad-dition on mechanical properties and microstructures of Ni-free Co-Cr-W alloys subjected to thermomechanical processing[J].Jour-nal of the Mechanical Behavior of Biomedical Materials, 2014,37: 274-285.
[24]RODRIGUES W C, BROILO L R, SCHAEFFER L, et al.Powder metallurgical processing of Co-28% Cr-6% Mo for den-tal implants: physical, mechanical and electrochemical properties [J].Powder Technology, 2011, 206(3): 233-238.
[25]SHI Z M, YU Y Y, WANG Y Y, et al.Effect of nickel content on the processing and microstructure evolution of Co-Cr-Mo-Ni alloys[J].Materials Science and Engineering:A, 2019, 759:195-202.
[26]王杨洋, 石增敏, 李光宇, 等 .钴铬镍合金铸造过程的边界条件及胞晶生长[J].热加工工艺, 2021, 51(1): 50-55.
WANG Y Y, SHI Z M, LI G Y, et al.Boundary conditions and cellular crystal growth in casting process of cobalt-chromium-nickel alloy[J].Hot Working Technology, 2021, 51(1): 50-55.
[27]周玉 .材料分析方法[M].北京:机械工业出版社, 2006.
ZHOU Y.Analysis techniques in materials science[M].Beijing:China Machine Press, 2006.
[28]UNGÁR T, DRAGOMIR I, RÉVÉSZ Á, et al.The contrast factors of dislocations in cubic crystals: the dislocation model of strain anisotropy in practice [J].Journal of Applied Crystallogra-phy, 1999, 32(5): 992-1002.
[29]AGUILAR C, ORDONEZB S, GUZMANC D, et al.Mechani-cal alloying of Cu-xCr (x=3, 5 and 8wt.%) alloys[J].Journal of Alloys and Compounds, 2010,504(1): 102-109.
[30]TISONE T C.The concentration and temperature dependence of the stacking fault energy in face-centered cubic Co-Fe alloys[J].Acta Metall, 1973, 21: 229-236.
[31]RITTEL D, ROMAN I.Tensile fracture of coarse-grained cast austenitic manganese steels[J].Metallurgical Transactions A,1988,19(9): 2269-2277.
[32]RITTEL D, ROMAN I.Tensile deformation of coarse-grained cast austenitic manganese steels[J].Materials Science and Engi-neering: A, 1989, 110: 77-87.
[33]KAITA W, HAGIHARA K, ROCHA L A, et al.Plastic defor-mation mechanisms of biomedical Co-Cr-Mo alloy single crystals with hexagonal close-packed structure[J].Scripta Materialia,2018, 142: 111-115.
基 金 项 目 :水 电 机 械 设 备 设 计 与 维 护 湖 北 省 重 点 实 验 室 开 放 基 金(2020KJX01)
收稿日期:2022-04-19;修订日期:2022-06-17
通讯作者:石增敏(1973—),女,教授,博士,研究方向:超高强度钢的成形制造及高性能金属陶瓷材料的应用研究,联系地址:湖北省宜昌市大学路
8号三峡大学机械与动力学院(443002), E-mail:shzm@ctgu.edu.cn
无相关信息