航空发动机作为飞机的核心动力装置,为飞机提供源源不断的动力,需要在高温、高压、高转速恶劣环
境条件下长期反复服役,对飞机的性能、安全性和可靠性具有决定性的作用,其发展水平已经成为衡量一个
国家军事装备水平、科技工业实力和综合国力的重要标志。航空发达国家实施的综合化高性能涡轮发动机技
术计划(IHPTET )和先进核心军用发动机(ACME)计划,在高推重比,低耗油率,低成本航空发动机上
取得了很大进展[1-2] 。
材料是航空发动机发展的物质基础,是决定航空发动机现代化水平的关键因素之一。“一代材料、一代
发动机”,材料是航空发动机性能、耐久性、维修性和成本的决定性因素[3] 。近年来,新一代航空发动机
提出了更高的增压比、推重比和涡轮前进口温度,航空发动机性能指标的大幅提高,使得材料的服役条件越
加恶劣,因此对材料性能有着更加苛刻的要求,目前推重比为10的发动机涡轮进口温度已达1850K~1900K
,推重比12~15发动机涡轮进口温度超过2000K[4-5] 。为了满足先进航空发动机对材料越来越苛刻的要求
,高温、高强、低密度材料的研究不断加快,图 1 列出了部分不同温度下服役的先进材料。
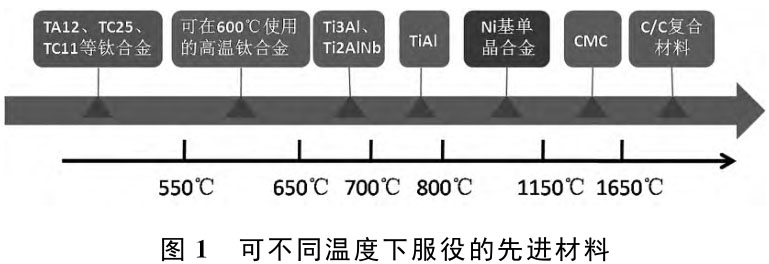
而航空发动机先进新材料要达到成熟应用必须走完材料研制和应用研究两个全过程。通过实际使用环境
下的考核验证,且性能稳定、可靠,即技术成熟度必须达到7~8级,才能在型号上应用[6] 。因此,能应
用在航空发动机上先进材料的研制周期非常长,为了确保型号的研制进度,往往需要提前开展关键技术的攻
关。所以有必要对可应用于航空发动机先进材料的发展情况进行研究分析,掌握国内外先进材料的研究和应
用情况,为发动机主机设计单位技术规划提供支撑,同时为材料研制单位进一步发展指明方向。
因此,本文对近年来航空发动机先进材料的国内外研究进展和应用情况进行分析总结,并结合航空发动
机型号和未来新一代先进航空发动机材料的需求,提出发展建议。
1、国内外研究进展
1.1 高温材料
为了进一步提升材料的性能,满足航空发动机零部件愈加苛刻的性能要求,于是材料科学家们开始通过
深入研究传统高温合金制造工艺来进一步挖掘材料的性能,如涡轮叶片采用单晶铸造工艺,涡轮盘采用粉末
冶金工艺等,应用这些工艺后传统高温合金性能得到了极大的提升,为三代航空发动机的研制提供了基础,
而材料性能已趋近极限,要满足新一代先进航空发动机对材料的要求,传统高温合金不再能满足于先进发动
机的发展,急需开展新材料及工艺研究,向着高比强度、高比刚度、抗氧化、耐腐蚀等新型材料发展[5] 。
1.1.1 陶瓷基复合材料
陶瓷基复合材料工作温度可达 1650℃ ,与镍基高温合金的性能比较如图2所示,与高温合金相比具有
更低的密度、更好的抗氧化性和更高的承温能力等优势。作为发动机热端部件材料不仅能实现减重、降低油
耗、提高涡轮前温度,而且能够承受极端高温环境下的应力要求,延长部件服役寿命[7] 。
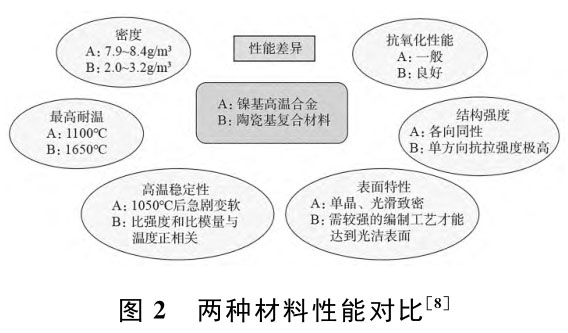
当前陶瓷基复合材料主要应用于发动机低压涡轮静子叶片、喷管等热端部件非转子组件,向着高压涡轮
叶片等服役环境更加恶劣的高温部件。国外经过四十年的发展, GE 、罗罗和 HyperTherm
HTC等公司针对陶瓷基复合材料在航空发动机热端部的应用开展了大量的研究工作,已成功应用于多款型航
空发动机并实现了工程化生产,并逐渐从低承力部件(尾喷管,火焰筒)发展到高承力部件(涡轮导向器叶
片和涡轮转子叶片)。国内陶瓷基复合材料的在材料研制和构件制备上开展了一系列的研究工作,具备了构
件研制和小批量生产能力,但是在航空发动机热端部件的应用研究尚属于起步阶段,仅部分静子件上开展了
试验考核[8-12] 。
陶瓷基复合材料由陶瓷基体、增强纤维和界面层构成,在陶瓷基体中通过引入纤维作为增强材料,即保
留了陶瓷材料的耐高温、抗氧化、耐磨耗、耐腐蚀等优点,同时纤维增强相的增韧机制使得材料对裂纹不敏
感,克服了陶瓷材料脆性大、可靠性低等缺点[13-14] 。陶瓷基复合材料构件制备流程可分为 4 个阶段,
如图 3 所示[15-16] 。
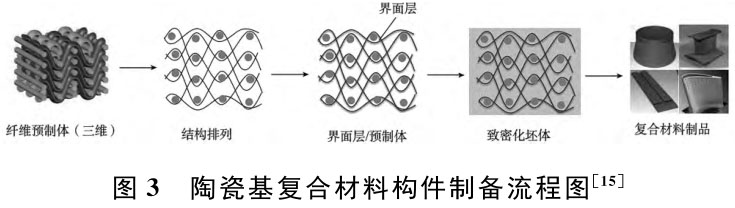
目前,应用最多的是碳纤维增强碳化硅陶瓷基复合材料,其综合性能优越,但是在燃气环境中长时间服
役需要借助环境热障涂层技术。环境障涂层结构致密,具有高的熔点、良好的表面稳定性、低的氧渗透能力
低等特点,除了能够抵抗环境腐蚀,同时还兼具阻碍及愈合裂纹和空隙的作用[17-18] 。相比美国等少数
国家掌握的连续纤维碳化硅陶瓷基复合材料产业化技术,中国陶瓷基复合材料的成形工艺和高性能纤维制备
技术与国外相比还有差距,局限了陶瓷基复合材料的批量生产。
1.1.2 碳/碳复合材料
碳/碳复合材料是一种新型的高温材料,具有低的密度(理论密度为 2.2g / cm2 )、低的热膨胀系
数、高的强度和良好的耐高温性能,同时还具有力学性能随温度的升高而升高的特点。将其应用于航空发动
机具有提高发动机推重比/功重比和热端部件工作温度等优点[19] 。
然而,碳在370℃空气中、在650℃水蒸气中、在750℃的CO2 中就会发生氧化[20] ,氧化使得碳/碳
复合材料结构疏松和不连续,从而使得力学性能大幅度的下降[21] 。较差抗氧化性能限制其应用,因此涂
层和基体改性等抗氧化技术被应用到了碳/碳复合材料中。目前国外在一定温度范围内的抗氧化技术已经较
为成熟,特别是多层涂覆技术已满足了 1700℃ 以上的抗氧化要求。
F100 航空发动机的喷嘴和加力燃烧室喷管均采用碳/碳复合材料进行制备。近年来,随着碳/碳复合
材料技术的发展,美国 LTV公司已生产出了碳/碳复合材料整体涡轮叶盘,并已完成地面超转试验。此外,
俄罗斯、德国、法国也已经生产出碳碳复合材料的涡轮转子外环、喷油杆等部件[19] 。
1.1.3 金属间化合物
金属间化合物是金属元素之间或金属元素与类金属元素之间通过共价键连接,具有良好的耐高温、耐磨
损和抗氧化性能的新型耐高温材料[22] 。目前在航空发动机上应用趋势较为明显的有 Ti-Al 系金属间化合
物。在 Ti-Al 系金属间化合物中,主要研究的是 Ti3 Al 合金、TiAl 合金以及 Ti2AlNb合金,其中 Ti3
Al 和 Ti2AlNb合金长期工作温度可达 650℃~700℃,而TiAl 合金工作温度则可达 760℃~800℃ 。采
用 TiAl 合金制造叶片可降低叶片零件
质量,实现系统的减重,同时显著降低轮盘载荷。目前 TiAl合金叶片主要采用精密锻造工艺制备,图4
为铸造TiAl合金与锻造 TiAl 合金及其它金属结构材料比强度的比较,通过锻造变形,可以大幅度提高
TiAl合金的塑性、强度和疲劳性能[23] 。图5为锻造TiAl合金叶片的工艺路线图。
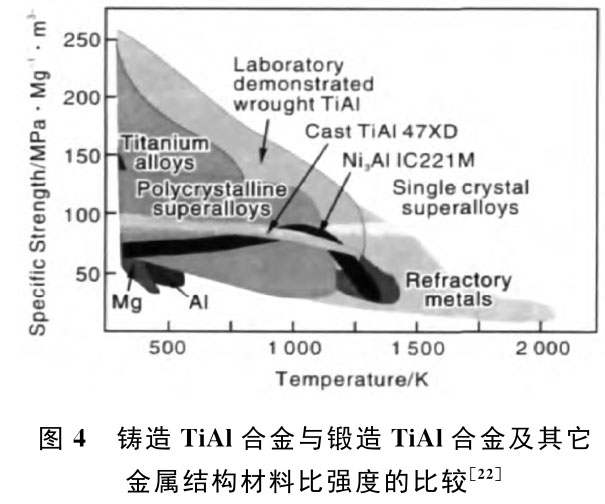
从 2000 年开始,国外开始采用锻造工艺制造 TiAl 合金叶片, ROlls- ROyce 公司研制了
锻造 TiAl 高压压气机 7 、8 、 9级叶片,并通过了发动机试车考核;普惠 PW1100G发动机第三级低
压涡轮叶片装备空客 A320NeO飞机,并于2014年9月首飞,如图6所示[24] 。国内,北京航空材料研究院
、西北工业大学、北京航空航天大学、南京理工大学、北京科技大学等在锻造 TiAl合金做了大量的研究工
作,尤其突破了大规格高纯净工业化铸锭制备、包套挤压开坯、矩形截面细晶挤压棒材制备、叶片等温模锻
、薄板包覆轧制、复杂构件超塑成形、叶片零件加工等一系列关键技术,逐步缩短与国外的差距。
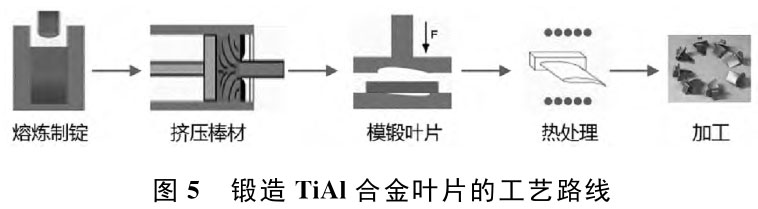
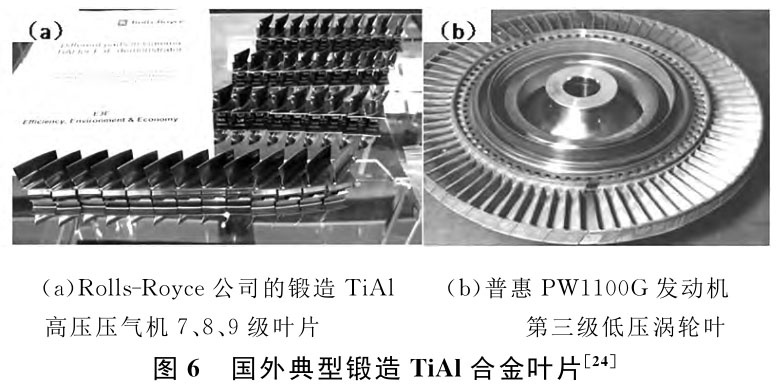
1.2 耐高温涂层材料
1.2.1 高温防护涂层材料
高温材料的应用可大大提高热端部件的高温强度,但新一代航空发动机涡轮进口温度进一步提高,已超
过了镍基单晶高温合金的熔点,高温合金的承温能力逐渐不能满足其需求,而采用高温涂层加冷却结构结合
,其使用温度可达到 1650℃以上,保证了发动机的可靠服役。因此,在材料表面涂覆抗高温性能优异的防
护涂层是提高热端部件的性能和延长寿命的有效措施之一。
目前,航空发动机高温防护涂层包括热障涂层、抗氧化涂层、内腔涂层等,对涡轮叶片内外表面进行防
护,涂层结构如图 7所示。热障涂层主要应用于涡轮叶片外表面,提高叶片材料的高温抗氧化腐蚀及隔热
;抗氧化涂层主要应用于涡轮叶片的外表面,提高叶片材料的高温抗氧化性能,同时还可以作为热障涂层的
金属粘接层,以改善热障涂层间的界面匹配性;内腔涂层主要应用于涡轮叶片的内腔,以提高内腔的高温抗
氧化性能[25] 。
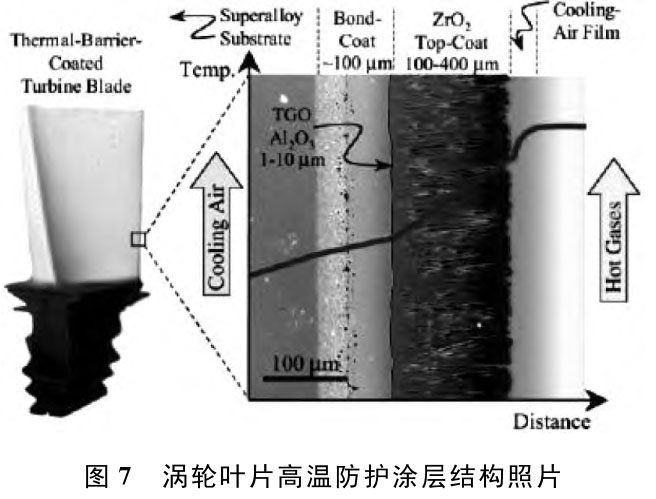
1.2.1.1 热障涂层
热障涂层的陶瓷层材料需要具有难熔、相稳定、化学惰性和低热导、高热反射率等重要物理化学特征,
同时要考虑其热膨胀系数与基体材料之间的匹配。 ZrO2 是目前应用广泛,综合性能较好的热障涂层材料
,它具有高熔点、化学稳定性耐和高温氧化等特点,但纯 ZrO 2 具有同素异晶转变,温度升高后由单斜
结构转变为立方结构,伴随着4%~6% 体积分数的变化而产生内部热应力,目前广泛使用 Y 2 O 3 作为
稳定剂,通过自由膨胀和收缩来释放中间粘结层与陶瓷层因热膨胀系数不匹配而产生的内部热应力,达到增
韧的效果,从而提高材料的抗热震性与寿命。20世纪80年代初,普惠公司成功地开发了PWA264第2代 热
障 涂 层,成 功 应 用 在 了JT9D 、 PW2000 、 PW4000 和V2500等发 动 机 涡 轮 叶 片 上,
截 至1992年,该 涂 层 用 于JT9D 、 PW2000 等发动机涡轮叶片上已经累计飞行了 400 万小时以上
[26-27] 。为了适应更高的温度要求,普惠公司又成功地开发了 PWA266第3代涡轮叶片热障涂层,涂层
制备工艺采用 EB-PVD ,应 用 至 JT9D-7R4、 V2500 、 F100-PW-229 和F119等发动机涡
轮叶片上,应用该涂层后, F119发动机高压涡轮工作叶片工作温度可提高150K左右[28-30] 。截至目前
国外应用于热障涂层的陶瓷层粉末和靶材技术已十分成熟,正在开展更低热导率的新型陶瓷材料、或者对现
役传统材料进行改进研究,以提高涂层的使用温度和隔热性能。
国内近十年来也开始自主研制喷涂用YSZ粉末,尤其是纳米YSZ粉末取得了一定的进展,然而国内自主研
制的喷涂用YSZ粉末还存在 Cl- 1含量偏高、杂质元素含量超标、造粒度均匀性差等问题,此外纳米YSZ
粉末还存在团聚前的原始晶粒度偏大、粉末的流动性、喷涂工艺性较差等问题,且批次一致性有待提高。
1.2.1.2 抗氧化涂层
目前报道获得应用的高温抗氧化涂层主要是 MCrA -lY (M 是 过 渡 族 金 属Ni 、 CO 、或
NiCO )和 PtAl 两 种。
MCrAlY涂层的抗氧化机理一般是通过高温氧化环境中,在表面首先形成 Al2O3 保护性氧化层以阻
止涂层的进一步氧化,达到保护基体的目的。国外对 MCrAlY 涂层的研究主要集中在改变成分含量以及
添加一些元素(Si 、 Ti、Ta 、 W 、 CO 、 Mo 、 Hf 、 Re )或氧化物以提高粘结层的抗氧化和耐热腐蚀
性能方面。 PtAl 涂层由于贵金属 Pt 的加入使得涂层在高温下保护膜的成膜性能更好,氧化膜自修复
性能更加突出。国外对PtAl粘结层材料的研究集中在Pt含量对其抗氧化性能的影响方面[31-34] 。
国内高温抗氧化涂层的承温能力、抗氧化性能与国外还存在差距。目前实际应用较多抗氧化涂层的是
MCrA -lY ,北京航空材料研究院、金属所、中国农业机械化科学研究院等单位先后研制了 MCr
AlX系涂层(NiCrAlY 、 NiCrAl-YSi 、 NiCOCrAlYTa和 NiCOCrAlY等)高温防护
涂层,用于发动机涡轮叶片的防护,并进入小批量生产阶段。国内在PtAl 涂层方面,还未开展 Pt 、
Al 的相对含量对抗氧化性能的影响研究,制备的 PtAl 粘结层抗氧化性能还有待提高。
1.2.1.3 内腔防护涂层
内腔防护涂层主要包括简单型铝化物涂层和改进型铝化物涂层两种。简单型铝化物涂层是在高温合金基
体上简单渗铝,具有良好的抗氧化性能,但其抗热腐蚀能力不足。近二十年来国外研究人员在简单型铝化物
涂层中加入少量 Cr 、 Si 、 Pt等元素,包括 Cr改性的铝化物涂层(Al- Cr涂层)、 Si改性的铝
化物涂层(Al-Si涂层)、 Pt改性的铝化物涂层(Pt- Al涂层)和稀土元素改性铝化物涂层(RE-Al涂层)
等改进型铝化物涂层,其具有比简单型铝化物涂层抗热腐蚀性能[35-37] 。
根据资料显示,美国 P&W 公司和 CFM 国际发动机公司生产的民用航空发动机涡轮叶片内腔均有
铝化物防护 涂 层,并 已 在 PW2000 、 PW4000-94 、 PW4000-100 、PW4000-112 、 PW4500
、 PW6000 、 PW8000 、 CFM56-3 、CFM56-5 、 CFM56-7等发动机型号上应用。
铝化物内腔涂层主要通过固体粉末渗、料浆渗、气相渗和化学气相沉积等工艺制备。化学气相沉积被认
为是制备内腔防护涂层最为理想的方法,美国完成了化学气相沉积工艺铝化物沉积过程反应中间体生成控制
等关键技术突破,有效地实现了叶片内腔的防护, GE 公司和英国 R-R23公司采用化学气相沉积工艺制
备涡轮叶片内腔铝化物涂层用于装备 GE90 、 GE90-115B 、 RB211-535 、BR700发动机。
与国外相比较,国内在叶片复杂内腔防护涂层技术成熟度仍需进一步提高,内腔涂层的均匀性、防护性
能等存在较大差距。采用的涂层工艺技术以传统的包埋渗、料浆渗和气相渗为主,化学气相沉积技术应用于
叶片内腔涂层制备的研究工作处于研制阶段。
1.2.2 耐高温隐身涂层材料
航空发动机作为作战飞机重要的雷达散射源和红外辐射源,其后腔体及其内部件、边缘等的雷达散射信
号和后腔体及其热端部件、尾喷流等的红外辐射信号占整个飞机尾部特征信号的 95% 以上,因此发动机隐
身性能严重影响着飞机的作战能力和生存率。耐高温隐身涂层作为飞行器高温隐身工程化应用的主要技术途
径,具有对飞行器外形影响小、工艺简单、成本较低与可靠性高等优点。
耐高温隐身涂层包括耐高温红外、雷达及兼容涂层等,用于低压涡轮叶片、整流支板、混合器、内锥体
、喷管唇口等部位,通过降低目标的红外辐射和缩减目标的雷达散射截面达到隐身的效果。
传统的红外低发射率涂层不能满足发动机苛刻的使用环境,新型材料如金属粉体涂层、金属薄膜以及无
机涂层逐渐成为国外开展耐高温红外隐身涂层的研究方向,其中金属微粉(主要包括锌、铝、铁、镍、铜以
及银、金、铂等金属材料)来源广,效果好,是低发射率涂层中最常用的功能填料之一,可以实现 3μ m~
5 μ m 和 8 μ m~14 μ m 波段的全波段红外低发射率效果[38-40] 。
耐高温雷达吸波材料是由基体材料和耐高温吸收剂所组成,通常将耐高温吸收剂分散在基体材料中,承
担吸波功能。国外研究及应用较多的是耐高温介电损耗吸波材料,基体主要 分 为 陶 瓷 基 体(Si3 N 4
、 Al 2 O 3 、 AlN 、莫 来石、 ZrO2 等)和玻璃基体(磷酸盐、 Li 2 O-Al 2 O 3-SiO 2 、 Li
2 O -B 2 O 3-SiO 2 、 MgO-Al2O 3-SiO 2 )两大类;而耐高温吸收剂主要有 SiC 、 Si3 N 4 、
钛酸钡、硼硅酸铝、乙炔炭黑、碳纳米管、纳米 Si-C-N 、 Si-C-O 、 Si-C-Fe 等[41-42] 。
目前实现材料雷达/红外兼容隐身主要有两种技术途径:一是材料本身具有雷达波高吸收、红外低辐射
特性(单一型雷达/红外兼容隐身材料);二是利用结构设计将雷达隐身材料和红外隐身材料复合,复合后
可维持材料的雷达与红外隐身性能保持不变或变化不大(复合型雷达/红外兼容隐身材料)。但由于雷达隐
身与红外隐身的机理有所不同,材料红外发射率的降低与雷达波吸收能力的提高存在着一定矛盾,使得它们
性能相互制约,因此单一型雷达/红外兼容隐身材料的雷达、红外隐身性能相对有限,目前发展最 多 的
复 合 型 雷 达/红 外 兼 容 隐 身 材 料,如 英 国BTRRLC 公司、澳大利亚国防科技组织的材料
研究室、德国 PUSH GUNTER以及瑞典巴拉居达公司均研制在新一代雷达/红外兼容隐身涂层技
术取得了很大进展。
国外新一代先进战机用发动机均采用了隐身涂层技术,如美国 F-22 、 F-35 、 F-117A 、 B-2
以及法国幻影-2000战机。国外耐高温隐身涂层技术发展较早,多种涂层均实现了工程化应用,涂层及制备
技术都较为成熟。相比国外,中国的耐高温涂层技术发展较晚,在现实应用中还存在较多问题,如雷达吸波
涂层的低频隐身性能较差,涂层厚度过厚,耐腐蚀性能不足等问题突出。
1.3 中低温材料
1.3.1 钛合金
先进航空发动机钛合金用量约 30%~40% ,钛合金主要用于制造航空发动机压气机叶片、盘和机匣等
零部件,代替钢和镍基合金减重效果可达到40%左右,显著提高推重比和工作效率。
目前在中国航空发动机上获得应用的主要是 α+ β 型钛合金,具有良好的热加工性能,同时在中温
环境下又有良好的综 合 性 能,工 作 温 度 大 多 在 500℃ 以 下,其 中 在400℃ 以下的钛合金主要
有 TC4 、 TC6 、 TC17 ,应用于发动机工作温度较低的风扇叶片和低压压气机叶片,500℃ 左右工作的
钛合金有 TC11 、 TC25 、 TA15和 TA7合金,其中TC11 是中国目前航空发动机上用量最大的钛合金
[43-44] 。
随着发动机零部件温度的要求越来越高,发展了能在600℃使 用 的 钛 合 金,如 Ti60 以 及 国 外
的 IMI834 、 Ti-1100 、 BT36 、 BT41等,国外600℃钛合金获得了广泛的应用,例如IMI834
广泛应用于 EJ200发动机高压压气机第3级整体叶盘和隔圈、 F119发动机高压压气机后机匣等。
钛合金的发展趋势如图 8 所示,使用温度越来越高,钛合金强化技术从固溶强化向有序强化发展,并
进一步向SiC纤维复合强化发展,国内、欧美和俄罗斯在不同温度段对应的牌号如表 1 所示[44] 。
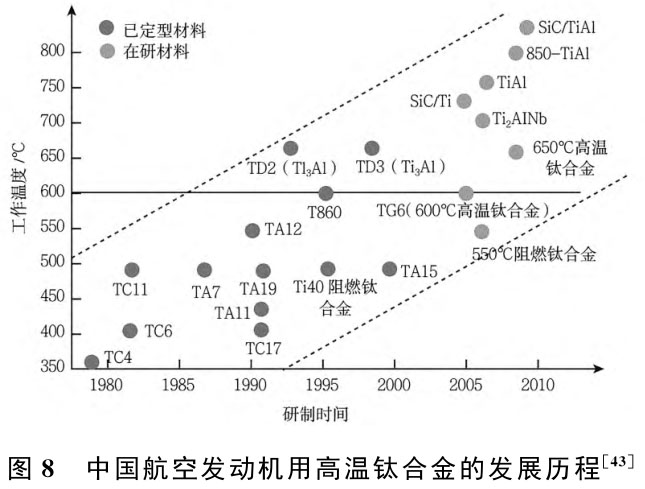
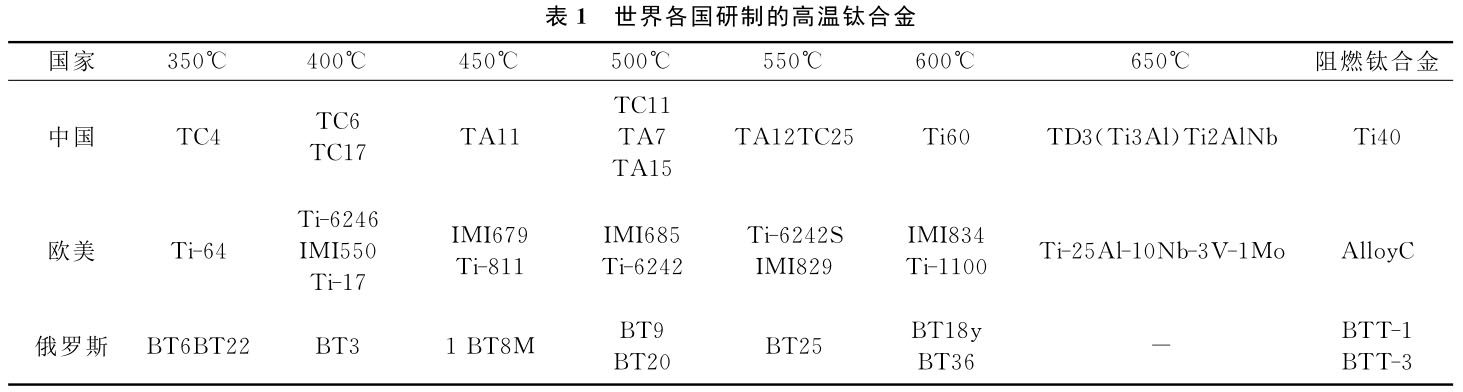
1.4 树脂基复合材料
树脂基复合材料具有高的比强度和比模量、疲劳性能和耐腐蚀性能好等特点,已在多型航空发动机的风
扇叶片、风扇机匣、外涵机匣等部件上得到成熟应用,并朝着结构形式更优、材料性能更高、制造成本更低
、自动化程度更高的方向发展,相比于钛合金材料,采用树脂基复合材料减重效率提高了 25% 以上[45-
46] 。树脂基复合材料包括增强材料和树脂基体,其中增强材料有碳纤维、玻璃纤维、 Kevlar纤维
等,树脂基体有环氧、聚酰亚胺、双马等。表2为树脂基复合材料在国外航空发动机上的主要应用情况,主
要用于发动机风扇叶片、机匣、出口导流叶片等部件[47-52] 。当前航空发动机用树脂基复合材料主要为
碳纤维增强树脂基复合材料。经过几十年的技术攻关和发展,国内也形成了高韧性、耐高温复合材料体系及
热压罐和树脂传递模塑(RTM )制造技术体系,图9为国内航空碳纤维复合材料发展历程[53-56] 。
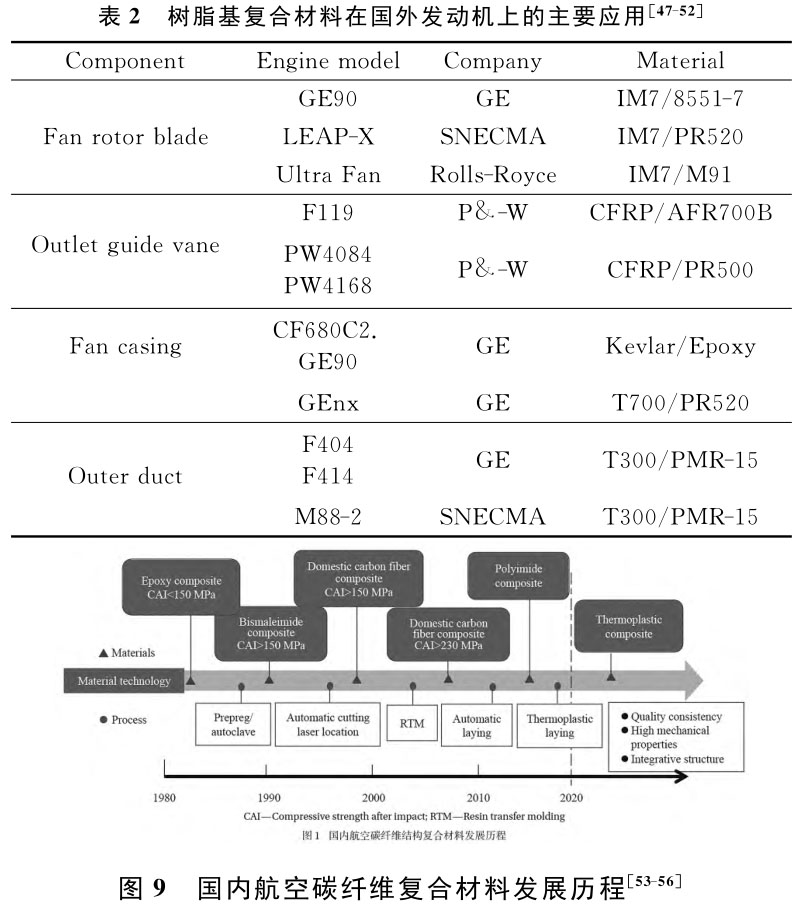
在先进碳纤维和树脂的研制上,国内已经初步建立了国产碳纤维技术与评价体系,并成功研制了达到
T300 /T700 / T800 级碳纤维,国产 T300/T800 级碳纤维实现了在航空发动机上的考核和应用,
图10为国内外部分碳纤维的基本 力 学 性 能,国 内 先 进 树 脂 长 期 使 用 温 度 突 破350℃ ,韧
性 CAI 达到 300MPa 以上,其中耐高温聚酰亚胺基体在航空发动机上得到了大量的应用[57-59] 。
国内外部分树脂基复合材料的使用温度和冲击后压缩强度(CAI )如图11所示,向着高温性能和高的冲击
后压缩强度(CAI )发展,高的 CAI值可获得更高的减重效率和损伤 安 全 性 能[58-60] 。 发 展 能 够
长 期 使 用 温 度 达 到350℃以上,同时要求具有良好的热氧化、稳定性和成型工艺性能的树脂基复合材
料是满足新一代高推重比航空发动机服役温度和整体结构成型必要要求。
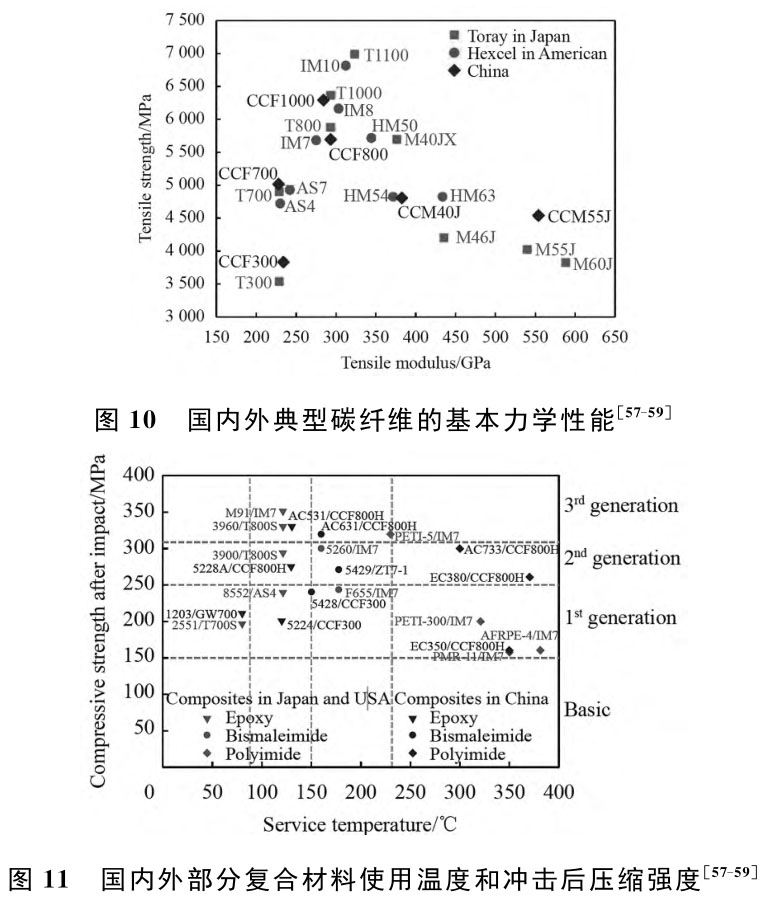
2、发展趋势与展望
一代新材料的出现支撑了一代新装备的研发,一代新装备的研制牵引一代新材料的应用。经过数十年的
发展,中国航空发动机材料技术取得了快速的进步,逐渐从引进、仿制走向自主研制,从上文对航空发动机
新材料国内外研究进展的分析看,中国在先进复合材料、金属间化合物、高温钛合金、涂层等先进高、中、
低温材料的研究上取得了一系列的研究进展,逐渐缩短了和欧美发达国家的差距,但材料的成熟度还不高,
很多关键技术成熟度亟待优化,导致产品合格率较低,且型号应用研究和考核不充分。
此外,随着中国军用航空发动机向着更加复杂严苛服役环境的转变,以及未来先进航空发动机的研制需
求,目前航空发动机材料技术储备尚不能满足高推重比高可靠发动机发展的迫切需要,特提出如下展望:
(1 )随着中国军事实力的增强,航空发动机的服役环境开始由原本单一的内陆环境向复合极端环境转
变,其中,“高温、高湿、高盐雾”的海洋环境带来的航空发动机腐蚀问题已经严重制约发动机性能的充分
有效发挥,而中国航空发动机的腐蚀防护技术,尤其是中低温防护技术(包括不锈钢及焊接部位、压气机钢
叶片、可磨耗封严涂层等)亟待提升,所采用的工艺无法满足长期使用要求,急需开展先进的腐蚀防护涂层
和表面处理工艺研究;同时国内发动机主干材料和涂层在典型服役环境下的腐蚀性能数据匮乏,造成在恶劣
环境下发动机零部件的寿命预测存在瓶颈,急需开展主干材料及表面防护在典型服役环境下的耐腐蚀能力及
性能衰减研究,搭建材料-连接件/模拟件-零件/组件-整机的积木式腐蚀试验验证体系。此外,为了保证
发动机在真实环境下的长期稳定可靠服役,持续开展外场服役腐蚀数据收集,不断迭代腐蚀防护与控制设计
。
(2 )目前四代战斗机及未来的先进战机对发动机提出了较高的隐身性能指标,发动机是飞机主要的红
外辐射源,也是后向主要雷达散射源,其隐身隐身性能严重影响飞机的作战能力和生存率。随着国内耐高温
红外、雷达及兼容涂层等耐高温隐身涂层材料的不断工程化应用及验证,涂层脱落、维护困难、成本高昂等
问题不断凸现,以及飞机方对红外雷达技术指标要求的不断提高,更耐温、更薄、更轻、宽频谱、可维修性
等更高要求的隐身涂层和针对不同服役环境、不同结构的隐身构件材料及制备工艺的需求更加迫切。此外,
隐身涂层的维修/维护和性能检测技术也需同步开展研究,为型号全寿命周期的隐身能力提供保障。
(3 )随着中国航空发动机材料技术的不断发展,材料品类日趋齐全,建立了符合中国国情的材料体系
,但与欧美等发达国家相比,中国发动机材料技术基础不够雄厚,材料全面性能数据匮乏,尚不能满足在役
、在研先进航空
发动机研制生产的迫切需求,主要存在以下问题:
1 )部分关键工艺成熟度有待提高,比如金属材料返回料回收利用技术、合金纯净度控制技术、组织均
匀性及批次稳定性控制、大型复杂构件精密制造技术等;
2 )部分关键和重要件材料级、毛料级及零部件级材料性能数据缺乏,在支撑强度寿命仿真计算中凸显
不足,直接影响关重件强度及寿命可靠性的评估,有必要对关重键材料进行全面性能数据补充测试,建立起
可实现数据对比、数据推送、数据交互等功能的现代化全面性能数据库;
3 )加强材料-结构一体化设计研究,如按照复合材料各向异性的设计思想去开展零件结构设计;根据承
载和隐身指标开展结构隐身一体化构件的设计等,建立起一体化结构件设计准则;
4 )先进材料的应用成熟度不高,为满足新一代航空发动机对先进材料的需求,需开展先进复合材料、
金属间化合物、高温/耐蚀防护涂层、高温钛合金等新材料的工程化应用研究,提高材料和制造技术的成熟
度,为先进航空发动机的研制提供技术储备。
参考文献:
[1]焦华宾,莫松 . 航空涡轮发动机现状及未来发展综述[J] .航空制造技术, 2015 (12 ): 62-
65.
[2]傅恒志.未来航空发动机材料面临的挑战与发展趋向[J] .航空材料学报, 1998 , 18 (4 ):
52-61.
[3]刘大响.一代新材料,一代新型发动机:航空发动机的发展趋势及其对材料的需求[J] .材料工程
, 2017 , 45(10 ): 1-5.
[4]袁睿豪,廖玮杰,唐斌,等.数据驱动的航空发动机材料设计研究进展[J] .航空制造技术,
2021 , 64 (18 ): 22-30.
[5]付青峰,杨细莲,刘克明.航空发动机高温材料的研究现状及展望[J] .热处理技术与装备,
2018 , 39 (12 ): 69-73.
[6]益小苏,李兴无,苏彬,等 . 航空发动机材料技术学科发展研究[C] .2014- 2015航空科学技术
学科发展报告, 2016.
[7]张小锋 .PS-PVD 制备 Yb2SiO5 环境障涂层及水蒸气腐蚀性能研究[C]第九届国际稀土开
发与应用研讨会暨2019 中国稀土学会学术年会 .北京,2019.
[8] ROBINSON R C , HATTON K S.SiC / SiC leading edge
turbine airfOil tested under Simulated gas turbi
ne COndiTiOns :NASA / CR-1999-209314 [M] .Cleveland : NaTiOnAl
AerO -nauTics and Space Ad-ministraTiOn , Glenn Rese
arch Center ,1999.
[7]杨金华 ,董禹飞 ,杨瑞 ,等 .航空发动机用陶瓷基复合材料研究进展 [J] .航空动力 ,
2021 (5 ): 56-59.
[8]王恒 ,张帆 ,傅正义 . 先进陶瓷及陶瓷基复合材料 :从基础研究到工程应用 一 先进陶瓷及陶
瓷基复合材料分论坛侧记 [J] . 中国材料进展 , 2019 , 38 (10 ): 940-941.
[9]刘巧沐,许建锋,刘佳.碳化硅陶瓷基复合材料基体和涂层改性研究进展 [J] . 硅酸盐学报,
2018 , 46 (12 ): 1700-1706.
[10]陈智勇,刘建寿,徐颖强,等 .碳纤维增韧碳化硅陶瓷基复 合 材 料 界 面 相 的 研 究 进 展
[J] . 陶 瓷 学 报 ,2019 , 40 (6 ): 701-709.
[11]左平,何爱杰,李万福,等 . 连续纤维增韧陶瓷基复合材料的发展及在航空发动机上的应用[J
] . 燃气涡轮试验与研究,2019 , 32 (5 ): 47-52.
[12]刘巧沐,黄顺洲,何爱杰 .碳化硅陶瓷基复合材料在航空发动机上的应用需求及挑战 [J] .材料
工程 ,2019 , 47 (2 ): 1-10.
[13]刘鑫,乔逸飞,董少静,等 .SiC / SiC 陶瓷基复合材料涡轮导叶热疲劳试验研究与损伤分析
[J] . 燃气涡轮试验与研究,2020 , 33 (4 ): 26-30.
[14]陈志英,汪宇峰,刘勇,等 . 基于封严间隙的涡轮盘篦齿综合优化设计[J] .航空发动机,
2019 , 45 (5 ): 19-25.
[15]江舟,倪建洋,张小锋,等.陶瓷基复合材料及其环境障涂层 发 展 现 状 研 究[J] .航 空 制
造 技 术,2020 , 63(14 ): 48-64.
[16]陈明伟,谢巍杰,邱海鹏.连续碳化硅纤维增强碳化硅陶瓷基复合材料研究进展[J] . 现代技术
陶瓷, 2016 ,37 (6 ): 393-402.
[17]邹豪,王宇,刘刚,等.碳化硅纤维增韧碳化硅陶瓷基复合材料的发展现状及其在航空发动机上
的应用[J] . 航空制造技术, 2017 , 60 (15 ): 76-84 , 91.
[18]黄璇璇,郭双全,姚改成,等.航空发动机 SiC /SiC复合材料环境障碍涂层研究进展[J] .
航空维修与工程,2017 (2 ): 28-31.
[19]李贺军,罗瑞盈,杨峥 . 碳/碳复合材料在航空领域的应用研究现状[J] . 材料工程, 1997
(8 ): 8-10.
[20] Sheehan J E , Buesking K W , Sullivan B J.Ca
rbOn -carbOn COmpOSites [J] .AnnuAl Review OfMateriAlsSc
ience , 1994 , 24 (1 ): 19-44.
[21]付前刚,李贺军,史小红,等.沉积位置对化学气相沉积 SiC 涂层微观组织的影响[J] .西安
交通大学学报, 2005 , 39 (1 ): 49-52.
[22]吴建鹏,朱振峰,曹玉泉 . 金属间化合物的研究现状与发展[J] .热加工工艺, 2004 (5 ):
41-43.
[23] China AerOnauTicAl MateriAls HandbOOk EditOriAlBO
ard (中国航空材料手册编委会) .China AerOnauTi-cAl MateriAls Han
dbOOk (中国 航 空 材 料 手 册)[M] .Beijing : AviaTiOn Industry
Press , 2006.
[24] Alan Gilchrist , Tresa M POllOck.Cast Gamma Ti
tani -um AluminidesFOr LOw Pressure Turbine Blade
: ADeSign Case Study FOr ntermetAllics [C] .2001.War -
rardAle : TMS , 2001 : 1-11.
[25]李铁藩.材料的高温氧化与防护[J]材料保护, 1990 ,23 (1-2 ): 19-22.
[26]文生琼,何爱杰,王皓.热障涂层在航空发动机涡轮叶片上的应用[J] .燃气涡轮试验与研究,
2009 (22 ): 59-62.
[27]牟仁德,陆峰,何利民,等.热障涂层技术在航空发动机上的应用与发展[J] . 热喷涂技术,
2009 (1 ): 53-8.
[28]周宏明,易丹青,余志明,等.热障涂层的研究现状与发展方向[J] . 材料导报, 2006 , 20
(3 ): 4-8.
[29]付超,孔维凯,廖文俊,等 . 应用于燃气轮机的热障涂层技术的研究现状[J] . 装备机械,
2014 (3 ): 16-22.
[30] Vaen R , JarligO M O , Steinke T , et Al.Overvi
ewOn advanced thermAl barrier COaTings [J] .Surface &
COaTings TechnOlOgy , 2010 , 205 (4 ): 938-42.
[31] LOnga Y , TakemOtO M.IR-laser treatment Of the
rmAlsprayed MCrAlY COaTings and their high temperat
ureCOrrOSiOn behaviOr [J] .MateriAls and Manufacturing
PrOcesses , 1995 , 10 (2 ): 217-227.
[32] Liang Y P , ZhOu Z R , Cheng J M , et Al.Laser
remelTingOf NiCOCrAlY clad COaTing On superAlIOy [J] .S
urface andCOaTings TechnOlOgy , 1996 , 79 (1-3 ): 131-134.
[33] DragOs U , Gabriela M , WAltraut B , et Al.ImprO
ve -ment Of the OxidaTiOn behaviOur Of electrOn bea
mremelted MCrAlY COaTings [J] .SOlid State Sciences ,
2005 , 7 (4 ): 459-464.
[34] Utu D , Brandi W , Marginean G , et Al.MOphOlOgy
and phase mOdificaTiOn Of HVOF sprayed MCrAlY -COaTin
gs remelted by electrOn beam irradiaTiOn [J] .Vacu
um , 2005 , 77 (4 ): 451-455.
[35]潘刚.熔烧型料浆法制备 Al-Si涂层的应用研究[J] .热加工工艺,2006 , 10 (1 ): 28-30.
[36] H He.MicrOstmcture and hOt COrrSiOn behviOr Of
CO -Si mOdifed Aluminide COaTings On nickel based sup
erAl -lOys [J] .COrrOSiOn science , 2015 , 100 : 466-473.
[37] COsta W Da , GleesOn B , et Al.COdepOSited chrOmi
-um-Aluminide COaTings II.KineTics and mOrphOlOgy OfCO
aTing grOwth [J] .JOumAl Of the ElectrOchemicAlSOciet
y.1994 (10 ): 2690-2698.
[38]翁小龙,张捷,刘孝会.热红外低辐射率涂料的研制[J] .表面技术, 2001 , 30 (4 ): 36-
38.
[39]李新华,陈雷,孟晓雄,等.国外涂料型红外隐身材料研究现状和发展方向分析[J] .红外技术,
1994 , 16(1 ): 5-11.
[40] FULGHUM D A , WAlL R.New steAlth COaTingsbOOst
B-2perfOrmance [J] .AviaTiOn Week and SpaceTechnOlOgy
, 2000 , 153 (21 ): 53-54.
[41]刘毅,魏世丞,童辉,等.热喷涂制备吸波涂层的研究进展[J] .材料工程, 2014 (9 ): 106
-112.
[42]李斌玲,谢国治,宋晓龙,等.多层雷达波段吸波涂层的研究现状及展望[J] .河海大学, 2011
, 39 (4 ): 464-469.
[43] VAlenTin N MOiseyev.Titanium AllOys : RusSian Air
-craft and AerOspace ApplicaTiOns [M], New YOrk :Tay
lOr & Francis GrOup , 2006.
[44]黄旭,李臻熙,高帆,等.航空发动机用新型高温钛合金研究进展[J] . 航空制造技术, 2014
, 7 : 70-75.
[45] PATERRH , CURTOPA.Advanced materiAls fOrspace
applicaTiOns [J] .Acta AstrOnauTiOn , 2007 , 61(11 / 12 ): 1121-
1129.
[46]焦泽辉,于慧臣,吴学仁,许瑞达,武亮亮 . 激光选区熔化 TC4钛合金的室温及高温拉伸各向异
性与断裂机制研究?[J] . 材料导报 .2023 (S2 ) .
[47]赵云峰,孙宏杰,李仲平 . 航天先进树脂基复合材料制造技术及其应用[J] . 宇航材料工艺
, 2016 , 46 (4 ): 1-7.
[48]梁春华,李晓欣.先进材料在战斗机发动机上的应用与研究趋势[J] . 航空材料学报, 2012 ,
32 (6 ): 32-36.
[49]陈巍 . 先进航空发动机树脂基复合材料技术现状与发展趋势[J] . 航空制造技术, 2016 (5 )
: 68-72.
[50]沈尔明,王志宏,滕佰秋,等.先进树脂基复合材料在大涵道比发动机上的应用[J] .航空制造
技术, 2011 (17 ): 56-61.
[51]陈亚莉 . 复合材料在民用航空发动机上的应用[J] . 国际航空,2012 (10 ): 54-55.
[52]李军,刘燕峰,倪洪江,等 . 航空发动机用树脂基复合材料应用进展与发展趋势[J] .材料工
程, 2022 (6 ): 49-60.
[53]陈祥宝 . 先进复合材料技术导论[M] . 北京:航空工业出版社,2017.
[54]马金瑞,黄峰,赵龙,等.树脂传递模塑技术研究进展及在航空领域的应用[J] .航空制造技术
, 2015 (14 ): 56-59.
[55]唐见茂.航空航天复合材料非热压罐成型研究进展[J] .航天器环境工程, 2014 , 31 (6 ):
577-583.
[56]邢丽英,李亚锋,陈祥宝.先进复合材料在航空装备发展中的地位与作用[J] .复合材料学报,
2022 , 39 (9 ): 4179-4186.
[57]包建文,钟翔屿,张代军,等.国产高强中模碳纤维及其增强高韧性树脂基复合材料研究进展[
J] .材料工程, 2020 ,48 (8 ): 33-48.
[58]包建文,蒋诗才,张代军.航空碳纤维树脂基复合材料的发展现状和趋势[J] .科技导报, 2018
, 36 (19 ): 52-63.
[59]邢丽英,蒋诗才,周正刚.先进树脂基复合材料制造技术进展[J] .复合材料学报, 2013 , 30
(2 ): 7-15.
[60]邢丽英,冯志海,包建文,等.碳纤维及树脂基复合材料产业发展面临的机遇与挑战[J] .复合
材料学报,2020 , 37 (11 ): 2700-2706.
无相关信息