难熔金属钼具有高导热性、良好的导电性及热稳定性等优点。钼靶材溅射薄膜, 主要应用于TFT-LCD 屏幕的薄膜晶体管,能够瞬间控制个体图像点(像素),从而确保显示屏的图像质量[1-2]。但纯钼靶材溅射出的薄膜在耐腐蚀性(变色)和密着性(膜的玻璃)方面存在问题,国外研究中通过在钼靶材中加入铌元素,可使溅射后薄膜的比阻抗、应力、
耐腐蚀性等各种性能达到均衡。因此, 钼铌用于极耐腐蚀的触摸屏ITO 传感器金属接线,表现出优异的性能。钼铌靶材是一种附加值和技术要求都较高的钼深加工产品, 触摸屏的快速发展使得钼铌靶材有着巨大的市场需求和发展空间[3-4]。

随着市场的竞争日趋激烈, 客户对钼铌合金靶材的品质要求愈来愈高,主要指标氧含量愈来愈低,密度接近钼铌合金的理论密度,因此,烧结态的钼铌合金靶材无法满足客户要求, 在烧结保证氧含量的前提下, 钼铌合金靶材需要经过压力加工方能接近理论密度。钛靶材生产厂家-凯泽金属结合研究钼铌合金的轧制工艺及主要的轧制影响因素,通过对有关资料文献整理,分享如下。
1、试验
1.1 试验原料
采用前期不同的粉末冶金工艺制备了4 种单重为1kg 钼(90%)铌合金板坯,主要指标参数见表1。
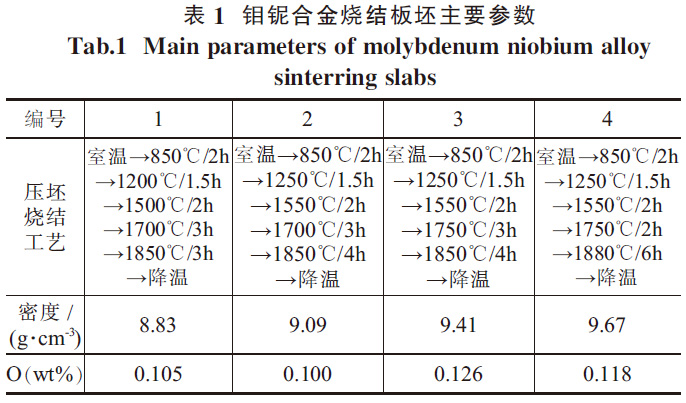
图1 为4 种烧结板坯的断口形貌。从图1(a)可以看到,断口中孔洞较多,不仅在晶界上存在明显的烧结孔,在晶粒内部也存在大量的烧结孔;从1 号到4 号随着制品密度的增加,制品内部孔洞逐渐减少;图1(d)中孔洞最少,仅在晶粒表面有少量存在,且较为均匀。
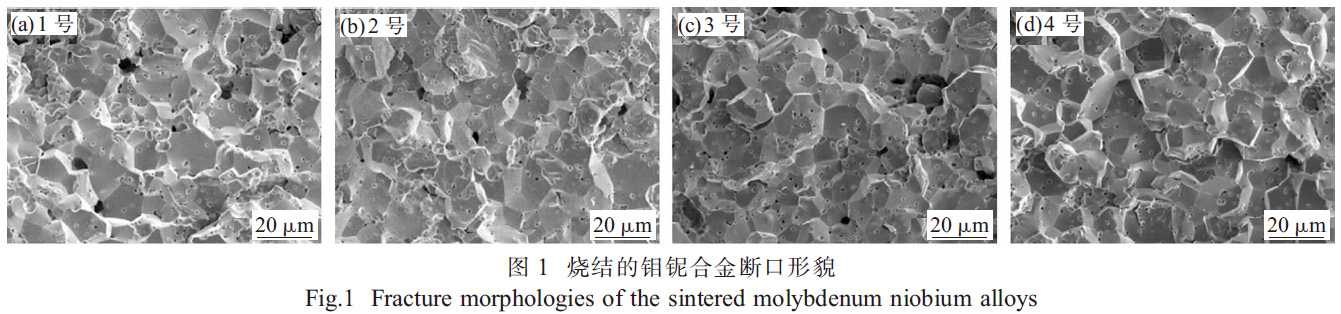
1.2 试验方法
钼铌合金靶材经过轧制后, 在较大的道次压下量下密度增大, 晶粒变小。试验通过调整轧制工艺参数(不同温度和不同变形量),研究各种因素对钼铌板坯轧制成形的影响。轧制用传统的二辊轧机进行,坯锭及板材高温加热炉为钨丝(发热体)电炉,在H2 气氛保护中加热。为保证得到细晶粒组织,在1300~1400℃变形时, 每道次变形量要大于15%。
钼板坯在高于1500℃变形时,晶粒都会明显长大。
钼铌合金板坯的轧制工艺为: ①第一火开坯温度(1300~1400)℃×1 h,变形量为15%~30%;②第二火加热温度(1200~1400)℃×30 min, 变形量为10%~20%;③第三火加热温度(1100~1350)℃×20min, 变形量为7%~15% ; ④第四火加热温度(1000~1300)℃×10min,变形量为10%~13%。
2、结果和分析
在轧制过程中,随着开坯轧制的开始,轧件在轧制力作用下发生塑性变形,产生加工硬化。在后续的热轧、温轧中,通常一次加热后进行多道次轧制,加工产生的硬化和回复再结晶的软化两相反过程同时存在,即发生动态回复和动态再结晶。开坯后随轧制的进行,轧件厚度不断变薄,变形量增大,自身储存能力增加,再结晶驱动力大,从而使轧件的再结晶温度降低。因此开坯后的热轧、温轧的加热温度随变形程度的增加逐次降低。这有利于保持加工态组织,使轧件只发生回复而避免再结晶组织的形成, 保证产品的质量和性能。
2.1 坯料的密度对轧制板材的影响
不同密度钼铌合金板坯轧制工艺如表2 所示,轧制后板材的实物照片如图2 所示。从轧制结果来看,4 号样板坯轧制后的板材中间部分没有开裂,边部有少量的开裂,2、3 号板坯轧制时出现了不同程度的开裂,且随着密度的降低开裂程度越大,1 号板坯轧制时几乎碎成多块。
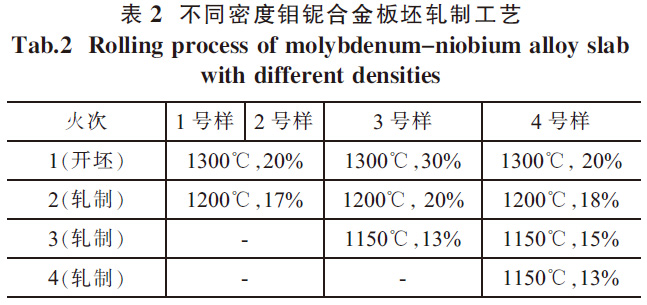
板坯密度不同是由于烧结态的钼铌合金板坯晶内存在不同程度的孔洞而表现出的物理性质, 因为钼粉和铌粉的颗粒大小存在很大的差距, 铌粉颗粒的实际大小是钼粉颗粒的近十倍, 这样在相同的压制烧结工艺下, 不同颗粒的变形和烧结过程的差异会导致压坯和烧结坯组织不均匀, 产生晶粒度不理想等缺陷, 甚至在烧结坯中会出现孔洞、裂纹等缺
陷,如图1 所示,这种坯料在后续轧制过程中很容易出现开裂甚至断裂等现象。
图1 的1 和2 号样存在大量明显孔洞, 很容易在孔洞处产生裂纹源,轧制过程中导致晶界失稳。孔洞越多,发生失稳越严重,因此经过初始轧制,板坯未致密就已经开裂。从金属塑性变形全过程得知,塑性变形过程和断裂过程是同时发生的, 从力学角度看,多晶体金属在外力的作用下发生塑性变形,初始阶段并不是在所有晶粒内同时发生变形, 而是首先在位向有利的晶粒中以滑移或孪晶等方式发生塑性变形。为了保证各晶粒间变形的连续性,要求在一个晶粒内的滑移带可以穿过晶界而传播到位向比较有利的晶粒,并且晶粒要有多种变形方式,以保证塑性变形能不断进行。一旦晶粒内的变形方式不能满足塑性变形连续性的要求,即塑性变形受阻或中断,则在严重变形不协调的局部区域将造成裂纹生核。如果裂纹核出现后还不能以形变方式来协调整体形变的连续性,则裂纹核将长大和扩展。
从位错理论的观点看: 金属的塑性变形实质上是位错在滑移面上的运动和不断增殖的过程。塑性变形受阻意味着运动的位错遇到某种障碍, 形成各种形态的位错塞积, 结果在塞积位错前端形成一个高应力集中区域。如果在应力集中区域所积累的应变能足够大,足以破坏原子结合键时,便开始裂纹生核。当裂纹长大到临界尺寸时,裂纹尖端的能量释放
率达到裂纹扩展单位面积时所吸收的能量, 裂纹便开始失稳扩展直到最终断裂。图1 中3 号样,在经过两火轧制后,没有发现明显裂纹,板坯已近致密化,但经过三火轧制,板坯边部出现开裂裂纹迅速长大。
2.2 氧元素对轧制板材的影响
根据金属断裂的基本理论, 发生断裂主要取决于晶界的状态,按照晶体学的观点,晶界本身就是晶体中的一种缺陷,是高位错密度区域,也是原子键合力薄弱的环节。如果在晶界发生杂质原子的偏析,析出脆性第二相或出现合金元素的脱溶, 必将导致晶界表面能下降,很容易沿晶界发生破坏。因此,考虑到钼铌合金中最有可能在晶界处发生偏析的杂质元
素为氧元素, 分析是否因为氧元素的升高使得晶界处出现大量的孔洞而引起轧制过程的开裂。将这四种不同密度的板坯所对应的氧含量进行对比, 氧含量并没有随着板坯密度的增大而有一定的规律,反而密度最高的板坯所对应的氧含量(0.118%)也是最高的, 说明氧元素不是引起晶界表面能下降的因素。
2.3 轧制工艺对轧制板材的影响
由于钼及钼合金具有高熔点、高变形抗力以及粉末冶金坯料多孔的等轴晶粒结构, 易导致低温脆断,通常开坯轧制温度应该高于再结晶温度。轧制温度的提高有利于提高成材率,对于一般钼合金来说,合金元素的添加使其具有比纯钼更高的再结晶温度, 因此一般开坯温度要比纯钼高些。但钼和铌可以形成连续固溶体,具有体心立方晶体结构,且铌的
熔点(2469℃)比钼低,本文研究的钼铌合金熔点低于纯钼[5]。
取四组不同密度的板坯,每组取3 块样品,开坯温度分别为1400、1350、1300℃,开坯轧制变形量为20%,按此进行开坯轧制。轧制后密度较低的1、2 号板材边部都有开裂情况;然后进行第二火轧制,轧制温度为1200℃,变形量为17%,轧制后密度较低的1、2 号板材开裂都更加严重,1 号板材已经出现了如图2(a)所示的现象,无法进行后续轧制。随后对其他样品继续进行第三火轧制, 轧制温度为1150℃,变形量13%, 轧制后的板材只有4 号没有出现开裂,2、3 号开裂严重无法进行后续轧制;4 号继续进行第四火轧制,轧制温度1150℃,变形量13%,没有开裂。由此可见,在试验温度范围内,开裂情况和开坯轧制温度没有太大关系。
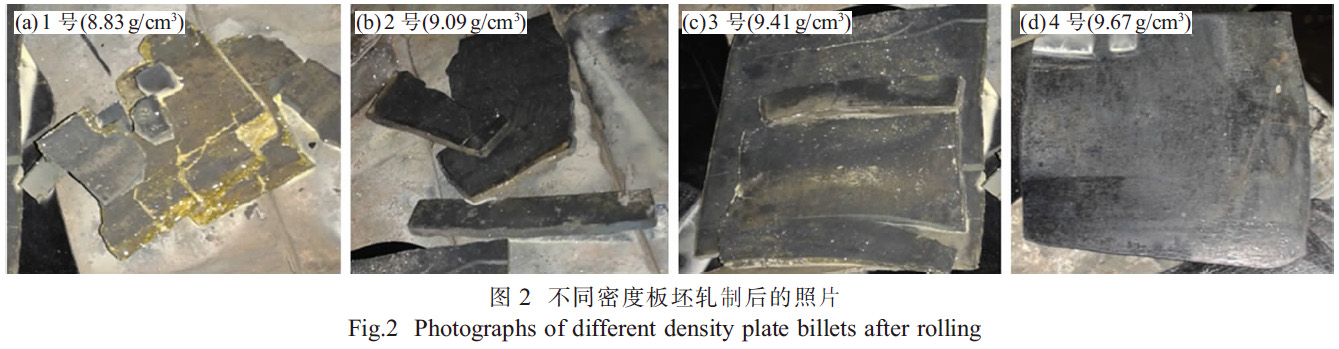
取上述试验中四组不同密度的板坯中每组剩余的1 块样品,将轧制开坯温度设定为1350℃,轧制开坯变形量增大至30%,第一火轧制后1、2 号板坯已经完全断裂成碎块,3、4 板坯边部也出现了不同程度的开裂现象。随后对3、4 号板坯进行轧制,第二火温度为1200℃,变形量为18%,边部开裂的情况加重, 但仍可以进行继续轧制, 第三火温度为
1150℃,变形量为13%,3 号板已经出现了图2(c)中情况,4 号板边部也有开裂,但还可以进行加工。分析表明, 轧制过程中较大的开坯变形量加重了低密度板材的开裂。为了证明结果的正确性,重新取1、2号两块板坯进行小变形量的轧制加工, 第一火开坯温度1350℃,变形量调整为15%,轧制后两块板材边部虽开裂但轻微,仍可继续轧制。随后进行第二火轧制,温度1200℃,变形量为10%,轧后边部开裂稍加重;第三火温度1150℃,变形量7%,两块板已经开裂。但相比较而言,第一火轧制变形量过大,增加了低密度板的开裂程度, 小变形量多道次加工可以适当改善低密度板坯的轧制开裂情况。
3、结论
(1) 钼铌合金中氧含量在0.001%~0.126%时,氧元素不是引起晶界处表面能下降的主要因素。
(2) 由于钼粉和铌粉颗粒大小存在很大差异,烧结坯中存在大量孔洞、裂纹等缺陷,这也使得晶界处原子键合力下降,导致晶界处表面能下降,以至于在轧制过程中因晶界处存在的缺陷而很容易出现分层、开裂、起皮甚至断裂。
参考文献:
[1] 赵宝华,范海波,孙院军.TFT-LCD制造用钼薄膜溅射及其靶材[J].中国钼业,2011,35(1):7-11.
[2] 徐克玷.钼的材料科学与工程[M].北京:冶金工业出版社,2014.
[3] 安耿,李晶,刘仁智,等. 钼溅射把菜的应用制备及发展[J].中国钼业,2011,35(2):45-46.
[4] 党晓明,安耿,李晶,等.铌粉粒度和烧结方法对钼铌合金的影响[J].粉末冶金技术,2016,34(4):272-276.
[5] 梁基谢夫HN.金属二元系相图手册[M].北京:化学工业出版社,2009.
相关链接