1、概述
溅射属于物理气相沉积(PVD)技术的一种,其工作原理是在真空中利用离子源产生的高速离子束流轰击溅射靶材表面,高速离子束中离子和靶材表面的原子产生动能交换,使得靶材表面的原子离开靶材表面并沉积在基底表面。利用各种高纯单质贵金属及新型合金及化合物制得的功能薄膜则为高纯溅射靶材。21 世纪以来,新型溅射技术出现,使得高纯金属溅射靶材成为热点材料。
靶材的纯度与沉积薄膜的纯度息息相关,靶材中的杂质会使得薄膜电阻率的增加,从而影响薄膜均匀性,最终降低器件的良品率。目前,高纯度甚至超高纯度靶材是高端集成电路半导体芯片的必备材料,一般来讲,其纯度需≥ 99.999%。如何持续降低靶材中杂质元素的含量,提升靶材的纯度是目前靶材制备技术发展的热点。
众所周知,生产高纯溅射靶材的基础是对金属材料进行提纯,化学以及物理提纯是目前制备高纯金属常见的两种方式,也可将化学提纯和物理提纯结合使用。金属材料提纯后,
一般需配比其他类型金属元素进行后续使用。
目前,在高纯溅射靶材行业中,跨国公司的优势比较明显,特别是日本等国家的半导体行业发展相继催生了一批高纯溅射靶材生产厂商。但是近年来国内靶材厂商发展迅速,逐渐缩小与国外厂商的差距,经过数年科研攻关、技术累积,国内企业已经拥有部分产品的规模化生产能力和供应水平。
本文主要研究高纯溅射靶材全球专利申请状况及其技术进展,数据检索选用中国专利文摘数据库(CNABS)和德温特世界专利索引数据库(DWPI)。通过关键字和分类号在数据库中检索获得初步结果,通过浏览配合分类号去除明显噪声。数据检索截止时间为2021 年12 月31 日。
2、专利申请情况分析
2.1 申请量分析
高纯溅射靶材专利申请情况如下:
2.1.1 技术萌芽期
阴极溅射现象是1842 年在格罗夫才实验室发现的,20世纪初期,只有化学活性极强的材料、介质材料等采用溅射技术,20 世纪70 年代,随着磁控溅射技术出现,溅射靶材开始应用于实验和小型生产,20 世纪80 年代,溅射技术进入工业化生产的应用领域,所以这段时间专利申请有小幅上涨的趋势,但是整体数量较少,这与技术发展的水平是相关的。
2.1.2 技术发展期
21 世纪以来,新型溅射技术出现、相关薄膜技术的不断进步、集成电路和微电子行业等应用领域出现爆发式的发展,对高纯溅射靶材关注也与日俱增,因此,专利申请量开始逐
步增加。21 世纪初我国的相关研究才开始起步,前期主要处于探索阶段,2008 年全球性经济萧条,导致靶材供货减少和市场需求疲软,全球溅射靶材专利申请量波动不大,而我
国从战略高度关注支持电子材料行业的发展,专业从事高纯溅射靶材研发和生产的国内企业开始出现,且高校和科研院所的研发热情也比较高涨,研制出了部分高端应用领域的溅
射靶材,为该领域的产业化提供了科研基础和市场化条件。
其中以江丰电子为代表的中国靶材厂商专利申请量也迈上了新的台阶,导致全球溅射靶材市场的结构性调整。
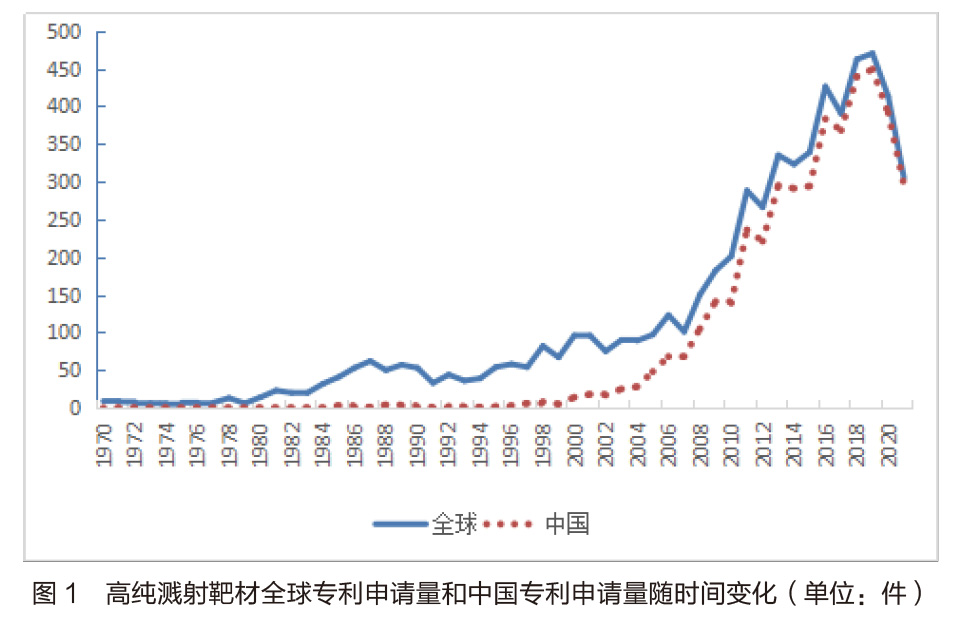
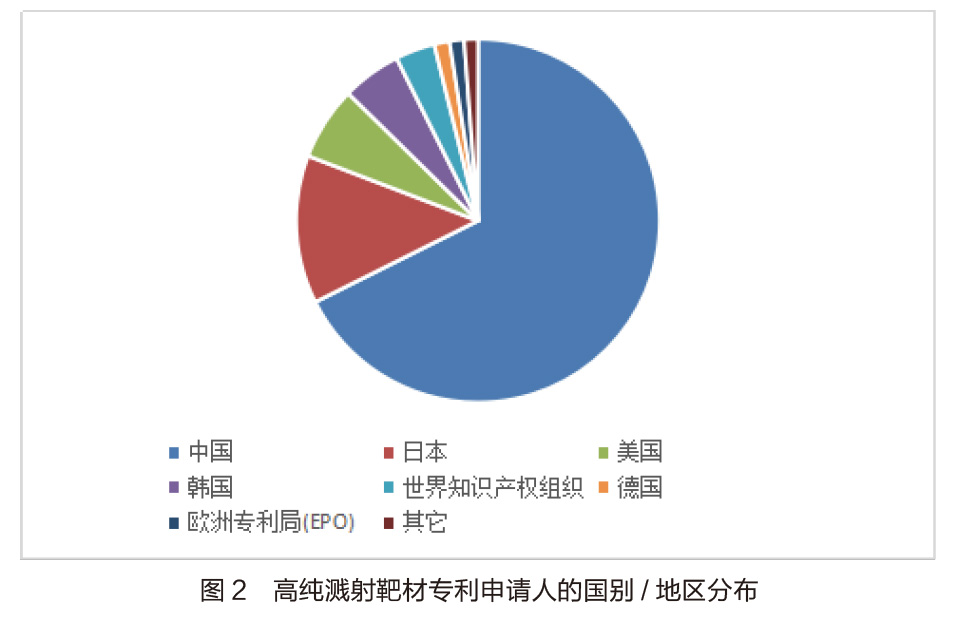
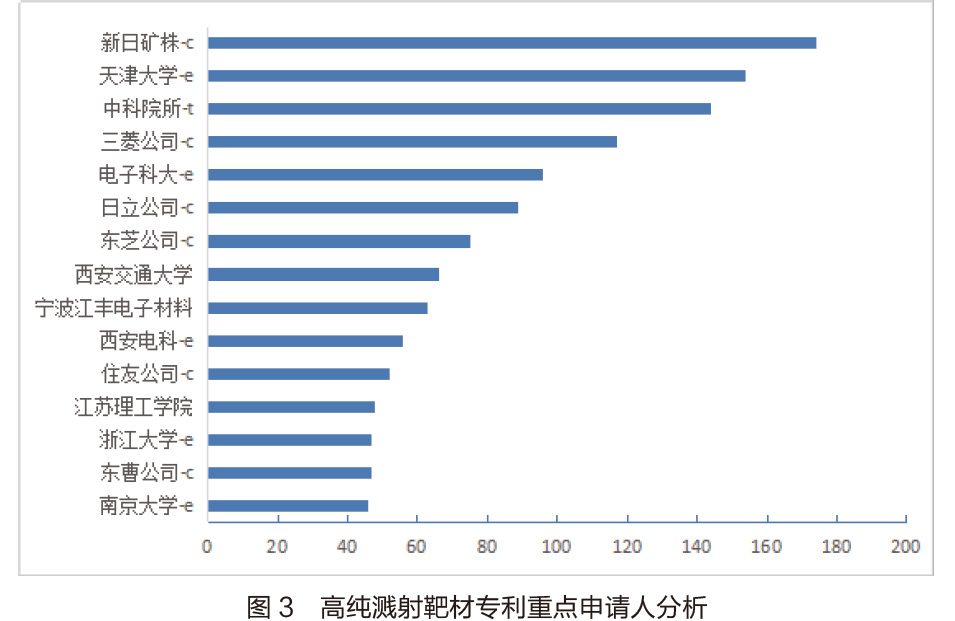
2.2 创新主体分布分析
通过对高纯溅射靶材专利申请人的国别/ 地区进行统计可知,中国的专利申请数量占比最高,这与目前国家的政策支持及行业发展息息相关,日本和美国的专利申请量居二、三名,日美两国在全球的高纯溅射靶材行业一直处于领导地位,掌握较多的核心技术,其靶材生产企业既具有金属材料的高纯制备技术、也掌握靶材制造过程中整体生产线,因此其技术垂直整合能力较强,在全球高端电子制造用靶材的市场中占据主导话语权。但是随着近年来国内靶材企业,例如宁波江丰、有研亿金新材料有限公司等的技术实力持续提升、市场开拓不断加强,相关领域的投资持续加速,中国半导体业的发展更为迅速。
同时,随着新技术、新器件的开发应用不断加速,对材料提出更高要求。
2.3 重点创新主体分析
通过对高纯溅射靶材专利重点申请人分析,按照申请人进行排序,得到了该领域中专利申请的前15 位申请人如图3 所示。
其中,日本申请人为6 名,主要集中为企业申请,其属于产业驱动型的技术研究,具有较强的产业应用前景。排名第一的申请人为日本新日矿,日本新日矿集团是一个综合性企业集团,总部位于东京,经营范围包括资源、石油化工、金属事业,电子材料事业,金属加工事业等。其旗下的日矿金属在靶材市场占比达30%,尤其是铜靶材的最大供应商。另外,日本东曹也已经实现溅射靶材的全品类覆盖,产品纯度最高达6N9 以上,在高纯溅射靶材市场具有一定的份额。可见,该领域在国外的研究相对比较集中,主要由几家企
业掌握相关专利技术。
中国申请人为9 名,主要集中在高校和企业申请,我国虽然专利申请量较高,但是技术发展主要集中在近几年,且研究相对较为分散,在市场中占比也相对较少,但是随着其技术累积,后续发展值得期待。
就国内企业而言,江丰电子是近年来快速崛起的靶材制造企业,其专利申请量突出,成为台积电、中芯国际、海力士、联华电子等客户的主要供应商。
2.4 重点专利分析
高纯溅射靶材制备过程中,高纯金属材料纯化是首要条件,针对铜、镍、银、钛等金属常采用电解精炼提纯(化学提纯法)。针对金、银、铜、铝等金属及其合金往往采用真空感
应熔炼制备(物理提纯法)。在实际的生产过程中,往往采用多种手段联合提纯,例如采用的物理加化学方法实现高纯材料的制备。
高纯溅射靶材制备过程中,靶材制备技术同样重要。常见的制备方法有铸造法以及粉末冶金法,对于难熔金属,也可采用熔炼法。
铸造法主要涉及真空感应熔炼、真空电子轰击熔炼、真空电弧等工艺,主要制备过程为先将合金原料熔炼、然后进行浇注、利用模具成型铸锭、机械加工后即可得到产品。
粉末冶金法主要涉及冷压、真空热、热等静压等工艺,主要制备过程为合金原料通过熔炼后浇注、模具、铸锭、粉末、成形、高温、烧结后得到靶材产品。
株式会社东芝于1987 年在JP62063670A 中提出一种由高纯度镍形成,能够实现高功率密度,高效率操作的一体化溅射靶,高纯度的镍是通过电子束熔化和浇铸成锭,即,物理提纯金属+ 铸造法成型。三菱公司于1987 年在JP62107855A 中记载,在真空中溶解,精制的高纯度金属熔融液,同样在真空中铸造成水冷金属模具并迅速冷却,从而制造蒸镀用材料或溅射用靶材料的方法,即,物理提纯金属+ 铸造法成型。
株式会社东芝于1987 年在JP62294175A 中提出将纯钛进一步高纯度化的方法之一就是卤化物分解法,特别是碘化物分解法,用于钛的精制,即,化学提纯金属法。
日本能源公司(系由日本矿业和KYO-DO 石油公司合并而成)于2000 年在JP2000239836A 中提出制造高纯度铜或铜合金溅射靶的方法,其特征在于,使用电子束熔融或真空感应锡熔融铸造的高纯度铜或铜合金锭,其氧含量在100ppm 以下,碳含量在150ppm 以下,氮含量在50ppm以下,硫黄含量在200ppm 以下。即,物理提纯金属法。
该公司于2000 年还在JP2000212678A 中提出一种高纯度钽的方法,其特征在于,将钽化合物或钽废料进行熔融盐电解,使其成为电解析出高纯度钽后,通过电子束等溶解除去挥发成分。即,采用化学+ 物理提纯金属法。
日矿金属于2010 在WO2010038641A1 中提出一种高纯度铜,高纯度铜具有纯度不小于6N,该含量的磷,S,O,和C 组分为每个不大于1,和具有非金属夹杂物的数量粒径为0.5 至20μm 中所含的铜或铜合金不超过10, 000颗粒/ 克,并提出一种电解制造高纯度铜的方法,在阴极和阳极之间设置隔膜,将从阳极一侧的电解槽中抽出的电解液或追加电解液供给阴极一侧的电解槽时,在向阴极一侧的电解槽供应电解液之前通过活性炭过滤器,然后向阴极一侧的电解槽供应电解液,从而实现高纯度的电解。即,采用化学提纯金属法。
该公司于2015 年在WO2015050041A1 中提到一种均质溅射的高纯度钽溅射靶,粉碎钽原料矿石,用氢氟酸溶解粉碎粉,提取溶剂,得到钽溶液,然后在钽溶液中加入氟化钾和氯化钾,沉淀、分离氟钽酸钾,得到的高纯度钽,除气体成分以外,所有的杂质都不足1massppm,纯度达到99.9999mass% 以上,并通过电子束溶解进一步除去杂质。即,采用化学提纯金属法。
宁波江丰电子材料股份有限公司于2015 年在CN103418798B 中提出一种利用钛残靶制备高纯钛粉的方法,包括:切割步骤,切割钛残靶成钛样块;酸洗步骤,酸洗所述钛样块;氢化步骤,氢化所述钛样块形成氢化钛样块;成粉步骤,破碎所述氢化钛样块成氢化钛粉;脱氢步骤,加热去除所述氢化钛粉内的氢,得到高纯钛粉。本发明所提供的制备高纯钛粉的方法可回收利用钛残靶,制备用途广泛的高纯钛粉。即,采用化学提纯金属法。
宁波江丰电子材料股份有限公司于2020 年在CN111230131A 提出的钛粉的制备方法,其将原材料进行处理后得到钛棒,然后将钛棒进行无坩埚电极感应熔化气体雾化,即可得到钛粉,不仅工艺流程短,而且制得的钛粉氧含量低、纯度高。在合适的真空条件及保护气体条件下将预处理后的钛棒进行区域精炼,金属液体连续垂直穿过喷嘴往下流,通过紧耦合喷嘴由高压气流将金属液体雾化破碎成大量细小的液滴,细小的液滴在飞行中凝固成颗粒,最终可制得高纯低氧的钛粉。即,采用物理提纯方法。
3、结语
本文基于目前公开的全球专利申请,简述了高纯溅射靶材全球专利申请状况及其技术进展。从上面的专利分析可以看出,全球的高纯溅射靶材的专利申请量仍然保持上涨的趋势,我国的相关研究虽然起步较晚,但是专利申请呈现快速增长趋势。在创新主体方面,全球的高纯靶材制造业仍呈现寡头垄断格局,特别是国外的少数企业技术发展成熟、具有
完备的产业链,占据主导地位,尤其是日本新日矿,是全球最大的靶材供应商;而国内靶材申请人虽然近年来经过一定的研发投入、技术积累,取得了一定的成果,掌握了部分超
高纯金属材料的提纯及溅射靶材制备的核心技术,但是多数种类的靶材原材料仍为进口,相关的金属提纯类研究较少,在原材料上容易受到国外进口商的制约。目前集成电路等行
业的发展,对靶材的质量都提出了更高要求。国内靶材发展面临更高的挑战。因此,应继续加大溅射靶材基础研究、加大人才培养、加强顶层设计,共同推动靶材产业的发展。
相关链接