引言
钛基材料因具有耐腐蚀性能好、密度低、比强度高等优良的物理性质,在真空镀膜领域中常被用做靶材来制备钛基复合材料,从而提高基材性能和使用寿命,不仅可以合理的利用资源,降低生产成本,也促进了钛材在工业领域的应用[1-2]。在众多的镀膜技术中,磁控溅射技术具有基片温升慢、沉积速率快等优点,能够有效提高薄膜附着力和均匀性,而且几乎所有的金属都可以作为溅射靶,因此广泛应用于各种工业薄膜制备领域中。高纯钛材作为一种昂贵的金属靶材,其冶炼过程复杂,制造成本较高,作为溅射镀膜过程中的核心部件,其特性直接影响到膜层质量以及镀膜成本,因此,提高钛靶的利用率和稳定性尤为重要[3-4]。

在磁控溅射镀膜过程中,溅射靶的功率密度受到靶热负荷的限制,其中80%的电能都会转化为热量,导致钛靶急剧升温[5-6]。当溅射电流较大时,过多阳离子对靶进行轰击会使溅射靶过热而烧毁,或因热应力过大使表面出现裂纹,进而导致薄膜出现大量斑点缺陷,使用寿命远远达不到正常水平[7]。
对于造价较高的靶材,如氚钛靶而言,靶温过高还会造成氚气释放,影响靶的热稳定性及使用寿命[8-9]。因此,磁控溅射靶都会设置冷却系统,通过冷却水带走离子轰击靶材产生能量的约70%[10],从而保证溅射过程的稳定性。目前针对钛靶制造工艺的研究很多,但对钛靶磁控溅射镀膜过程中的冷却研究却很少,因为测量靶面温度本身就存在难度[11-13]。随着计算机相关软件的开发和应用,为钛靶的冷却模拟提供了平台。本研究基于FLUENT软件对磁控溅射过程中钛靶的冷却系统进行模拟,通过改变水流入口速度和水流通道结构,对冷却系统进行优化,以达到控制钛靶温度、提高钛靶寿命及磁控溅射稳定性的目的。
1、钛靶冷却系统的建立与仿真
1.1物理模型的建立
图1为钛靶冷却系统的物理模型,钛靶(r=75mm,t=8mm)和铜背板(r=100mm,t=14mm)组成。其中铜背板内部刻有蛇形冷却通道结构,如图1a所示。冷却水进出口(截面尺寸为20mm×5mm)分布在同一侧,水流进入背板后,经过三次转折流出背板,设计该结构的目的是为了增加水流的湍流效果,增强换热效率。整个冷却系统在LUENT的前处理器GAMBIT中进行建模并划分网格[14],图1b为简化后的钛靶磁控溅射冷却系统计算模型。
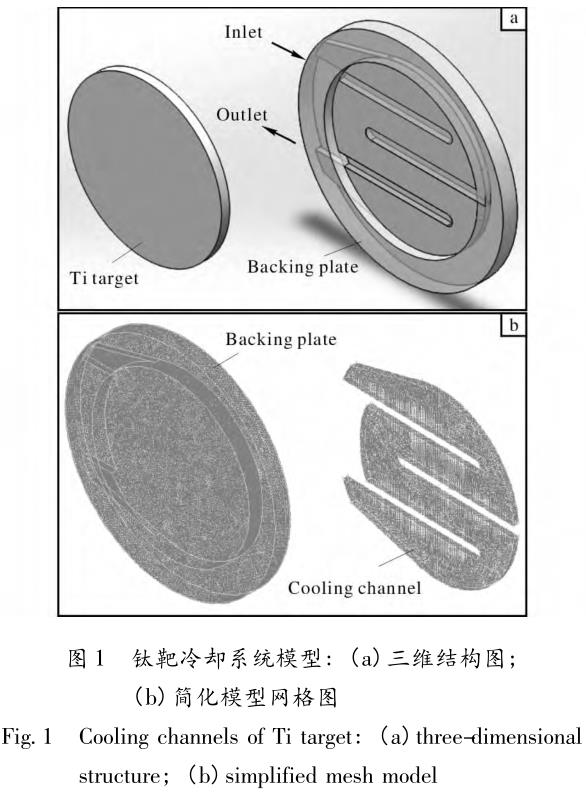
1.2边界条件设置
钛靶冷却系统的建模包括三部分:铜背板、钛靶和冷却水,在FLUENT中进行计算之前,需要设置合适的边界条件来保证计算结果的正确性。假设在冷却过程中,流体流动为稳态流动,流体设为湍流模型,即雷若数介于2530~5050之间,选择标准的k-ε模型。在流体换热的过程中,由于钛靶表面局部温度会高达几百摄氏度,所以会有很少一部分液体形成蒸汽,但在模拟过程中,为了简化计算模型,这部分相变产生的蒸汽忽略不计[15]。流体入口设为VELOCITY-INLET,温度设为288K,速度为0.5、1.0、1.5m/s,出口设为OUTFLOW。在磁控溅射过程中,大部分的电能都通过离子轰击作用转化为靶材的热能,故将钛靶表面设置为一个发热壁面(HEATWALL),热流密度为100kW/m2。
由于背板对钛材换热影响较小,设置为WALL,所有的壁面都为无滑移边界条件[16],具体的设置如表1所示。
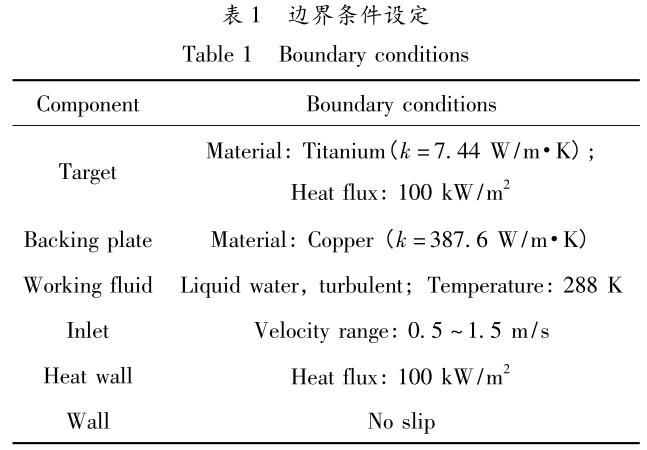
1.3模拟结果分析
图2为蛇形冷却通道的钛靶表面温度分布云图以及水流速度分布云图。由图2a可知,当水流入口速度为0.5m/s时,在冷却通道的空白处对应的钛靶表面换热效果比较差,热量聚集在此处无法被有效转移,靶面局部最高温度可以达到530K;当水流入口速度分别增加到1.0m/s和1.5m/s时,钛靶表面最高温度分别为492K和477K。为了便于比较,将三种水流入口速度对应的温度分布图放在同一个温度刻度表内进行比较。通过对比可知:随着入口水流速度的增加,钛靶表面整体温度有明显的下降,说明水流入口流速在很大程度上影响着换热效果[17]。
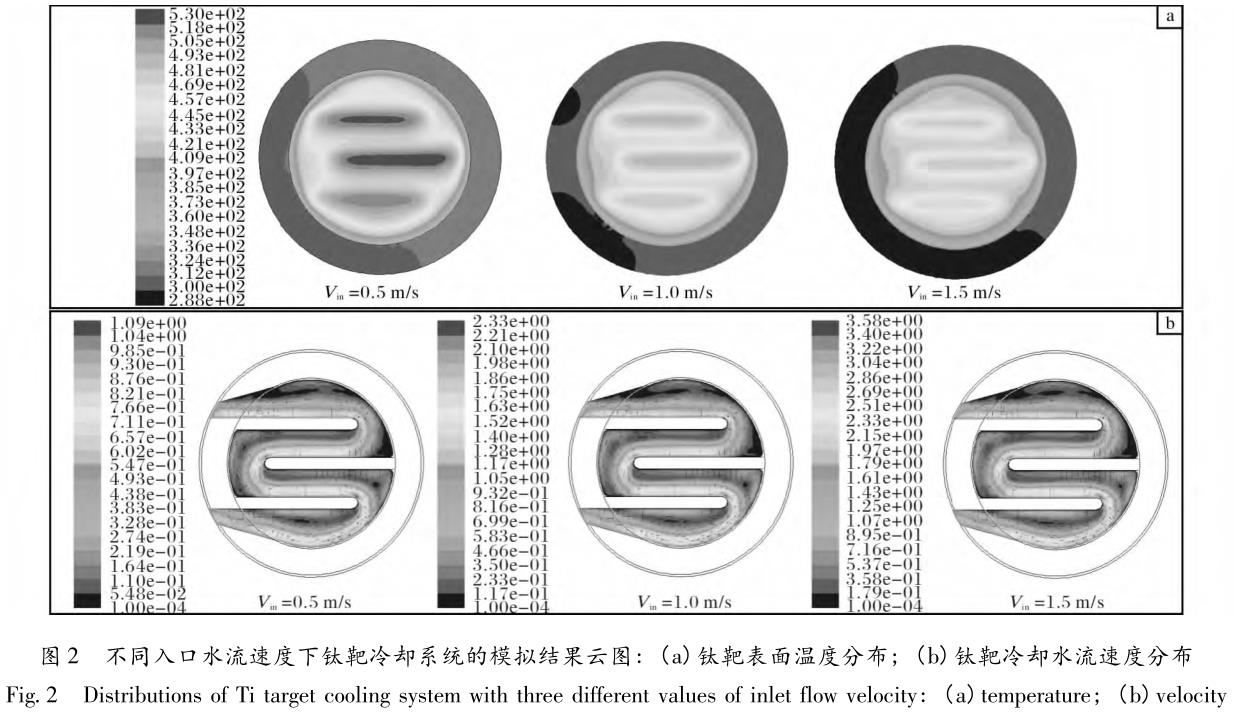
图2b为蛇形冷却通道的水流速度分布情况。在结构的限制下,水流发生强制转折,故湍流效果较明显,水流的流动轨迹大致成“M”形状,但湍流效果随着水流速度的增加效果没有太大的变化。
2、钛靶冷却系统优化设计与分析
2.1钛靶冷却通道结构的改进
针对上述模拟结果提出的问题,提出了如下优化结构,如图3所示。
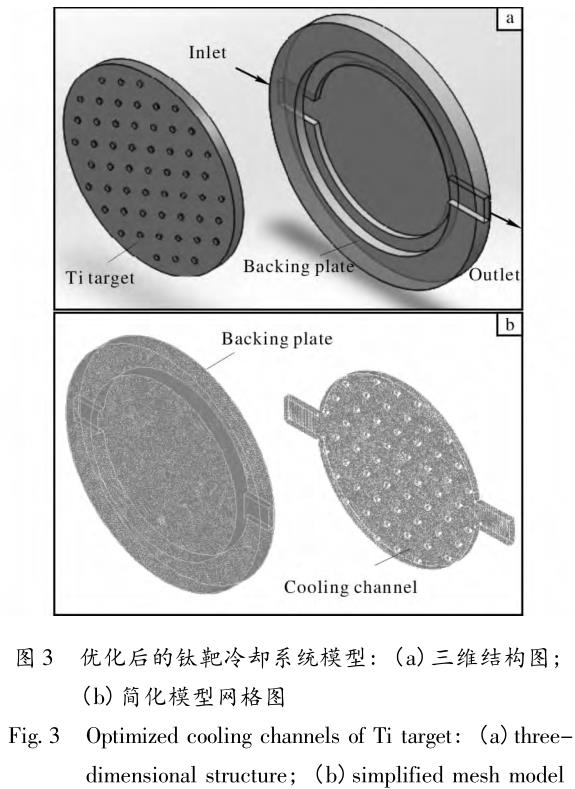
优化结构的冷却通道为平面结构,该结构较蛇形结构简单,冷却水的进出口(截面尺寸为20mm×5mm)位于同一轴线上。该结构的设计目的是增大水流换热面积,增强换热效率,同时通过在钛靶表面上增加均匀分布的小圆柱体结构(r=5mm,H=2mm)来加强水流的湍流效果。图3b为简化后的计算模型,分别为背板和水流通道模型。在冷却模拟的过程中,边界条件的设置与上文相同,分别取入口水流速度为0.5、1.0、1.5m/s,模拟结果如图4所示,其中图4a为钛靶冷却系统的温度分布云图,图4b为水流速度分布云图。由图4a可以看出,当水流入口速度为0.5m/s时,钛靶表面最高温度达到464K,与优化前相比降低63K,说明优化后的结构有利于提高冷却系统的换热效率。随着入口水流速度的增加,钛靶表面温度分布有所改善,高温区域逐渐减少,并在入口水流速度为1.5m/s时优良。
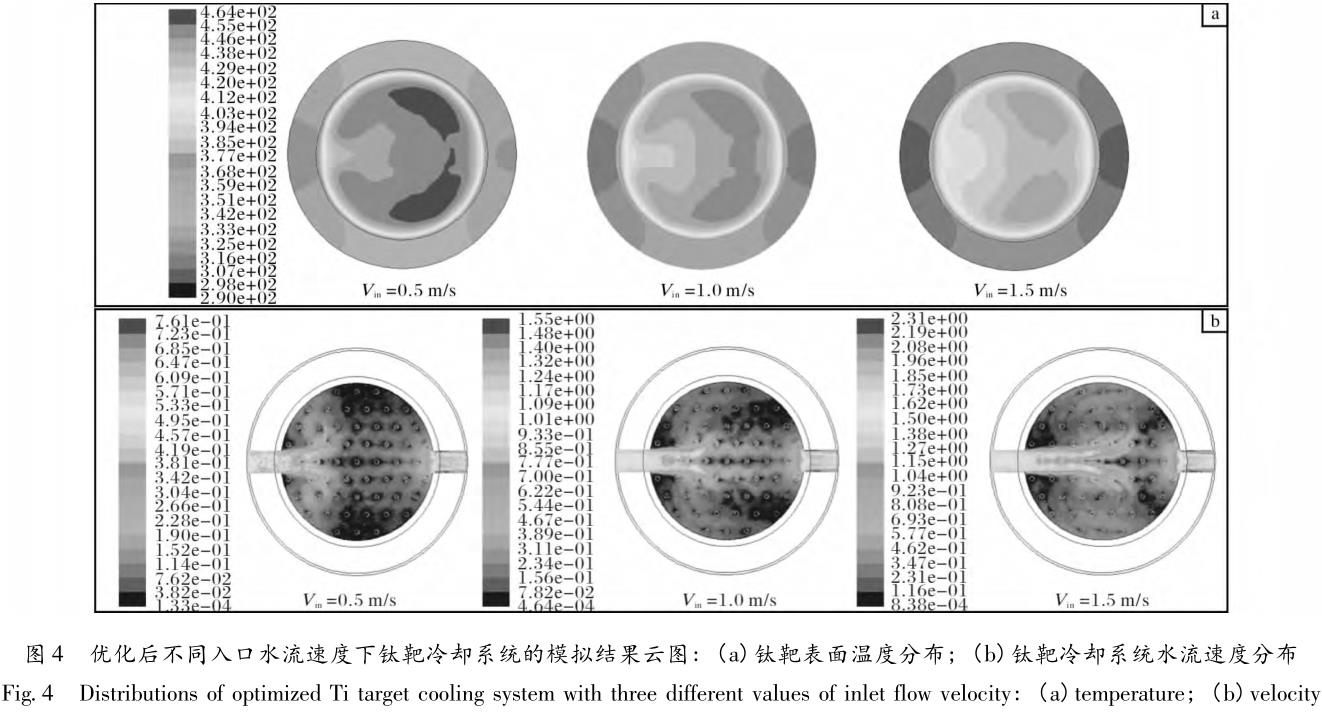
结合冷却系统的水流速度分布云图(图4b)可知,随着水流入口速度的增加,湍流效果显著增强,水流的速度分布在进出口轴线的两侧形成漩涡,冷却水与钛靶表面之间的换热增强,因此钛靶表面的平均温度降低。但该结构仍然存在弊端,整个钛靶表面的温度分布并不均匀,在水流出口处两侧形成了半圆环状的高温区域。
在钛靶表面建立半径为50mm的环形(钛靶表面高温环形区域),其温度变化趋势图如图5所示。
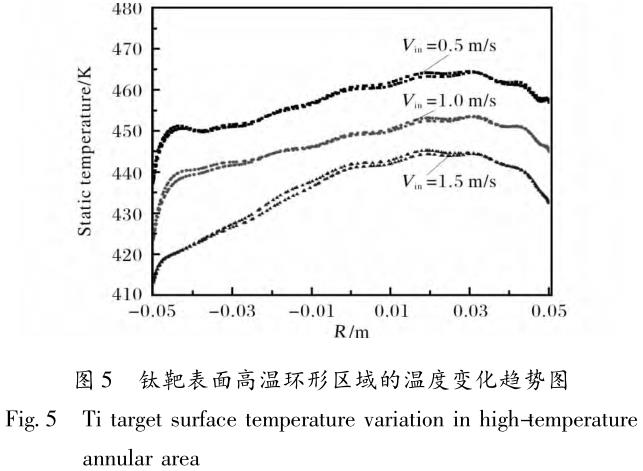
从冷却水的入口到出口方向看,钛靶表面环形区域温度整体呈现递增的趋势,温度值波动较大造成钛靶表面温度分布不均,所以有必要对冷却系统结构进行进一步的优化。
鉴于以上分析结果,结合冷却通道本身是圆柱形内腔,如果水流沿着内腔切向方向进入,水流流动的阻力就会大大减小,所以在上述平面冷却通道结构的基础上,将进出口改为沿内壁切向,并研究不同进出口夹角对冷却效果的影响。
2.2水流进出口方向对钛靶换热效率的影响
水流进出口方向沿着冷却内墙壁切向的结构如图6所示,分别是夹角α为135°、150°、180°时的三种背板结构。在冷却模拟的过程中,边界条件的设置与上文相同,将三种不同的冷却系统结构分别导入FLUENT中进行冷却模拟,其中水流进口速度均设置为1.5m/s,经过100次迭代后计算结果已经收敛。模拟结果如图7所示,其中图7a为进出口水流速度矢量夹角α为135°、150°、180°时冷却系统的水流速度分布云图,图7b为冷却水流动轨迹图。
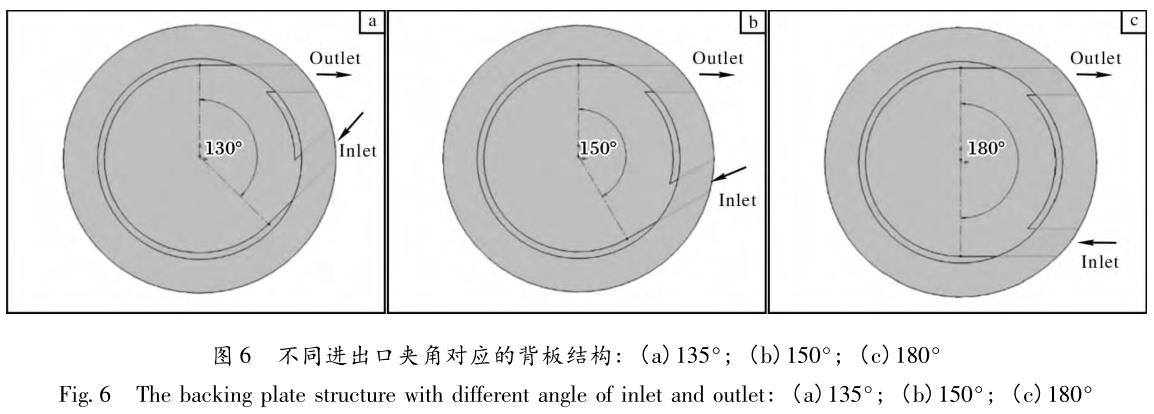
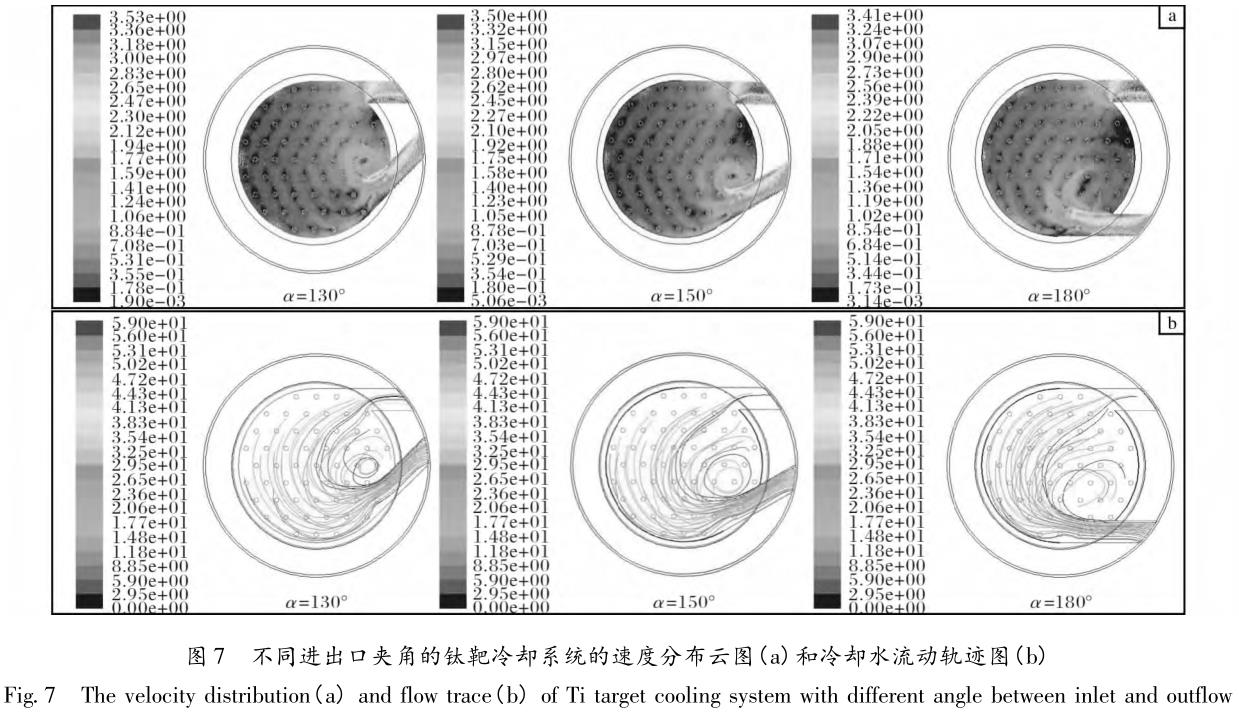
由图7a可以看出,冷却水沿着内腔切线的流入方式能有效改善速度分布情况,更符合内腔本身的结构特点。水流速度在进出口附近比较大,这是由于在进出口与内腔的连接处水流截面面积发生突增,导致速度突降,但水流速度的降低势必会影响冷却水与钛靶的换热效率,这也是在钛靶表面均匀布置凸起小圆柱体的原因。通过在钛靶表面均匀布置凸起的小圆柱体,能有效增强水流湍流效果,增加冷却水与钛靶表面的碰撞强度,在流动过程中将热量进行有效转移,提高冷却系统的换热效率。由图7a还可以看出,随着进出口距离的增大,冷却内腔速度分布更加均匀,并在进出口呈相对平行布置时效果达到最佳,这对钛靶表面的温度分布有一定程度的改善。
由图7b可以明显看出水流进入冷却系统后,入口附近的流线分布较密集,而且在进出口之间会形成完整的漩涡,尤其在α角比较小时更为明显。在冷却系统内腔结构的限制下,水流轨迹从入口到出口形成了一定半径的圆弧,且距离进出口越远,圆弧轨迹半径越大,同时流线分布也越稀疏。这是因为距离进出口越远的区域水流速度越小,能量相对较弱,因此会出现流线稀疏的现象,甚至在出口附近会形成空白。但随着α角的增大,流线的整体分布情况会有所改善,在进出口呈相对平行布置时的流线分布较为理想。
为了更加直观地呈现不同进出口布置下钛靶表面的温度分布情况,在FLUENT后处理中,将钛靶表面温度数据导出并通过origin进行数值分析,得出如图8所示的钛靶表面温度分布云图。
由图8a可知,当夹角α为135°时,钛靶表面的高温区域集中在距离进出口较远的区域,最高温度值达到447K。由图8b、c可以看出,随着α角的增大,高温区域逐渐减小,并在进出口呈平行布置时最小,且钛靶表面最高温度为440K。数值分析结果与上述流场分析结果一致,证明了当冷却水的入口速度保持不变时,水流进出口速度矢量夹角对钛靶表面冷却效果具有较大的影响,当夹角增加至180°,即进出口呈平行布置时,钛靶表面冷却效果优良。
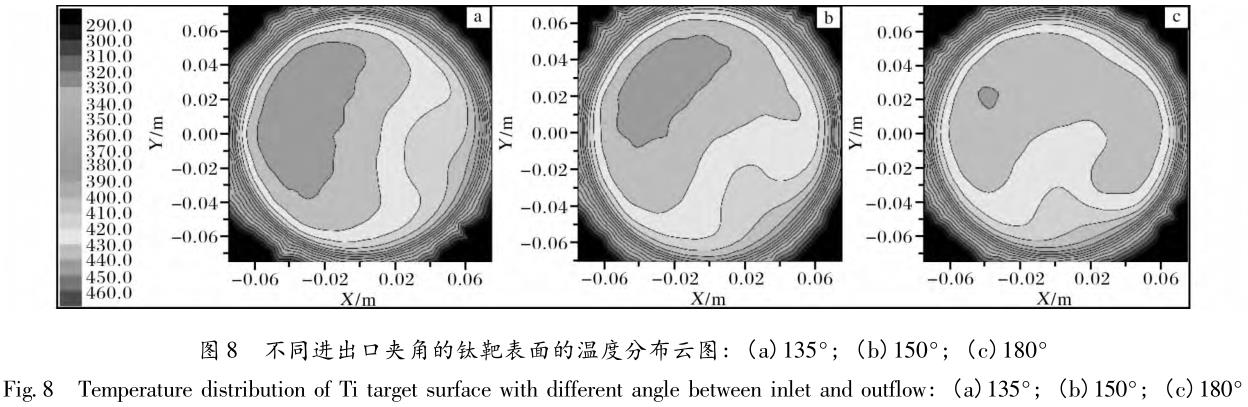
图9为当水流流速为1.5m/s且进出口呈相对平行(α=180°)时水流分别沿着图3和图6c所示的进出口方向流入冷却系统时的钛靶表面温度分布情况。从图中可以明显看出优化后的钛靶表面温度分布更均匀,且平均温度也有所降低,也进一步的说明优化后的结构是合理的。
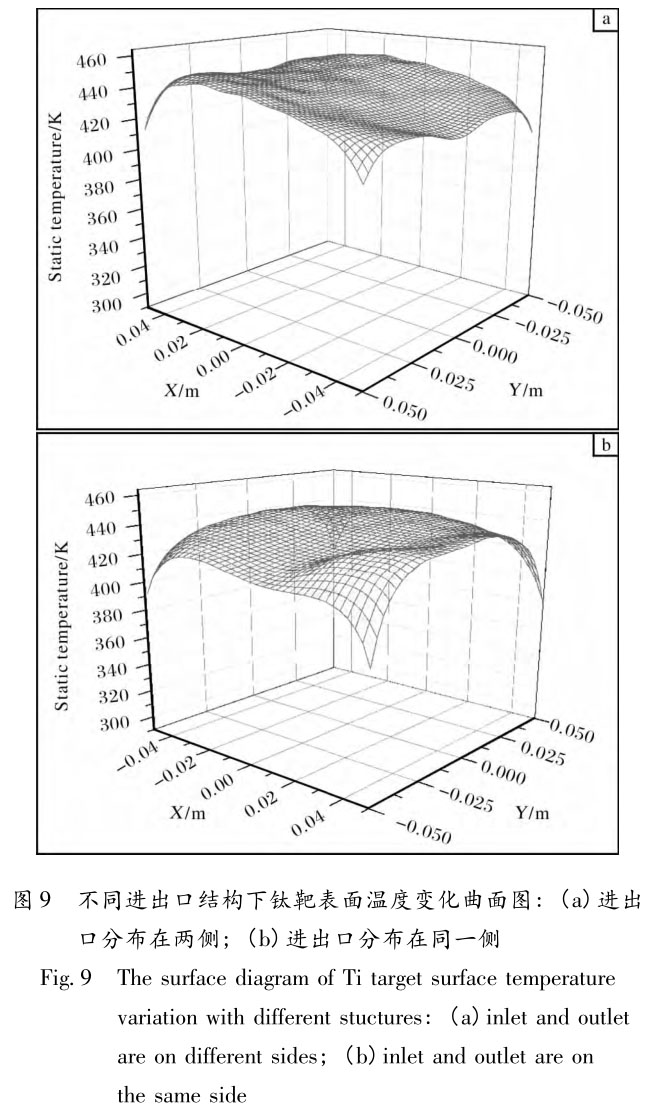
3、结论
基于FLUENT软件对钛靶的冷却系统进行仿真并做出合理优化,得到的主要结论如下:
(1)平面冷却通道结构的换热效果优于蛇形冷却通道结构,同时水流入口速度对冷却系统的换热效率有较大的影响,随着水流入口速度的增加,靶面整体温度显著降低。
(2)提高冷却系统的换热效率应兼顾换热面积最大化以及冷却水的湍流效果,针对平面冷却通道而言,靶面均布凸起小圆柱体结构能有效增加水的湍流效果,提高冷却水与靶材的换热效率。
(3)冷却水沿着内腔的切线进出更符合冷却系统结构本身的特点,流体轨迹在腔体内呈旋转状,流体湍流效果较好,系统的冷却效率明显提高。且当水流进出口呈相对平行时靶面最高温度最小,整个靶面温度分布也更均匀。
参考文献
[1]杨江.采用磁控溅射法在钢材表面镀钛膜研究[D].成都:西华大学,2012.
[2]杨江,邹敏,赖奇,等.真空镀膜技术制备钛基复合材料研究现状[J].攀枝花学院学报:综合版,2011,28(6):4-8.
[3]张以忱.真空镀膜技术与设备[M].北京:冶金工业出版社,2014:33-43.
[4]张以忱.真空镀膜设备[M].北京:冶金工业出版社,2015:157-160.
[5]BrauerG,SzyszkaB,VerghlM,etal.Magnetronsputte-ring-Milestonesof30years[J].Vacuum,2010,84(12):1354-1359.
[6]李希平.高功率复合脉冲磁控溅射等离子体特性及TiN薄膜制备[D].哈尔滨:哈尔滨工业大学,2008.
[7]张之圣,白天,王秀宇.薄膜电阻器用磁控溅射高阻靶材[J].压电与声光,2009,31(4):525-527.
[8]曹文钢,展亮,曹昌胜,等.氚钛靶系统靶温升瞬态分析的方法研究[J].真空科学与技术学报,2014,34(6):575-578.
[9]姚泽恩,陈尚文,苏桐龄,等.高速旋转氚钛靶系统设计和靶温度的数值模拟[J].核技术,2004,27(10):787-791.
[10]余东海,王成勇,成晓玲,等.磁控溅射镀膜技术的发展[J].真空,2009,46(2):19-25.
[11]吴全兴.高纯钛靶表面处理技术开发[J].稀有金属快报,2004,23(12):40-41.
[12]刘正红,陈志强.高纯钛的应用及其生产方法[J].稀有金属快报,2008,27(2):1-8.
[13]关亚兰,崔秀清,刁训刚,等.TX1800磁控溅射镀膜机冷却系统的改进[J].真空,2012,49(5):62-64.
[14]李鹏飞.精通CFD工程仿真与案例实战[M].北京:人民邮电出版社,2011.
[15]BaikJS,KimYJ.Astudyontheheattransferenhance-mentinmagnetronsputteringsystem[C]//ASME/JSME2007ThermalEngineeringHeatTransferSummerConfer-encecollocatedwiththeASME2007InterPACKConfer-ence.Vancouver:ASME,2007:315-320.
[16]王德志.圆平面磁控溅射靶的优化研究[D].沈阳:东北大学,2011.
[17]王伟明,王保华,李大永,等.等离子枪体中冷却水流动与换热的数值模拟[J].计算物理,2005,22(1):83-87
相关链接