1、引言
提高钛合金零件的加工效率、减少零件加工变形一直是钛合金加工过程中的研究重点。钛合金高速加工可有效降低零件的变形量,是钛合金零件加工的研究方向[1]。本文在分析钛合金异形零件加工方案的基础上,针对实际加工过程中影响加工效率的问题提出新的工艺方案:采用高速铣削对零件进行粗加工,并根据零件结构特点将零件划分为不同加工区域,分析确定各加工区域的加工顺序,对零件进行精加工。通过对工艺的优化,使零件加工变形得到了有效控制,而且加工效率得到明显提高。
2、零件加工方案分析
2.1零件加工方案
如图1所示,某机型钛合金零件呈“人”字形,零件外廓尺寸约1000mm×600mm×70mm,零件头部厚度为27mm,腹板厚度从紧邻头部腹板到腿部腹板逐渐减小,紧邻头部腹板厚度为6mm,腿部腹板厚度为2mm。
钛合金异形零件原加工方案为:粗铣外形→粗铣第一面内形→粗铣第二面内形→精铣第二面内形→精铣第一面内形→精铣外形→铣切零件工艺凸台,所用刀具为立铣刀。零件加工仿真结果见图2。
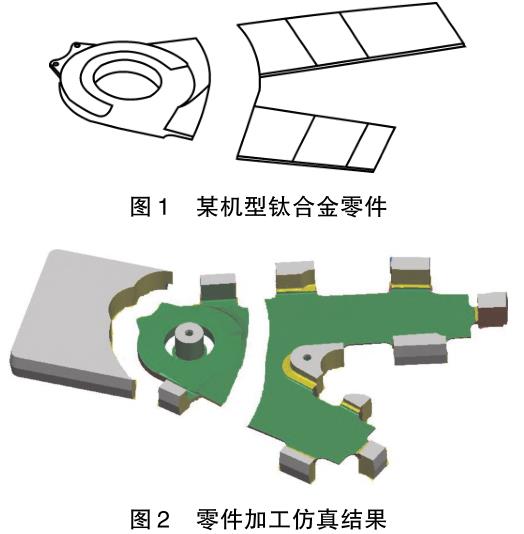
2.2加工方案分析
通过对原加工方案进行分析,提出如下问题:
①钛合金零件毛料为模锻件,材料较大,铣外形工作量大,采用上述方案加工零件,毛料最终去除量约占毛坯料重量的70%;铣外形工序的毛料去除量约占毛坏料总去除量的40%。由于铣外形工序为非增值工序(不直接产生生产价值的工序),因此,若将该工序优化或取消,将大幅提高零件加工效率;②采用上述方案加工零件,在实际加工过程中,腿部腹板处易发生翘曲变形,导致零件型面检测出现问题;③铣外形工序对压板摆放位置要求严格,若压板位置出现偏差,容易出现刀具与压板相撞的加工事故。因此,铣外形时,需要操作人员时刻留意刀具与压板是否会发生碰撞,浪费大量精力;④分析可知,铣外形工序需要在开敞式机床上进行加工,以便于观察零件加工状态,但目前主流机床为封闭或半封闭式机床,无法直观查看零件的加工状态,容易出现加工事故。
综上所述,该零件加工方案急需进行工艺优化改进,可优化点分析如下:
①由于铣外形工序为非增值工序,加工工作量占总加工工作量比重较大,且铣外形过程中极易出现加工事故,可取消铣外形工序;②立铣刀粗加工零件时,切削深度大,切削速度慢,易造成零件变形,可采用高速铣削进行零件粗加工,留少量余量,再利用立铣刀进行零件精加工;③零件精加工时,腹板厚度不同,刚度不同。若不分区域加工,薄处腹板容易因相邻腹板不能提供足够刚度而发生振颤,需根据腹板厚度,结合零件自身结构特点进行加工区域划分,并合理规划各区域加工顺序进行零件精加工。
3、零件加工工艺优化
通过对零件加工方案进行分析,结合可优化点分析,从工艺流程优化、粗加工优化及精加工优化三个部分对该钛合金异形零件进行加工工艺优化。
3.1加工工艺流程优化
钛合金异形零件在铣切外形时存在诸多弊端,因此,在工艺流程优化过程中,取消铣切外形工序,直接进行零件内形的加工,并在加工过程中引入钛合金高速铣削加工技术。
优化后的加工工艺流程见图3。具体加工过程:①采用高速铣削加工技术进行零件粗加工,以减小因毛料去除量大所引起的加工变形;②根据零件结构特点对零件加工区域进行划分及排序,完成零件精加工。
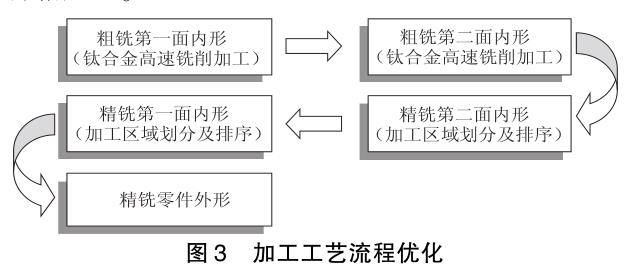
3.2钛合金高速铣削加工技术
切削线速度达到100m/min以上的钛合金切削方式被称为高速切削[2]。高速铣削是钛合金零件铣削加工的发展方向,具有加工效率高、切削热量少及切削振动小的特点[3],不仅能够提高零件加工效率,还可有效减小零件变形量。
由于零件腿部腹板较薄,粗加工材料去除量大,在实际加工中极易发生翘曲变形,因此将高速铣削引入零件粗加工过程,充分利用高速铣削中切削力小、引起零件变形量小的特点进行该钛合金异形零件的粗加工。该钛合金异形零件高速铣削粗加工时,使用ϕ63R4浅切刀,考虑到零件最终的表面粗糙度及光度要求,零件粗加工后留0.5mm余量,利用立铣刀进行精加工,加工参数设置见表1。

3.3零件加工区域划分及加工顺序规划
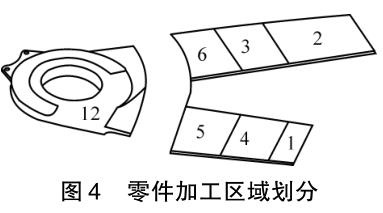
该钛合金异形零件的腹板厚度从紧邻头部腹板到腿部腹板逐渐减薄,紧邻头部腹板厚度为6mm,腿部腹板厚度为2mm。在精加工过程中,为保证腹板在加工时的刚度要求,避免发生振颤造成厚度超差,根据零件自身结构特点,将腹板划分为12个区域(见图4)。加工顺序由小到大排列,加工腹板厚度由薄到厚,使得在加工薄处腹板时,相邻腹板面可为其提供足够刚度,从而避免发生震颤。该零件头部厚度为27mm,不存在切削震颤问题,放至最后加工,采用ϕ25R4硬质合金刀具进行精加工。该钛合金异形零件正反面结构类似,均采用相同的区域划分方法进行加工。采用优化后的工艺方案加工零件,不仅将零件加工效率提升40%,还避免了零件腿部腹板发生翘曲变形,该优化方案已成功应用到实际加工中。利用优化后的方案加工零件,仿真结果见图5。
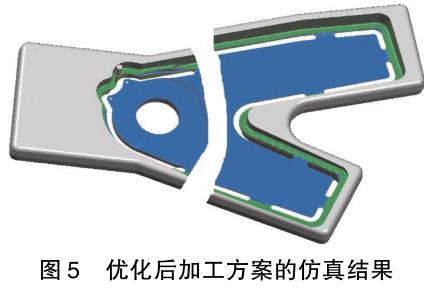
4、结语
提高钛合金零件加工效率和减小零件加工过程中的变形是钛合金零件加工过程中的重要研究课题。针对某机型钛合金异形零件加工方案所存在的问题,提出加工工艺优化方法:将高速铣削技术应用到钛合金异形零件粗加工过程中,并根据零件特点将腹板进行区域划分,规划各区域加工顺序,进行零件精加工。
采用优化后工艺方案加工零件发现,加工效率明显提升。本文工艺优化分析方法对后续类似结构的钛合金零件加工具有一定借鉴意义。
参考文献
[1]王晓明,韩江.TC4钛合金高速铣削表面粗糙度研究[J].机械设计与制造,2019(5):232-240.
[2]耿国盛.钛合金高速铣削技术的基础研究[D].南京:南京航空华天大学,2006.
[3]赵勋,屈植华,王社权,等.钛合金高速铣刀的开发及试验研究[J].工具技术,2018,52(8):77-82.
第一作者:卜庆奎,硕士,工程师,沈阳飞机工业(集团)有限公司,110850沈阳市
FirstAuthor:BuQingkui,Master,Engineer,ShenyangAir⁃craftCorporation,Shenyang110850,China
相关链接