半导体磁控溅射用高纯钽靶材加工流程为通过铸造制备成分合格的锭材,形状根据铸造模具,为不同直径的圆柱形,然后对锭材进行切片,对圆片进行变形与热处理,控制其晶粒度和晶粒取向,晶粒取向是影响溅射出的薄膜性能(电阻以及厚度均匀性)的关键参数,因此变形与热处理是靶材生产非常关键的工序。
对经过了塑性变形和热处理的 Ta 靶坯与背板进行焊接,之后进行机械加工成匹配溅射机台的尺寸形状,然后检测、清洗包装出货,整个 Ta 靶生产流程如图1所示。
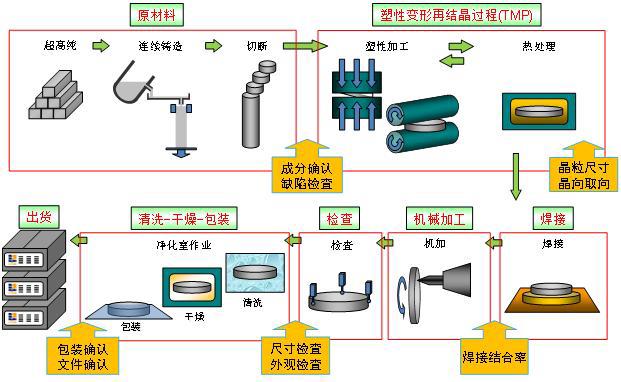
目前主要用熔炼铸造和粉末冶金的方法制备出高纯钽材料。熔炼铸造法是用真空电弧熔炼、等离子熔炼或者电子束熔炼来制备钽铸锭。其优点是靶材纯度高、气体元素含量低、致密度高且可大批量制造,其缺点是对密度与熔点差异较大的两种或两种以上金属,普通的熔炼法比较难以获得成分均匀的材料。
相比于熔炼铸造法,粉末冶金的方法更容易制备出细小均匀的组织,粉末冶金制备的 Ta 产品有着微观组织均匀、织构均匀性较好等优点而广泛使用,但是缺点是杂质含量高、致密度低,而集成电路用的靶材对于纯度以及致密度有着极高的要求,因此粉末冶金制备的 Ta 材料无法应用于半导体集成电路产业。
实际生产中通常采用电子束熔炼并辅以轧制与热处理方式获得不同生产要求的钽产品。电子束熔炼法具有良好的除杂净化能力,可以使钽材料中的杂质含量如氧和氮降低到 150 wt-ppt 以下水平。现在通过电子束熔炼的方法可制备出 99.999%(5N)的高纯度钽。
钽靶材背板采用黄铜材料(CuZn标准牌号C46400),成分表如表1。

靶坯焊接面进行0.45×0.15mm毛化处理,与背板用不锈钢包套进行真空密封,密封后放入热等静压(HIP)腔体,焊接温度与时间分别为750℃、5h,焊接最大压力为115MPa。焊接结果评价方式为超声波无损探伤检测焊接结合率,焊接结合率要求99%以上。
靶材在焊接后,到成品之前,需要经过精密的外形尺寸机械加工,其加工精度需 0.1mm 以下,使靶材的表面平面度以及表面质量符合半导体磁控溅射的要求。
对尺寸较大的靶材进行机械加工时容易出现变形等问题,从而引起靶材的表面平整度、平面度以及表面粗糙度等较差,从而影响溅射性能。尺寸较大的 Ta 靶材(300mm 晶圆用 Ta 靶最大外径尺寸为 524mm),需要在大型的加工车床或者是加工中心设备上进行精密的机加工,具体工艺如下:

Ta 材料在高温的状态下容易发生表面氧化的问题,因此在机械加工的过程中,加工刀具与 Ta 材料接触时的热量尽可能的少,在这个前提下,要求加工时的进刀量需要减少,一般进给量在 300mm 每分钟以下,吃刀量在 0.03mm 以下,靶材溅射面的表面粗糙度 Ra 在 0.5μm 以下,以保证靶材在溅射初期的溅射性能 。
无相关信息